- お役立ち記事
- Practical Methods for SMEs to Succeed in Milling Processes
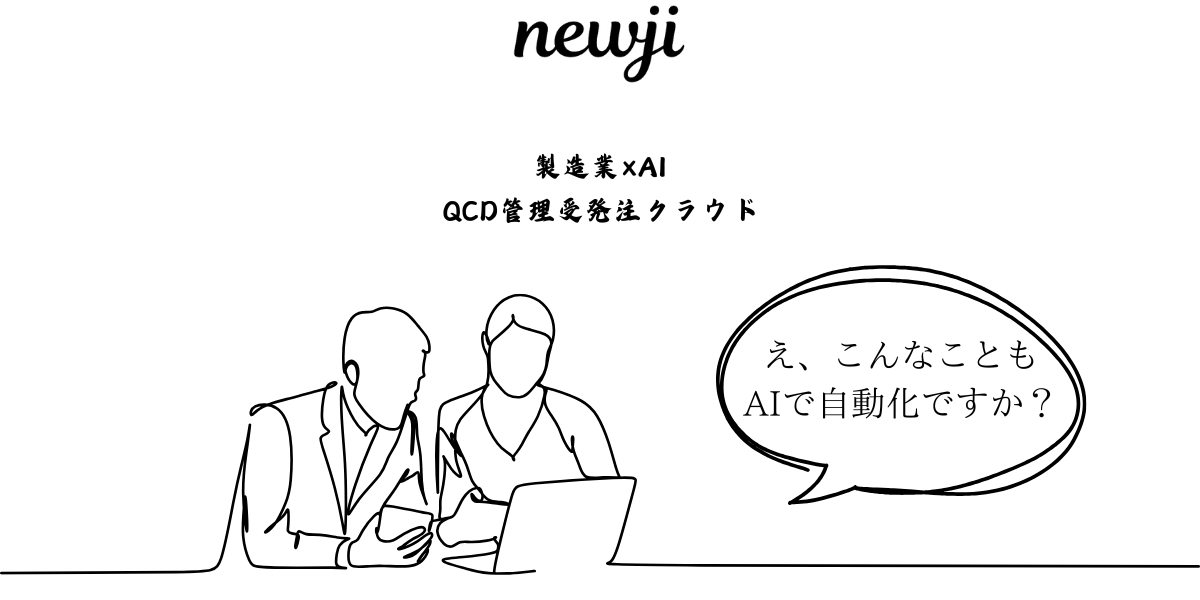
Practical Methods for SMEs to Succeed in Milling Processes
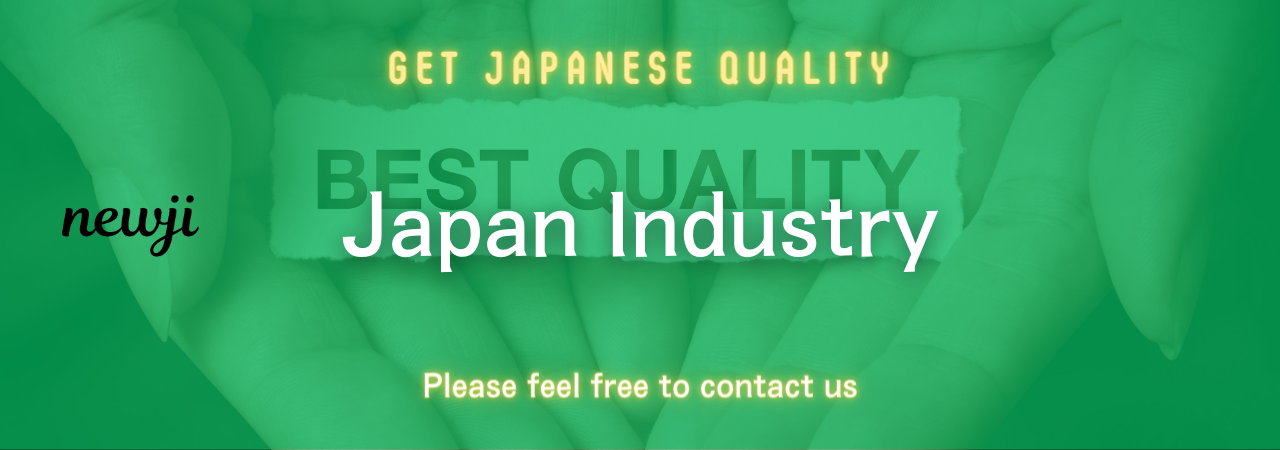
Milling processes are fundamental in many small and medium enterprises (SMEs) engaged in manufacturing.
These processes involve removing material from a workpiece using rotary cutters.
Efficiency and precision are of utmost importance, as these factors directly impact product quality and operational costs.
Here are some practical methods that will help SMEs succeed in their milling processes.
目次
Invest in High-Quality Milling Machines
The cornerstone of a successful milling operation is the milling machine.
Investing in high-quality equipment can significantly improve your efficiency and product quality.
While initial costs may be higher, the long-term benefits far outweigh these expenses.
Modern machines come with advanced features like CNC (Computer Numerical Control), which makes the operation more user-friendly and less prone to human error.
Benefits of CNC Machines
CNC machines provide several advantages.
They allow for precise control of milling operations, which results in better quality products.
They can also operate continuously, making them more efficient.
With CNC, you can reduce human error and labor costs considerably.
If you’re considering upgrading your milling machine, CNC technology should be at the top of your list.
Regular Maintenance and Calibration
Once you’ve invested in a high-quality milling machine, the next crucial step is regular maintenance.
