- お役立ち記事
- Points to note when designing pressed products and molded products, and points to prevent rework
Points to note when designing pressed products and molded products, and points to prevent rework
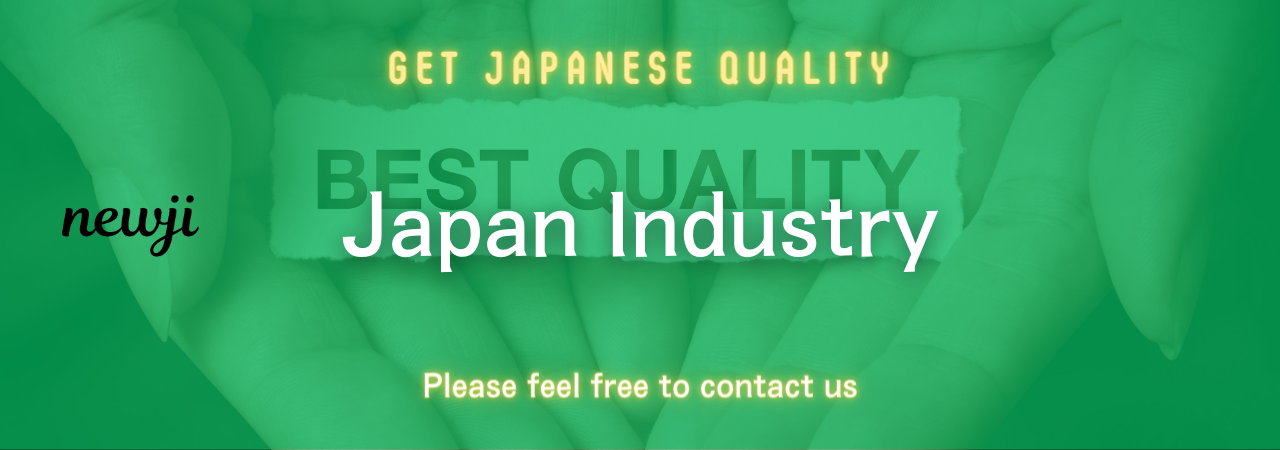
When it comes to designing pressed products and molded products, careful planning and attention to detail can significantly reduce the likelihood of rework.
Rework not only increases costs but can also delay production timelines, impacting the overall efficiency of a project.
Understanding the nuances involved in these design processes is crucial for achieving quality outcomes.
目次
Understanding Pressed Products and Molded Products
Pressed products and molded products are created using distinct manufacturing processes.
Pressed products are typically made by applying pressure to material in a die, while molded products are formed by shaping material in a mold.
Each method has its unique set of advantages, challenges, and applications.
Pressed Products
Pressed products often involve sheet metal fabrication, where sheets of metal are shaped into desired forms through pressing techniques.
This method is excellent for creating complex shapes with precision.
However, it requires an understanding of material properties, die design, and the appropriate application of force to ensure product integrity.
Molded Products
Molded products are often crafted from plastics, resins, or rubber, using processes like injection molding, blow molding, or compression molding.
These products benefit from the ability to produce uniform and intricate designs.
However, careful control of temperature, pressure, and cycle times is essential to prevent defects.
Key Design Considerations
Designing pressed and molded products requires attention to several key factors to minimize the risk of defects and rework.
Material Selection
Choosing the right material is fundamental.
For pressed products, consider the ductility, strength, and thickness of the metal.
Inappropriate material selection can lead to cracking or wrinkling.
For molded products, select materials that can withstand the molding process temperatures and pressures without deforming or degrading.
Tolerances and Dimensions
Accurate dimensions and tolerances are critical to ensure that parts fit together correctly.
Designers should account for material shrinkage during molding and potential deformation during pressing.
Adhering to specified tolerances reduces the risk of producing parts that require rework.
Draft Angles and Radii
In molded product design, incorporating appropriate draft angles allows for easy removal of the part from the mold, reducing the risk of damage or defects.
For pressed products, ensuring smooth transitions with adequate radii on edges reduces stress concentrations and potential fracture points.
Design for Manufacturability
Designing with manufacturability in mind can prevent many common issues.
Simple and Clear Design
Complicated designs increase the potential for error.
Simplicity should be prioritized while still achieving the necessary functionality.
Clear documentation and communication about design specifications also help manufacturers understand the requirements better.
Considering Production Capabilities
Understanding the capabilities and limitations of manufacturing equipment is important.
Designs should be tailored to suit the available technology and tools, taking into account their precision and capacity.
This alignment ensures that the production process is smooth and reduces the likelihood of rework.
Prototyping and Testing
Prototyping is a crucial step in the design process of pressed and molded products.
Creating Prototypes
Developing prototypes allows designers to test different materials, dimensions, and processes in real-time.
It helps in identifying potential problems early on, making adjustments before mass production.
Prototypes act as a proof of concept, saving time and resources in the long run.
Stress Testing and Quality Control
Before finalizing a design, subjecting prototypes to rigorous stress tests ensures they meet quality and durability standards.
Implementing a robust quality control process will identify defects before products reach customers, reducing the need for rework post-production.
Preventing Rework Through Continuous Improvement
Implementing strategies for continuous improvement can significantly minimize rework.
Feedback and Iteration
Incorporating feedback loops from manufacturing staff and customers allows for ongoing design refinement.
Each iteration provides insights that can lead to improved product quality and manufacturability.
Lean Manufacturing Principles
Adopting lean manufacturing principles can streamline processes and eliminate waste.
By continuously evaluating design and production processes, companies can identify inefficiencies and apply solutions that prevent rework.
Conclusion
Designing pressed and molded products requires a comprehensive understanding of materials, processes, and manufacturing capabilities.
By focusing on key design considerations, such as material selection, dimensions, and manufacturability, designers can greatly reduce the need for costly reworks.
Additionally, embracing prototyping, rigorous testing, and continuous improvement strategies ensures high-quality outcomes and efficient production.
With these best practices in place, manufacturers can create reliable and effective products that meet market demands efficiently.
資料ダウンロード
QCD調達購買管理クラウド「newji」は、調達購買部門で必要なQCD管理全てを備えた、現場特化型兼クラウド型の今世紀最高の購買管理システムとなります。
ユーザー登録
調達購買業務の効率化だけでなく、システムを導入することで、コスト削減や製品・資材のステータス可視化のほか、属人化していた購買情報の共有化による内部不正防止や統制にも役立ちます。
NEWJI DX
製造業に特化したデジタルトランスフォーメーション(DX)の実現を目指す請負開発型のコンサルティングサービスです。AI、iPaaS、および先端の技術を駆使して、製造プロセスの効率化、業務効率化、チームワーク強化、コスト削減、品質向上を実現します。このサービスは、製造業の課題を深く理解し、それに対する最適なデジタルソリューションを提供することで、企業が持続的な成長とイノベーションを達成できるようサポートします。
オンライン講座
製造業、主に購買・調達部門にお勤めの方々に向けた情報を配信しております。
新任の方やベテランの方、管理職を対象とした幅広いコンテンツをご用意しております。
お問い合わせ
コストダウンが利益に直結する術だと理解していても、なかなか前に進めることができない状況。そんな時は、newjiのコストダウン自動化機能で大きく利益貢献しよう!
(Β版非公開)