- お役立ち記事
- New employees in the refractory cement manufacturing industry for high-temperature furnaces should learn about material selection to maintain heat resistance and viscosity.
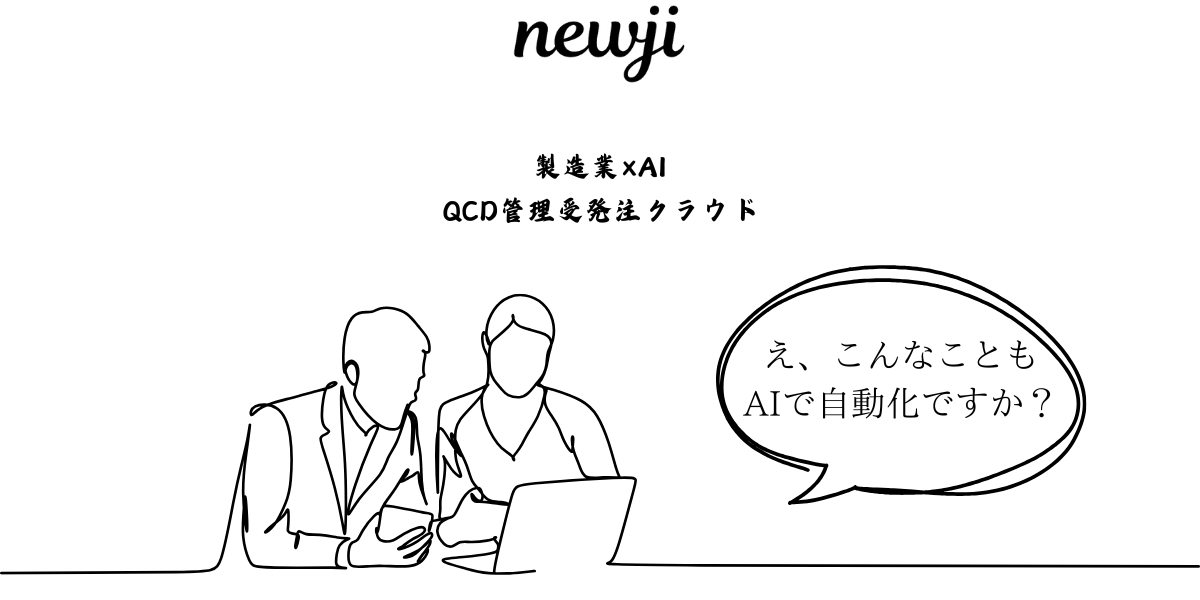
New employees in the refractory cement manufacturing industry for high-temperature furnaces should learn about material selection to maintain heat resistance and viscosity.
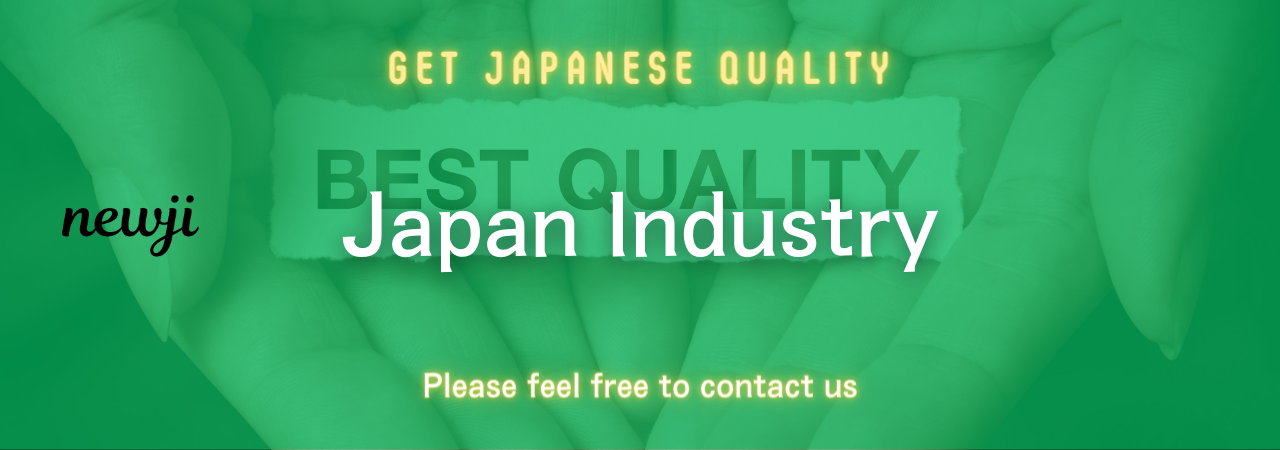
目次
Understanding Refractory Cement Basics
When starting in the refractory cement manufacturing industry, it’s crucial to understand the basics of this essential material.
Refractory cement is specifically designed to endure extremely high temperatures, making it an indispensable component in furnaces, kilns, and reactors.
