- お役立ち記事
- Revolutionizing Japanese Manufacturing: Advanced Processing Techniques and Innovative Machine Tools
月間77,185名の
製造業ご担当者様が閲覧しています*
*2025年2月28日現在のGoogle Analyticsのデータより
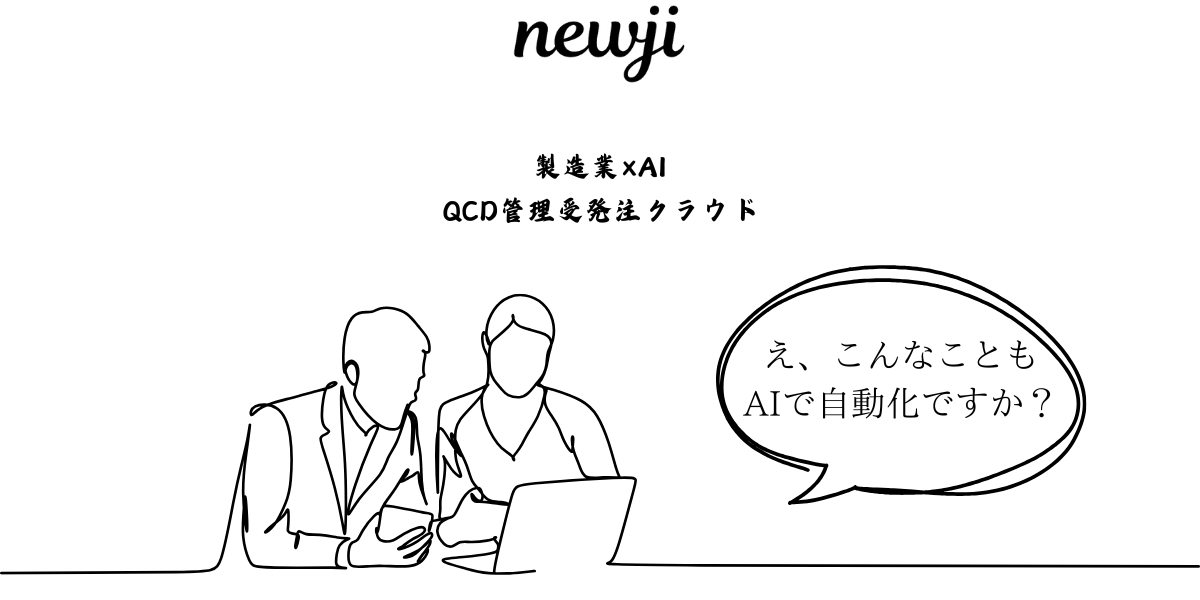
Revolutionizing Japanese Manufacturing: Advanced Processing Techniques and Innovative Machine Tools
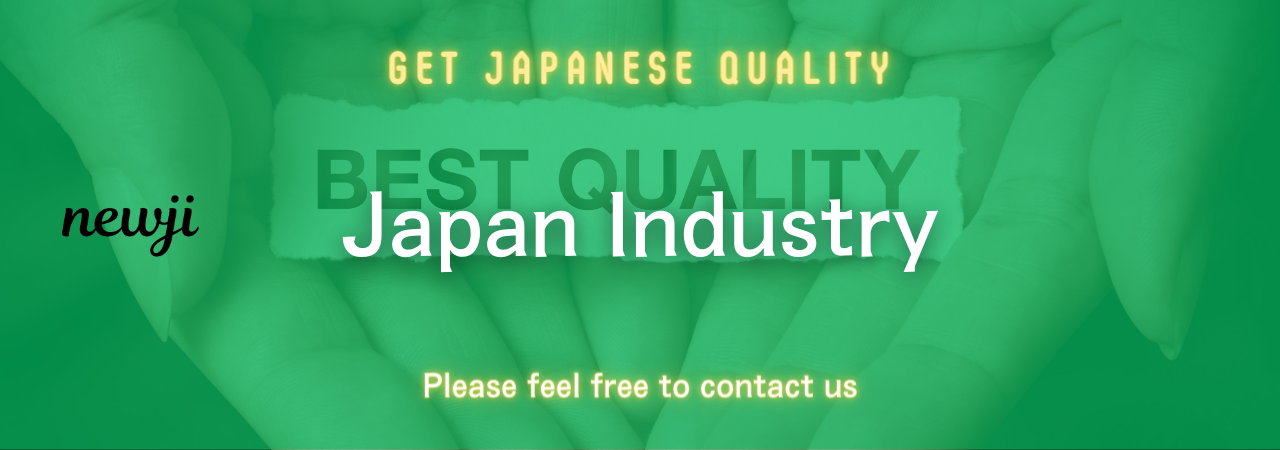
In recent years, Japanese manufacturing has undergone a transformation driven by advanced processing techniques and innovative machine tools. This revolution in the manufacturing sector has significantly elevated the quality, efficiency, and competitiveness of Japanese products in the global market. With over two decades of experience in procurement and purchasing, I have witnessed firsthand the essence of Japanese manufacturing and the transformative impact of their advanced methodologies. Here is a comprehensive exploration of these developments, highlighting practical insights, benefits, challenges, and best practices.
