- お役立ち記事
- “Preventive Measures for Quality Problems”—Specific quality control methods required by management at the workplace
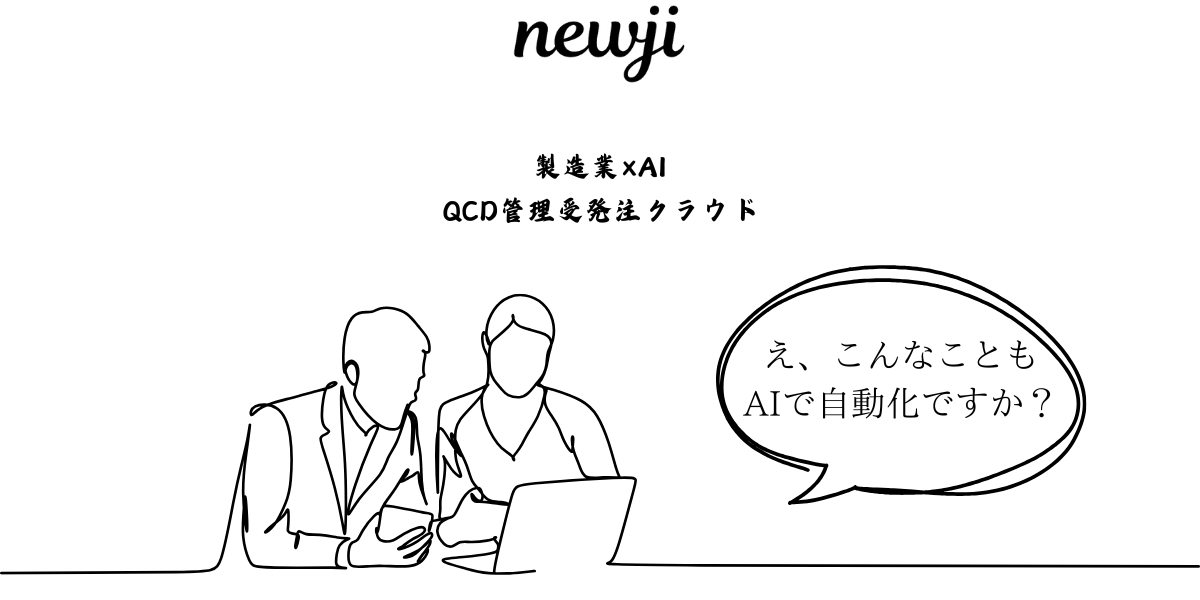
“Preventive Measures for Quality Problems”—Specific quality control methods required by management at the workplace
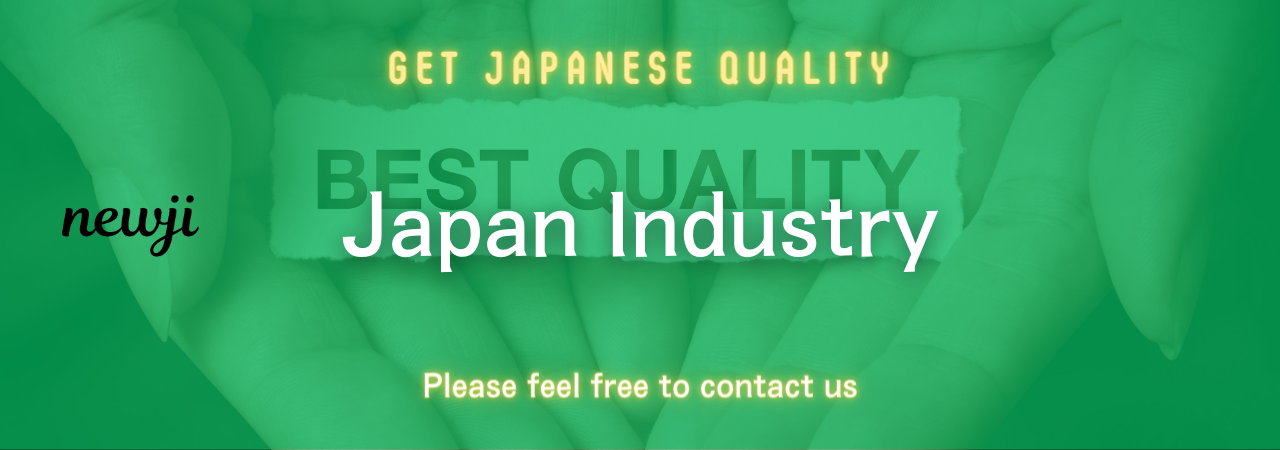
目次
Introduction to Quality Control
Quality control is essential for any business that aims to deliver high-standard products and services to its customers.
Ensuring quality in every phase of production and service delivery requires a systematic approach to prevent problems before they occur.
By implementing effective quality control measures, companies can improve customer satisfaction, reduce waste, and increase efficiency.
This article will discuss specific quality control methods that management can enforce at the workplace to prevent quality problems.
