- お役立ち記事
- Optimizing the Heat Treatment Process to Enhance Product Performance
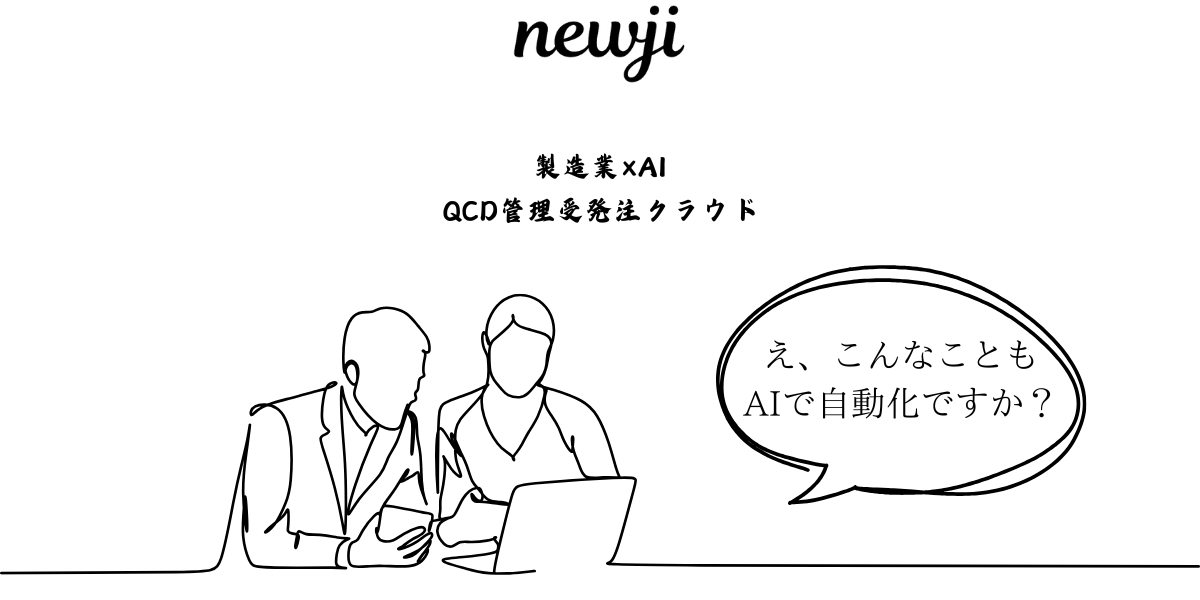
Optimizing the Heat Treatment Process to Enhance Product Performance
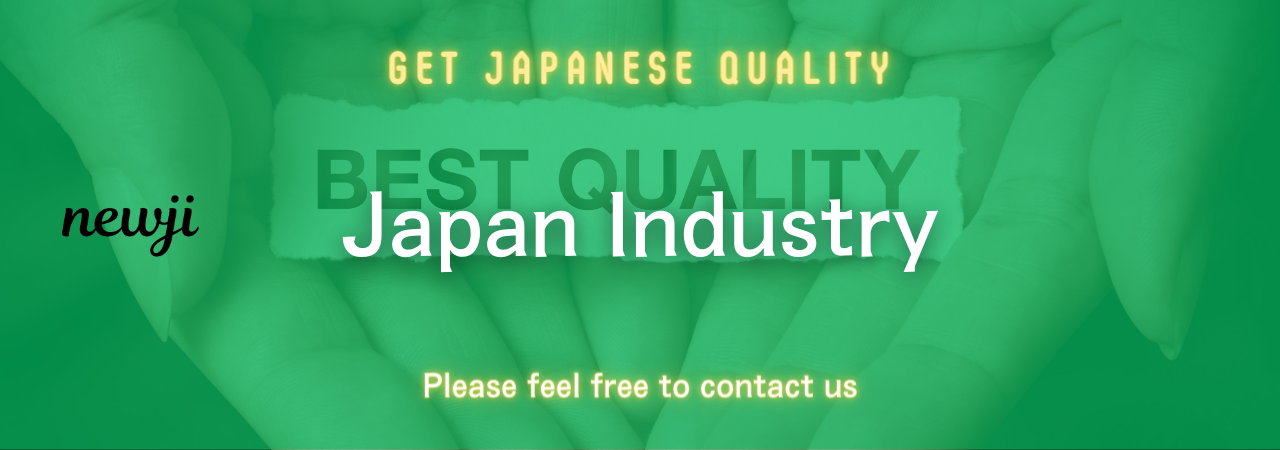
Manufacturing high-performance products often hinges on the heat treatment process.
Improper heat treatment can lead to suboptimal product qualities, such as brittleness or a reduced lifespan.
Optimizing this process can significantly enhance the durability, strength, and functionality of the materials.
This article delves into key strategies to refine the heat treatment process for superior product performance.
目次
Understanding the Basics of Heat Treatment
Heat treatment involves heating and cooling materials in a controlled manner to alter their physical and sometimes chemical properties.
Common heat treatment techniques include annealing, quenching, and tempering.
Each method serves a specific purpose, from softening metals to increasing their hardness.
Annealing
Annealing is a process used to soften metals, improving their ductility and reducing hardness.
This technique entails heating the material to a specific temperature, holding it there for a period, and then allowing it to cool gradually.
Annealed materials are easier to work with and are often used in forming processes.
