- お役立ち記事
- Proposal and implementation to support purchasing department in stabilizing material supply
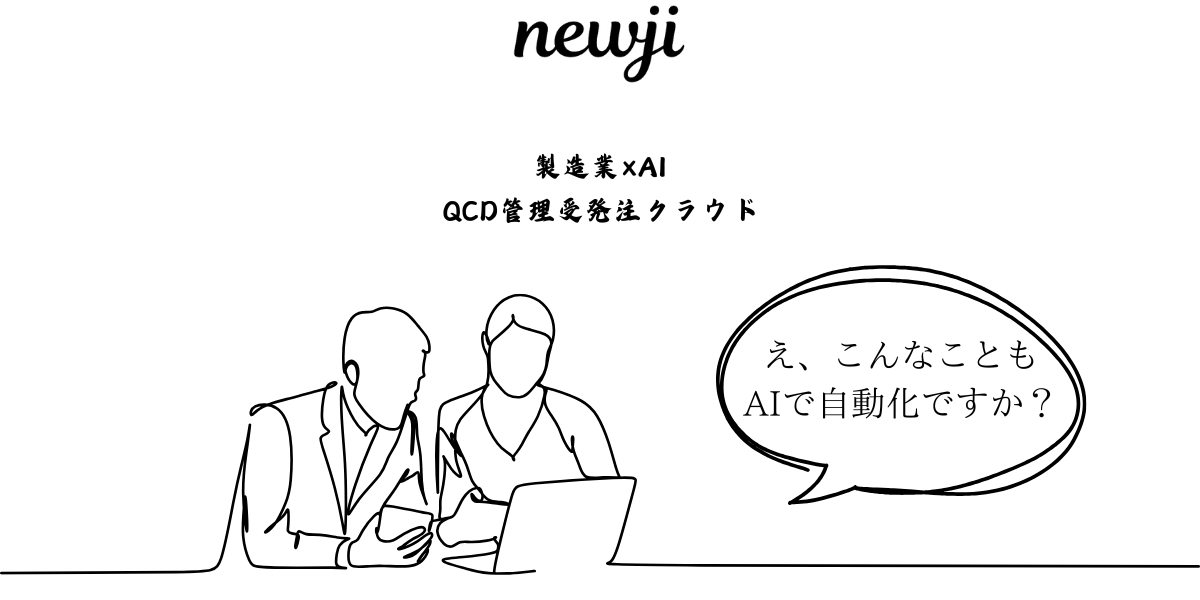
Proposal and implementation to support purchasing department in stabilizing material supply
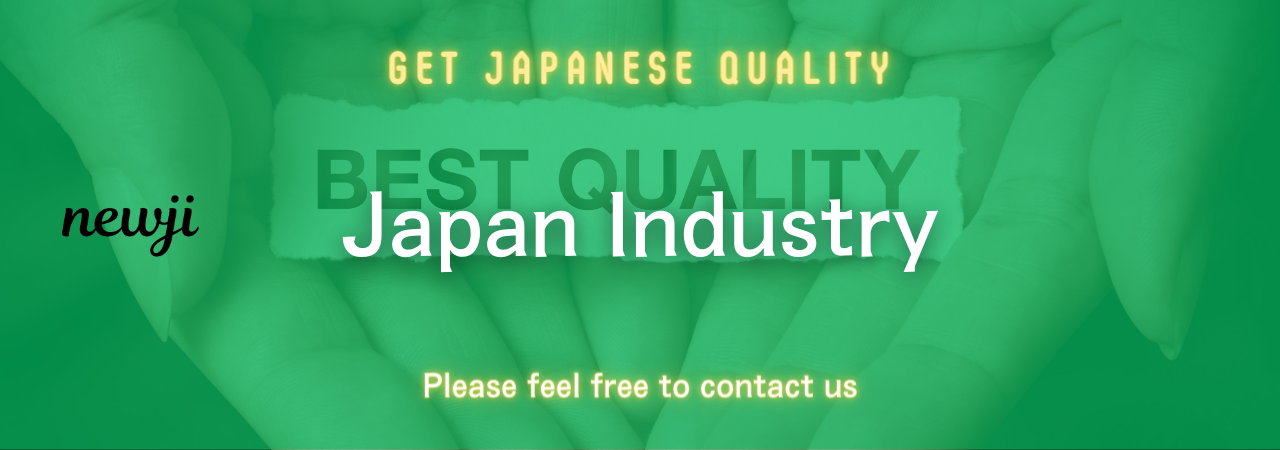
目次
Understanding the Challenge
The role of a purchasing department is crucial in any organization, especially when it comes to stabilizing material supply.
A stable supply chain ensures a continuous flow of materials, enabling production processes to run smoothly without interruptions.
However, achieving this stability can be challenging due to various factors such as supplier reliability, market fluctuations, and logistical hurdles.
Stabilizing material supply is essential not only for maintaining production efficiency but also for controlling costs.
Interruptions can lead to significant operational disruptions and financial losses.
To address these challenges, companies must adopt strategies and approaches that support their purchasing department in ensuring a steady material supply.
