- お役立ち記事
- Revolutionizing Japanese Manufacturing: The Critical Role of Non-Destructive Testing (NDT)
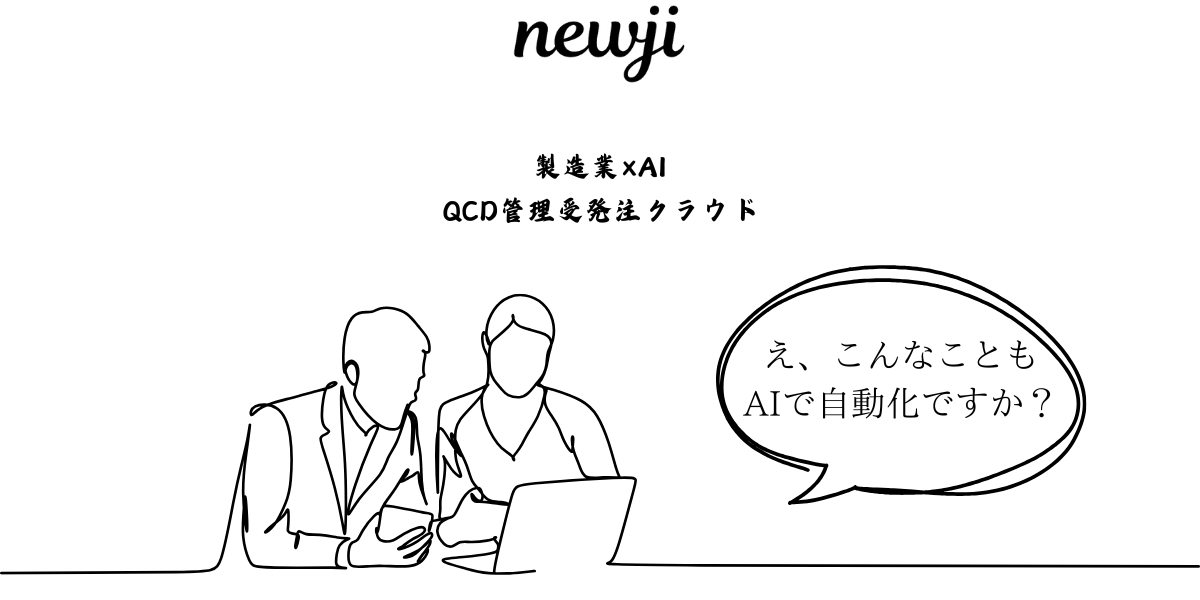
Revolutionizing Japanese Manufacturing: The Critical Role of Non-Destructive Testing (NDT)
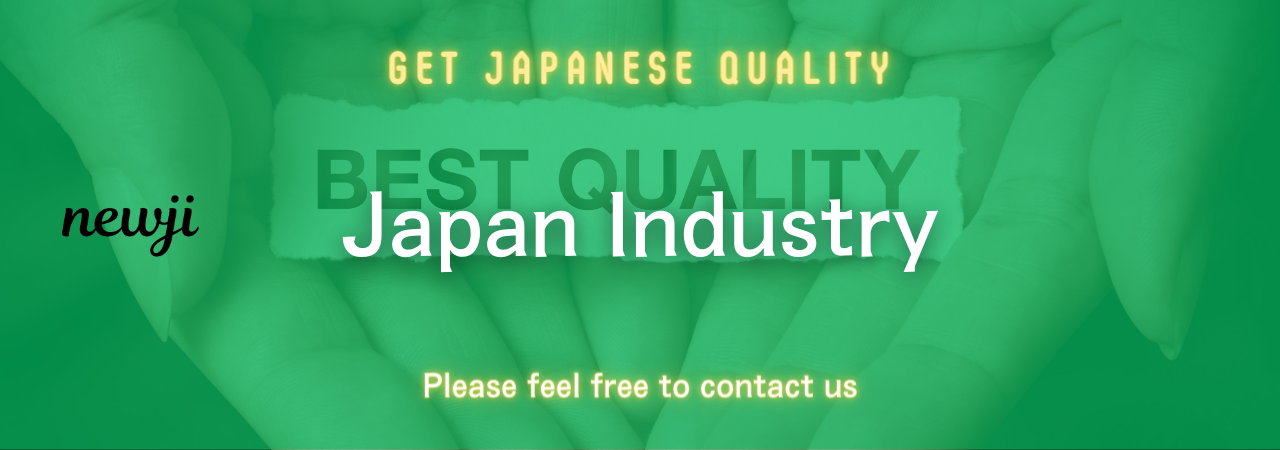
目次
Introduction to Non-Destructive Testing in Japanese Manufacturing
Non-Destructive Testing (NDT) has become a cornerstone in the evolution of Japanese manufacturing.
