- お役立ち記事
- Precautions to Prevent Mold Design Failures in Injection Molding
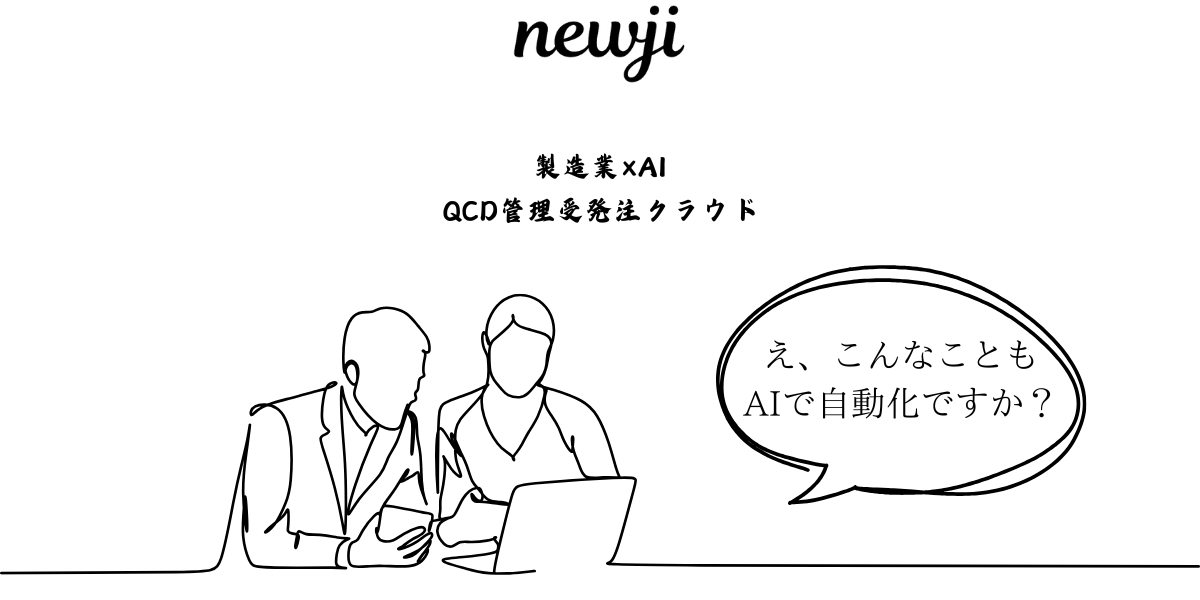
Precautions to Prevent Mold Design Failures in Injection Molding
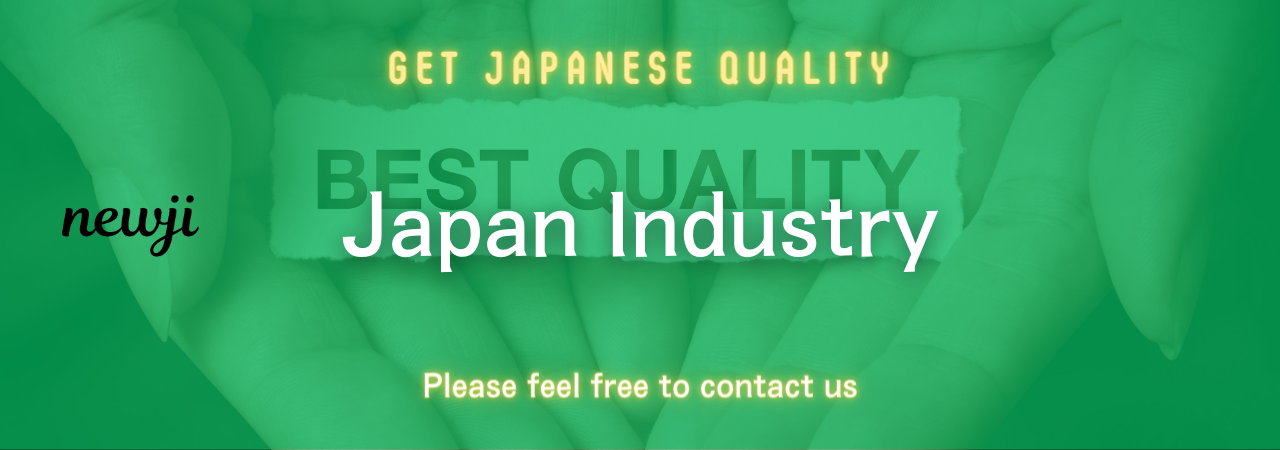
目次
Understanding Mold Design in Injection Molding
Injection molding is a popular manufacturing process used to produce plastic parts for a wide range of industries.
It involves injecting molten material into a mold cavity, where it cools and solidifies into the desired shape.
A critical aspect of this process is the mold design, which can significantly affect the quality and consistency of the final product.
The design of the mold must be carefully considered to prevent potential failures.
This involves understanding the properties of the material being used, the operational parameters, and the desired specifications of the product.
Proper mold design can reduce waste, improve efficiency, and enhance product quality.
The Importance of Precision in Mold Design
Precision in mold design is crucial for successful injection molding.