Quenching
Quenching is a rapid cooling process used to increase the hardness of metals.
After heating the material to a high temperature, it is immediately cooled in a quenching medium such as water, oil, or air.
Though it makes the material harder, quenching can also make it more brittle.
Therefore, other processes like tempering are often required to balance hardness and ductility.
Tempering
Used mainly after quenching, tempering involves reheating the material to a lower temperature and then cooling it.
This reduces brittleness while retaining the hardness gained from quenching.
Tempered materials are more durable and can withstand stresses without breaking.
Critical Factors in Optimizing Heat Treatment
Fine-tuning the heat treatment process involves several critical factors, including temperature control, cooling methods, and material composition.
Let’s explore these in more detail:
Temperature Control
Accurate temperature control is crucial for successful heat treatment.
Incorrect temperatures can lead to undesirable material properties.
Advanced temperature monitoring systems and pyrometers can help maintain the precise heat levels needed for optimal treatment.
Cooling Rate
The rate at which a material is cooled directly affects its final properties.
Different cooling mediums (like oil, water, or air) and cooling rates can produce varied results.
For example, slower cooling often results in softer, more ductile materials, while faster cooling can provide harder, more brittle outcomes.
Material Composition
Different materials respond uniquely to heat treatment.
Therefore, understanding the composition of the material being treated is essential.
Certain alloys may require specific heat treatment protocols to achieve desired properties.
For instance, carbon steel and stainless steel need different tempering temperatures to reach optimal hardness.
Automation and Technology in Heat Treatment
Modern technological advancements have revolutionized the heat treatment process.
Automation and computerized systems can significantly improve the efficiency and accuracy of heat treatment operations.
Automated Heating Systems
Automated heating systems can maintain consistent temperatures and heating profiles, minimizing human error.
These systems can be programmed to follow specific heat treatment cycles, ensuring that the material is heated and cooled according to precise specifications.
Computerized Monitoring
Computerized monitoring tools allow for real-time analysis and adjustments to the heat treatment process.
These systems can detect any deviations from the desired heat treatment profile and make necessary adjustments automatically.
This capability ensures that the material properties meet stringent quality standards.
Energy Efficiency
Energy-efficient heating systems can reduce operational costs and environmental impact.
New technologies such as induction heating and advanced insulation materials can minimize energy consumption during the heat treatment process.
These innovations contribute to a more sustainable manufacturing process.
Best Practices for Enhanced Product Performance
Implementing best practices in heat treatment can lead to superior product performance.
Consistently applying these strategies ensures high-quality outcomes in every batch processed.
Routine Maintenance
Regular maintenance of heating equipment ensures stable operation and longevity.
Routine checks on heating elements, insulation, and cooling systems can prevent unexpected downtimes and ensure consistent quality.
Quality Control
Employing stringent quality control measures at every stage of the heat treatment process guarantees that the final product meets the required standards.
Periodic testing of treated materials can validate that they achieve the desired properties and perform optimally in their applications.
Training and Skill Enhancement
Continuous training for technicians on the latest heat treatment techniques and technologies is essential.
Skilled operators can better manage the heat treatment process, ensuring that materials achieve the desired properties efficiently.
Real-World Applications
Optimizing heat treatment has significant implications across various industries, from automotive to aerospace.
Automotive Industry
In the automotive sector, heat-treated components are crucial for safety and performance.
For instance, heat-treated gears and shafts have enhanced wear resistance and durability, contributing to the vehicle’s overall reliability.
Aerospace Industry
In aerospace, lightweight yet strong components are essential.
Heat treatment processes are optimized to produce parts that can withstand high stress and temperature variations, ensuring the safety and longevity of aerospace components.
Conclusion
Optimizing the heat treatment process is fundamental for enhancing product performance.
By understanding the basics of various heat treatment techniques, controlling critical factors, and leveraging modern technology, manufacturers can significantly improve material properties.
Implementing best practices ensures consistent quality and reliability, offering a competitive edge in demanding industries like automotive and aerospace.
Incorporating these strategies will lead to robust, durable, and high-performance products, meeting the diverse needs of today’s market.
資料ダウンロード
QCD調達購買管理クラウド「newji」は、調達購買部門で必要なQCD管理全てを備えた、現場特化型兼クラウド型の今世紀最高の購買管理システムとなります。
ユーザー登録
調達購買業務の効率化だけでなく、システムを導入することで、コスト削減や製品・資材のステータス可視化のほか、属人化していた購買情報の共有化による内部不正防止や統制にも役立ちます。
NEWJI DX
製造業に特化したデジタルトランスフォーメーション(DX)の実現を目指す請負開発型のコンサルティングサービスです。AI、iPaaS、および先端の技術を駆使して、製造プロセスの効率化、業務効率化、チームワーク強化、コスト削減、品質向上を実現します。このサービスは、製造業の課題を深く理解し、それに対する最適なデジタルソリューションを提供することで、企業が持続的な成長とイノベーションを達成できるようサポートします。
オンライン講座
製造業、主に購買・調達部門にお勤めの方々に向けた情報を配信しております。
新任の方やベテランの方、管理職を対象とした幅広いコンテンツをご用意しております。
お問い合わせ
コストダウンが利益に直結する術だと理解していても、なかなか前に進めることができない状況。そんな時は、newjiのコストダウン自動化機能で大きく利益貢献しよう!
(Β版非公開)