Japanese industries are renowned for their commitment to quality and precision.
NDT plays a vital role in maintaining these high standards without compromising the integrity of materials or products.
This article explores the critical role of NDT in revolutionizing Japanese manufacturing.
It delves into the practical aspects from a procurement and purchasing perspective.
Advantages and disadvantages are examined alongside supplier negotiation techniques, market conditions, and best practices.
The Importance of NDT in Japanese Manufacturing
Japanese manufacturing is synonymous with excellence and durability.
Achieving such high standards requires meticulous quality control.
NDT provides essential insights into the structural integrity and performance of materials and products.
It ensures that manufacturing processes meet stringent quality requirements without damaging the items being tested.
Enhancing Product Quality and Reliability
NDT techniques, such as ultrasonic testing and radiography, allow manufacturers to detect flaws and defects that are not visible to the naked eye.
This early detection prevents faulty products from reaching the market.
In industries like automotive and aerospace, where safety is paramount, NDT ensures that components can withstand operational stresses.
By maintaining high levels of product reliability, Japanese manufacturers strengthen their reputation globally.
Cost Efficiency and Waste Reduction
Implementing NDT can lead to significant cost savings.
By identifying defects early in the production process, manufacturers can avoid the costs associated with rework or scrapping faulty products.
NDT also minimizes material waste, contributing to more sustainable manufacturing practices.
This efficiency is crucial in Japan’s highly competitive manufacturing sector.
Procurement and Purchasing Considerations for NDT
Effective procurement and purchasing strategies are essential for integrating NDT into manufacturing processes.
Japanese companies prioritize relationships with reliable NDT suppliers to ensure consistent quality and performance.
Selecting the Right NDT Suppliers
Choosing the appropriate NDT suppliers involves evaluating their technical expertise and equipment.
Suppliers must offer a range of NDT services tailored to the specific needs of the manufacturer.
Japanese manufacturers often seek suppliers with a proven track record in their industry.
Quality certifications and adherence to international standards are critical factors in the selection process.
Evaluating Supplier Capabilities and Reliability
Assessing a supplier’s capabilities goes beyond their service offerings.
Japanese companies consider the supplier’s ability to deliver timely and accurate results.
Reliability in maintaining equipment and staying updated with the latest NDT technologies is also vital.
Building long-term relationships with dependable suppliers contributes to the overall efficiency of the manufacturing process.
Advantages of Implementing NDT in Manufacturing
The integration of NDT into manufacturing processes offers numerous benefits.
These advantages extend beyond quality control, impacting various aspects of production and business operations.
Improved Product Quality
NDT ensures that products meet high-quality standards by detecting internal and surface defects.
This leads to the production of more reliable and durable products.
Consistent quality enhances customer satisfaction and strengthens brand reputation.
Enhanced Safety
In industries where safety is critical, such as aerospace and automotive, NDT plays a crucial role in ensuring that components can withstand operational stresses.
This reduces the risk of failures that could lead to accidents or costly recalls.
Enhanced safety measures protect both consumers and the manufacturer’s reputation.
Cost Savings
Early detection of defects allows manufacturers to address issues before they escalate.
This proactive approach minimizes the costs associated with rework, scrap, and warranty claims.
Additionally, by optimizing the use of raw materials, NDT contributes to overall cost efficiency.
Regulatory Compliance
Adhering to international quality and safety standards is essential for Japanese manufacturers.
NDT helps ensure compliance with these regulations, facilitating smoother entry into global markets.
Compliance also reduces the risk of legal issues and associated penalties.
Disadvantages and Challenges of NDT
While NDT offers significant advantages, it also presents certain challenges.
Understanding these drawbacks is essential for effective implementation and management.
High Initial Investment
Implementing NDT requires substantial upfront investment in equipment and training.
High-quality NDT tools and technologies can be expensive, posing a barrier for smaller manufacturers.
Additionally, training personnel to effectively use NDT equipment involves ongoing costs.
Dependence on Skilled Personnel
NDT relies heavily on the expertise of skilled technicians.
A shortage of qualified NDT professionals can hinder the effectiveness of testing processes.
Continuous training and development are necessary to maintain a proficient workforce.
Time-Consuming Processes
Some NDT methods can be time-consuming, potentially slowing down production schedules.
Balancing thorough testing with efficient production is a challenge for manufacturers.