Developing a Strategic Approach
The first step toward stabilizing material supply is developing a strategic approach.
This involves understanding both the internal and external factors impacting supply chain stability.
Internal factors include the company’s inventory policies, procurement processes, and supplier relationships.
External factors encompass market dynamics, geopolitical influences, and technological changes.
By analyzing these factors, companies can identify potential risks and develop strategies that mitigate these risks effectively.
For instance, building strong relationships with key suppliers can enhance reliability and responsiveness, while diversifying the supplier base can reduce dependency on a single source and minimize risk.
Leveraging Technology for Better Forecasting
Technology plays an integral role in supporting the purchasing department.
One effective way to stabilize material supply is by leveraging advanced forecasting tools.
These tools use data analytics and artificial intelligence to predict demand patterns and market trends, enabling purchasing teams to make informed decisions.
With accurate forecasting, companies can adjust their procurement strategies proactively.
This means ordering materials in a timely manner, avoiding overstocking or understocking, and ultimately maintaining a consistent supply flow.
Moreover, technology can facilitate better communication and collaboration with suppliers, ensuring transparency and efficiency in the supply chain.
Enhancing Supplier Relationships
Strong supplier relationships are the backbone of a stable supply chain.
By fostering open communication and transparency, companies can build trust and reliability with their suppliers.
Regular performance evaluations and feedback sessions can help both parties understand expectations and address any issues promptly.
Additionally, establishing long-term partnerships with suppliers provides an opportunity to work collaboratively on improving supply chain processes.
This can involve joint efforts in cost-saving initiatives, quality improvements, and risk management strategies.
Collaborative relationships often result in better service levels and dependable material delivery, ultimately supporting the purchasing department in stabilizing supply.
Risk Management and Contingency Planning
Risk management is a critical aspect of supply chain stability.
Unexpected disruptions such as natural disasters, political instability, or supplier defaults can severely impact the supply of materials.
Therefore, it is vital for purchasing departments to have contingency plans in place.
Contingency planning involves identifying potential risks and developing strategies to respond effectively.
This may include having alternative suppliers, maintaining safety stock, or implementing flexible logistics arrangements.
By being prepared for unforeseen events, companies can minimize disruptions and continue their operations seamlessly.
Optimizing Inventory Management
Optimal inventory management is another key factor in stabilizing material supply.
Purchasing departments must balance the cost of holding inventory with the risk of running out of critical materials.
Implementing inventory management systems can help monitor stock levels, track usage patterns, and automate reordering processes.
Just-in-time (JIT) inventory systems, for example, can reduce waste and storage costs by aligning production schedules with delivery times.
On the other hand, maintaining a buffer stock of essential materials can protect against supply chain interruptions.
Finding the right balance is crucial for ensuring material availability while minimizing unnecessary expenses.
Continuous Monitoring and Improvement
Stabilizing material supply is not a one-time effort; it requires continuous monitoring and improvement.
By regularly reviewing supply chain performance metrics, purchasing departments can identify areas for enhancement and implement necessary changes.
Key performance indicators (KPIs) such as supplier lead times, order accuracy, and fulfillment rates provide valuable insights into supply chain efficiency.
By analyzing these metrics, companies can make data-driven decisions to strengthen their supply chain and support the purchasing department in maintaining consistent material supply.
Conclusion
Stabilizing material supply is a complex yet essential task for purchasing departments.
By adopting a strategic approach that includes leveraging technology, enhancing supplier relationships, optimizing inventory management, and implementing effective risk management and contingency planning, organizations can achieve greater supply chain stability.
Continuous monitoring and improvement further ensure that the purchasing department is well-equipped to handle challenges and maintain a steady flow of materials.
This not only supports operational efficiency but also drives overall business success.
資料ダウンロード
QCD調達購買管理クラウド「newji」は、調達購買部門で必要なQCD管理全てを備えた、現場特化型兼クラウド型の今世紀最高の購買管理システムとなります。
ユーザー登録
調達購買業務の効率化だけでなく、システムを導入することで、コスト削減や製品・資材のステータス可視化のほか、属人化していた購買情報の共有化による内部不正防止や統制にも役立ちます。
NEWJI DX
製造業に特化したデジタルトランスフォーメーション(DX)の実現を目指す請負開発型のコンサルティングサービスです。AI、iPaaS、および先端の技術を駆使して、製造プロセスの効率化、業務効率化、チームワーク強化、コスト削減、品質向上を実現します。このサービスは、製造業の課題を深く理解し、それに対する最適なデジタルソリューションを提供することで、企業が持続的な成長とイノベーションを達成できるようサポートします。
オンライン講座
製造業、主に購買・調達部門にお勤めの方々に向けた情報を配信しております。
新任の方やベテランの方、管理職を対象とした幅広いコンテンツをご用意しております。
お問い合わせ
コストダウンが利益に直結する術だと理解していても、なかなか前に進めることができない状況。そんな時は、newjiのコストダウン自動化機能で大きく利益貢献しよう!
(Β版非公開)