- お役立ち記事
- Optimizing Real-Time Production Line Monitoring with Measurement Engineering
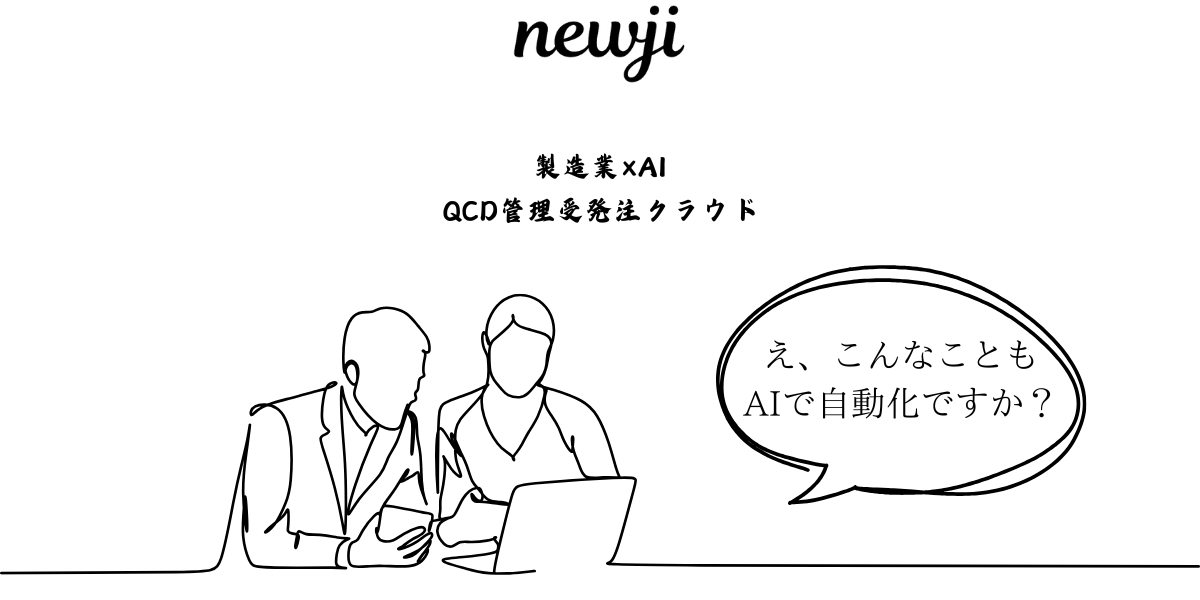
Optimizing Real-Time Production Line Monitoring with Measurement Engineering
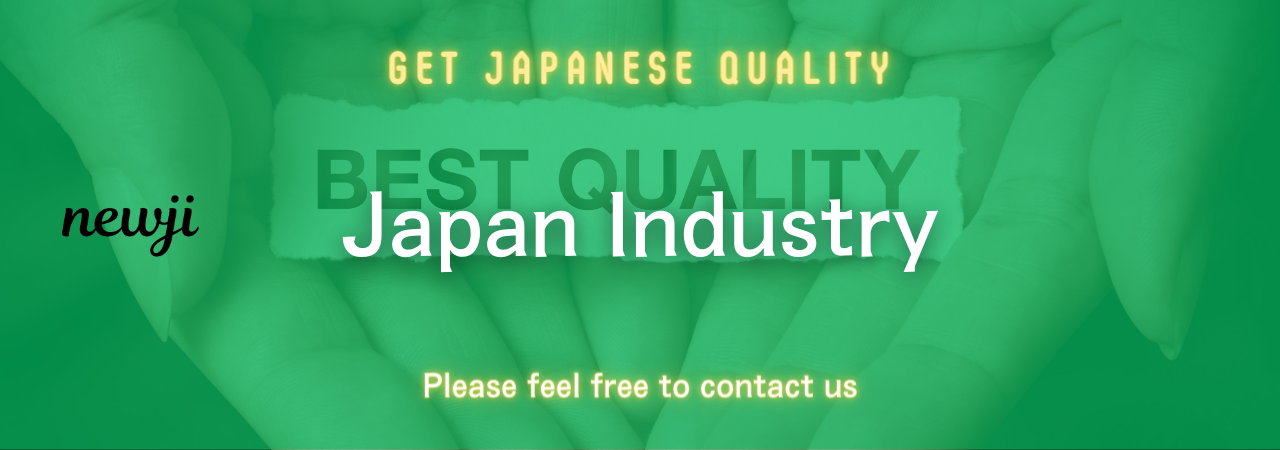
目次
Introduction to Real-Time Production Line Monitoring
Production lines are at the heart of manufacturing, serving as intricate systems that transform raw materials into finished products.
Monitoring these production lines in real-time is crucial for maintaining efficiency, ensuring quality, and optimizing operations.
Real-time monitoring provides immediate data on the performance of production processes, allowing for quick adjustments and enhancements.
Incorporating measurement engineering into real-time monitoring helps in precise data collection, enabling more accurate analysis and informed decision-making.
This synergy enhances the capability to troubleshoot issues, maintain equipment, and predict failures before they occur, ultimately saving time and costs.
