- お役立ち記事
- Revolutionizing Japanese Manufacturing: The Growth and Impact of 3D Printing Technology
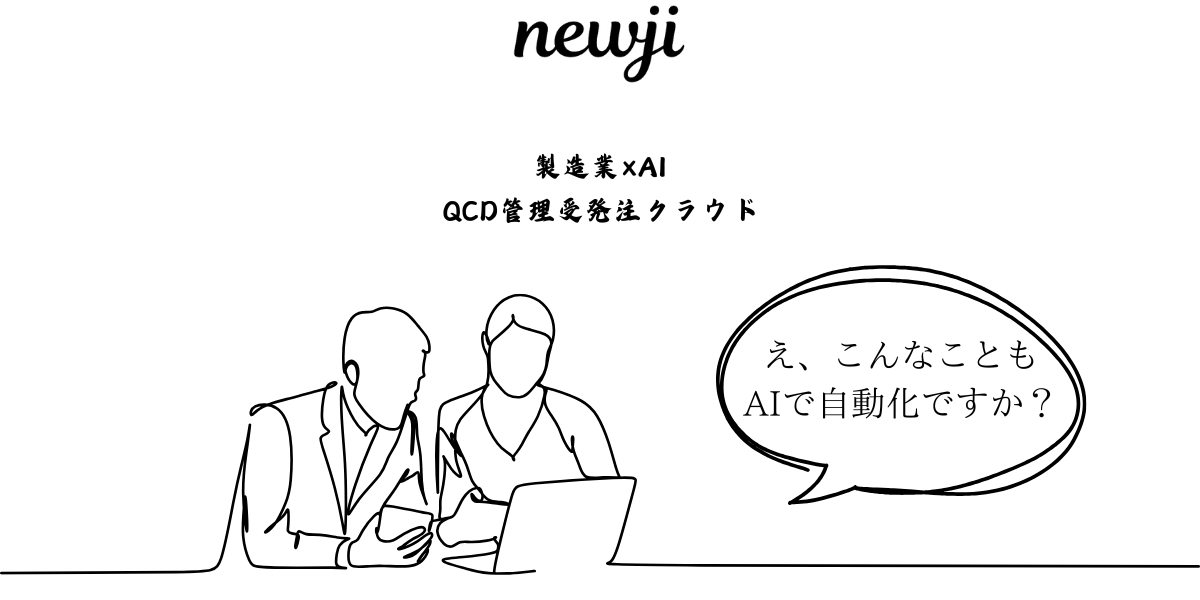
Revolutionizing Japanese Manufacturing: The Growth and Impact of 3D Printing Technology
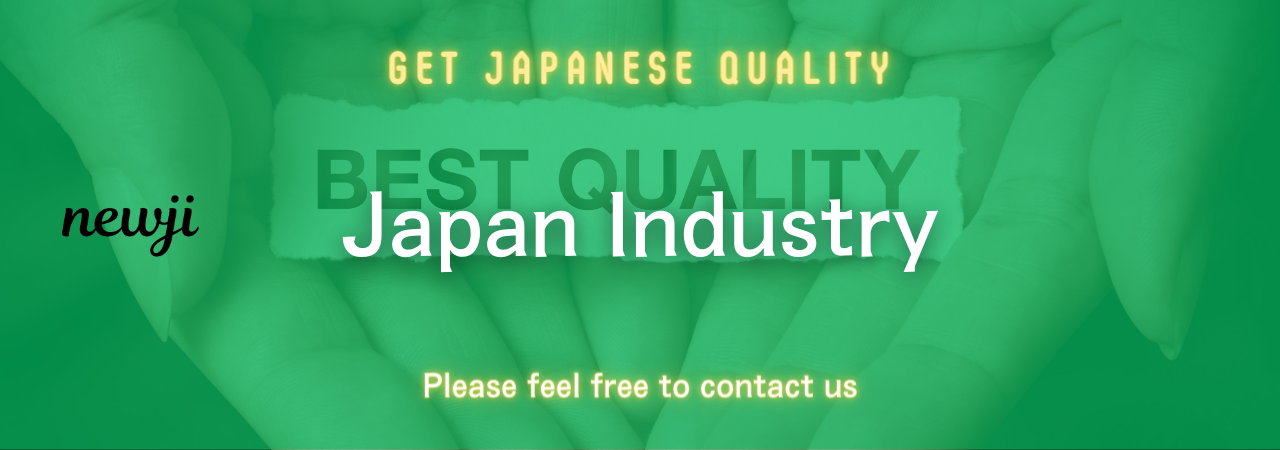
The rapid advance of 3D printing technology, also known as additive manufacturing, is bringing transformative change to industries worldwide. Japanese manufacturing, renowned for its precision, quality control, and efficiency, stands at the forefront of this revolution.
With a robust tradition in technological innovation, Japan’s integration of 3D printing technology is set to redefine the landscape in areas like prototyping, production workflows, and supply chain management.
目次
The Evolution of 3D Printing in Japan
The journey of 3D printing in Japan began in the early 1980s when the technology was initially developed. Japanese firms quickly recognized the potential of this breakthrough to enhance various aspects of manufacturing and invested heavily in research and development.
Today, the country is home to numerous cutting-edge 3D printing companies and research institutions. These entities work tirelessly not only to advance the capabilities of additive manufacturing but also to integrate them into existing production paradigms.
Prototyping and Product Development
In its early stages, 3D printing was primarily used for rapid prototyping. This allowed designers and engineers to create and test product models swiftly, accelerating the product development cycle.
