- お役立ち記事
- Quality and Delivery Management of Contract Manufactured Parts Valued by Majors
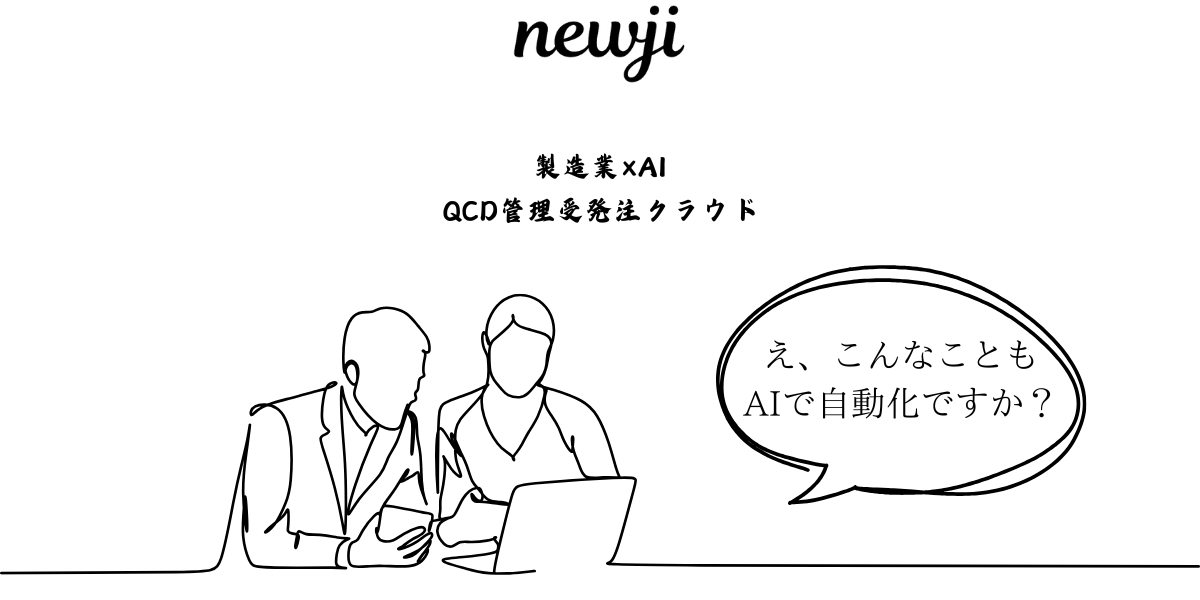
Quality and Delivery Management of Contract Manufactured Parts Valued by Majors
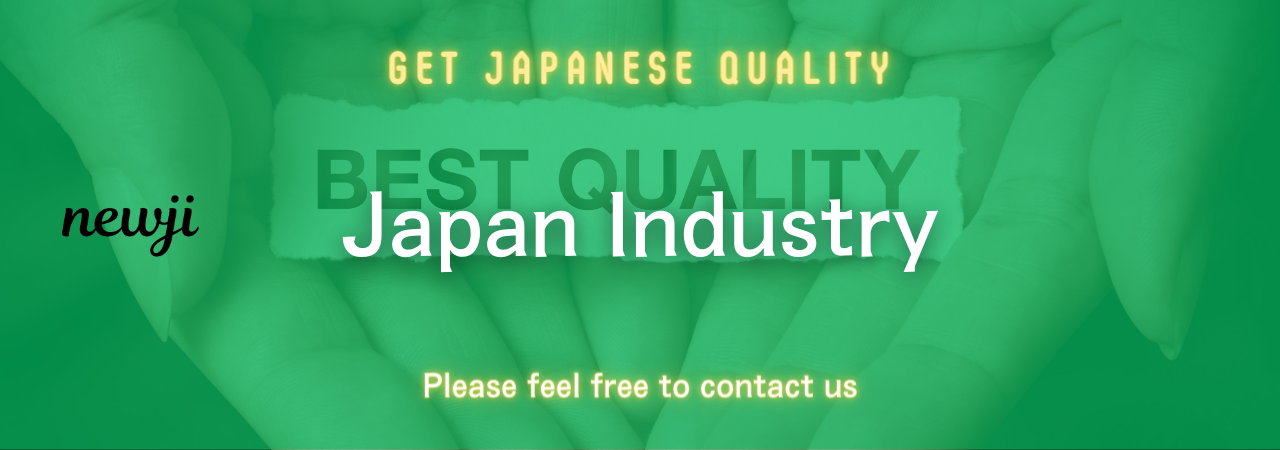
Contract manufacturing has become an essential strategy for many large companies seeking to focus on core competencies while outsourcing production.
Ensuring the quality and timely delivery of these contract-manufactured parts is crucial for majors in various industries.
Let’s dive into the critical elements involved in quality and delivery management in contract manufacturing.
目次
Importance of Quality Management
Quality management is fundamental in contract manufacturing.
The products delivered must meet stringent quality standards to ensure customer satisfaction and maintain brand reputation.
Setting Clear Quality Standards
It is essential to establish clear and detailed quality guidelines from the outset.
This includes defining specifications, acceptable materials, and tolerances.
These standards act as a benchmark against which the products are measured.
Regular Audits
Periodic audits of the manufacturing process are vital to ensure compliance with predetermined standards.
These audits can be scheduled or surprise inspections to get an accurate picture of the operations.
