- お役立ち記事
- Quality Audits of Batch Production Processes: A Procurement Department Perspective
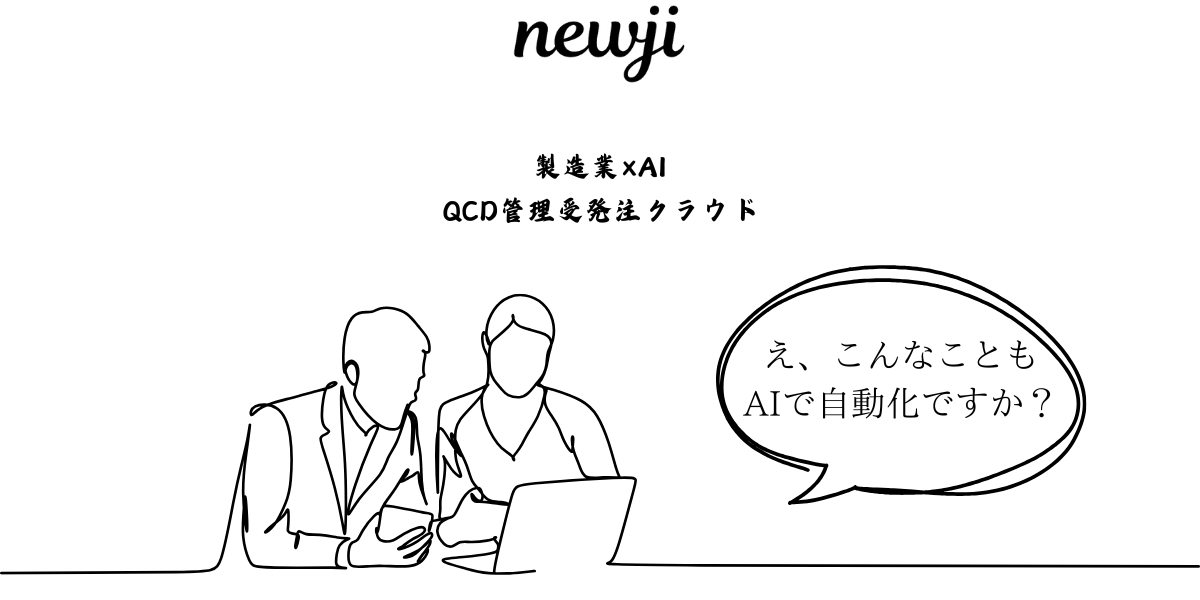
Quality Audits of Batch Production Processes: A Procurement Department Perspective
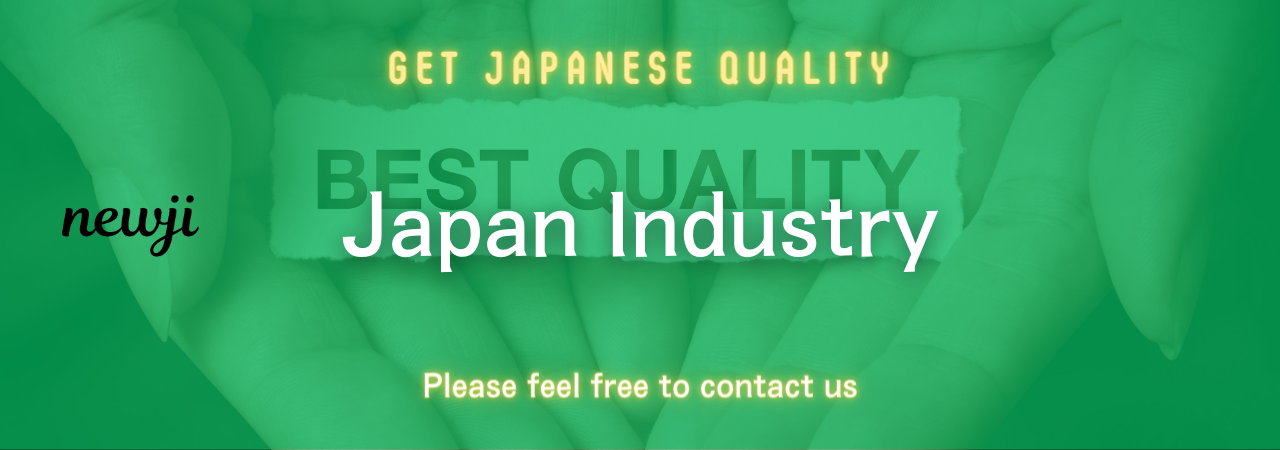
The role of the procurement department is vital within any manufacturing company.
Their responsibility isn’t just to ensure timely supply of raw materials but also to guarantee the quality of these materials.
Effective quality control measures can prevent production hiccups, costly recalls, and customer complaints.
One such measure is the quality audit of batch production processes.
From a procurement department perspective, these audits are essential for maintaining high standards.
目次
Understanding Quality Audits
What is a Quality Audit?
A quality audit is a systematic examination that assesses whether processes are being followed correctly and if they meet predefined standards.
In the context of batch production processes, this means evaluating every step from raw material procurement to the final product.
Audits help identify areas of improvement and ensure compliance with industry regulations.
Importance of Quality Audits in Batch Production
Batch production involves producing goods in large quantities in a single run.
This method is efficient but also leaves room for mistakes to proliferate if not checked adequately.
A single error in one batch can compromise the entire production run.
Quality audits help in catching these errors early, thus preventing widespread issues.
