- お役立ち記事
- Quality Assurance: How Japanese Companies Ensure Global Satisfaction
Quality Assurance: How Japanese Companies Ensure Global Satisfaction
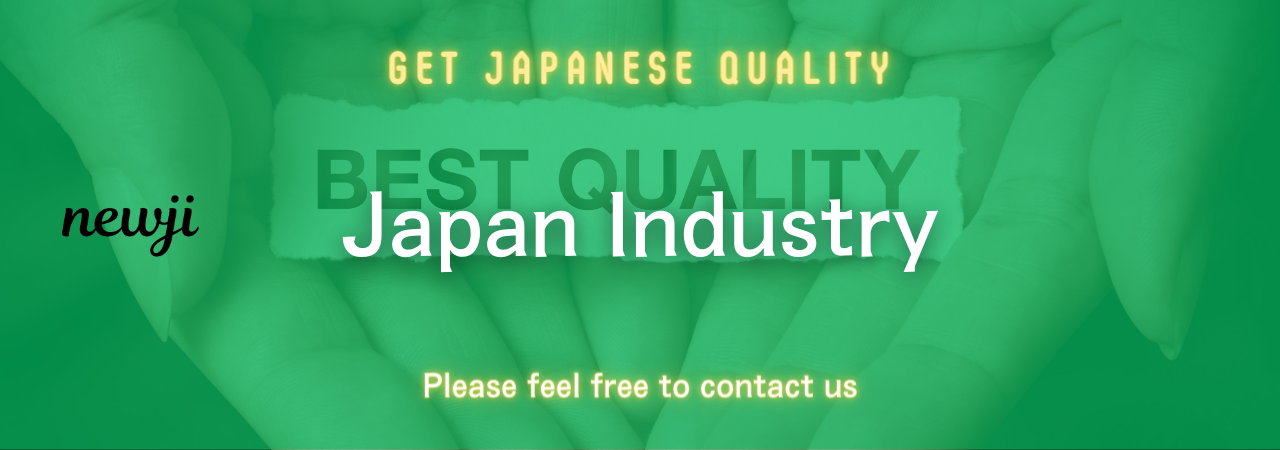
Quality assurance is a crucial element for companies around the world, but Japanese companies have taken this to another level. With a reputation for precision, reliability, and customer satisfaction, Japan’s approach to quality assurance is studied and admired globally. But what makes Japanese companies so effective in this area?
One of the fundamental principles of quality assurance in Japan is the concept of “Kaizen,” which means continuous improvement. This philosophy is embedded into every facet of Japanese corporate culture, inspiring everyone from top executives to factory workers to consistently look for ways to improve their processes. Kaizen encourages small, incremental changes that collectively lead to significant improvements in quality over time.
Japanese companies also adopt a holistic approach to quality assurance. This means they consider the entire production process, from raw materials to customer feedback, to ensure quality at every step. For instance, many Japanese companies implement the PDCA (Plan-Do-Check-Act) cycle. This cycle is a four-step management method that aims to ensure processes are effective and efficient. The “Plan” phase involves determining the objectives and processes needed to deliver results. The “Do” phase is about implementing the plan. The “Check” phase involves monitoring and evaluating the implemented plan by comparing the results with the expected outcomes. Finally, the “Act” phase is about taking actions based on the evaluation.
Employee involvement is another critical factor. Japanese companies often employ extensive training programs to ensure every employee understands their role in maintaining and improving quality. This might include workshops, on-the-job training, and mentorship programs to build a culture of quality consciousness. This method ensures that every team member is fully committed to and involved in the quality assurance process.
Another way Japanese firms ensure quality is through stringent supplier management. Japanese companies meticulously select their suppliers and often work closely with them to ensure materials and components meet their high standards. Visits to suppliers’ factories, detailed audits, and even joint improvement activities are common. This close collaboration helps in maintaining a consistent quality even before a product reaches the manufacturing stage.
The concept of “Jidoka” or automation with a human touch is widely embraced by Japanese companies. Jidoka is part of the renowned Toyota Production System and emphasizes making machines that can detect errors and stop automatically, allowing human operators to address issues before they affect the production line. This helps in maintaining high quality by preventing the accumulation of defects.
Customer feedback plays an integral role in the Japanese quality assurance system. Japanese companies go to great lengths to ensure they are in tune with their customers’ needs and perceptions. They often employ rigorous feedback mechanisms, such as detailed surveys, focus groups, and direct interactions, to gather comprehensive data on customer satisfaction and preferences. This feedback is then systematically analyzed and used to make improvements.
Statistical process control (SPC) is another technique used extensively. SPC involves collecting data from various points in the production process and using statistical methods to analyze it. By understanding the variations in the process, companies can identify and minimize inefficiencies and defects. This data-driven approach ensures a higher degree of precision and reliability in the final product.
Lean manufacturing principles, such as Just-In-Time (JIT) production, also play a role in Japanese quality assurance. JIT aims to reduce waste and improve efficiency by producing only what is needed, when it is needed, and in the amount needed. This minimizes excess inventory and resources, allowing companies to focus on creating high-quality products.
Incorporating quality assurance into product design is another characteristic of Japanese manufacturing. This is often referred to as “Quality by Design” (QbD). During the design phase, potential issues are identified and addressed to ensure the product can be manufactured to high standards. This proactive approach reduces the likelihood of defects and increases customer satisfaction since potential problems are ironed out early in the process.
Benchmarking against both domestic and international standards is another strategy. Japanese companies are often ahead of the curve in meeting or exceeding industry standards, which keeps them competitive on the global stage. They frequently update their practices to align with the latest ISO standards, which not only helps in improving quality but also boosts their credibility in international markets.
Finally, Japanese companies often employ advanced technologies and innovations to enhance quality assurance. From sophisticated robotics to artificial intelligence in quality control systems, leveraging cutting-edge technology allows for greater precision and efficiency. These technologies aid in real-time monitoring and quick identification of potential issues, which can be addressed promptly to maintain high quality.
In summary, Japanese companies’ approach to quality assurance is comprehensive and inclusive, focusing on continuous improvement, employee involvement, supplier management, advanced technologies, and a holistic view of the production process. This multifaceted strategy ensures they consistently deliver products and services that meet high global standards and exceed customer expectations. As businesses worldwide look to elevate their quality assurance processes, they would do well to take a leaf out of Japan’s book.
資料ダウンロード
QCD調達購買管理クラウド「newji」は、調達購買部門で必要なQCD管理全てを備えた、現場特化型兼クラウド型の今世紀最高の購買管理システムとなります。
ユーザー登録
調達購買業務の効率化だけでなく、システムを導入することで、コスト削減や製品・資材のステータス可視化のほか、属人化していた購買情報の共有化による内部不正防止や統制にも役立ちます。
NEWJI DX
製造業に特化したデジタルトランスフォーメーション(DX)の実現を目指す請負開発型のコンサルティングサービスです。AI、iPaaS、および先端の技術を駆使して、製造プロセスの効率化、業務効率化、チームワーク強化、コスト削減、品質向上を実現します。このサービスは、製造業の課題を深く理解し、それに対する最適なデジタルソリューションを提供することで、企業が持続的な成長とイノベーションを達成できるようサポートします。
オンライン講座
製造業、主に購買・調達部門にお勤めの方々に向けた情報を配信しております。
新任の方やベテランの方、管理職を対象とした幅広いコンテンツをご用意しております。
お問い合わせ
コストダウンが利益に直結する術だと理解していても、なかなか前に進めることができない状況。そんな時は、newjiのコストダウン自動化機能で大きく利益貢献しよう!
(Β版非公開)