- お役立ち記事
- Optimizing Manufacturing Processes with Inline Inspection Systems
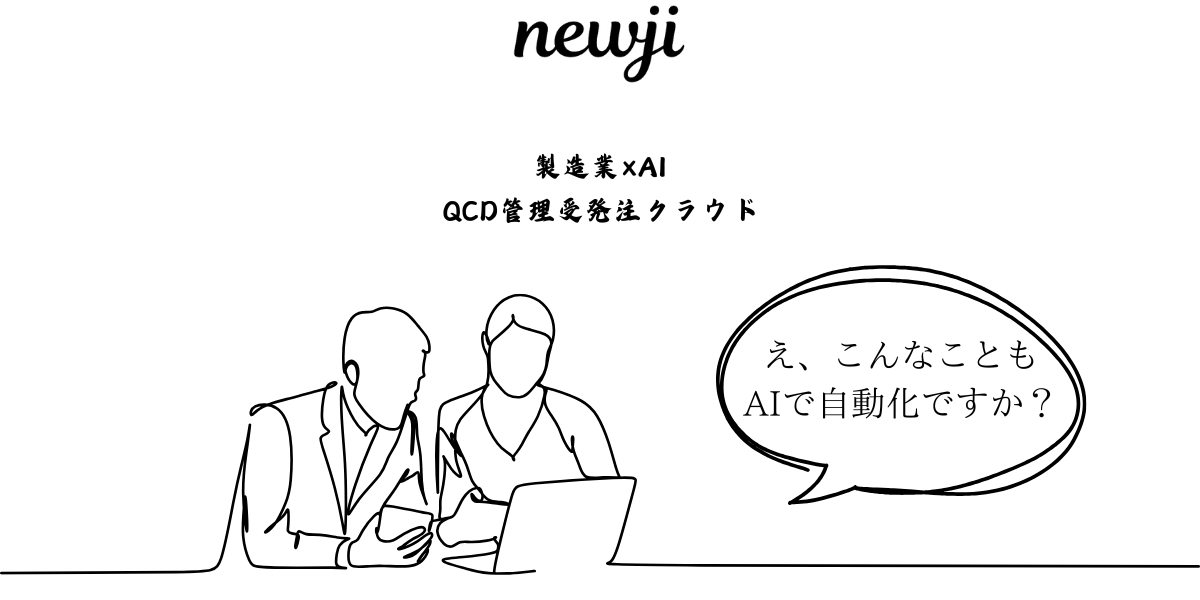
Optimizing Manufacturing Processes with Inline Inspection Systems
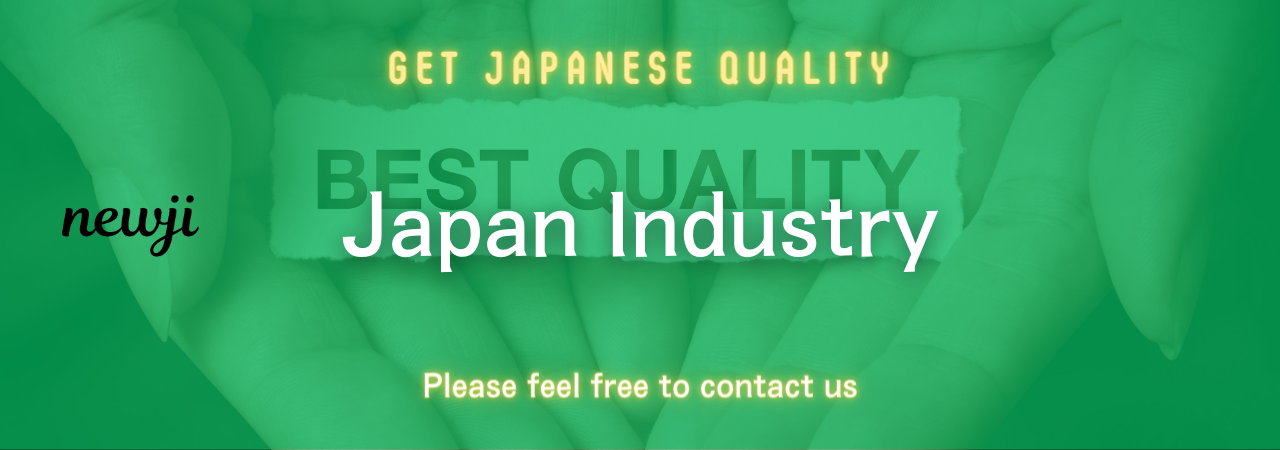
目次
Introduction to Inline Inspection Systems
Inline inspection systems are revolutionizing the way manufacturers ensure quality and efficiency in their production processes.
These systems are integrated directly into the production line, allowing for real-time monitoring and inspection of products.
This eliminates the need for separate quality control steps, thereby streamlining the entire manufacturing process.
The Importance of Quality Control in Manufacturing
Quality control is critical in manufacturing because it helps maintain product standards and customer satisfaction.
Ensuring that products meet certain criteria prevents defects and reduces waste.
It also minimizes the risk of costly recalls and enhances the brand’s reputation.
Challenges in Traditional Quality Control
Traditional quality control methods often require manual inspection, which can be time-consuming and prone to human error.