Regular maintenance ensures your machine operates at optimal efficiency and extends its lifespan.
Calibration is equally important, as even the most advanced machines can lose precision over time.
Maintenance Tips
Regularly check all moving parts for wear and tear.
Lubricate components to ensure smooth operation.
Clean the machine to remove any debris that could interfere with its functioning.
Implementing a regular maintenance schedule can prevent unexpected downtimes and costly repairs.
Calibration Checklist
Measure the machine’s output regularly to ensure it’s producing parts within the desired tolerances.
Use standardized tools and gauges for accurate calibration.
Keep detailed records of your calibration activities to track performance over time.
Train Your Workforce
Even the best milling machine is only as good as the person operating it.
Proper training for your workforce is essential for maximizing the benefits of your equipment.
Invest in comprehensive training programs to educate your staff about machine operation, maintenance, and safety protocols.
Training Modules
Offer specific modules focused on different aspects of milling operations.
Start with basic machine operation, then move on to more advanced topics like CNC programming and maintenance.
Hands-on training is most effective, so make sure your staff gets plenty of practice.
Optimize Your Milling Processes
Process optimization is a continuous activity aimed at improving every aspect of your milling operations.
Use data analysis to identify bottlenecks and inefficiencies in your current processes.
Implement strategies to eliminate these bottlenecks and enhance overall efficiency.
Lean Manufacturing
One popular approach is Lean Manufacturing, which focuses on minimizing waste while maximizing productivity.
Techniques like 5S (Sort, Set in order, Shine, Standardize, Sustain) and Kaizen (continuous improvement) can be very effective.
Evaluate your current setup and identify areas where you can apply these techniques for improvement.
Automation
Consider automating repetitive tasks to save time and reduce human error.
Automation tools and software can handle tasks like material loading and unloading, measurement, and even quality control.
Integrating automation into your milling operations can significantly boost your efficiency and product quality.
Utilize Quality Materials
The quality of your finished product is greatly influenced by the quality of the raw materials you use.
Always opt for materials that meet your specifications and are consistent in quality.
Using subpar materials can lead to defects, increased waste, and greater operational costs.
Supplier Relationships
Establish strong relationships with reliable suppliers.
Communicate your quality requirements clearly and regularly perform quality checks on the received materials.
Having a reliable supply chain can make a substantial difference in your milling operations.
Implement Quality Control Systems
Quality control systems are essential for ensuring the precision and consistency of your milling operations.
Implement rigorous quality control checks at multiple stages of the production process.
Statistical Process Control (SPC)
Use SPC techniques to monitor and control your production processes.
These techniques involve collecting and analyzing data to detect and eliminate variances in the manufacturing process.
By implementing SPC, you can ensure that your products meet the required quality standards consistently.
Inspection Protocols
Create predefined inspection protocols for different stages of the milling process.
Make use of advanced measuring instruments like calipers, micrometers, and coordinate measuring machines (CMM) for precise measurements.
Regular inspections help in identifying and addressing issues before they escalate into major problems.
Leverage Technology and Software
Advancements in technology offer numerous tools and software designed to optimize milling processes.
Computer-Aided Manufacturing (CAM) software can be particularly beneficial.
CAM Software
CAM software helps in planning, managing, and controlling the milling operations.
These platforms can simulate the milling process, enabling you to identify and correct potential issues before they occur.
Integration of CAM software with your CNC machines can streamline operations and improve accuracy.
Monitor and Analyze Performance
Regular monitoring and analysis of your milling operations are essential for continuous improvement.
Use Key Performance Indicators (KPIs) to measure your efficiency and productivity.
KPIs to Track
Some important KPIs to consider include machine uptime, cycle time, scrap rate, and overall equipment effectiveness (OEE).
Regularly review these metrics and identify areas for improvement.
Use the insights gained to implement changes that enhance overall performance.
In conclusion, a combination of high-quality equipment, regular maintenance, workforce training, process optimization, quality materials, quality control systems, and leveraging technology can significantly improve the success of milling processes in SMEs.
By focusing on these areas, small and medium enterprises can achieve higher efficiency, better product quality, and reduced operational costs.
Consistently applying these practical methods will pave the way for sustained success in your milling operations.
資料ダウンロード
QCD調達購買管理クラウド「newji」は、調達購買部門で必要なQCD管理全てを備えた、現場特化型兼クラウド型の今世紀最高の購買管理システムとなります。
ユーザー登録
調達購買業務の効率化だけでなく、システムを導入することで、コスト削減や製品・資材のステータス可視化のほか、属人化していた購買情報の共有化による内部不正防止や統制にも役立ちます。
NEWJI DX
製造業に特化したデジタルトランスフォーメーション(DX)の実現を目指す請負開発型のコンサルティングサービスです。AI、iPaaS、および先端の技術を駆使して、製造プロセスの効率化、業務効率化、チームワーク強化、コスト削減、品質向上を実現します。このサービスは、製造業の課題を深く理解し、それに対する最適なデジタルソリューションを提供することで、企業が持続的な成長とイノベーションを達成できるようサポートします。
オンライン講座
製造業、主に購買・調達部門にお勤めの方々に向けた情報を配信しております。
新任の方やベテランの方、管理職を対象とした幅広いコンテンツをご用意しております。
お問い合わせ
コストダウンが利益に直結する術だと理解していても、なかなか前に進めることができない状況。そんな時は、newjiのコストダウン自動化機能で大きく利益貢献しよう!
(Β版非公開)