- お役立ち記事
- Prototype development using 3D printing that new leaders of design departments in the medical device manufacturing industry should know
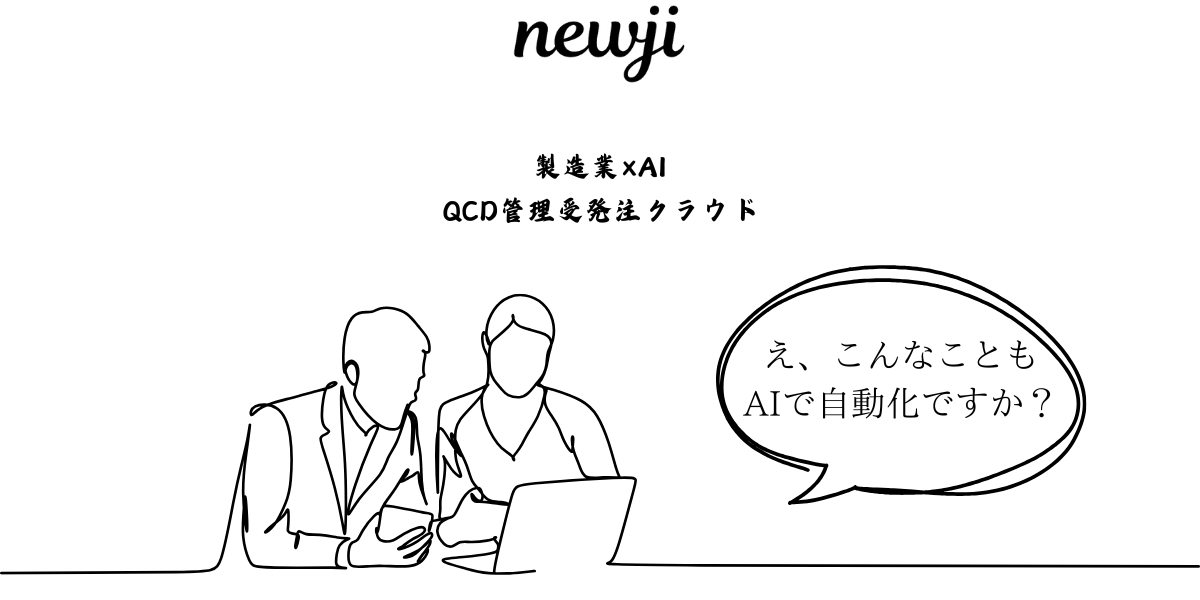
Prototype development using 3D printing that new leaders of design departments in the medical device manufacturing industry should know
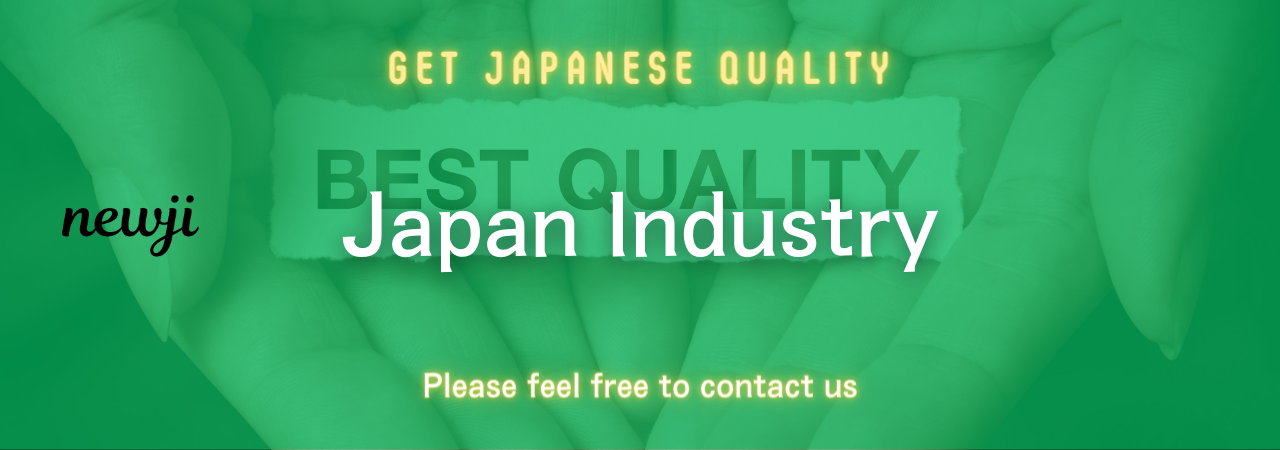
目次
Understanding 3D Printing for Prototype Development
3D printing, or additive manufacturing, has revolutionized product development across various industries, including medical device manufacturing.
As a new leader in a design department, it is essential to understand the role of 3D printing in prototype development.
This technology enables the creation of complex geometries and intricate designs that are often impossible with traditional manufacturing methods.
3D printing allows for rapid prototyping, which is particularly beneficial in the medical field where innovation and time-to-market are critical.
By using 3D printers, design teams can produce prototypes quickly and efficiently, facilitating faster iterations based on intuitive feedback and testing results.
The Benefits of 3D Printing in Medical Device Design
There are several advantages to integrating 3D printing into the prototype development process for medical devices.
Faster Development Cycles
One of the most significant benefits of 3D printing is the ability to shorten development cycles.