These methods may also necessitate stopping the production line to perform tests, causing delays and reducing overall efficiency.
Moreover, manual inspections might not be able to catch all potential defects, leading to subpar products reaching the market.
How Inline Inspection Systems Work
Inline inspection systems use advanced technologies such as cameras, sensors, and machine learning algorithms to monitor and analyze products as they move through the production line.
They can detect a wide range of defects, including sizing errors, surface imperfections, and internal flaws.
Real-Time Data Collection
One of the key advantages of inline inspection systems is their ability to collect data in real-time.
This means that any defects or issues can be identified and addressed immediately, without the need to halt production.
This real-time data collection helps optimize the manufacturing process by allowing for instant corrections.
Automation and Integration
Inline inspection systems are fully automated and can be seamlessly integrated into existing production lines.
This eliminates the need for manual intervention, further reducing the risk of human error.
Automation also enhances the speed and accuracy of inspections, ensuring that each product meets the required standards.
Benefits of Using Inline Inspection Systems
There are numerous benefits to incorporating inline inspection systems into manufacturing processes.
Increased Efficiency
By automating the inspection process, inline systems can significantly boost production speed.
There is no need to stop the line for quality checks, leading to faster turnaround times.
This increased efficiency can result in higher productivity and lower operational costs.
Enhanced Product Quality
Inline inspection systems are highly accurate and can detect even the smallest defects.
This ensures that only high-quality products reach the market.
Higher product quality translates to higher customer satisfaction and reduced returns or complaints.
Cost Savings
Using inline inspection systems can lead to substantial cost savings.
By identifying defects early, manufacturers can reduce waste and avoid the expenses associated with scrapping defective products.
Additionally, the automation of inspections reduces labor costs and minimizes the financial impact of recalls.
Applications of Inline Inspection Systems
Inline inspection systems are versatile and can be used across various industries.
Automotive Industry
In the automotive industry, these systems can inspect parts such as engine components, transmissions, and body panels.
Ensuring that each part meets strict quality standards is crucial for the safety and reliability of the vehicles.
Food and Beverage Industry
Food and beverage manufacturers use inline inspection systems to check for packaging errors, contamination, and proper labeling.
This helps ensure that products are safe for consumption and comply with regulatory standards.
Electronics Industry
In the electronics industry, inline inspection systems can detect issues such as solder defects, component misplacements, and circuit board errors.
This is essential for maintaining the performance and reliability of electronic devices.
Choosing the Right Inline Inspection System
Selecting the appropriate inline inspection system for your manufacturing process is a critical decision.
Assessing Your Needs
The first step is to assess your specific needs and requirements.
Consider the type of products you manufacture, the common defects you encounter, and the inspection speed you require.
Evaluating Features and Capabilities
Look for systems that offer the features and capabilities you need.
This may include high-resolution cameras, advanced software analytics, and compatibility with your existing equipment.
Cost and Return on Investment
While the initial cost of an inline inspection system can be significant, it is important to consider the long-term return on investment.
Evaluate the potential cost savings, productivity gains, and quality improvements that the system can provide.
Implementing Inline Inspection Systems
Once you have chosen the right system, effective implementation is key to maximizing its benefits.
Staff Training
Ensure that your staff is properly trained to operate and maintain the inline inspection system.
This will help you get the most out of the technology and avoid potential issues.
Regular Maintenance
Regular maintenance is essential to keep the system running smoothly.
Scheduled maintenance checks can prevent breakdowns and ensure continuous high performance.
Monitoring and Optimization
Continuously monitor the performance of the inline inspection system and make necessary adjustments.
Optimization can help you address any emerging issues and improve the overall efficiency of your manufacturing process.
Conclusion
Inline inspection systems are a powerful tool for optimizing manufacturing processes.
They offer numerous benefits, including increased efficiency, enhanced product quality, and cost savings.
By integrating these systems into your production line, you can stay competitive in the market and deliver high-quality products to your customers.
資料ダウンロード
QCD調達購買管理クラウド「newji」は、調達購買部門で必要なQCD管理全てを備えた、現場特化型兼クラウド型の今世紀最高の購買管理システムとなります。
ユーザー登録
調達購買業務の効率化だけでなく、システムを導入することで、コスト削減や製品・資材のステータス可視化のほか、属人化していた購買情報の共有化による内部不正防止や統制にも役立ちます。
NEWJI DX
製造業に特化したデジタルトランスフォーメーション(DX)の実現を目指す請負開発型のコンサルティングサービスです。AI、iPaaS、および先端の技術を駆使して、製造プロセスの効率化、業務効率化、チームワーク強化、コスト削減、品質向上を実現します。このサービスは、製造業の課題を深く理解し、それに対する最適なデジタルソリューションを提供することで、企業が持続的な成長とイノベーションを達成できるようサポートします。
オンライン講座
製造業、主に購買・調達部門にお勤めの方々に向けた情報を配信しております。
新任の方やベテランの方、管理職を対象とした幅広いコンテンツをご用意しております。
お問い合わせ
コストダウンが利益に直結する術だと理解していても、なかなか前に進めることができない状況。そんな時は、newjiのコストダウン自動化機能で大きく利益貢献しよう!
(Β版非公開)