The Role of Measurement Engineering
Measurement engineering involves the design, construction, and use of measurement devices and systems to obtain data concerning various processes.
In the context of production lines, it focuses on implementing technology and methodologies that capture accurate real-time data.
By integrating measurement engineering principles, businesses can streamline their production processes.
They gain insights into various parameters such as temperature, pressure, speed, and efficiency, which are essential for maintaining product quality and ensuring compliance with industry standards.
Importance of Accurate Data
Accurate data is fundamental to effective production line monitoring.
Measurement engineering ensures this accuracy by employing calibrated instruments and sophisticated techniques to minimize errors.
With precise data, businesses can pinpoint inefficiencies, understand the causes of waste, and identify opportunities for optimization.
This data serves as a foundation for strategic planning, helping to align production with demand and minimize inventory costs.
The Benefits of Real-Time Monitoring
Real-time monitoring provides several advantages that extend beyond immediate process control.
Here are some key benefits:
Enhanced Operational Efficiency
The constant flow of data allows for the rapid detection of anomalies within the production line.
Operators can make informed decisions on the spot, fine-tuning equipment and workflows to maximize output and quality.
This immediate feedback loop aids in reducing downtime and improving the overall production efficiency.
Predictive Maintenance
With real-time data and measurement engineering, companies can move from reactive to predictive maintenance.
Monitoring equipment health continuously allows for the prediction of failures before they happen.
This proactive approach leads to reduced unexpected breakdowns, prolonged equipment life, and minimal disruptions in production.
Improved Product Quality
Monitoring production with precision leads to better quality control.
Real-time data helps identify defects as they occur, allowing for immediate correction without affecting subsequent processes.
Consistency in product quality boosts customer satisfaction and strengthens the brand’s reputation.
Implementing Real-Time Monitoring with Measurement Engineering
Successfully implementing a real-time monitoring system with measurement engineering involves several steps:
Analyzing Current Systems
Before integrating new technologies, it is vital to analyze the existing production line systems and identify areas that can benefit from enhanced monitoring.
Understanding the limitations and capabilities of current processes will guide the selection of appropriate measurement tools and technologies.
Choosing the Right Technology
Selecting the right sensors and instruments is crucial.
Three main criteria for selection are accuracy, reliability, and compatibility with existing systems.
Collaborating with experienced measurement engineers can ensure that the chosen devices meet these requirements effectively.
Data Integration and Analysis
Post installation, integrating and managing the data from these sensors is the next step.
The data needs to be processed and analyzed with real-time analytics software, which provides actionable insights.
This process should be seamless to ensure that data is readily available for decision-making.
Training and Adaptation
Employees must be trained to use the new monitoring systems efficiently.
This includes understanding how to interpret the data and make data-driven decisions.
Moreover, the management must be willing to adapt processes based on the insights gained from the monitoring system.
Challenges in Real-Time Monitoring
Implementing real-time monitoring comes with its challenges, including:
Data Overload
With continuous monitoring come large volumes of data, which can be overwhelming to manage and analyze.
It is essential to employ robust data management systems to filter and prioritize the data effectively.
Upfront Costs
The initial cost of implementing real-time monitoring and measurement engineering can be significant.
However, these costs are often offset by the long-term savings achieved through increased efficiency and reduced waste.
Integration with Legacy Systems
Many manufacturing facilities operate with legacy systems that may not easily integrate with modern monitoring technologies.
This requires careful planning and potentially upgrading existing systems to be compatible with new technologies.
Conclusion
Optimizing production line monitoring through the integration of measurement engineering is a strategic move that offers numerous benefits.
Real-time monitoring enhances operational efficiency, supports predictive maintenance, and ensures improved product quality.
Though challenges exist, careful planning and execution can lead to successful implementation.
By continuously innovating and embracing advanced technologies, manufacturing operations can maintain a competitive edge in the ever-evolving industrial landscape.
The future of production efficiency lies in leveraging accurate, real-time data to make informed decisions and drive continuous improvement.
資料ダウンロード
QCD調達購買管理クラウド「newji」は、調達購買部門で必要なQCD管理全てを備えた、現場特化型兼クラウド型の今世紀最高の購買管理システムとなります。
ユーザー登録
調達購買業務の効率化だけでなく、システムを導入することで、コスト削減や製品・資材のステータス可視化のほか、属人化していた購買情報の共有化による内部不正防止や統制にも役立ちます。
NEWJI DX
製造業に特化したデジタルトランスフォーメーション(DX)の実現を目指す請負開発型のコンサルティングサービスです。AI、iPaaS、および先端の技術を駆使して、製造プロセスの効率化、業務効率化、チームワーク強化、コスト削減、品質向上を実現します。このサービスは、製造業の課題を深く理解し、それに対する最適なデジタルソリューションを提供することで、企業が持続的な成長とイノベーションを達成できるようサポートします。
オンライン講座
製造業、主に購買・調達部門にお勤めの方々に向けた情報を配信しております。
新任の方やベテランの方、管理職を対象とした幅広いコンテンツをご用意しております。
お問い合わせ
コストダウンが利益に直結する術だと理解していても、なかなか前に進めることができない状況。そんな時は、newjiのコストダウン自動化機能で大きく利益貢献しよう!
(Β版非公開)