- お役立ち記事
- Paperless Manufacturing Sites: How to Choose Digital Tools
Paperless Manufacturing Sites: How to Choose Digital Tools
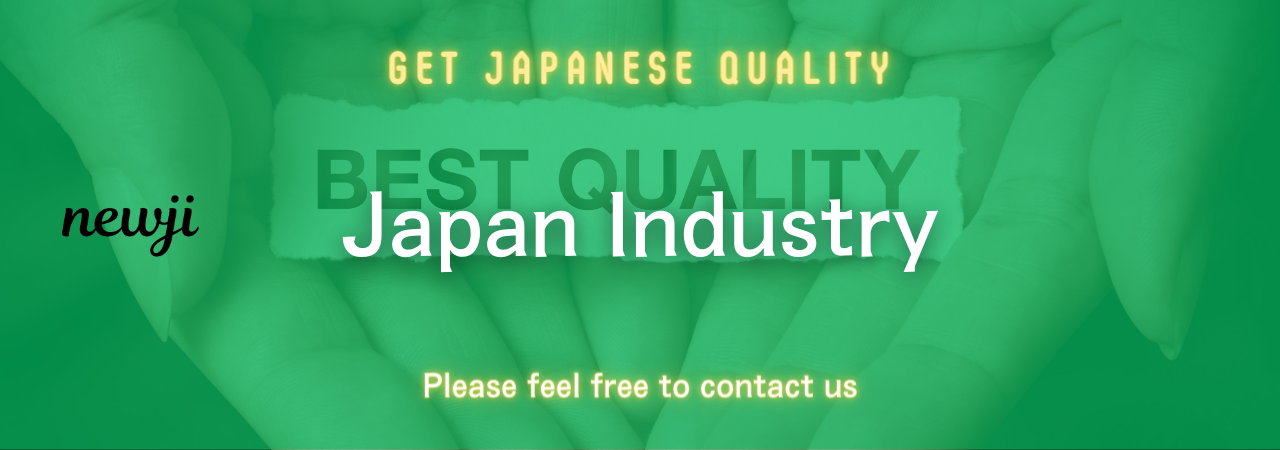
Today’s manufacturing sites are rapidly evolving with the integration of digital tools.
Going paperless is becoming an industry standard, as it promotes efficiency, reduces waste, and enhances productivity.
But how do you choose the right digital tools for a paperless manufacturing site?
This article will guide you through the process.
目次
Understanding the Benefits of Paperless Manufacturing
Before jumping into the selection process of digital tools, it is crucial to comprehend why paperless manufacturing sites are beneficial.
Firstly, it significantly reduces physical clutter.
With digital document management, all necessary information is accessible with a click.
This not only streamlines workflow but also minimizes errors associated with paper documentation.
Additionally, going paperless is environmentally friendly.
It lessens the carbon footprint associated with paper production and disposal.
Moreover, it leads to cost savings by eliminating the need for purchasing, printing, and storing paper documents.
Identifying Your Needs
The first step in selecting digital tools is to identify the specific needs of your manufacturing site.
Not every tool will be suitable for every operation.
Analyze Your Current Processes
Start by analyzing your current processes.
What areas generate the most paperwork?
Where are the bottlenecks in your workflow?
Identifying these aspects will help you determine which areas could benefit most from digitization.
Set Clear Goals
Once you have analyzed your processes, set clear goals for what you want to achieve.
Do you want to speed up production?
Reduce human error?
Enhance data accessibility?
Your goals will guide you in selecting the right digital tools.
Choosing the Right Software Solutions
There are various software solutions available for paperless manufacturing.
It is essential to choose one that aligns with your identified needs and goals.
Enterprise Resource Planning (ERP) Systems
ERP systems are powerful tools that integrate various functions like inventory management, production planning, and order processing.
They provide a centralized database that enhances accuracy and real-time data sharing.
Manufacturing Execution Systems (MES)
MES solutions focus on monitoring and controlling the production process.
They provide real-time updates on production status and performance, facilitating better decision-making and efficiency.
