- お役立ち記事
- Quality Management Tips for SMEs in Frame Manufacturing
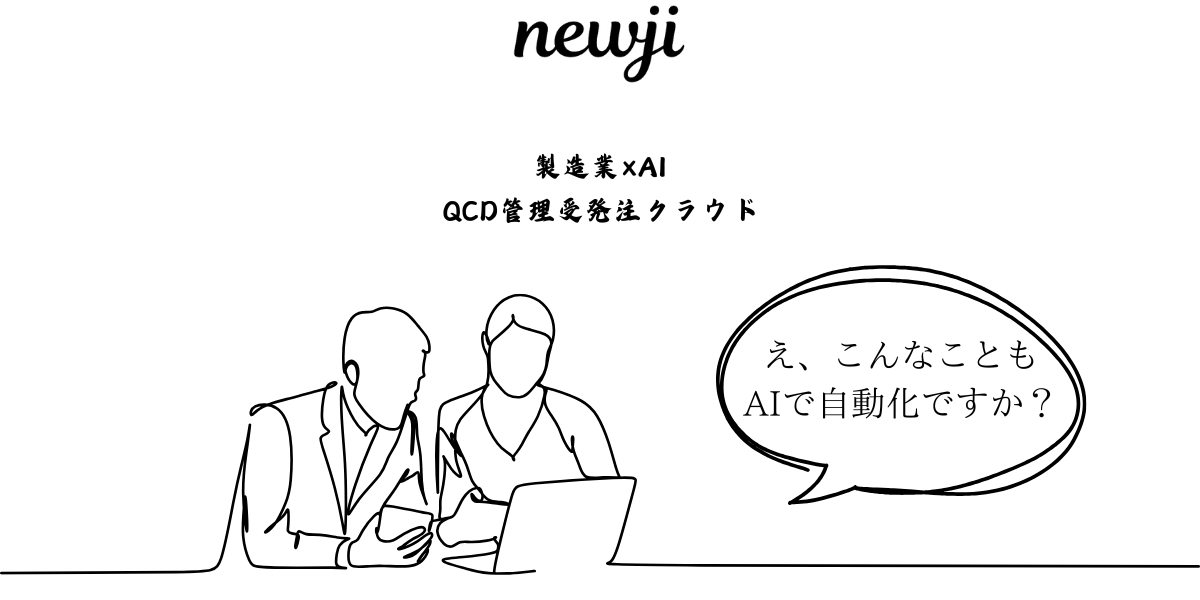
Quality Management Tips for SMEs in Frame Manufacturing
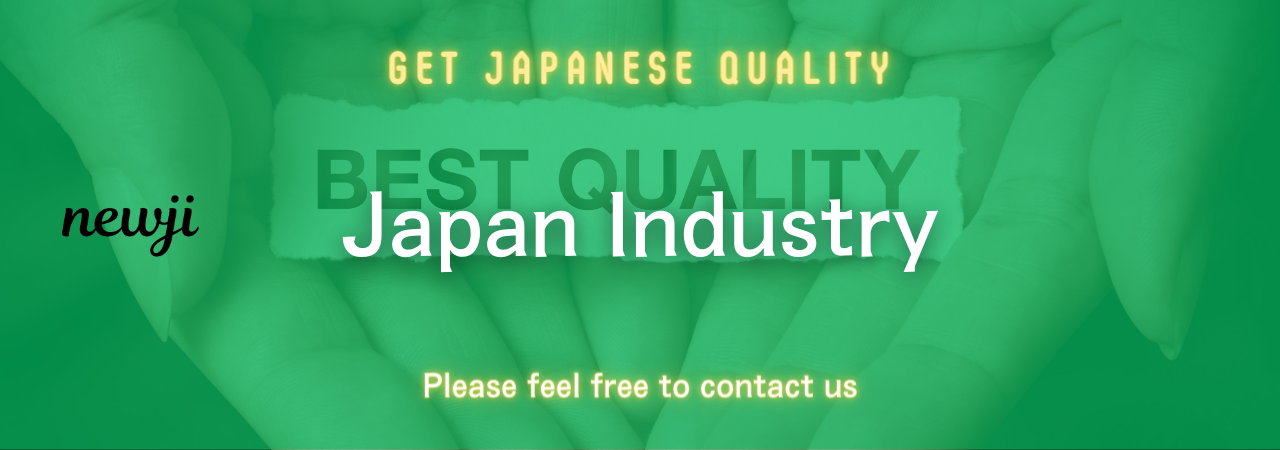
In today’s competitive market, ensuring the quality of your products is more important than ever.
Small and Medium Enterprises (SMEs) in the frame manufacturing industry need to consistently produce high-quality products to stay ahead.
Quality management can seem challenging, especially for smaller businesses, but it is possible with the right strategies in place.
This article will provide actionable tips to help SMEs in frame manufacturing improve their quality management processes.
目次
Understanding Quality Management in Frame Manufacturing
Quality management refers to the processes and procedures in place to ensure that products meet certain standards and specifications that satisfy customer needs.
In frame manufacturing, this includes everything from the materials used to the final product delivered to customers.
Quality management isn’t only about identifying defects; it’s about preventing them and ensuring continuous improvement.
The Benefits of Quality Management for SMEs
Investing in quality management yields numerous benefits for SMEs in frame manufacturing.
Firstly, it builds customer trust and loyalty, which can increase repeat business and referrals.
Secondly, it reduces costs associated with rework, returns, and waste.
Thirdly, it can improve employee morale and job satisfaction as it often involves a more organized and systematic approach to production.
Lastly, it can provide a competitive edge over rivals who may not prioritize quality as strongly.
Implementing a Quality Management System (QMS)
A Quality Management System (QMS) is a structured system that documents the processes, procedures, and responsibilities for achieving quality policies and objectives.
