- お役立ち記事
- Optimization of picking system and its effect: Improved warehouse efficiency and procurement process
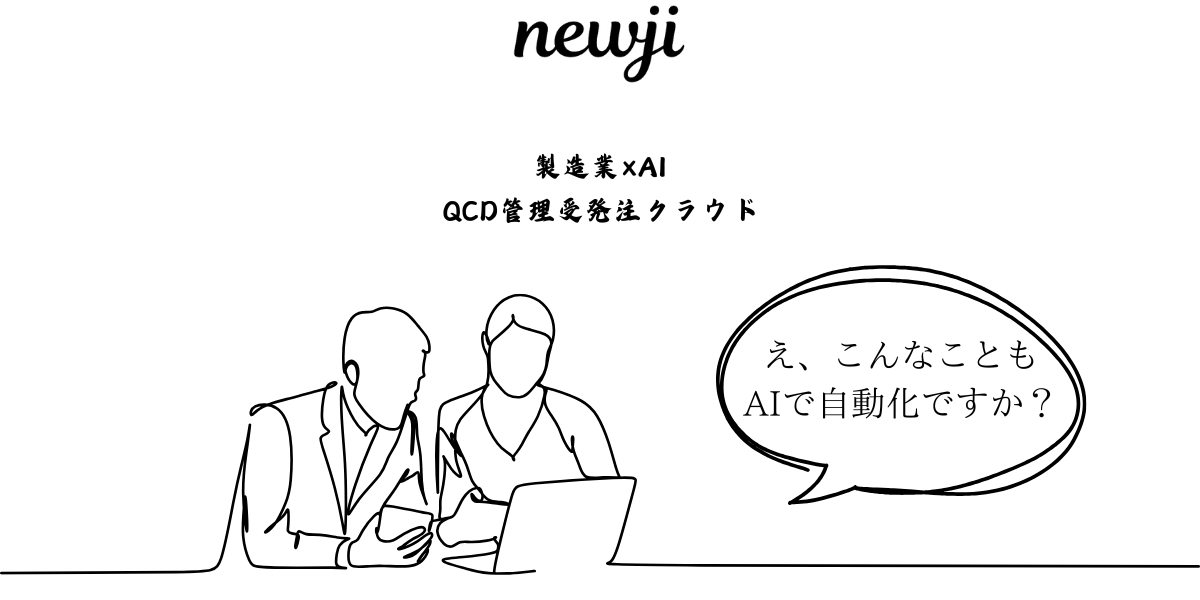
Optimization of picking system and its effect: Improved warehouse efficiency and procurement process
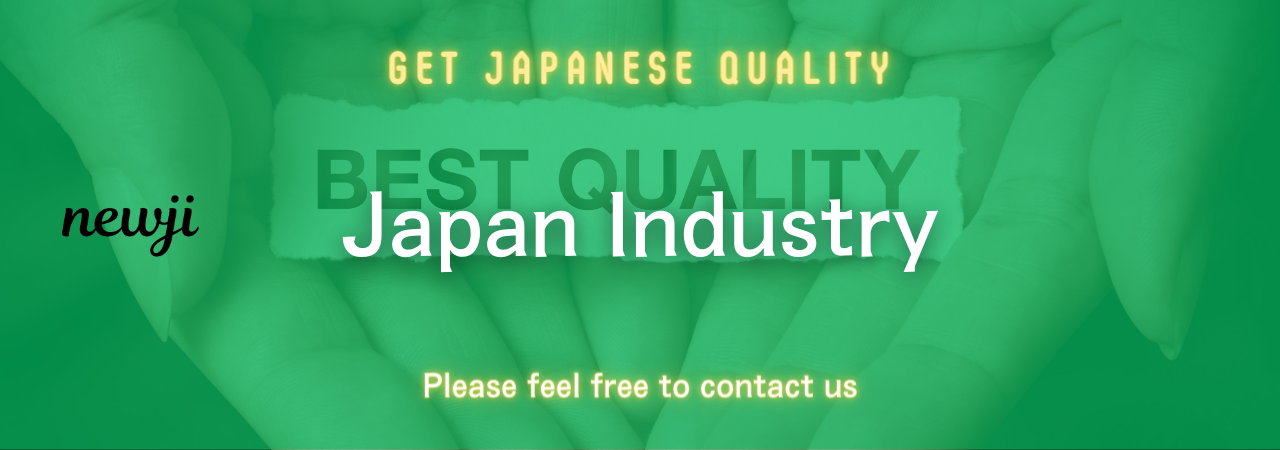
目次
Understanding the Basics of a Picking System
A picking system is a crucial part of any warehouse operation.
In essence, it is the method by which products are selected and readied for shipment to customers.
Efficiency in this process can dramatically impact overall warehouse operations, including procurement and fulfillment times.
A well-optimized picking system can reduce errors, save time, and improve worker productivity.
Types of Picking Systems
Various picking systems are used in warehouses, each with specific advantages and drawbacks.
