- お役立ち記事
- Overcoming the Digital Skills Gap in Manufacturing
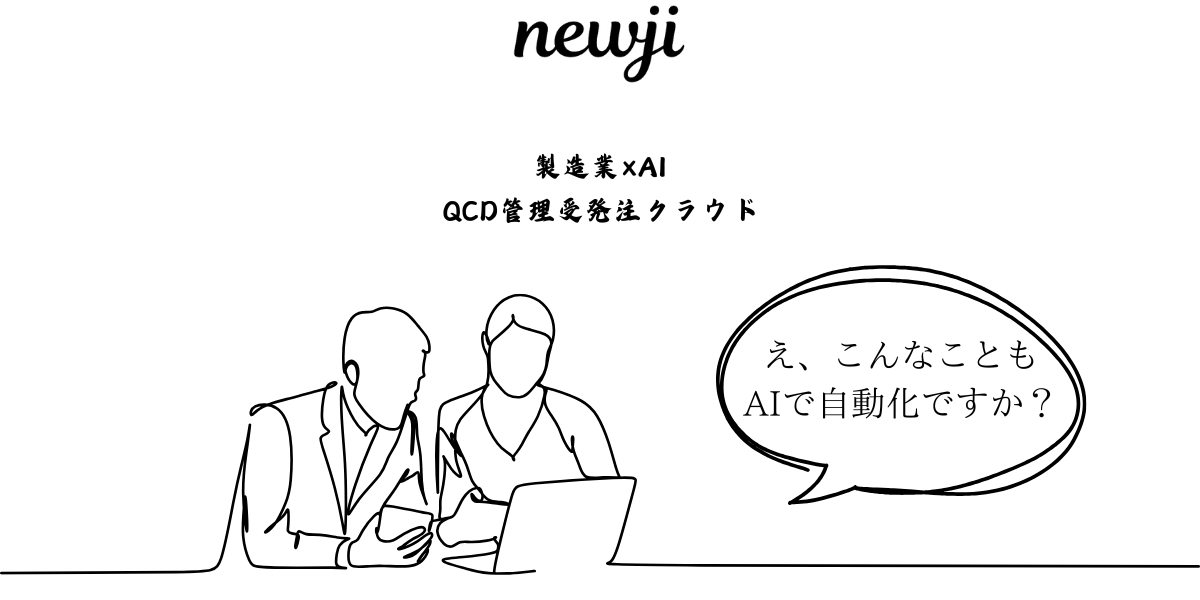
Overcoming the Digital Skills Gap in Manufacturing
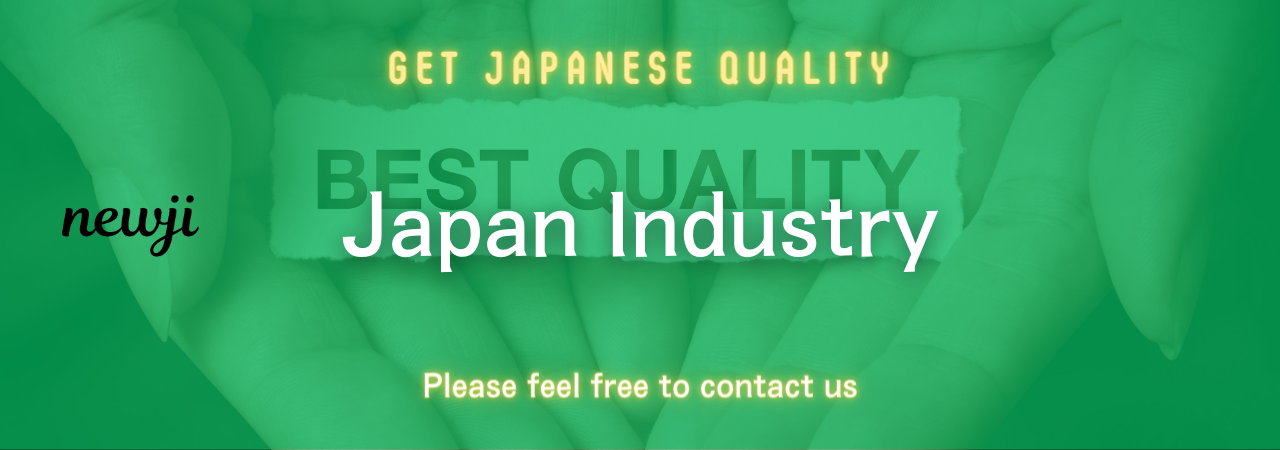
The manufacturing industry, once driven by manual labor and mechanical processes, is now increasingly propelled by digital technologies.
However, a significant challenge arises as the gap between the required digital skills and the current workforce capabilities widens.
Addressing this digital skills gap in manufacturing is essential to maintain competitiveness, enhance productivity, and foster innovation.
目次
Understanding the Digital Skills Gap
The digital skills gap in manufacturing refers to the disparity between the skills required to operate and leverage modern technologies and the skills currently possessed by the workforce.
This gap is fueled by rapid advancements in technologies such as automation, robotics, and data analytics.
Manufacturers need workers who can understand and manage these advanced systems to ensure smooth operations and continued innovation.
The Role of Advanced Technologies
In recent years, the manufacturing sector has embraced advanced technologies like Artificial Intelligence (AI), the Internet of Things (IoT), and machine learning.
These technologies streamline processes, enhance precision, and reduce operational costs.
