- お役立ち記事
- Reducing Lead Times: Methods for Streamlining Manufacturing Processes
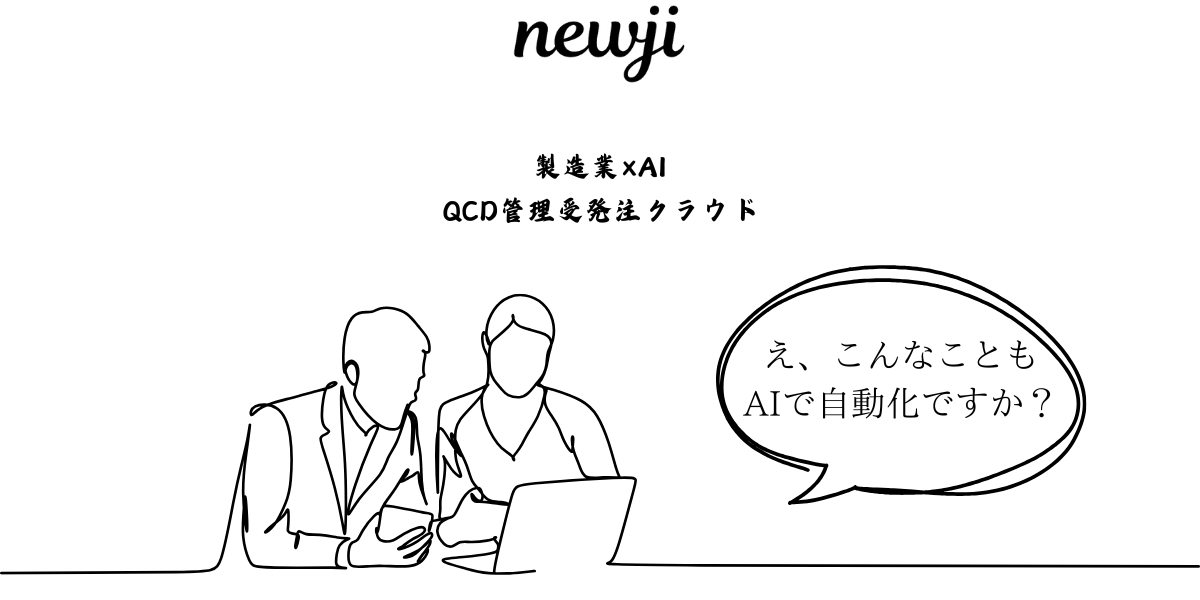
Reducing Lead Times: Methods for Streamlining Manufacturing Processes
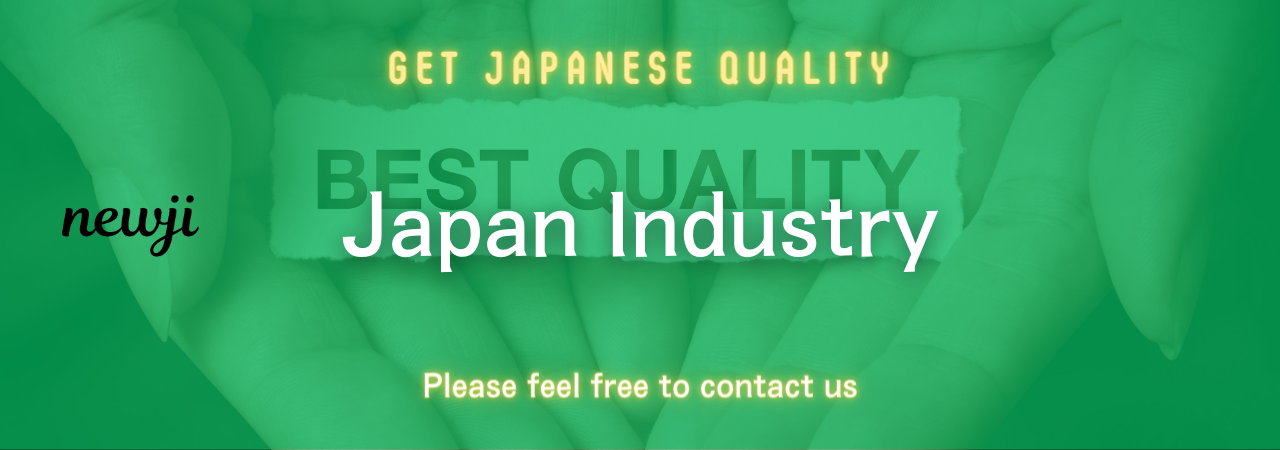
In today’s competitive market, reducing lead times is crucial for manufacturing businesses.
Speedy production not only satisfies customer demand but also increases overall efficiency and profitability.
Let’s explore some key methods to help streamline manufacturing processes.
目次
Understanding Lead Time
Lead time is the total time it takes from the initiation of a production order until the final product is delivered to the customer.
This includes all stages of the manufacturing process, such as procurement, production, and delivery.
Long lead times can result in delayed deliveries, customer dissatisfaction, and increased costs.
Hence, reducing lead times is essential for maintaining a competitive edge in the market.
Implementing Lean Manufacturing
Lean manufacturing is a systematic method for minimizing waste without compromising productivity.
It focuses on creating more value for customers with fewer resources.
Implementing lean principles can significantly reduce lead times.
Identifying and Eliminating Waste
One of the core principles of lean manufacturing is to identify and eliminate waste.
