- お役立ち記事
- Optimization techniques for material costs and inventory management that purchasing personnel should know
Optimization techniques for material costs and inventory management that purchasing personnel should know
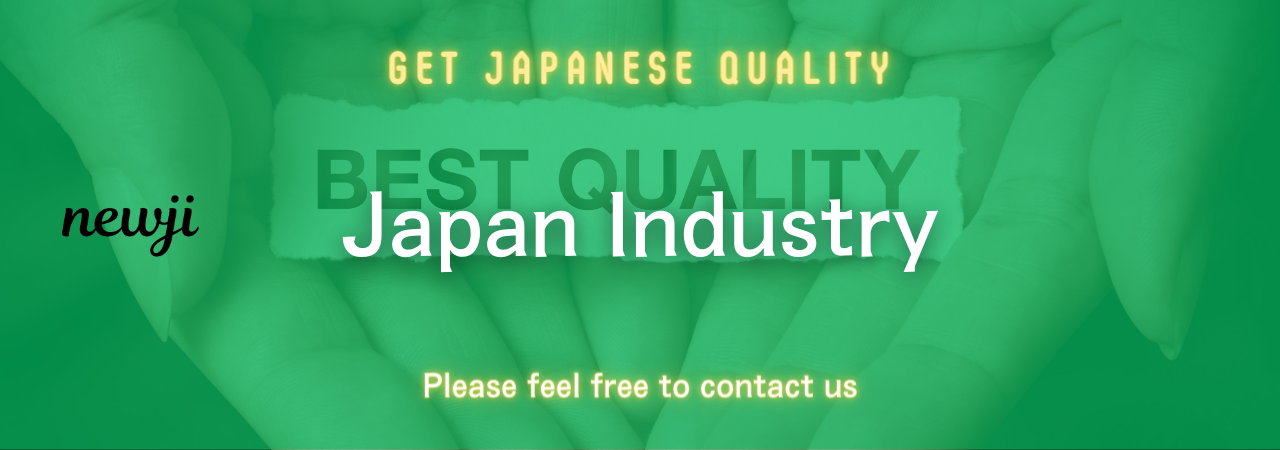
目次
Understanding Material Costs and Inventory Management
Managing material costs and inventory is crucial for purchasing personnel in any organization.
Effective management ensures that materials are procured at optimal prices and are available when needed without overstocking.
This balance can significantly affect a company’s bottom line, making it essential to apply optimization techniques.
Purchasing personnel need to be well-versed in strategies that streamline processes and control costs.
Let’s explore some of these techniques to achieve efficiency and cost-effectiveness.
Importance of Optimizing Material Costs
Material costs make up a substantial portion of a company’s expenses, particularly in manufacturing and retail sectors.
These costs can vary due to market fluctuations, supplier pricing, and changes in demand.
By optimizing material costs, purchasing personnel can help reduce overall expenditure and boost profitability.
1. Supplier Evaluation and Negotiation
One of the first steps in optimizing material costs is conducting a thorough evaluation of suppliers.
Comparing quality, reliability, and pricing among different suppliers can uncover opportunities for better deals.
Engaging in negotiations to secure favorable terms, such as bulk discounts or extended payment terms, can also lead to significant cost savings.
2. Bulk Purchasing and Strategic Partnerships
Buying in bulk can often lead to lower per-unit costs, as suppliers are generally willing to offer discounts for larger orders.
However, it’s essential to balance bulk purchasing with inventory constraints to avoid overstocking.
Strategic partnerships with key suppliers can also result in preferential pricing, access to new materials, and insights into market trends.
3. Cost Analysis and Market Trends
Constantly analyzing material costs and staying informed about market trends is vital for making informed purchasing decisions.
Tools such as cost analysis software can help track price changes and identify potential savings.
Understanding market trends ensures that purchasing personnel are proactive in sourcing materials at the best possible times.
Effective Inventory Management Techniques
Inventory management is about having the right amount of stock at the right time.
Poor inventory management can result in either excess stock or stockouts, both of which can be costly.
Optimizing inventory management involves techniques that ensure materials are available as needed without tying up excessive capital in stock.
1. Just-In-Time (JIT) Inventory
Just-In-Time inventory management is a strategy where materials are ordered just in time for production or sale.
This approach minimizes inventory costs by keeping stock levels as low as possible while meeting demand.
However, it requires precise coordination with suppliers and a reliable demand forecast to avoid delays.
2. Demand Forecasting and Planning
Accurate demand forecasting is a cornerstone of successful inventory management.
By analyzing historical sales data and market trends, purchasing personnel can predict future material needs more precisely.
This allows for better planning, reduces the risk of overstocking, and helps avoid stockouts.
3. Inventory Turnover Ratio
The inventory turnover ratio measures how often inventory is sold and replaced over a period.
A higher ratio indicates efficient inventory management and strong sales.
Monitoring this ratio helps purchasing personnel identify slow-moving stock and make informed decisions about inventory levels.
Technology’s Role in Optimization
Technology plays a vital role in optimizing both material costs and inventory management.
Advanced software tools can automate and streamline various processes, providing greater accuracy and efficiency.
1. Automated Procurement Systems
Automating procurement processes through software solutions can significantly reduce the time and effort required for purchasing activities.
Automated systems can manage supplier communications, track order statuses, and keep detailed records, enhancing productivity and reducing errors.
2. Inventory Management Software
Inventory management software provides real-time data on stock levels, helping purchasing personnel make informed decisions.
These tools often include features like demand forecasting, order tracking, and stock notifications, ensuring optimal inventory levels at all times.
3. Data Analytics for Insight
Utilizing data analytics can give purchasing personnel deep insights into spending patterns, supplier performance, and inventory trends.
Analyzing this data helps identify areas for cost savings and efficiency improvements, fostering better decision-making overall.
Conclusion
Effective optimization of material costs and inventory management is essential for purchasing personnel to contribute to an organization’s success.
By employing strategies such as supplier evaluation, demand forecasting, and leveraging technology, it’s possible to streamline operations and reduce costs.
Staying informed and proactive in applying these techniques ensures that materials are available when needed, at the best possible prices, without overstocking.
With these practices in place, companies can maintain a competitive edge and enhance their profitability.
資料ダウンロード
QCD調達購買管理クラウド「newji」は、調達購買部門で必要なQCD管理全てを備えた、現場特化型兼クラウド型の今世紀最高の購買管理システムとなります。
ユーザー登録
調達購買業務の効率化だけでなく、システムを導入することで、コスト削減や製品・資材のステータス可視化のほか、属人化していた購買情報の共有化による内部不正防止や統制にも役立ちます。
NEWJI DX
製造業に特化したデジタルトランスフォーメーション(DX)の実現を目指す請負開発型のコンサルティングサービスです。AI、iPaaS、および先端の技術を駆使して、製造プロセスの効率化、業務効率化、チームワーク強化、コスト削減、品質向上を実現します。このサービスは、製造業の課題を深く理解し、それに対する最適なデジタルソリューションを提供することで、企業が持続的な成長とイノベーションを達成できるようサポートします。
オンライン講座
製造業、主に購買・調達部門にお勤めの方々に向けた情報を配信しております。
新任の方やベテランの方、管理職を対象とした幅広いコンテンツをご用意しております。
お問い合わせ
コストダウンが利益に直結する術だと理解していても、なかなか前に進めることができない状況。そんな時は、newjiのコストダウン自動化機能で大きく利益貢献しよう!
(Β版非公開)