Implementing automated NDT systems can mitigate this issue but requires additional investment.
Technological Limitations
Not all NDT techniques are suitable for every material or product type.
Manufacturers must carefully select the appropriate methods to achieve accurate results.
Technological limitations can sometimes lead to incomplete assessments, compromising quality control.
Supplier Negotiation Techniques for NDT Services
Effective negotiation with NDT suppliers is crucial for securing favorable terms and ensuring quality services.
Japanese manufacturers employ strategic negotiation techniques to build strong supplier relationships.
Understanding Supplier Capabilities
Before entering negotiations, it is essential to thoroughly understand the supplier’s capabilities.
Assessing the range of NDT services, technological proficiency, and past performance provides a solid foundation for discussions.
Knowledge of the supplier’s strengths and limitations enables informed decision-making.
Building Long-Term Partnerships
Japanese companies often prioritize long-term relationships over short-term gains.
Establishing trust and mutual respect with suppliers fosters collaboration and reliability.
Long-term partnerships can lead to better pricing, priority service, and tailored solutions.
Leveraging Competitive Bidding
Utilizing competitive bidding processes encourages suppliers to offer the best possible terms.
Japanese manufacturers may solicit proposals from multiple NDT providers to compare pricing, services, and value-added benefits.
This approach ensures that the selected supplier meets both quality and cost expectations.
Negotiating Flexible Contracts
Flexibility in contracts allows manufacturers to adapt to changing requirements and market conditions.
Negotiating terms such as scalable services, adjustable pricing structures, and performance-based incentives can benefit both parties.
Flexible agreements enhance the ability to respond to unforeseen challenges and opportunities.
Market Conditions and Trends in NDT
The NDT market is continuously evolving, influenced by technological advancements and industry demands.
Japanese manufacturers must stay abreast of these trends to maintain a competitive edge.
Technological Advancements
Advancements in NDT technologies, such as digital imaging and automated inspection systems, are transforming the industry.
These innovations enhance the accuracy and efficiency of testing processes.
Japanese manufacturers are at the forefront of adopting these technologies to improve their quality control measures.
Integration with Industry 4.0
The integration of NDT with Industry 4.0 principles, including automation and data exchange, is gaining momentum.
Smart sensors and interconnected systems enable real-time monitoring and analysis of manufacturing processes.
This synergy enhances predictive maintenance and reduces downtime, contributing to overall factory efficiency.
Increasing Demand for Quality Assurance
Global markets demand higher standards of quality and reliability, driving the need for advanced NDT solutions.
Japanese manufacturers respond by enhancing their NDT capabilities to meet these expectations.
This focus on quality assurance helps maintain Japan’s reputation for manufacturing excellence.
Environmental and Sustainability Considerations
Sustainability is becoming a key consideration in manufacturing processes.
NDT contributes by minimizing material waste and optimizing resource usage.
Japanese companies are integrating eco-friendly NDT methods to align with environmental goals and regulatory requirements.
Best Practices for Implementing NDT in Manufacturing
Adopting best practices ensures the effective integration of NDT into manufacturing processes.
These practices enhance the benefits of NDT while mitigating potential challenges.
Comprehensive Training Programs
Investing in comprehensive training programs for NDT personnel is essential.
Skilled technicians are crucial for accurate and reliable testing results.
Ongoing education and certification ensure that staff remain proficient with the latest technologies and methodologies.
Regular Maintenance and Calibration of Equipment
Maintaining NDT equipment in optimal condition is critical for accurate results.
Regular maintenance and calibration prevent equipment malfunctions and measurement inaccuracies.
Implementing a strict maintenance schedule enhances the reliability of NDT processes.
Integration with Quality Management Systems
NDT should be seamlessly integrated into the overall quality management system.
Aligning NDT processes with quality objectives ensures consistency and effectiveness.
This integration facilitates continuous improvement and adherence to quality standards.
Data Management and Analysis
Effective data management is essential for leveraging NDT results.
Implementing robust data collection and analysis systems enables manufacturers to identify trends and make informed decisions.
Advanced software solutions can enhance the interpretation of NDT data, leading to better quality control and process optimization.
Collaborative Supplier Relationships
Building collaborative relationships with NDT suppliers fosters innovation and continuous improvement.
Engaging suppliers in quality initiatives and joint problem-solving enhances the effectiveness of NDT processes.
This collaboration leads to more efficient and reliable testing solutions.
Case Studies: Successful Implementation of NDT in Japanese Manufacturing
Examining real-world examples provides valuable insights into the effective use of NDT in manufacturing.