Supplier Evaluation
Selecting the right contract manufacturer involves careful evaluation.
Consider factors like their reputation, previous work, technological capabilities, and financial stability.
This helps prevent potential quality issues down the line.
Training and Development
Investing in the training and development of the contract manufacturer’s staff can significantly enhance product quality.
Conduct regular training sessions to keep them updated on the latest industry practices and standards.
Continuous Improvement Programs
Encourage a culture of continuous improvement in the contract manufacturing process.
Implementing frameworks like Six Sigma can help in identifying areas for improvement and achieving higher quality standards.
Ensuring Timely Delivery
Timely delivery of parts is as crucial as their quality.
Delayed parts can disrupt production schedules, leading to financial losses and missed market opportunities.
Effective Communication
Maintaining open and transparent communication with the contract manufacturer is key.
Regular updates and feedback loops help in addressing potential delays promptly.
Clear Delivery Schedules
Establishing clear delivery schedules at the beginning of the contract is essential.
Include buffer periods to accommodate any unforeseen delays without impacting the overall timeline.
Advanced Planning and Scheduling
Utilizing advanced planning and scheduling tools can optimize the manufacturing process.
These tools can forecast demand, plan production, and schedule deliveries efficiently.
Risk Management
Identify potential risks that could hinder timely delivery and develop mitigation strategies.
This could include alternative suppliers, additional inventory, or contingency plans for logistical challenges.
Performance Metrics
Define and monitor key performance indicators (KPIs) related to delivery timelines.
Regularly review these metrics to identify and address any issues proactively.
Balancing Quality and Cost
While focusing on quality and timely delivery, it’s crucial to manage costs effectively.
Balancing these aspects ensures that the products are economically viable without compromising on quality.
Cost Analysis
Conduct a thorough cost analysis at the outset.
Understand the cost implications of different quality standards and delivery timelines.
This helps in making informed decisions that balance quality, delivery, and cost.
Negotiation
Effective negotiation with the contract manufacturer can help in achieving favorable terms.
This includes negotiating costs, payment schedules, and penalties for non-compliance with quality or delivery standards.
Value Engineering
Implementing value engineering techniques can help in optimizing production processes.
This involves analyzing the function of parts, identifying cost-saving opportunities, and ensuring the product meets quality standards.
Leveraging Technology
Technology plays a crucial role in modern contract manufacturing management.
It aids in ensuring quality, managing delivery schedules, and optimizing costs.
Quality Management Systems (QMS)
Implementing advanced QMS helps in maintaining high-quality standards.
These systems automate quality checks, document control, and non-conformance management.
Supply Chain Management (SCM) Systems
Integrating SCM systems ensure seamless coordination between different entities in the supply chain.
This aids in timely delivery of parts and efficient management of inventory.
Data Analytics
Utilizing data analytics helps in making informed decisions.
By analyzing data on supplier performance, production processes, and delivery timelines, you can identify trends and make proactive adjustments.
Internet of Things (IoT)
IoT technologies enable real-time monitoring of production processes.
Sensors and devices collect data, providing insights into equipment performance, environmental conditions, and product quality.
Building Strong Relationships with Contract Manufacturers
A solid relationship with the contract manufacturer is vital for successful quality and delivery management.
Partnership Approach
Adopt a partnership approach rather than a transactional one.
This involves working collaboratively with the contract manufacturer, sharing best practices, and aligning goals.
Trust and Transparency
Building trust through transparency is crucial.
Openly share information, expectations, and feedback.
This fosters a cooperative environment and ensures alignment on quality and delivery standards.
Regular Meetings and Reviews
Conduct regular meetings and performance reviews.
Discuss progress, address any issues, and make adjustments as necessary.
This helps in maintaining focus and ensuring that both parties are on the same page.
Contract manufacturing offers significant advantages, but ensuring quality and timely delivery requires diligent management.
By implementing robust quality management practices, effective delivery strategies, and leveraging technology, large companies can achieve their goals efficiently.
Building strong relationships with contract manufacturers further enhances collaboration and success.
資料ダウンロード
QCD調達購買管理クラウド「newji」は、調達購買部門で必要なQCD管理全てを備えた、現場特化型兼クラウド型の今世紀最高の購買管理システムとなります。
ユーザー登録
調達購買業務の効率化だけでなく、システムを導入することで、コスト削減や製品・資材のステータス可視化のほか、属人化していた購買情報の共有化による内部不正防止や統制にも役立ちます。
NEWJI DX
製造業に特化したデジタルトランスフォーメーション(DX)の実現を目指す請負開発型のコンサルティングサービスです。AI、iPaaS、および先端の技術を駆使して、製造プロセスの効率化、業務効率化、チームワーク強化、コスト削減、品質向上を実現します。このサービスは、製造業の課題を深く理解し、それに対する最適なデジタルソリューションを提供することで、企業が持続的な成長とイノベーションを達成できるようサポートします。
オンライン講座
製造業、主に購買・調達部門にお勤めの方々に向けた情報を配信しております。
新任の方やベテランの方、管理職を対象とした幅広いコンテンツをご用意しております。
お問い合わせ
コストダウンが利益に直結する術だと理解していても、なかなか前に進めることができない状況。そんな時は、newjiのコストダウン自動化機能で大きく利益貢献しよう!
(Β版非公開)