It provides stability and protection for the structures subjected to immense heat, ensuring safe and efficient operations in various industrial settings.
Importance of Material Selection
Material selection is a fundamental aspect for new employees to focus on when working with refractory cement.
Selecting the right materials can significantly impact the performance and longevity of the cement used in high-temperature environments.
Optimal material choice ensures the refractory cement maintains its heat resistance and viscosity, crucial characteristics for efficient and safe thermal management.
Key Components of Refractory Cement
Understanding the components of refractory cement is essential for making informed decisions regarding material selection.
Refractory cement comprises a mixture of several ingredients, each contributing to the overall performance under high temperatures:
Alumina (Al2O3)
Alumina is a primary component of refractory cement, known for its excellent resistance to high temperatures and abrasive conditions.
It enhances the heat resistance properties, making the cement suitable for use in environments with sustained thermal exposure.
Silica (SiO2)
Silica acts to improve the cement’s thermal shock resistance.
This component helps in maintaining strength and structural integrity during rapid temperature changes, a frequent occurrence in high-temperature industrial processes.
Calcium Aluminate
Calcium aluminate provides binding properties, ensuring that the cement remains intact and performs efficiently under thermal stress.
It contributes to the quick setting and enhanced performance of the cement, especially in environments with fluctuating temperatures.
Magnesium Oxide (MgO)
Magnesium oxide is often incorporated into refractory cement for its superior thermal stability and resistance to basic slags.
It enhances the cement’s ability to withstand exposure to various chemical elements encountered in industrial environments.
Criteria for Effective Material Selection
When selecting materials for refractory cement, several criteria should be considered to ensure optimal performance:
Heat Resistance
The primary function of refractory cement is to withstand high temperatures.
It is vital to select materials with excellent heat resistance to ensure that the cement maintains its integrity and structural stability in extreme thermal conditions.
Viscosity
Viscosity impacts the cement’s ability to flow and adequately fill spaces during application.
Materials affecting the viscosity should be chosen carefully to achieve a balance between workability and strength once the cement sets.
Durability
Durability under prolonged exposure to high temperatures is a key factor.
Materials that contribute to the longevity and stability of the cement in high-stress environments should be prioritized to ensure continuous operation without frequent repairs.
Chemical Resistance
In industrial settings, refractory cement may be exposed to chemical reactants.
Thus, selecting materials that enhance the cement’s chemical resistance is essential to prevent corrosion or degradation over time.
Challenges in Material Selection
Selecting materials for refractory cement can present specific challenges:
Balancing Cost and Performance
While high-performance materials enhance cement quality, they may also increase costs.
Finding an optimum balance between cost-effectiveness and material performance is vital to maintain economic efficiency without compromising safety and functionality.
Environmental Considerations
As sustainability becomes an increasing concern, selecting environmentally friendly materials for refractory cement is crucial.
This approach helps in minimizing environmental impact while maintaining high performance.
Gaining Practical Experience
New employees should seek practical experience to better understand material selection and application.
Hands-on experience in mixing, testing, and applying refractory cement provides invaluable insights into how different materials behave and perform under diverse conditions.
Participating in workshops or field training can enhance understanding and confidence in making material-related decisions.
Conclusion
For new employees in the refractory cement manufacturing industry, learning about material selection is a vital step in ensuring the cement’s effectiveness in high-temperature furnace applications.
By understanding the components, selection criteria, and challenges, new workers can contribute positively to the productivity and safety of industrial operations.
Building a strong foundation in these areas will empower employees to make informed decisions, ensuring that refractory cement continues to perform at its best.
資料ダウンロード
QCD調達購買管理クラウド「newji」は、調達購買部門で必要なQCD管理全てを備えた、現場特化型兼クラウド型の今世紀最高の購買管理システムとなります。
ユーザー登録
調達購買業務の効率化だけでなく、システムを導入することで、コスト削減や製品・資材のステータス可視化のほか、属人化していた購買情報の共有化による内部不正防止や統制にも役立ちます。
NEWJI DX
製造業に特化したデジタルトランスフォーメーション(DX)の実現を目指す請負開発型のコンサルティングサービスです。AI、iPaaS、および先端の技術を駆使して、製造プロセスの効率化、業務効率化、チームワーク強化、コスト削減、品質向上を実現します。このサービスは、製造業の課題を深く理解し、それに対する最適なデジタルソリューションを提供することで、企業が持続的な成長とイノベーションを達成できるようサポートします。
オンライン講座
製造業、主に購買・調達部門にお勤めの方々に向けた情報を配信しております。
新任の方やベテランの方、管理職を対象とした幅広いコンテンツをご用意しております。
お問い合わせ
コストダウンが利益に直結する術だと理解していても、なかなか前に進めることができない状況。そんな時は、newjiのコストダウン自動化機能で大きく利益貢献しよう!
(Β版非公開)