Document Management Systems (DMS)
DMS are crucial for a paperless environment.
They provide tools for storing, managing, and tracking electronic documents and images.
With features like version control and secure access, DMS ensure that the right people have access to the right documents at the right time.
Product Lifecycle Management (PLM)
PLM software helps manage the entire lifecycle of a product from inception to disposal.
It offers tools for collaboration, design, and change management, ensuring that all stakeholders are on the same page.
Considering Ease of Use and Integration
Choosing a digital tool also involves considering its ease of use and how well it integrates with your existing systems.
User-friendly interfaces are essential to ensure that your team can quickly adapt to the new tools.
Training and Support
Ensure that the provider offers adequate training and support.
This will help in the seamless transition from paper-based to digital processes.
Proper training ensures that your team can maximize the potential of the tools, leading to smoother operations.
Integration Capabilities
The tool should be compatible with your existing systems.
It should easily integrate without causing disruptions.
Interoperability is key to ensuring a cohesive and efficient digital ecosystem.
Focusing on Scalability and Customization
Your chosen digital tools should be scalable and customizable to cater to your growing and evolving needs.
Scalability
As your manufacturing site expands, the tools should be able to handle increased volumes of data and users.
Scalable software ensures that you do not have to replace systems frequently, thereby saving costs and disruptions.
Customization
Every manufacturing site has unique requirements.
Customizable software allows you to tailor the tools to your specific needs, ensuring that they provide maximum benefit.
Prioritizing Security and Compliance
In the digital age, data security is paramount.
Ensure that the tools you choose have robust security features to protect sensitive information.
Additionally, they should comply with industry standards and regulations.
Data Encryption and Access Control
Data encryption ensures that your data is safe from unauthorized access.
Access control features allow you to define who has access to what information, providing an additional layer of security.
Compliance with Regulations
Ensure that the tools comply with relevant industry standards and regulations.
This will help you avoid legal issues and penalties.
Compliance features also ensure that the tools are reliable and trustworthy.
Testing and Implementation
Before fully deploying a digital tool, it is advisable to test it on a small scale.
This helps identify any potential issues and allows for adjustments.
Pilot Testing
Conduct a pilot test to evaluate the tool’s performance in a real-world scenario.
Gather feedback from users and address any issues that arise during the test.
Phased Implementation
Implement the tools in phases to ensure that any potential problems can be managed without disrupting your entire operation.
Gradual implementation also allows for easier troubleshooting and fine-tuning.
Going paperless on your manufacturing site can significantly enhance efficiency, reduce waste, and improve overall productivity.
By understanding your needs, choosing the right software solutions, considering ease of use and integration, focusing on scalability and customization, prioritizing security and compliance, and conducting thorough testing, you can successfully transition to a paperless environment.
資料ダウンロード
QCD調達購買管理クラウド「newji」は、調達購買部門で必要なQCD管理全てを備えた、現場特化型兼クラウド型の今世紀最高の購買管理システムとなります。
ユーザー登録
調達購買業務の効率化だけでなく、システムを導入することで、コスト削減や製品・資材のステータス可視化のほか、属人化していた購買情報の共有化による内部不正防止や統制にも役立ちます。
NEWJI DX
製造業に特化したデジタルトランスフォーメーション(DX)の実現を目指す請負開発型のコンサルティングサービスです。AI、iPaaS、および先端の技術を駆使して、製造プロセスの効率化、業務効率化、チームワーク強化、コスト削減、品質向上を実現します。このサービスは、製造業の課題を深く理解し、それに対する最適なデジタルソリューションを提供することで、企業が持続的な成長とイノベーションを達成できるようサポートします。
オンライン講座
製造業、主に購買・調達部門にお勤めの方々に向けた情報を配信しております。
新任の方やベテランの方、管理職を対象とした幅広いコンテンツをご用意しております。
お問い合わせ
コストダウンが利益に直結する術だと理解していても、なかなか前に進めることができない状況。そんな時は、newjiのコストダウン自動化機能で大きく利益貢献しよう!
(Β版非公開)