- お役立ち記事
- Reducing Energy Consumption Technology for Manufacturing Sustainability
Reducing Energy Consumption Technology for Manufacturing Sustainability
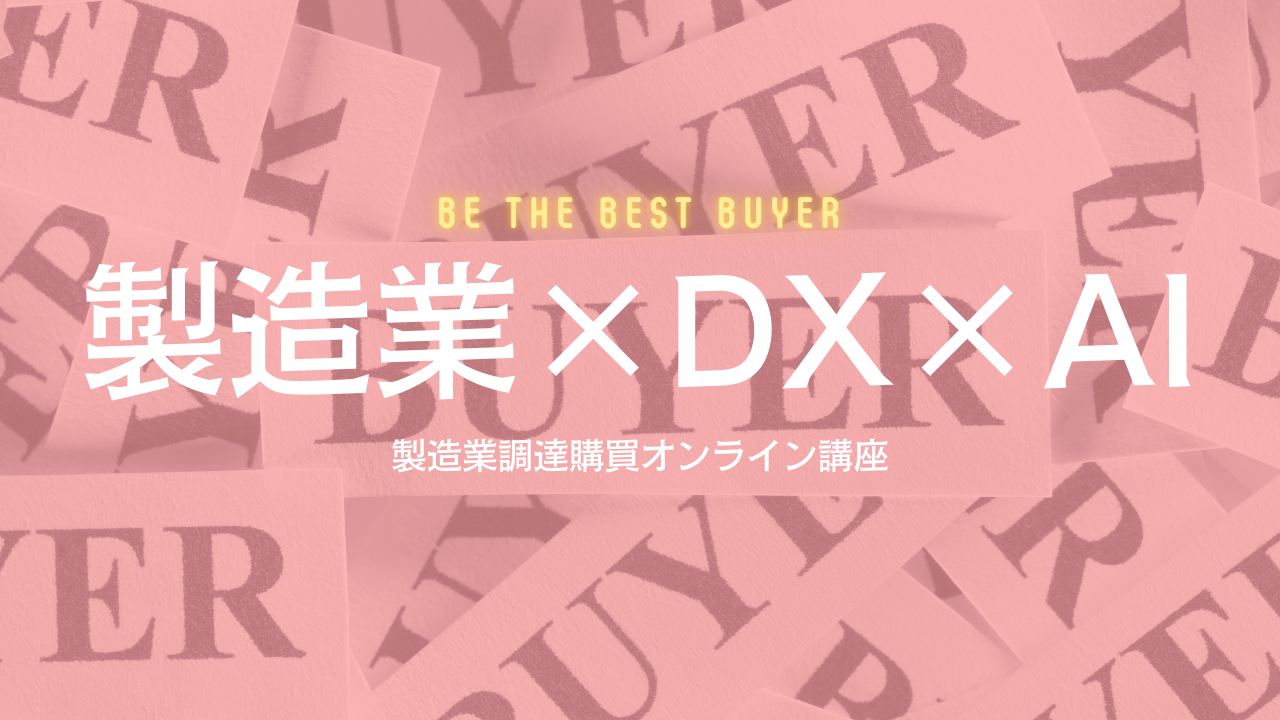
Manufacturing is a very important industry that produces many of the goods and products we rely on every day. However, the manufacturing process can often use large amounts of energy and resources. This can be bad for the environment if we are not careful. There are technologies we can use to help manufacturers reduce their energy use and become more sustainable.
Some key technologies that can help manufacturers cut down on energy consumption include energy-efficient lighting, energy management systems, smart HVAC systems, and renewable energy sources like solar panels. Switching to LED lighting is one of the simplest and most effective changes a factory can make. LED lights use up to 90% less energy than traditional incandescent or halogen lights and last much longer. This means huge savings on electricity bills over time. LEDs also don’t produce as much heat, keeping factories cooler without needing as much air conditioning.
