- お役立ち記事
- Optimization of traceability systems that leaders of logistics management departments in medical device manufacturing industries should know about
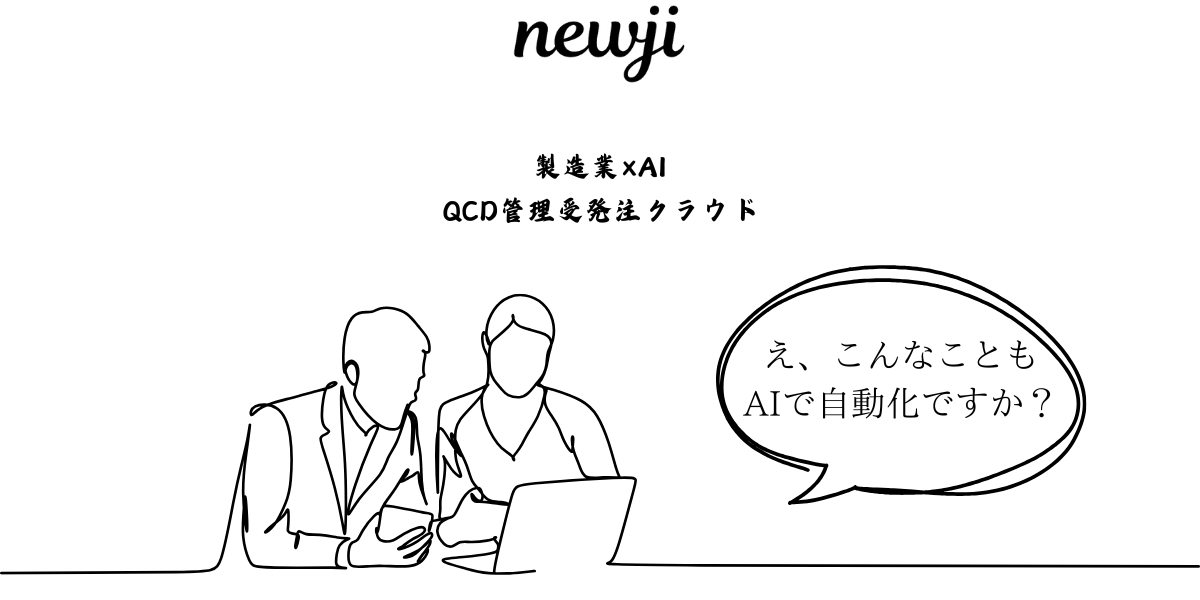
Optimization of traceability systems that leaders of logistics management departments in medical device manufacturing industries should know about
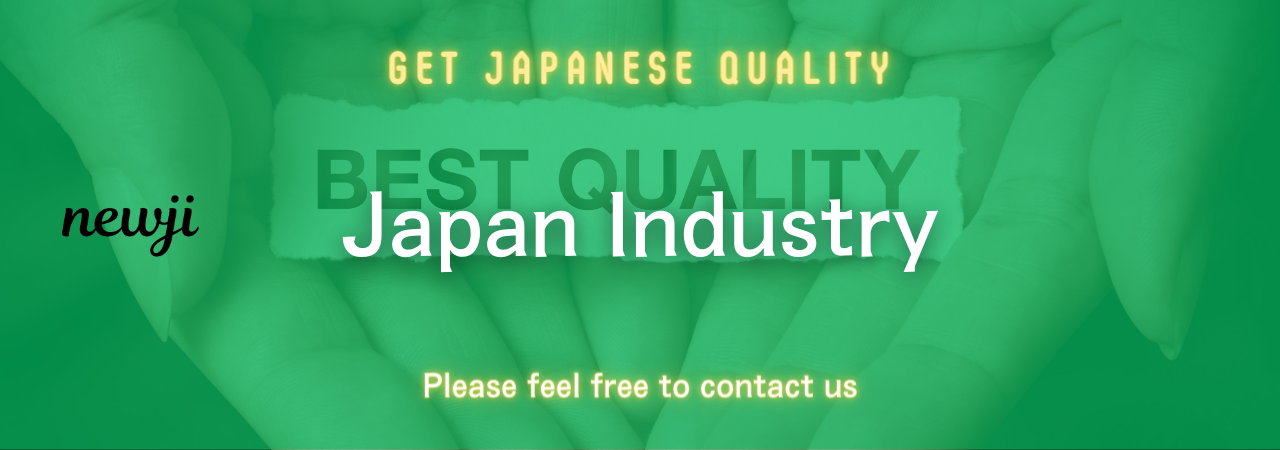
目次
Understanding Traceability Systems in Medical Device Manufacturing
Traceability systems play a crucial role in the medical device manufacturing industry, providing a robust framework for tracking products from production through to end-user delivery.
These systems are key to ensuring product safety, compliance with regulatory standards, and efficient recall processes when necessary.
Optimizing these systems can enhance operational efficiency, reduce costs, and improve customer satisfaction.