Japanese companies have demonstrated the successful integration of NDT in various industries.
Automotive Industry: Ensuring Component Integrity
A leading Japanese automotive manufacturer implemented ultrasonic NDT to inspect engine components.
This proactive approach identified micro-cracks and defects early in the production process.
As a result, the company reduced warranty claims and enhanced the durability of its vehicles.
The use of NDT contributed to maintaining the brand’s reputation for high-quality automobiles.
Aerospace Sector: Enhancing Safety Standards
A prominent aerospace manufacturer in Japan adopted radiographic NDT to examine critical aircraft parts.
This method ensured that components met stringent safety standards without compromising their structural integrity.
The integration of NDT into the production process minimized the risk of in-flight failures and reinforced the company’s commitment to safety.
Electronics Manufacturing: Improving Product Reliability
A Japanese electronics manufacturer utilized X-ray NDT to inspect printed circuit boards (PCBs).
This technique detected internal defects and soldering issues that could affect product performance.
By implementing NDT, the company enhanced the reliability of its electronic devices and reduced the incidence of returns and repairs.
Future Outlook: The Evolving Role of NDT in Japanese Manufacturing
The role of NDT in Japanese manufacturing is poised to grow as industries continue to seek higher levels of quality and efficiency.
Emerging technologies and evolving market demands will shape the future landscape of NDT.
Advancements in NDT Technologies
Continuous advancements in NDT technologies will enhance the precision and scope of testing.
Innovations such as automated inspection systems and artificial intelligence-driven analysis will further improve the effectiveness of NDT.
Japanese manufacturers are likely to lead in adopting and developing these cutting-edge technologies.
Expansion into New Industries
While NDT is already integral to industries like automotive and aerospace, its application is expanding into new sectors.
Fields such as renewable energy, medical devices, and advanced materials will increasingly rely on NDT for quality assurance.
This diversification offers opportunities for Japanese manufacturers to apply their NDT expertise in broader markets.
Enhanced Data Integration and Analytics
The integration of NDT data with broader manufacturing systems will enable more comprehensive analysis and decision-making.
Advanced analytics and machine learning will facilitate predictive maintenance and process optimization.
This holistic approach will drive further efficiencies and innovation in manufacturing processes.
Focus on Sustainability and Green Manufacturing
Sustainability considerations will continue to influence the adoption of NDT in manufacturing.
Eco-friendly NDT methods and practices will align with global sustainability goals and regulatory requirements.
Japanese manufacturers are expected to integrate sustainable NDT solutions to support environmentally responsible manufacturing.
Conclusion
Non-Destructive Testing is a pivotal element in the success and advancement of Japanese manufacturing.
Its ability to enhance product quality, ensure safety, and achieve cost efficiencies makes NDT indispensable.
From a procurement and purchasing perspective, selecting the right suppliers and negotiating favorable terms are critical for maximizing the benefits of NDT.
While challenges such as high initial investments and the need for skilled personnel exist, the advantages far outweigh the disadvantages.
Adopting best practices and staying abreast of market trends will ensure that Japanese manufacturers continue to lead in quality and innovation.
As technology evolves and new industries emerge, the role of NDT will only become more significant, cementing its place as a cornerstone of manufacturing excellence in Japan.
資料ダウンロード
QCD調達購買管理クラウド「newji」は、調達購買部門で必要なQCD管理全てを備えた、現場特化型兼クラウド型の今世紀最高の購買管理システムとなります。
ユーザー登録
調達購買業務の効率化だけでなく、システムを導入することで、コスト削減や製品・資材のステータス可視化のほか、属人化していた購買情報の共有化による内部不正防止や統制にも役立ちます。
NEWJI DX
製造業に特化したデジタルトランスフォーメーション(DX)の実現を目指す請負開発型のコンサルティングサービスです。AI、iPaaS、および先端の技術を駆使して、製造プロセスの効率化、業務効率化、チームワーク強化、コスト削減、品質向上を実現します。このサービスは、製造業の課題を深く理解し、それに対する最適なデジタルソリューションを提供することで、企業が持続的な成長とイノベーションを達成できるようサポートします。
オンライン講座
製造業、主に購買・調達部門にお勤めの方々に向けた情報を配信しております。
新任の方やベテランの方、管理職を対象とした幅広いコンテンツをご用意しております。
お問い合わせ
コストダウンが利益に直結する術だと理解していても、なかなか前に進めることができない状況。そんな時は、newjiのコストダウン自動化機能で大きく利益貢献しよう!
(Β版非公開)