However, the successful integration of these technologies depends on a workforce proficient in digital skills.
Traditional manual skills are no longer sufficient.
Identifying the Skills Needed
To bridge the digital skills gap, it is essential to identify the specific skills required.
These include data analysis, programming, system integration, cybersecurity, and digital literacy.
Employees must understand how to interact with digital tools, interpret data, and secure digital environments.
Without these skills, the industry cannot fully leverage the benefits of modern technologies.
Strategies to Overcome the Digital Skills Gap
Addressing the digital skills gap in manufacturing requires a multifaceted approach, including upskilling current employees, attracting new talent, and fostering a culture of continuous learning.
Upskilling Current Employees
One effective strategy is to invest in the development of the existing workforce.
This can be achieved through targeted training programs and on-the-job learning opportunities.
Workshops, online courses, and certifications can help employees acquire the necessary skills.
Employers should encourage and support their workers’ professional development by providing resources and time for training.
Attracting New Talent
Another approach is to attract new talent with the required digital skills.
This involves reshaping recruitment strategies to focus on candidates with strong technical backgrounds, such as those in STEM fields.
Collaborating with educational institutions to create internship and apprenticeship programs can also provide a pipeline of skilled workers.
Highlighting the opportunities for growth and innovation within the manufacturing sector can make it more appealing to tech-savvy individuals.
Fostering a Culture of Continuous Learning
A culture of continuous learning is vital to keep pace with technological advancements.
Employers should promote a mindset of ongoing education and adaptability.
Regularly updating training programs and encouraging curiosity and innovation can help maintain a skilled workforce.
Implementing mentorship programs where experienced employees can share knowledge and skills with newer recruits can also be beneficial.
The Role of Education and Industry Partnerships
Educational institutions and industry partnerships play a critical role in closing the digital skills gap.
Integrating Digital Skills into Curriculum
Educational institutions should integrate digital skills training into their curriculum, particularly in technical and vocational programs.
This ensures that graduates are prepared for the digital demands of the modern manufacturing environment.
Collaboration between educators and industry professionals can help keep curricula relevant and up-to-date.
Industry Partnerships
Partnerships between manufacturing companies and educational institutions can lead to the development of specialized training programs and certifications.
These programs can be tailored to the specific needs of the industry, ensuring that graduates have the necessary skills.
Internships, co-op programs, and real-world project opportunities provide students with practical experience, making them more job-ready.
Leveraging Technology for Training
Technology itself can be a powerful tool in addressing the digital skills gap.
Online Learning Platforms
Online learning platforms offer flexible and accessible training options for employees.
These platforms provide a wide range of courses, from basic digital literacy to advanced technical skills.
Employers can utilize these resources to create customized learning paths for their workforce, allowing employees to learn at their own pace.
Simulation and Virtual Reality
Simulation and virtual reality (VR) technologies offer immersive training experiences that can replicate real-world manufacturing scenarios.
These tools allow employees to practice skills and troubleshoot problems in a controlled environment.
Such training methodologies enhance understanding and retention, making employees more competent in handling digital technologies.
Measuring Progress and Adapting
It is crucial to measure the effectiveness of strategies aimed at closing the digital skills gap.
Regular Assessments
Regular assessments of employee skills and training programs help identify areas for improvement.
Surveys, tests, and performance evaluations can provide insights into the effectiveness of training initiatives.
Adjusting training programs based on feedback and assessment results ensures that the workforce continues to develop the necessary skills.
Keeping Up with Technological Advances
As technology continues to evolve, so must the skills of the workforce.
Continuous monitoring of technological trends and advancements is essential.
Employers should stay informed about emerging technologies and incorporate relevant training into their programs.
This proactive approach ensures that employees are always equipped with up-to-date skills.
In conclusion, overcoming the digital skills gap in manufacturing is a complex but essential task.
It requires a concerted effort from employers, educational institutions, and employees themselves.
By investing in training, attracting skilled talent, fostering a culture of continuous learning, and leveraging technology for education, the manufacturing industry can bridge the gap.
This will lead to enhanced productivity, innovation, and competitiveness in the digital age.
資料ダウンロード
QCD調達購買管理クラウド「newji」は、調達購買部門で必要なQCD管理全てを備えた、現場特化型兼クラウド型の今世紀最高の購買管理システムとなります。
ユーザー登録
調達購買業務の効率化だけでなく、システムを導入することで、コスト削減や製品・資材のステータス可視化のほか、属人化していた購買情報の共有化による内部不正防止や統制にも役立ちます。
NEWJI DX
製造業に特化したデジタルトランスフォーメーション(DX)の実現を目指す請負開発型のコンサルティングサービスです。AI、iPaaS、および先端の技術を駆使して、製造プロセスの効率化、業務効率化、チームワーク強化、コスト削減、品質向上を実現します。このサービスは、製造業の課題を深く理解し、それに対する最適なデジタルソリューションを提供することで、企業が持続的な成長とイノベーションを達成できるようサポートします。
オンライン講座
製造業、主に購買・調達部門にお勤めの方々に向けた情報を配信しております。
新任の方やベテランの方、管理職を対象とした幅広いコンテンツをご用意しております。
お問い合わせ
コストダウンが利益に直結する術だと理解していても、なかなか前に進めることができない状況。そんな時は、newjiのコストダウン自動化機能で大きく利益貢献しよう!
(Β版非公開)