The Importance of Traceability
In the medical device industry, traceability is not optional; it’s a regulatory requirement.
The ability to track and trace every component and process involved in manufacturing a device helps ensure quality and compliance.
Regulatory bodies like the FDA (U.S. Food and Drug Administration) mandate stringent traceability standards to protect patient safety and maintain market trust.
Traceability systems enable detailed record-keeping, providing essential data for audits, inspections, and any necessary corrective actions.
Components of a Traceability System
Effective traceability systems in medical device manufacturing generally consist of several key components:
1. **Unique Device Identification (UDI):** A system to identify medical devices through distribution and use, facilitating post-market surveillance.
2. **Batch/Lot Number Tracking:** Vital for tracking production batches, ensuring quick action can be taken in case of product failures or recalls.
3. **Barcoding and RFID:** Technologies that streamline data capture and product tracking through automated scanning.
4. **Data Management Software:** Software solutions that compile, store, and analyze data, providing insights into product history and facilitating regulatory compliance.
Optimizing Traceability Systems
Optimization of traceability systems can greatly enhance the efficiency and effectiveness of logistics management within the medical device industry.
Here are several strategies for improvement:
Implement Advanced Technologies
Introducing advanced technologies such as blockchain can revolutionize traceability by providing immutable records and increased transparency.
Blockchain technology ensures that every transaction or modification in the production lifecycle is securely recorded and accessible.
IoT (Internet of Things) can also enhance traceability systems by enabling real-time monitoring of products throughout the supply chain.
Sensors and smart devices can provide immediate updates on location, handling conditions, and more.
Enhance Data Integration
Integrating traceability systems with other enterprise systems like ERP (Enterprise Resource Planning) and CRM (Customer Relationship Management) can streamline data flow across the organization.
This integration allows for a single source of truth, reduces redundancy, and ensures that all departments have access to the most current information.
Improve User Training and Engagement
A traceability system is only as good as the people who use it.
Investing in comprehensive training programs ensures that all users understand how to effectively operate these systems and appreciate their importance.
Engaged and informed employees are more likely to adhere to data entry protocols and maintain high-quality data.
Regularly Review and Update Systems
Regular reviews and updates of traceability systems are crucial to adapt to technological advancements and changing regulatory requirements.
Conduct periodic audits to identify any weaknesses or inefficiencies in the current system.
Stay informed about technological trends and regulatory changes that could impact traceability requirements.
Benefits of Optimized Traceability Systems
The benefits of optimizing traceability systems extend beyond compliance and regulation.
Companies can achieve significant operational advantages through efficient traceability systems.
Reduced Risk and Improved Compliance
Optimized systems reduce the risk of non-compliance and associated penalties by ensuring alignment with current regulatory standards.
They enable timely identification and resolution of issues, helping to avert potential product recalls or market withdrawals.
Enhanced Product Quality
With improved traceability, manufacturers can quickly isolate and rectify any product flaws.
This not only reduces waste and rework but also enhances overall product quality and customer satisfaction.
Streamlined Recall Processes
In case of product defects, a robust traceability system allows for swift and precise recalls.
This minimizes the impact on consumer safety and limits potential legal and financial repercussions for the manufacturer.
Increased Customer Trust
Customers have greater confidence in products when they know their safety and quality are ensured through detailed traceability.
Transparent supply chains foster greater customer trust and loyalty, providing a competitive advantage in the marketplace.
Conclusion
For leaders in logistics management within the medical device manufacturing industry, understanding and optimizing traceability systems is paramount.
By leveraging advanced technologies, enhancing integration, and equipping users with the necessary training, companies can achieve a robust traceability framework.
The resulting benefits, from enhanced compliance to improved customer trust, underscore the integral role of traceability systems in securing success in the medical device sector.
資料ダウンロード
QCD調達購買管理クラウド「newji」は、調達購買部門で必要なQCD管理全てを備えた、現場特化型兼クラウド型の今世紀最高の購買管理システムとなります。
ユーザー登録
調達購買業務の効率化だけでなく、システムを導入することで、コスト削減や製品・資材のステータス可視化のほか、属人化していた購買情報の共有化による内部不正防止や統制にも役立ちます。
NEWJI DX
製造業に特化したデジタルトランスフォーメーション(DX)の実現を目指す請負開発型のコンサルティングサービスです。AI、iPaaS、および先端の技術を駆使して、製造プロセスの効率化、業務効率化、チームワーク強化、コスト削減、品質向上を実現します。このサービスは、製造業の課題を深く理解し、それに対する最適なデジタルソリューションを提供することで、企業が持続的な成長とイノベーションを達成できるようサポートします。
オンライン講座
製造業、主に購買・調達部門にお勤めの方々に向けた情報を配信しております。
新任の方やベテランの方、管理職を対象とした幅広いコンテンツをご用意しております。
お問い合わせ
コストダウンが利益に直結する術だと理解していても、なかなか前に進めることができない状況。そんな時は、newjiのコストダウン自動化機能で大きく利益貢献しよう!
(Β版非公開)