Waste can be categorized into several types, including overproduction, waiting, transportation, excess inventory, motion, defects, and underutilization of employees’ skills.
By systematically identifying and eliminating these wastes, manufacturers can streamline their processes and reduce lead times.
Just-in-Time Production
Just-in-Time (JIT) production is a strategy designed to improve a business’s return on investment by reducing in-process inventory and associated carrying costs.
With JIT, goods are produced only when they are needed, reducing the time products spend in storage.
This method enables manufacturers to respond quickly to customer orders and reduce lead times significantly.
Optimizing Supply Chain Management
An efficient supply chain is critical for reducing lead times.
Improving supply chain management can lead to faster procurement and delivery processes.
Supplier Relationships
Building strong relationships with suppliers is key to optimizing supply chain efficiency.
Reliable suppliers can provide quality materials promptly, reducing the wait time for raw materials.
Maintaining open communication and collaborating closely with suppliers can help resolve issues swiftly and ensure a smooth supply chain flow.
Inventory Management
Effective inventory management ensures that the right materials are available when needed, without excessive stock that can slow down the production process.
Implementing an inventory management system or software can help monitor stock levels, track lead times, and predict demand more accurately.
This can prevent production delays caused by material shortages.
Enhancing Workflow and Process Efficiency
Improving the efficiency of manufacturing processes and workflows can significantly reduce lead times.
Here are a few methods to enhance workflow efficiency.
Standardized Work Instructions
Creating standardized work instructions ensures that all employees follow the same procedures, reducing variability and errors.
Consistency in processes can lead to quicker production times, as employees become more proficient in their tasks.
Regularly reviewing and updating these instructions can help keep the processes up-to-date with the latest best practices.
Adopting Automation
Automation involves using technology to perform tasks without human intervention.
By automating repetitive and time-consuming tasks, manufacturers can increase production speed and reduce lead times.
Investing in automated machinery and equipment, such as robotic arms, conveyor belts, and automated quality control systems, can streamline production processes and improve overall efficiency.
Continuous Improvement and Monitoring
Continuous improvement is a fundamental concept in manufacturing that involves regularly analyzing and improving processes.
Monitoring performance and implementing improvements can lead to sustained reductions in lead times.
Key Performance Indicators (KPIs)
Tracking KPIs related to lead times can provide valuable insights into the performance of manufacturing processes.
Common KPIs include cycle time, on-time delivery rate, and yield rates.
By regularly analyzing these metrics, manufacturers can identify areas for improvement and develop strategies to enhance efficiency and reduce lead times.
Employee Training and Engagement
Well-trained and engaged employees are crucial for maintaining efficient manufacturing processes.
Regular training programs can equip employees with the necessary skills and knowledge to perform their tasks efficiently.
Moreover, involving employees in identifying and solving problems can foster a culture of continuous improvement.
When employees feel valued and engaged, they are more likely to contribute positively to reducing lead times.
Implementing Advanced Planning and Scheduling (APS)
Advanced Planning and Scheduling (APS) systems can optimize production planning and scheduling, significantly reducing lead times.
APS systems use algorithms and real-time data to create efficient production schedules that consider various constraints, such as machine capacity, labor availability, and material requirements.
Real-Time Data Analysis
Utilizing real-time data analysis can help manufacturers make informed decisions quickly.
APS systems can provide a comprehensive overview of the production process, enabling better decision-making and more effective resource allocation.
Real-time data analysis helps address issues promptly, reducing downtime and ensuring a smooth production flow.
Capacity Planning
Proper capacity planning ensures that manufacturing resources are utilized efficiently.
APS systems can analyze demand forecasts and match them with available production capacity, ensuring that there are no bottlenecks or underutilized resources.
Effective capacity planning can lead to more efficient production schedules and reduced lead times.
In conclusion, reducing lead times in manufacturing processes is vital for maintaining competitiveness and profitability.
By implementing lean manufacturing principles, optimizing supply chain management, enhancing workflow efficiency, continuously improving processes, and utilizing advanced planning and scheduling systems, manufacturers can achieve significant reductions in lead times.
Investing in these methods not only improves productivity but also leads to greater customer satisfaction and business success.
資料ダウンロード
QCD調達購買管理クラウド「newji」は、調達購買部門で必要なQCD管理全てを備えた、現場特化型兼クラウド型の今世紀最高の購買管理システムとなります。
ユーザー登録
調達購買業務の効率化だけでなく、システムを導入することで、コスト削減や製品・資材のステータス可視化のほか、属人化していた購買情報の共有化による内部不正防止や統制にも役立ちます。
NEWJI DX
製造業に特化したデジタルトランスフォーメーション(DX)の実現を目指す請負開発型のコンサルティングサービスです。AI、iPaaS、および先端の技術を駆使して、製造プロセスの効率化、業務効率化、チームワーク強化、コスト削減、品質向上を実現します。このサービスは、製造業の課題を深く理解し、それに対する最適なデジタルソリューションを提供することで、企業が持続的な成長とイノベーションを達成できるようサポートします。
オンライン講座
製造業、主に購買・調達部門にお勤めの方々に向けた情報を配信しております。
新任の方やベテランの方、管理職を対象とした幅広いコンテンツをご用意しております。
お問い合わせ
コストダウンが利益に直結する術だと理解していても、なかなか前に進めることができない状況。そんな時は、newjiのコストダウン自動化機能で大きく利益貢献しよう!
(Β版非公開)