Pick-to-Order
This system involves selecting items directly from storage based on a specific order.
It is usually employed in situations with low-volume, high-mix products, where each order is unique.
While this method is straightforward, it can be time-consuming, particularly without a well-organized warehouse layout.
Batch Picking
In a batch picking system, items for multiple orders are picked in a single run.
This method is more efficient than pick-to-order, especially for items that are frequently purchased together.
However, it requires careful planning to avoid inaccuracies.
Zone Picking
Zone picking divides the warehouse into different areas or zones, each managed by a different worker.
Orders pass through multiple zones until completed.
This system minimizes the travel time for workers but requires strong coordination among different zones.
Wave Picking
In wave picking, orders are grouped into waves and picked at scheduled times during the day.
This method allows for better management of labor and resources, especially during peak times.
It is commonly used in high-volume operations.
Benefits of Optimizing a Picking System
Optimizing a picking system can offer numerous advantages, transforming the efficiency and effectiveness of your warehouse operations.
Enhanced Productivity
One of the primary benefits is enhanced productivity.
When your picking system is optimized, tasks are completed faster.
Workers spend less time searching for items, leading to quicker order fulfillment.
Reduced Errors
An optimized system significantly reduces the chances of picking errors.
Automated systems and clear procedures help ensure that the right items are selected every time.
Lower Costs
Efficiency also translates into cost savings.
Less time spent picking means lower labor costs.
Reduced errors also mean fewer returns and corrections, saving additional time and money.
Steps to Optimize Your Picking System
Achieving an optimized picking system requires a series of deliberate steps.
Analyze Current Performance
First, conduct a thorough analysis of your current system.
Identify bottlenecks, high-error zones, and areas where workers spend the most time.
Implement Technology
Consider integrating technology such as barcode scanners, RFID tags, and warehouse management systems (WMS).
These tools provide real-time data and automate tasks, reducing human error and increasing speed.
Streamline the Warehouse Layout
An intuitive layout can drastically reduce picking time.
Place high-demand items in easily accessible areas, and group similar products together.
Training and Employee Engagement
Employees play a crucial role in the optimization process.
Comprehensive Training
Provide comprehensive training to ensure all employees understand how to use new technologies and follow optimized procedures.
Regular training refreshers can also help maintain high performance levels.
Engagement and Feedback
Encourage employees to engage in the optimization process.
They often have valuable insights into bottlenecks and inefficiencies.
Collecting and acting on their feedback can lead to continuous improvement.
Measuring the Impact
Once optimization measures are in place, it’s essential to measure their impact.
Key Performance Indicators (KPIs)
Track KPIs such as order accuracy, picking speed, and labor costs.
Compare these metrics before and after optimization to gauge improvement.
Customer Satisfaction
Monitor customer feedback for changes in satisfaction levels.
An efficient picking system ensures faster deliveries and fewer errors, which should reflect positively in customer reviews.
The Role of Continuous Improvement
Optimization is not a one-time task.
Regular Audits
Conduct regular audits to keep up with any changes in demand and identify new bottlenecks.
Adapting to Change
The business environment is always changing, and so should your picking system.
Stay updated with the latest technologies and methodologies to keep your system at peak efficiency.
Conclusion
Optimizing your picking system can lead to remarkable improvements in warehouse efficiency and the procurement process.
Through careful analysis, the integration of technology, and continuous improvement, your warehouse can achieve faster turnaround times, reduced errors, and lower operational costs.
Ultimately, an optimized picking system not only benefits your business but also enhances customer satisfaction.
With well-implemented strategies, your warehouse can become a model of efficiency and reliability.
資料ダウンロード
QCD調達購買管理クラウド「newji」は、調達購買部門で必要なQCD管理全てを備えた、現場特化型兼クラウド型の今世紀最高の購買管理システムとなります。
ユーザー登録
調達購買業務の効率化だけでなく、システムを導入することで、コスト削減や製品・資材のステータス可視化のほか、属人化していた購買情報の共有化による内部不正防止や統制にも役立ちます。
NEWJI DX
製造業に特化したデジタルトランスフォーメーション(DX)の実現を目指す請負開発型のコンサルティングサービスです。AI、iPaaS、および先端の技術を駆使して、製造プロセスの効率化、業務効率化、チームワーク強化、コスト削減、品質向上を実現します。このサービスは、製造業の課題を深く理解し、それに対する最適なデジタルソリューションを提供することで、企業が持続的な成長とイノベーションを達成できるようサポートします。
オンライン講座
製造業、主に購買・調達部門にお勤めの方々に向けた情報を配信しております。
新任の方やベテランの方、管理職を対象とした幅広いコンテンツをご用意しております。
お問い合わせ
コストダウンが利益に直結する術だと理解していても、なかなか前に進めることができない状況。そんな時は、newjiのコストダウン自動化機能で大きく利益貢献しよう!
(Β版非公開)