Here are some steps SMEs can take to implement an effective QMS:
Set Clear Quality Objectives
Begin by establishing clear, measurable quality objectives that align with your business goals.
These objectives should be specific, attainable, relevant, and time-bound.
For example, you could aim for a 10% reduction in defective frames over the next six months.
Document Your Processes
Documenting your processes helps ensure consistency and serves as a reference for training new employees.
Create detailed guides for each stage of the manufacturing process, including material selection, cutting, assembling, and finishing.
Include checklists and standard operating procedures to ensure that nothing is overlooked.
Train Your Employees
Your team plays a crucial role in maintaining product quality.
Invest in regular training to ensure they understand the importance of quality management and know how to implement it in their daily tasks.
Training should cover not only the technical aspects but also the reasons behind each quality control step.
Perform Regular Inspections
Regular inspections at various stages of the manufacturing process can help catch issues early.
Consider implementing a schedule for quality checks, including incoming materials inspection, in-process inspections, and final product inspections.
Use tools like checklists and inspection reports to keep track of findings and corrective actions taken.
Adopting Continuous Improvement Practices
Quality management is not a one-time effort but an ongoing process.
Continuous improvement practices can help SMEs maintain and enhance their quality standards over time.
Implement the Plan-Do-Check-Act (PDCA) Cycle
The PDCA cycle is a well-known method for continuous improvement.
It involves four steps: Plan (identify an opportunity and plan for change), Do (implement the change), Check (use data to analyze the results of the change), and Act (if the change was successful, implement it on a larger scale; if not, begin the cycle again).
This iterative process helps businesses continually refine their operations.
Encourage Employee Feedback
Employees are often the first to notice issues or opportunities for improvement.
Encourage them to provide feedback and suggestions.
Implementing a structured feedback mechanism, such as regular team meetings or an anonymous suggestion box, can be beneficial.
This not only helps identify potential problems but also fosters a culture of continuous improvement.
Monitor Key Performance Indicators (KPIs)
KPIs are essential for tracking the effectiveness of your quality management efforts.
Some relevant KPIs for frame manufacturing might include the defect rate, rework rate, customer satisfaction levels, and on-time delivery rate.
Regularly reviewing these metrics can help pinpoint areas needing improvement.
Perform Root Cause Analysis
When quality issues occur, it’s essential to identify the root cause to prevent recurrence.
Tools like the fishbone diagram (Ishikawa), the five whys technique, and failure mode and effects analysis (FMEA) can be helpful in performing root cause analysis.
Understanding the underlying causes allows for more effective corrective actions.
Leveraging Technology for Quality Management
Incorporating technology into your quality management processes can greatly enhance efficiency and accuracy.
Here are some ways SMEs in frame manufacturing can benefit from technology:
Use Quality Management Software
Quality management software can streamline and automate many of the processes involved in maintaining product quality.
Features may include document control, audit management, non-conformance tracking, and corrective and preventive actions (CAPA).
This software can provide real-time data making it easier to monitor and improve quality.
Integrate Production and Quality Data
Integrating data from your production processes with your quality management system can provide valuable insights.
This integration allows for real-time tracking of quality metrics and quicker identification of trends and issues.
For instance, if you notice a certain machine consistently produces frames with defects, you can take immediate action to address the problem.
Utilize Automated Inspection Tools
Automated inspection tools, such as computer vision systems, can significantly improve the accuracy and speed of quality checks.
These tools can inspect various aspects of the frames, such as dimensions, structural integrity, and surface finish, with greater precision than manual inspections.
Engaging with Suppliers and Customers
Quality management extends beyond your manufacturing floor.
Engaging with both suppliers and customers can help ensure that the entire supply chain contributes to your quality objectives.
Develop Strong Supplier Relationships
Your suppliers play a critical role in the quality of your final products.
Work closely with them to ensure they understand your quality standards and expectations.
Regular performance assessments and feedback can help maintain high-quality supplies.
Gather Customer Feedback
Customer feedback is invaluable for understanding how well your products meet market needs.
Regularly collect and analyze feedback through surveys, reviews, and direct communication.
Use this feedback to make informed decisions about necessary improvements.
In conclusion, quality management is crucial for SMEs in frame manufacturing to stay competitive and build a reputation for excellence.
Implementing a robust Quality Management System, adopting continuous improvement practices, leveraging technology, and engaging with suppliers and customers can significantly enhance product quality.
By focusing on these areas, SMEs can not only meet but exceed customer expectations.
資料ダウンロード
QCD調達購買管理クラウド「newji」は、調達購買部門で必要なQCD管理全てを備えた、現場特化型兼クラウド型の今世紀最高の購買管理システムとなります。
ユーザー登録
調達購買業務の効率化だけでなく、システムを導入することで、コスト削減や製品・資材のステータス可視化のほか、属人化していた購買情報の共有化による内部不正防止や統制にも役立ちます。
NEWJI DX
製造業に特化したデジタルトランスフォーメーション(DX)の実現を目指す請負開発型のコンサルティングサービスです。AI、iPaaS、および先端の技術を駆使して、製造プロセスの効率化、業務効率化、チームワーク強化、コスト削減、品質向上を実現します。このサービスは、製造業の課題を深く理解し、それに対する最適なデジタルソリューションを提供することで、企業が持続的な成長とイノベーションを達成できるようサポートします。
オンライン講座
製造業、主に購買・調達部門にお勤めの方々に向けた情報を配信しております。
新任の方やベテランの方、管理職を対象とした幅広いコンテンツをご用意しております。
お問い合わせ
コストダウンが利益に直結する術だと理解していても、なかなか前に進めることができない状況。そんな時は、newjiのコストダウン自動化機能で大きく利益貢献しよう!
(Β版非公開)