- お役立ち記事
- Optimizing Clean Processes in Manufacturing with CIP (Clean-in-Place)
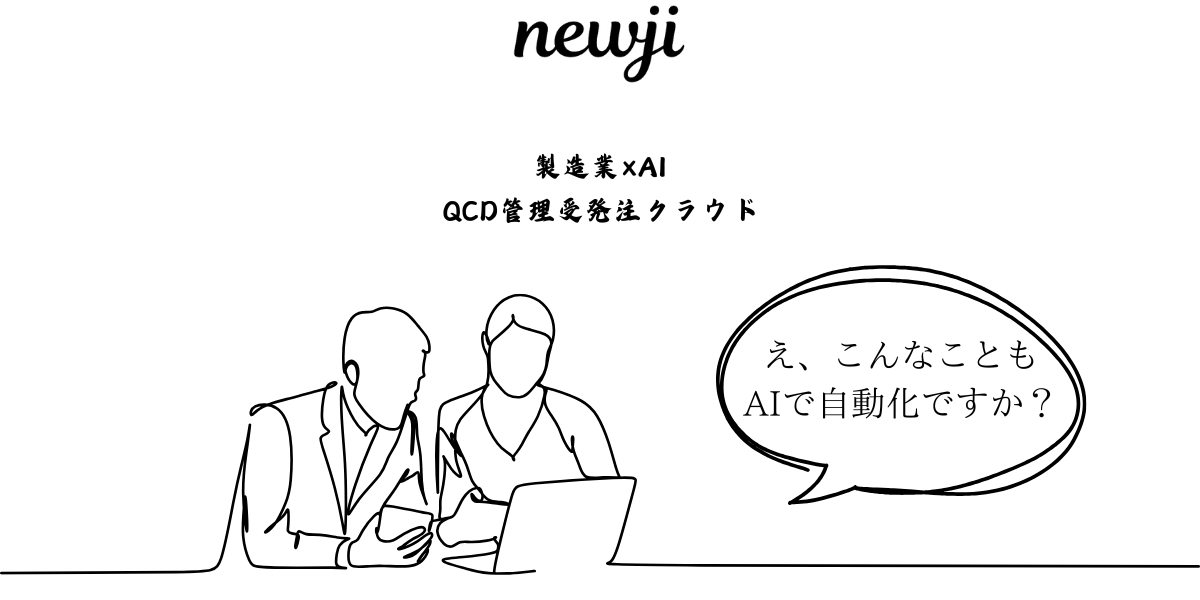
Optimizing Clean Processes in Manufacturing with CIP (Clean-in-Place)
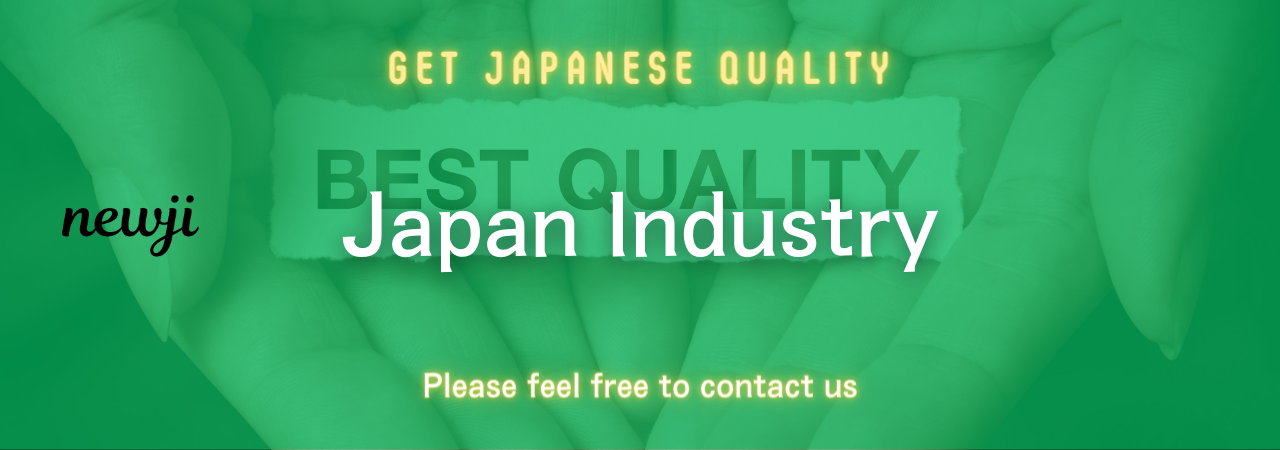
Clean-in-Place (CIP) technology has revolutionized the way industries approach sanitation and efficiency.
Whether you are in the pharmaceutical, food and beverage, or any other manufacturing sector, understanding how to optimize clean processes with CIP can significantly improve your operation.
Let’s delve into the essential aspects of CIP and how its application can benefit your manufacturing processes.
目次
Understanding Clean-in-Place (CIP) Systems
Clean-in-Place (CIP) is a method used to clean the interior surfaces of pipes, vessels, process equipment, filters, and associated fittings, without disassembly.
CIP has become an essential concept in manufacturing industries, especially where hygiene is crucial.
Through this system, you can ensure that all parts of the equipment are clean, thus preventing contaminants and adhering to strict hygiene standards.
What Is CIP?
CIP involves the use of high-pressure cleaning and sanitizing solutions that are circulated through process lines and vessels.
This method eliminates the need to dismantle machinery, which not only saves time but also enhances safety by reducing the risk of human error during reassembly.
The system utilizes automated controls to monitor and adjust variables like temperature, time, and chemical concentration, ensuring a consistent and reliable cleaning process.