With traditional methods, creating a prototype can take weeks or even months.
However, 3D printing can significantly reduce this time by allowing for instantaneous adjustments and rapid production of new iterations.
This acceleration enables design teams to test multiple versions of a prototype quickly, thus identifying the best solutions in a shorter time frame.
Cost-Effectiveness
3D printing can be more cost-effective than traditional manufacturing techniques, especially for low-volume production or custom parts.
It eliminates the need for expensive molds and tooling, which can be particularly advantageous when developing medical devices where precision and customization are paramount.
By reducing material waste and streamlining production, 3D printing helps keep costs down while maintaining high-quality standards.
Complexity and Customization
3D printing excels in producing highly complex structures that would be difficult or impossible to achieve with conventional methods.
This capability is particularly beneficial for the medical device industry, where products often require intricate designs and structures tailor-made for specific patient needs.
Custom implants, prosthetics, and dental devices can be designed and produced to exact specifications, enhancing patient outcomes and satisfaction.
Enhanced Collaboration
The rapid prototyping capabilities provided by 3D printing facilitate greater collaboration among design teams.
Realistic prototypes that closely resemble the final product allow for more effective communication between engineers, designers, and medical professionals.
This enhanced collaboration leads to better decision-making and faster problem-solving, ensuring that the final product meets both technical and clinical requirements.
Challenges of 3D Printing in Medical Device Prototype Development
Despite its many benefits, 3D printing also poses certain challenges that must be addressed by leaders in design departments.
Material Limitations
The range of materials available for 3D printing is still comparatively limited, especially in terms of biocompatibility and durability necessary for medical devices.
While advancements are continually being made, it’s crucial for design teams to stay informed about the latest material developments to ensure their prototypes meet all required standards.
Regulatory Compliance
Medical devices are subject to stringent regulations, which can complicate the use of 3D printing in prototype development.
Understanding and adhering to regulatory requirements is essential to ensure that prototypes can be successfully transitioned to final production.
Design leaders need to ensure their teams are familiar with the relevant regulations and can incorporate compliance checks throughout the prototyping process.
Quality Control
Achieving consistent quality in 3D-printed prototypes can be challenging.
Variability in printing conditions, such as temperature and humidity, can result in differences between prints, affecting the accuracy and functionality of prototypes.
Implementing robust quality control processes is necessary to ensure that each prototype meets the desired specifications.
Best Practices for Implementing 3D Printing in Prototype Development
To make the most of 3D printing technology, design department leaders should consider the following best practices:
Invest in Technology and Training
A crucial first step is investing in the right 3D printing technology that aligns with the department’s needs.
As the technology evolves, newer printers offer improved capabilities, speed, and material options.
Additionally, providing training for staff ensures they can effectively utilize these tools to produce high-quality prototypes.
Encourage Iterative Design
Leverage the rapid prototyping capabilities of 3D printing to foster an iterative design process.
Encourage designers to test multiple versions of prototypes, analyze results, and refine their designs based on data and feedback.
This approach promotes innovation and helps identify optimal solutions more efficiently.
Collaborate Across Teams
Strengthen collaboration among engineers, designers, and other stakeholders.
Encouraging cross-functional teams to work together can lead to more creative solutions and ensure that all perspectives are considered during development.
Enhanced communication will also speed up problem-solving and decision-making, ultimately benefiting the final product.
Stay Informed of Industry Trends
The field of 3D printing is ever-evolving, with new technologies, materials, and methods continually emerging.
Leaders should stay informed about the latest trends and advancements, attending industry conferences, taking courses, and networking with other professionals to ensure their department remains at the forefront of innovation.
Conclusion
For leaders in the medical device manufacturing industry, understanding and implementing 3D printing technology in prototype development can provide a competitive advantage.
By leveraging the benefits of faster development cycles, cost-effectiveness, and customization, while addressing challenges like material limitations and regulatory compliance, design teams can create innovative, high-quality products.
By embracing best practices and fostering a culture of collaboration and continuous learning, new leaders can drive their departments toward success in a rapidly advancing field.
資料ダウンロード
QCD調達購買管理クラウド「newji」は、調達購買部門で必要なQCD管理全てを備えた、現場特化型兼クラウド型の今世紀最高の購買管理システムとなります。
ユーザー登録
調達購買業務の効率化だけでなく、システムを導入することで、コスト削減や製品・資材のステータス可視化のほか、属人化していた購買情報の共有化による内部不正防止や統制にも役立ちます。
NEWJI DX
製造業に特化したデジタルトランスフォーメーション(DX)の実現を目指す請負開発型のコンサルティングサービスです。AI、iPaaS、および先端の技術を駆使して、製造プロセスの効率化、業務効率化、チームワーク強化、コスト削減、品質向上を実現します。このサービスは、製造業の課題を深く理解し、それに対する最適なデジタルソリューションを提供することで、企業が持続的な成長とイノベーションを達成できるようサポートします。
オンライン講座
製造業、主に購買・調達部門にお勤めの方々に向けた情報を配信しております。
新任の方やベテランの方、管理職を対象とした幅広いコンテンツをご用意しております。
お問い合わせ
コストダウンが利益に直結する術だと理解していても、なかなか前に進めることができない状況。そんな時は、newjiのコストダウン自動化機能で大きく利益貢献しよう!
(Β版非公開)