- お役立ち記事
- Pursuit of Optimal Balance between Quality and Productivity with DX of Pretreatment Processes
Pursuit of Optimal Balance between Quality and Productivity with DX of Pretreatment Processes
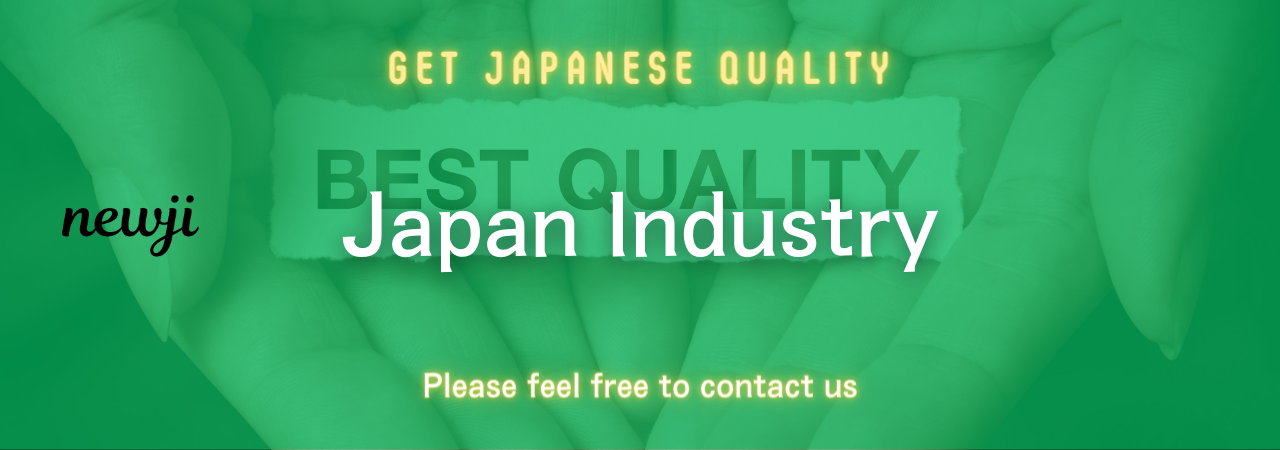
In the world of manufacturing, finding the sweet spot between quality and productivity is a constant challenge.
Digital transformation, often abbreviated as DX, serves as a powerful tool to address this issue.
When applied effectively to the pretreatment processes, DX can significantly enhance both quality and productivity.
This article explores how DX can streamline pretreatment processes, making them more efficient and ensuring high-quality outcomes.
目次
Understanding Pretreatment Processes
Pretreatment processes are essential steps in manufacturing, especially before finishing operations like painting or coating.
These processes prepare materials to ensure that the final outcome is optimal.
For instance, in the automotive industry, pretreatment helps in cleaning and conditioning the surface of metals to ensure that paint adheres properly.
Without a robust pretreatment, the final product can suffer from various issues like poor adhesion, corrosion, or uneven surfaces.
Types of Pretreatment Processes
Pretreatment often involves multiple steps, which may include cleaning, degreasing, etching, and rinsing.
Each of these steps is critical to preparing the surface for the next stage in the manufacturing process.
The goal is to remove contaminants such as oils, grease, and other residues that might interfere with subsequent steps.
The Role of DX in Pretreatment
Digital transformation can play a pivotal role in optimizing pretreatment processes.
Through the application of DX, manufacturers can automate, monitor, and analyze every step, resulting in greater precision and efficiency.
This can be achieved through various technologies such as IoT (Internet of Things), AI (Artificial Intelligence), and advanced data analytics.
Automation
Automating pretreatment processes can lead to substantial improvements in productivity.
Automated systems can operate continuously without breaks, unlike human labor.
They also offer more consistent results, reducing the likelihood of errors and deviations from the desired quality.
For example, an automated cleaning system could maintain consistent chemical concentrations, monitor temperature, and adjust settings in real-time.
This ensures that every part receives the same level of treatment, enhancing the overall quality.
Monitoring and Analytics
IoT devices can be deployed to monitor various parameters in real-time.
Sensors can track temperature, pressure, and chemical concentrations.
This data can then be analyzed to identify trends, predict maintenance needs, and optimize the pretreatment process.