The Importance of CIP in Manufacturing
CIP systems are indispensable in various manufacturing sectors for maintaining both product quality and production efficiency.
Here’s why they are so critical in today’s industrial landscape.
Ensuring Hygiene and Safety
One of the primary benefits of CIP is its ability to maintain high hygiene standards.
By cleaning equipment thoroughly, CIP helps prevent contamination, which is vital in industries like pharmaceuticals and food and beverage.
CIP systems mitigate the risk of cross-contamination, thereby safeguarding consumer health and complying with regulatory standards.
Maximizing Production Efficiency
Removing the need to disassemble and manually clean equipment significantly reduces downtime.
With CIP, cleaning can be conducted more frequently without major production halts, allowing for more consistent manufacturing cycles.
This increased efficiency can lead to higher output and better utilization of resources.
Cost-Effectiveness
While investing in a CIP system may seem costly initially, it can provide substantial long-term savings.
Automated cleaning reduces labor costs and minimizes the risk of extended shutdowns due to manual cleaning inconsistencies.
Also, the precise control of cleaning parameters optimizes chemical and water usage, contributing to more sustainable operations.
Key Components of a CIP System
A well-designed CIP system consists of several critical components that work together to ensure optimal cleaning.
Understanding these elements is crucial for anyone looking to implement or optimize CIP processes.
Control Units
Modern CIP systems come with advanced control units that automate the cleaning process.
These units manage parameters such as temperature, chemical concentration, and cycle time, ensuring a consistent and effective cleaning routine.
Automated controls also allow for real-time monitoring and data collection, facilitating better process analysis and optimization.
Cleaning Solutions
The types of cleaning solutions used in CIP systems vary depending on the specific requirements of the equipment and residues involved.
Common solutions include caustic soda, acid cleaners, and sanitizers.
It is crucial to select the right blend of chemicals and their concentrations to ensure thorough cleaning without damaging equipment.
Pumps and Valves
High-performance pumps and strategically placed valves are vital for the efficient circulation of cleaning solutions.
Pumps maintain the necessary flow rate and pressure, while valves control the direction and flow of the liquids, ensuring they reach all parts of the equipment.
Proper design and maintenance of these components are essential to avoid blockages and inefficiencies.
Heat Exchangers
Heat exchangers are used to regulate the temperature of cleaning solutions, ensuring optimal cleaning efficacy.
Maintaining the appropriate temperature is crucial, as it helps in breaking down residues and ensuring the effectiveness of sanitizing agents.
Best Practices for Optimizing CIP Processes
Implementing a CIP system is just the beginning.
To fully harness its potential, you need to adhere to certain best practices.
Regularly Monitor and Adjust Parameters
Constantly monitoring the key parameters of your CIP system—such as temperature, chemical concentration, and cycle duration—is essential.
These parameters should be adjusted based on the types of residues, equipment design, and specific hygiene requirements.
Regular audits and adjustments can help in maintaining the system’s effectiveness over time.
Conduct Routine Maintenance
Even with automated systems, routine maintenance is indispensable.
Regularly inspect pumps, valves, and other mechanical components for wear and tear.
Ensure that all control units are functioning correctly and update software as needed.
Maintenance activities should be logged and reviewed to anticipate and prevent potential issues.
Employee Training
A well-designed CIP system can only work effectively if the staff operating it are well-trained.
Ensure that employees understand the importance of each component, how to interpret control unit data, and how to respond to any anomalies.
Continuous training programs can also keep the team updated on the latest CIP technologies and practices.
Use of Modern Technologies
Incorporating modern technologies such as IoT (Internet of Things) and AI (Artificial Intelligence) can significantly enhance your CIP processes.
IoT devices can provide real-time data, enabling more precise monitoring and faster response times.
AI can analyze data trends to predict when maintenance is required, further minimizing downtime and increasing efficiency.
Conclusion
Clean-in-Place (CIP) systems offer numerous benefits that extend beyond simple sanitation.
From improving operational efficiency and maintaining high standards of hygiene to offering long-term cost savings, CIP is an invaluable tool for modern manufacturing.
By understanding the key components and best practices for optimization, you can make the most of what CIP systems have to offer.
With a strategic approach and the right technological integrations, your manufacturing processes can achieve new heights of cleanliness and efficiency.
資料ダウンロード
QCD調達購買管理クラウド「newji」は、調達購買部門で必要なQCD管理全てを備えた、現場特化型兼クラウド型の今世紀最高の購買管理システムとなります。
ユーザー登録
調達購買業務の効率化だけでなく、システムを導入することで、コスト削減や製品・資材のステータス可視化のほか、属人化していた購買情報の共有化による内部不正防止や統制にも役立ちます。
NEWJI DX
製造業に特化したデジタルトランスフォーメーション(DX)の実現を目指す請負開発型のコンサルティングサービスです。AI、iPaaS、および先端の技術を駆使して、製造プロセスの効率化、業務効率化、チームワーク強化、コスト削減、品質向上を実現します。このサービスは、製造業の課題を深く理解し、それに対する最適なデジタルソリューションを提供することで、企業が持続的な成長とイノベーションを達成できるようサポートします。
オンライン講座
製造業、主に購買・調達部門にお勤めの方々に向けた情報を配信しております。
新任の方やベテランの方、管理職を対象とした幅広いコンテンツをご用意しております。
お問い合わせ
コストダウンが利益に直結する術だと理解していても、なかなか前に進めることができない状況。そんな時は、newjiのコストダウン自動化機能で大きく利益貢献しよう!
(Β版非公開)