Installing an energy management system allows manufacturers to monitor and control their energy use from one centralized location. Sensors are placed around the facility to track things like lighting levels, temperatures, and machine operations. The system then automatically adjusts settings like dimming lights in empty rooms or turning off machines that aren’t in use. This prevents energy from being wasted on things running unnecessarily. Some advanced systems can even identify opportunities to optimize energy use, saving companies even more money.
Heating, ventilation, and air conditioning (HVAC) systems are another big energy user in manufacturing plants. Older HVAC systems may not be very efficient and could be wasting a lot of power. Upgrading to smart HVAC technology allows for tighter climate control and remote management. For example, HVAC units can be programmed to only run when certain production areas are occupied. Sensors check temperature and humidity levels frequently to make tiny adjustments as needed instead of full-blast heating or cooling all the time. Together these smarter features achieve greater comfort for employees while reducing HVAC energy usage by 15-30% on average.
While most manufacturing currently relies on utility-provided electricity generated from fossil fuels like coal and natural gas, using renewable energy is becoming more affordable and practical for factories. One popular option is installing solar panels on available roof space at manufacturing facilities. Not only does this provide clean electricity from the sun, but any excess power generated can be sold back to the local electric utility, essentially paying the company. Large scale solar farms are another renewable energy source some manufacturers partner with for cheaper rates on green power. Geothermal and biomass energy technologies are further developing renewable alternatives factories may adopt in the future.
Waste heat recovery presents yet another opportunity for manufacturers to cut energy costs and improve sustainability. Many production processes generate significant heat as a by-product that simply escapes into the air. But this wasted heat can be captured and reused to help power other areas of the plant or even nearby facilities. Technologies like heat exchangers extract heat from flue gases, cooling or boiling water which is then piped to locations needing temperature regulation like process machinery or space heating systems. This form of energy recycling captures energy that would otherwise be wasted and reduces dependence on external energy sources.
Adopting any of the technologies described here allows manufacturers to reduce their environmental impact while also saving money on utility bills each month. Government incentives and tax rebates are often available to offset initial costs of LED lighting conversions, energy management system installations, HVAC upgrades, renewable energy projects and more. With investment payback periods typically under 5 years for energy efficiency upgrades, now is a smart time for manufacturers to explore technologies to cut consumption and operate more sustainably for the future. The well-being of our planet and communities depends on all industries making these important changes where possible.
In summary, technologies like energy-efficient LED lighting, building automation controls, smart HVAC systems, renewable energy sources, and waste heat recovery can help factories significantly cut their energy use and costs. While requiring upfront investments, these sustainability upgrades provide quick returns and ensure manufacturing remains a financially viable industry for many years to come in an increasingly carbon-constrained world. Committing to energy reductions through available technologies is a win-win that benefits both businesses and the environment.
資料ダウンロード
QCD調達購買管理クラウド「newji」は、調達購買部門で必要なQCD管理全てを備えた、現場特化型兼クラウド型の今世紀最高の購買管理システムとなります。
ユーザー登録
調達購買業務の効率化だけでなく、システムを導入することで、コスト削減や製品・資材のステータス可視化のほか、属人化していた購買情報の共有化による内部不正防止や統制にも役立ちます。
NEWJI DX
製造業に特化したデジタルトランスフォーメーション(DX)の実現を目指す請負開発型のコンサルティングサービスです。AI、iPaaS、および先端の技術を駆使して、製造プロセスの効率化、業務効率化、チームワーク強化、コスト削減、品質向上を実現します。このサービスは、製造業の課題を深く理解し、それに対する最適なデジタルソリューションを提供することで、企業が持続的な成長とイノベーションを達成できるようサポートします。
オンライン講座
製造業、主に購買・調達部門にお勤めの方々に向けた情報を配信しております。
新任の方やベテランの方、管理職を対象とした幅広いコンテンツをご用意しております。
お問い合わせ
コストダウンが利益に直結する術だと理解していても、なかなか前に進めることができない状況。そんな時は、newjiのコストダウン自動化機能で大きく利益貢献しよう!
(Β版非公開)