Advanced analytics can provide insights into the performance of different pretreatment stages.
For instance, data could reveal that a specific soak time or temperature range yields the best results.
These insights allow manufacturers to fine-tune their processes for maximum efficiency and quality.
AI and Machine Learning
AI and machine learning algorithms can further enhance the capabilities of digital transformation in pretreatment.
These technologies can analyze large volumes of data to identify patterns and make predictive adjustments.
For example, a machine learning model could predict when a particular stage of the pretreatment process is likely to encounter issues, such as the need for chemical replenishment.
By anticipating these needs, manufacturers can avoid downtime and maintain a consistent level of productivity and quality.
Balancing Quality and Productivity
While it is essential to enhance productivity, manufacturers must not lose sight of quality.
Balancing these two aspects is where DX truly shines.
By leveraging digital tools, manufacturers can achieve high levels of productivity without compromising on quality.
Standardized Procedures
One way to balance quality and productivity is through the standardization of procedures.
Digitally controlled processes ensure that every operation follows the same protocol.
This uniformity reduces variability and ensures consistent quality.
Real-Time Adjustments
With the help of real-time monitoring and predictive analytics, adjustments can be made on-the-fly.
If a deviation from the desired quality standard is detected, the system can automatically adjust the relevant parameters.
This flexibility ensures that quality remains uncompromised while maintaining high levels of productivity.
Cost Efficiency
Optimizing pretreatment processes through digital transformation can also lead to significant cost savings.
By reducing the need for manual intervention, minimizing errors, and enhancing efficiency, manufacturers can lower operational costs.
These savings can be reinvested into further improving the quality and productivity of their manufacturing processes.
The Future of DX in Pretreatment
As technology continues to advance, the role of digital transformation in pretreatment processes is likely to grow.
Emerging technologies such as blockchain could offer new ways to track and verify the quality of pretreatment steps.
Additionally, advancements in AI and machine learning will provide even more sophisticated tools for optimizing these processes.
Collaborative Robotics
The integration of collaborative robots, or cobots, is another promising development.
Cobots can work alongside human operators to perform repetitive or hazardous tasks in pretreatment.
They can be programmed to handle specific tasks with high precision, further enhancing productivity and quality.
Advanced Materials
The development of advanced materials with enhanced properties could also impact pretreatment processes.
For example, materials that are more resistant to corrosion or require less intensive preparation could simplify pretreatment steps.
Using these advanced materials could improve efficiency and reduce costs.
Conclusion
Digital transformation holds the key to achieving an optimal balance between quality and productivity in pretreatment processes.
By harnessing the power of automation, real-time monitoring, and advanced analytics, manufacturers can streamline their operations and ensure high-quality outcomes.
As technology continues to evolve, the potential for further enhancements in pretreatment processes is vast.
By embracing DX, manufacturers can stay ahead of the curve and achieve sustainable growth in a competitive market.
資料ダウンロード
QCD調達購買管理クラウド「newji」は、調達購買部門で必要なQCD管理全てを備えた、現場特化型兼クラウド型の今世紀最高の購買管理システムとなります。
ユーザー登録
調達購買業務の効率化だけでなく、システムを導入することで、コスト削減や製品・資材のステータス可視化のほか、属人化していた購買情報の共有化による内部不正防止や統制にも役立ちます。
NEWJI DX
製造業に特化したデジタルトランスフォーメーション(DX)の実現を目指す請負開発型のコンサルティングサービスです。AI、iPaaS、および先端の技術を駆使して、製造プロセスの効率化、業務効率化、チームワーク強化、コスト削減、品質向上を実現します。このサービスは、製造業の課題を深く理解し、それに対する最適なデジタルソリューションを提供することで、企業が持続的な成長とイノベーションを達成できるようサポートします。
オンライン講座
製造業、主に購買・調達部門にお勤めの方々に向けた情報を配信しております。
新任の方やベテランの方、管理職を対象とした幅広いコンテンツをご用意しております。
お問い合わせ
コストダウンが利益に直結する術だと理解していても、なかなか前に進めることができない状況。そんな時は、newjiのコストダウン自動化機能で大きく利益貢献しよう!
(Β版非公開)