Understanding Quality Problems
Before diving into preventive measures, it’s important to understand what a quality problem is.
Quality problems occur when a product or service does not meet the established standards of performance, reliability, or design.
These issues can arise from various factors such as faulty materials, human error, inadequate processes, or insufficient training.
Identifying potential sources of quality issues is the first step toward preventing them.
The Role of Management in Quality Control
Management plays a critical role in establishing and maintaining a culture of quality within an organization.
By setting clear quality objectives and providing the necessary resources and training, managers can foster an environment where quality is prioritized.
Management also needs to implement structured quality control systems and ensure continuous monitoring and improvement of processes.
Implementing Preventive Quality Control Measures
1. Develop a Comprehensive Quality Management System (QMS)
A Quality Management System (QMS) helps maintain consistent quality standards across all operational areas.
Management should develop a QMS that is tailored to the specific needs of their industry and company size.
This system should include clear documentation of processes, procedures, and responsibilities.
An effective QMS integrates quality planning, quality assurance, and quality improvement measures to prevent problems from arising.
2. Conduct Regular Training and Development Programs
Well-trained employees are crucial in preventing quality issues.
Management should invest in regular training programs to ensure that staff are knowledgeable about quality standards, procedures, and best practices.
Training should cover both technical skills and quality management principles.
Additionally, encouraging ongoing professional development helps employees stay informed about new technologies and methodologies that can enhance quality.
3. Employ Statistical Process Control (SPC)
Statistical process control (SPC) involves using statistical methods to monitor and control production processes.
By analyzing data collected from production lines, SPC can help identify trends, patterns, and variations that may indicate potential quality issues.
Management should implement SPC tools and techniques, such as control charts, to detect deviations early and make necessary adjustments before problems escalate.
4. Implement Total Quality Management (TQM) Principles
Total Quality Management (TQM) is a holistic approach to long-term success through customer satisfaction.
It involves continuous improvement of processes, products, and services by involving all employees in quality control efforts.
Management should create a culture that supports TQM by promoting open communication, teamwork, and employee involvement in decision-making.
This approach encourages employees at all levels to identify areas for improvement and contribute to the overall quality goals of the company.
5. Perform Regular Audits and Inspections
Routine audits and inspections are critical for maintaining high quality standards.
They help ensure that processes are followed correctly and consistently.
Management should schedule regular internal and external audits to assess compliance with quality requirements and identify areas needing improvement.
Inspections should cover raw materials, work-in-progress, and finished products to catch any deviations from quality standards early.
6. Use Failure Mode and Effects Analysis (FMEA)
Failure Mode and Effects Analysis (FMEA) is a proactive approach to identify and mitigate risks associated with potential failures in products or processes.
By conducting FMEA, management can preemptively address weaknesses and implement controls to reduce the likelihood of defects.
It involves analyzing failure modes, their causes, and effects, and prioritizing actions based on severity, occurrence, and detectability scores.
Benefits of Preventive Quality Control Measures
By implementing preventive quality control measures, companies can enjoy numerous benefits.
These include enhanced product quality and reliability, cost savings from reduced waste and rework, improved customer satisfaction, and a stronger competitive position in the market.
Additionally, a focus on prevention supports a positive work culture where employees feel empowered to contribute to quality improvements.
Conclusion
In conclusion, preventing quality problems requires a strategic approach backed by management commitment and employee involvement.
Through developing a comprehensive QMS, investing in training, employing statistical tools, embracing TQM principles, conducting regular audits, and using FMEA, companies can effectively prevent quality issues.
These measures not only safeguard product and service quality but also drive continuous improvement and innovation.
By prioritizing quality control, businesses can build a reputation for excellence and achieve long-term success in their industries.
資料ダウンロード
QCD調達購買管理クラウド「newji」は、調達購買部門で必要なQCD管理全てを備えた、現場特化型兼クラウド型の今世紀最高の購買管理システムとなります。
ユーザー登録
調達購買業務の効率化だけでなく、システムを導入することで、コスト削減や製品・資材のステータス可視化のほか、属人化していた購買情報の共有化による内部不正防止や統制にも役立ちます。
NEWJI DX
製造業に特化したデジタルトランスフォーメーション(DX)の実現を目指す請負開発型のコンサルティングサービスです。AI、iPaaS、および先端の技術を駆使して、製造プロセスの効率化、業務効率化、チームワーク強化、コスト削減、品質向上を実現します。このサービスは、製造業の課題を深く理解し、それに対する最適なデジタルソリューションを提供することで、企業が持続的な成長とイノベーションを達成できるようサポートします。
オンライン講座
製造業、主に購買・調達部門にお勤めの方々に向けた情報を配信しております。
新任の方やベテランの方、管理職を対象とした幅広いコンテンツをご用意しております。
お問い合わせ
コストダウンが利益に直結する術だと理解していても、なかなか前に進めることができない状況。そんな時は、newjiのコストダウン自動化機能で大きく利益貢献しよう!
(Β版非公開)