Role of Procurement in Quality Audits
Ensuring Material Quality
The procurement department plays a critical role in the quality of end products by ensuring that raw materials meet required standards.
Quality audits often start with the raw materials.
Evaluating supplier performance and conducting audits at the supplier’s production facilities can ensure that only high-quality materials enter the production process.
This reduces the risk of defects in the final product.
Supplier Relationship Management
Building solid relationships with suppliers can make quality audits more effective.
Suppliers who understand the importance of quality are more likely to cooperate during audits.
The procurement team should maintain open lines of communication with suppliers to address any issues promptly.
Regularly scheduled audits can be part of the supplier agreements, ensuring ongoing compliance.
Steps Involved in Quality Audits of Batch Production Processes
Planning the Audit
The first step in a quality audit is meticulous planning.
This involves defining the scope, objectives, and criteria of the audit.
The procurement team should collaborate with quality assurance specialists to determine what needs to be checked and how.
This may include material specifications, production methods, and finished product standards.
Conducting the Audit
The actual audit involves detailed assessments of each stage of the production process.
This could range from raw material inspection to in-process checks and final product evaluations.
The procurement team should ensure that all checks are done according to the established criteria.
Data collected during these audits provide insights into where improvements are needed.
Documenting Findings
Documentation is a crucial part of any quality audit.
All findings, both positive and negative, should be thoroughly documented.
This not only helps in tracking improvements over time but also serves as evidence of compliance.
H3>Implementing Corrective Actions
No process is perfect, and audits will inevitably reveal some areas needing improvement.
The procurement team should work closely with the production and quality assurance departments to implement corrective actions.
These can range from adjusting supplier contracts to changing internal processes.
Continuous monitoring ensures that these measures effectively resolve the identified issues.
Benefits of Quality Audits
Enhanced Product Quality
One of the most apparent benefits of conducting regular quality audits is improved product quality.
A systematic review of batch production processes helps identify flaws and rectify them before they affect the end product.
High product quality leads to increased customer satisfaction and brand trust.
Cost Savings
Detecting issues early in the production process can result in significant cost savings.
For instance, identifying a defect in the raw materials before they are used in production can save the cost of reworking or scrapping defective batches.
Furthermore, it prevents the financial losses associated with product recalls and damage to the company’s reputation.
Regulatory Compliance
Staying compliant with industry regulations is non-negotiable for any manufacturing company.
Regular quality audits ensure that all processes, from procurement to production, comply with relevant standards and regulations.
This mitigates the risk of legal penalties and enhances the company’s standing in the industry.
Challenges in Conducting Quality Audits
Resource Constraints
Conducting thorough quality audits requires dedicated resources in terms of time and personnel.
Small to medium enterprises often struggle with allocating these resources, forcing them to delay or even skip audits.
Resistance to Change
Implementing corrective actions based on audit findings can face resistance from various stakeholders.
Staff may be reluctant to change established procedures, suppliers may not welcome additional scrutiny, and management might hesitate to invest in improvements.
The procurement team plays a crucial role in facilitating these changes by emphasizing the long-term benefits.
Tips for Effective Quality Audits
Train Your Team
A well-trained team is crucial for the success of quality audits.
Ensure that all members involved in the audit process understand the objectives, criteria, and techniques.
Provide ongoing training to keep them updated with the latest industry standards and best practices.
Use Technology
Modern technology offers various tools that can streamline the audit process.
Audit management software, for instance, can help in planning, executing, and documenting audits more efficiently.
Utilizing technological solutions can provide real-time data and analytics, making it easier to identify and address issues promptly.
Foster a Culture of Quality
Quality should not be an afterthought but an integral part of the company culture.
Encourage all employees, from top management to shop floor workers, to prioritize quality in their tasks.
Continuous education and awareness programs can instill the importance of quality.
Regular quality audits in batch production processes are indispensable.
They ensure that raw materials, production techniques, and final products meet high standards, benefiting both the company and its customers.
From a procurement department perspective, these audits not only secure material quality but also fortify supplier relationships and drive cost savings.
Despite challenges like resource constraints and resistance to change, effective audits backed by trained personnel and modern technology can pave the way for sustained excellence.
資料ダウンロード
QCD調達購買管理クラウド「newji」は、調達購買部門で必要なQCD管理全てを備えた、現場特化型兼クラウド型の今世紀最高の購買管理システムとなります。
ユーザー登録
調達購買業務の効率化だけでなく、システムを導入することで、コスト削減や製品・資材のステータス可視化のほか、属人化していた購買情報の共有化による内部不正防止や統制にも役立ちます。
NEWJI DX
製造業に特化したデジタルトランスフォーメーション(DX)の実現を目指す請負開発型のコンサルティングサービスです。AI、iPaaS、および先端の技術を駆使して、製造プロセスの効率化、業務効率化、チームワーク強化、コスト削減、品質向上を実現します。このサービスは、製造業の課題を深く理解し、それに対する最適なデジタルソリューションを提供することで、企業が持続的な成長とイノベーションを達成できるようサポートします。
オンライン講座
製造業、主に購買・調達部門にお勤めの方々に向けた情報を配信しております。
新任の方やベテランの方、管理職を対象とした幅広いコンテンツをご用意しております。
お問い合わせ
コストダウンが利益に直結する術だと理解していても、なかなか前に進めることができない状況。そんな時は、newjiのコストダウン自動化機能で大きく利益貢献しよう!
(Β版非公開)