An incorrectly designed mold can lead to a variety of defects, such as warping, sink marks, or incomplete filling.
These defects can result in rejected parts and increased costs due to material waste and time lost in correcting issues.
Moreover, precise mold design ensures that the dimensions and features of the final product meet the required specifications.
It helps maintain structural integrity and functionality, essential for parts used in sensitive applications, such as automotive or medical industries.
Common Mold Design Failures
Mold design failures can manifest in several ways, impacting production efficiency and product quality.
Understanding these common failures helps in taking preventive measures.
1. Warping and Distortion
Warping occurs when different areas of the molded part cool at different rates, causing it to bend or twist.
This can result from uneven mold cooling or improper design that doesn’t account for material shrinkage.
2. Parting Line Mismatches
A parting line is where two halves of the mold meet.
If the mold is not designed accurately, a visible line or mismatch may appear on the final product, affecting its appearance and function.
3. Sink Marks and Voids
Sink marks are depressions that occur in thicker areas of the part.
They happen when the material continues to shrink after the surface has solidified.
Void defects are similar but appear as empty spaces within the part.
Both issues arise from inefficient mold design, poor gate placement, or inadequate cooling.
Precautions to Prevent Mold Design Failures
Preventing mold design failures involves a combination of proper planning, precise execution, and continuous monitoring.
Here are some essential precautions:
1. Conduct Thorough Material Analysis
Understanding the material properties is fundamental to mold design.
Conduct tests to determine shrinkage rates, flow characteristics, and thermal properties.
This information guides the design process, ensuring it accommodates material-specific behaviors and prevents defects like warping or sink marks.
2. Implement Efficient Cooling Systems
Effective mold cooling is crucial for maintaining dimensional accuracy and preventing defects.
Design cooling channels to ensure uniform cooling throughout the mold.
This strategy minimizes the risk of warping and reduces cycle times, leading to increased productivity.
3. Optimize Mold Venting
Proper venting ensures that air trapped within the mold cavity can escape during the injection.
Inadequate venting can cause air pockets or burn marks on the part, leading to defects.
Design appropriate venting systems based on the complexity and size of the part.
4. Design for Uniform Wall Thickness
Maintaining a consistent wall thickness helps in reducing the risk of warping and sink marks.
Design the mold with consistent thickness to promote even cooling and shrinkage.
Consider incorporating ribs or gussets to add strength without adding unnecessary thickness.
5. Utilize Simulation Software
Simulation software can predict how the material will behave during the injection process.
It helps identify potential issues in mold design before physical production begins.
Use simulations to test different scenarios and optimize the mold design accordingly.
Collaboration and Communication Among Teams
Successful mold design also relies on effective collaboration among design engineers, material specialists, and manufacturers.
Transparent communication ensures that all teams have a unified vision of the product specifications and process parameters.
Regular meetings and updates among the teams help address any concerns or changes in the design process promptly.
Fostering a culture of open communication reduces the risk of errors and enhances the overall quality of production.
The Role of Quality Assurance
Quality assurance plays a pivotal role in detecting and preventing mold design failures.
Conduct careful inspections and tests on sample moldings to detect defects early.
Utilize advanced measurement tools and techniques to ensure precision in every part produced.
By maintaining strict quality control procedures, manufacturers can promptly identify any design flaws, allowing for quick adjustments.
This step is essential in mitigating costly errors that could disrupt production.
Conclusion
Mold design is a critical element in the success of the injection molding process.
By understanding the common failures and implementing effective precautions, manufacturers can improve product quality and operational efficiency.
Attention to detail, precise execution, and continuous collaboration among teams are key to preventing mold design failures.
With careful planning and adopting innovative tools and technologies, businesses can significantly reduce risks and maintain a competitive edge in the dynamic manufacturing landscape.
資料ダウンロード
QCD調達購買管理クラウド「newji」は、調達購買部門で必要なQCD管理全てを備えた、現場特化型兼クラウド型の今世紀最高の購買管理システムとなります。
ユーザー登録
調達購買業務の効率化だけでなく、システムを導入することで、コスト削減や製品・資材のステータス可視化のほか、属人化していた購買情報の共有化による内部不正防止や統制にも役立ちます。
NEWJI DX
製造業に特化したデジタルトランスフォーメーション(DX)の実現を目指す請負開発型のコンサルティングサービスです。AI、iPaaS、および先端の技術を駆使して、製造プロセスの効率化、業務効率化、チームワーク強化、コスト削減、品質向上を実現します。このサービスは、製造業の課題を深く理解し、それに対する最適なデジタルソリューションを提供することで、企業が持続的な成長とイノベーションを達成できるようサポートします。
オンライン講座
製造業、主に購買・調達部門にお勤めの方々に向けた情報を配信しております。
新任の方やベテランの方、管理職を対象とした幅広いコンテンツをご用意しております。
お問い合わせ
コストダウンが利益に直結する術だと理解していても、なかなか前に進めることができない状況。そんな時は、newjiのコストダウン自動化機能で大きく利益貢献しよう!
(Β版非公開)