目次
Understanding Advanced Processing Techniques
Precision Engineering
Precision engineering is pivotal in the Japanese manufacturing landscape. This technique focuses on developing highly accurate manufacturing processes and tools that can produce parts with tight tolerances and superior finish. The major advantages of precision engineering include reduced waste, higher consistency, and improved product performance.
One notable example is the use of advanced Computer Numerical Control (CNC) machines, which enable the production of intricate parts with exceptional precision. These machines minimize human error and optimize production time by automating complex machining tasks.
Lean Manufacturing
Lean manufacturing, rooted in the principles established by Toyota, focuses on maximizing value while minimizing waste. This technique is integral to the efficiency and effectiveness of Japanese manufacturing.
Lean practices such as Just-In-Time (JIT) production, 5S methodology (Sort, Set in order, Shine, Standardize, Sustain), and continuous improvement (Kaizen) enhance productivity and reduce costs.
JIT ensures that materials and components are supplied exactly when needed, reducing inventory costs and streamlining production workflows. The 5S methodology creates organized and efficient workplaces, while Kaizen fosters a culture of continuous improvement, enabling ongoing enhancements in processes and quality.
Innovative Machine Tools
Robotics and Automation
Robotics and automation have revolutionized Japanese manufacturing by enhancing efficiency, precision, and safety. Industrial robots are deployed to perform repetitive and hazardous tasks, allowing human workers to focus on more strategic activities.
Collaborative robots (cobots) work alongside human operators, providing assistance in tasks such as assembly, inspection, and material handling. These robots are equipped with advanced sensors and artificial intelligence (AI) capabilities, enabling them to adapt to dynamic production environments and improve overall productivity.
Automation extends beyond robotics, encompassing technologies such as automated guided vehicles (AGVs) and automated storage and retrieval systems (AS/RS). AGVs transport materials within the factory, optimizing logistics and reducing lead times. AS/RS systems enhance inventory management by automating the storage and retrieval of goods.
Additive Manufacturing (3D Printing)
Additive manufacturing, commonly known as 3D printing, has gained prominence in Japanese manufacturing for its ability to create complex geometries and customized products with ease. This technology enables the layer-by-layer construction of objects, reducing material waste and allowing for rapid prototyping.
Japanese manufacturers leverage 3D printing for various applications, including aerospace, automotive, medical devices, and consumer goods. The flexibility, speed, and cost-effectiveness of additive manufacturing make it an indispensable tool for innovation and product development.
Advantages of Advanced Processing Techniques and Machine Tools
Enhanced Product Quality
The adoption of advanced processing techniques and innovative machine tools has significantly improved product quality. Precision engineering ensures that products meet stringent specifications, resulting in superior performance and durability. As a result, Japanese products are often regarded as benchmarks of excellence in the global market.
Increased Efficiency
Efficiency is a hallmark of Japanese manufacturing. Lean manufacturing practices, automation, and robotics streamline production processes, reducing downtime and optimizing resource utilization. This efficiency translates to shorter lead times, lower costs, and higher profitability.
Competitive Advantage
By embracing cutting-edge technologies and methodologies, Japanese manufacturers gain a competitive edge in the global market. The ability to produce high-quality, innovative products at competitive prices positions them favorably against international competitors.
Challenges and Considerations
Initial Investment
One of the significant challenges of implementing advanced processing techniques and machine tools is the substantial initial investment required. High-tech equipment, robotics, and automation systems come with a hefty price tag, posing a barrier for smaller manufacturers.
To mitigate this, companies can explore financing options, government incentives, and collaborative partnerships. Additionally, a clear return on investment (ROI) analysis can help justify the expenditure by demonstrating long-term benefits and cost savings.
Skilled Workforce
The integration of advanced technologies necessitates a skilled workforce capable of operating and maintaining sophisticated machinery. Training and development programs are essential to equip employees with the knowledge and skills required for these advanced roles.
Collaboration with educational institutions, industry associations, and training providers can facilitate the upskilling of the workforce. Moreover, fostering a culture of continuous learning and innovation within the organization can enhance employee engagement and retention.
Adaptability to Change
The rapid pace of technological advancements in manufacturing requires companies to remain adaptable and agile. Embracing change and staying updated with the latest trends and innovations are crucial to maintaining competitiveness.
Businesses must cultivate a mindset that embraces change and fosters experimentation. Regularly reviewing and updating manufacturing strategies, processes, and technologies will ensure that companies stay ahead of the curve.
Supplier Negotiation Techniques
Building Strong Relationships
Strong supplier relationships are fundamental to successful procurement and purchasing. Building trust and fostering open communication with Japanese suppliers can lead to mutually beneficial partnerships.
Regular face-to-face meetings, factory visits, and collaborative problem-solving sessions help establish rapport and understanding. Investing time in relationship-building activities demonstrates commitment and reliability, encouraging suppliers to go the extra mile in delivering quality products and services.
Understanding Cultural Nuances
Japanese business culture values respect, harmony, and consensus. Understanding these cultural nuances is essential for effective supplier negotiation. Politeness, humility, and patience go a long way in building rapport and fostering positive interactions.
Avoiding confrontation and embracing a collaborative approach are key. Decision-making in Japanese companies often involves consensus-building, requiring time and careful consideration. Being patient and allowing the process to unfold naturally will yield better results than rushing negotiations.
Leveraging Data and Analytics
Data-driven decision-making is a powerful tool in supplier negotiations. Leveraging data and analytics can provide valuable insights into supplier performance, market trends, and pricing dynamics.
By analyzing historical data, procurement teams can identify patterns, anticipate future demand, and negotiate favorable terms. Statistical models and predictive analytics can enhance negotiation strategies, enabling informed decision-making and minimizing risks.
Market Conditions and Trends
Industries Embracing Advanced Techniques
Several industries in Japan are at the forefront of adopting advanced processing techniques and innovative machine tools. The automotive sector, for instance, leverages precision engineering and automation to manufacture high-performance vehicles with exceptional quality and efficiency.
The electronics industry benefits from additive manufacturing, enabling the production of intricate components and prototypes swiftly. Similarly, the aerospace sector utilizes advanced machining capabilities to create lightweight and durable parts for aircraft.
Sustainability and Green Manufacturing
Sustainability has become a critical consideration in modern manufacturing. Japanese companies are increasingly adopting green manufacturing practices to reduce their environmental footprint. This includes the use of eco-friendly materials, energy-efficient processes, and waste reduction initiatives.
Advanced processing techniques contribute to sustainability by minimizing material waste, reducing energy consumption, and optimizing resources. Automation and robotics enhance efficiency, resulting in lower emissions and a smaller carbon footprint.
Best Practices for Implementing Advanced Techniques
Conducting Comprehensive Assessments
Before adopting advanced processing techniques and machine tools, conducting comprehensive assessments is crucial. This involves evaluating current processes, identifying bottlenecks, and understanding specific requirements.
A thorough assessment provides insights into areas that can benefit from automation, precision engineering, or other advanced methodologies. It also helps in prioritizing investments and aligning them with strategic goals.
Phased Implementation
Implementing advanced techniques in a phased manner allows companies to manage risks and ensure smooth transitions. Starting with pilot projects or specific production lines enables testing and refinement before full-scale deployment.
Phased implementation also allows for gradual upskilling of the workforce and provides time to address any challenges that may arise. This approach minimizes disruptions and ensures a steady progression toward advanced manufacturing capabilities.
Continuous Monitoring and Improvement
The journey toward advanced manufacturing is an ongoing process. Continuous monitoring and improvement are essential to sustain the benefits of advanced techniques and machine tools.
Regularly reviewing performance metrics, conducting audits, and soliciting feedback from employees and stakeholders facilitate iterative improvements. Embracing a culture of continuous improvement ensures that the organization remains innovative, efficient, and competitive.
Conclusion
The revolution in Japanese manufacturing, driven by advanced processing techniques and innovative machine tools, has set new standards for quality, efficiency, and competitiveness. Precision engineering, lean manufacturing, robotics, automation, and additive manufacturing are reshaping the landscape, enabling Japanese companies to produce superior products with remarkable precision and efficiency.
While the initial investment and need for a skilled workforce present challenges, the long-term benefits, including enhanced product quality, increased efficiency, and competitive advantage, outweigh the hurdles. The key to success lies in building strong supplier relationships, understanding cultural nuances, and leveraging data-driven decision-making.
Adopting best practices such as conducting comprehensive assessments, phased implementation, and continuous monitoring and improvement ensures a successful transition to advanced manufacturing. As industries continue to evolve, embracing these transformative technologies and methodologies will position Japanese manufacturers at the forefront of innovation and excellence in the global market.
By sharing these insights and experiences, I hope to contribute to the ongoing growth and success of Japanese manufacturing, ultimately benefiting procurement and purchasing professionals, suppliers, and consumers worldwide.
資料ダウンロード
QCD管理受発注クラウド「newji」は、受発注部門で必要なQCD管理全てを備えた、現場特化型兼クラウド型の今世紀最高の受発注管理システムとなります。
ユーザー登録
受発注業務の効率化だけでなく、システムを導入することで、コスト削減や製品・資材のステータス可視化のほか、属人化していた受発注情報の共有化による内部不正防止や統制にも役立ちます。
NEWJI DX
製造業に特化したデジタルトランスフォーメーション(DX)の実現を目指す請負開発型のコンサルティングサービスです。AI、iPaaS、および先端の技術を駆使して、製造プロセスの効率化、業務効率化、チームワーク強化、コスト削減、品質向上を実現します。このサービスは、製造業の課題を深く理解し、それに対する最適なデジタルソリューションを提供することで、企業が持続的な成長とイノベーションを達成できるようサポートします。
製造業ニュース解説
製造業、主に購買・調達部門にお勤めの方々に向けた情報を配信しております。
新任の方やベテランの方、管理職を対象とした幅広いコンテンツをご用意しております。
お問い合わせ
コストダウンが利益に直結する術だと理解していても、なかなか前に進めることができない状況。そんな時は、newjiのコストダウン自動化機能で大きく利益貢献しよう!
(β版非公開)