Japanese companies are no strangers to intense global competition, and the ability to rapidly iterate on designs provides a significant advantage. By leveraging 3D printing, they can swiftly transition from concept to physical model, enabling real-time testing and evaluation.
Impact on Traditional Manufacturing
As 3D printing technology continues to mature, its impact is being felt across various manufacturing sectors in Japan.
Customization and Flexibility
Traditional manufacturing often relies on mass production techniques, which can be limiting when consumer demand trends toward personalized products. 3D printing breaks these constraints, allowing for the creation of bespoke items tailored to individual specifications without significant cost penalties.
This flexibility is particularly valuable in sectors like healthcare, where custom prosthetics and implants can be produced to meet the specific anatomical requirements of patients. Similarly, the automotive industry benefits from being able to produce complex, custom parts on-demand.
Supply Chain Optimization
3D printing holds promise for dramatically reshaping supply chains. By enabling on-demand production, the technology can reduce the need for large inventories and warehousing.
Parts and products can be printed as needed, reducing lead times and transportation costs. This transformation is especially beneficial for Japanese manufacturers who rely heavily on just-in-time (JIT) production systems.
Benefits of Integrating 3D Printing
The strategic incorporation of 3D printing within Japanese manufacturing brings numerous benefits.
Cost Efficiency
Although the initial investment in 3D printing technology can be high, the long-term cost benefits are significant. Traditional manufacturing methods often result in high material wastage, especially when machining complex parts.
3D printing, on the other hand, uses materials more efficiently, producing less scrap and reducing overall material costs. Additionally, the ability to consolidate multiple components into a single part can further streamline production processes and reduce assembly costs.
Increased Innovation
3D printing opens new horizons for innovation. Engineers and designers can experiment with complex geometries and structures that would be impossible or too costly to produce with conventional methods. This freedom fosters creativity and drives the development of advanced products with improved performance and functionality.
Improved Environmental Sustainability
Sustainability is a growing concern in manufacturing. 3D printing offers environmentally friendly benefits by minimizing waste and enabling the use of sustainable materials. Moreover, the potential for localized production reduces the carbon footprint associated with transporting goods over long distances.
Challenges and Limitations
Despite its numerous advantages, 3D printing in Japanese manufacturing does come with certain challenges and limitations that must be addressed.
Material Limitations
While advancements are continually being made, the range of materials available for 3D printing is still somewhat limited compared to traditional manufacturing. Some applications require materials with specific properties that are not yet achievable with current 3D printing technologies.
Production Speed
Although 3D printing excels in flexibility and customization, it can be slower than conventional manufacturing methods for high-volume production. This can be a hurdle in industries where speed is critical.
Best Practices for Integrating 3D Printing into Manufacturing
Successful integration of 3D printing into an existing manufacturing setup requires careful consideration and strategic planning.
Evaluating Applications
Not all parts or products are suitable for 3D printing. Manufacturers should conduct a thorough analysis to determine which components would benefit most from additive manufacturing—considering factors such as complexity, material requirements, and production volume.
Investing in Training
To fully capitalize on 3D printing technology, manufacturers must invest in training their workforce. Engineers and designers need to understand the possibilities and limitations of 3D printing, as well as how to optimize designs for additive manufacturing processes.
Collaborating with Suppliers
Working closely with 3D printing technology suppliers can provide insights into the latest advancements and best practices. Collaborations can foster innovation and ensure manufacturers are using the most efficient and effective technologies available.
Case Studies: 3D Printing in Japanese Manufacturing
Several Japanese manufacturers have already made significant strides in incorporating 3D printing into their operations.
Toyota
Toyota has been leveraging 3D printing for both prototyping and producing custom tooling and jigs. This not only accelerates the development of new vehicles but also enhances the efficiency of their assembly lines.
Panasonic
Panasonic utilizes 3D printing to create complex components for its electronic devices. The ability to iterate quickly on designs ensures they can keep pace with the rapid evolution of technology in the consumer electronics market.
Future Prospects of 3D Printing in Japan
The future of 3D printing in Japanese manufacturing looks promising. As the technology continues to advance, its applications will expand, driving further efficiency and innovation.
Emerging Materials
Research into new materials for 3D printing is ongoing. The development of advanced materials with enhanced properties will open up new possibilities for additive manufacturing across various industries.
Integration with Artificial Intelligence
Combining 3D printing with artificial intelligence (AI) and machine learning can optimize production processes and enhance quality control. AI algorithms can analyze data from previous prints to identify and correct potential issues, continually improving the reliability and precision of 3D printed products.
Decentralized Production
The potential for decentralized production, where products are manufactured close to the point of consumption rather than in centralized factories, could transform global supply chains. For Japanese manufacturers, this could mean establishing micro-factories worldwide, reducing transportation costs and lead times.
Conclusion
3D printing technology is poised to revolutionize Japanese manufacturing. By adopting this technology, manufacturers can achieve greater flexibility, cost efficiency, and innovation.
However, to fully realize the benefits, it is crucial to navigate the challenges and strategically integrate 3D printing into existing practices.
With the right approach, Japanese manufacturers can leverage 3D printing to reinforce their position as global leaders in high-quality, efficient production.
資料ダウンロード
QCD調達購買管理クラウド「newji」は、調達購買部門で必要なQCD管理全てを備えた、現場特化型兼クラウド型の今世紀最高の購買管理システムとなります。
ユーザー登録
調達購買業務の効率化だけでなく、システムを導入することで、コスト削減や製品・資材のステータス可視化のほか、属人化していた購買情報の共有化による内部不正防止や統制にも役立ちます。
NEWJI DX
製造業に特化したデジタルトランスフォーメーション(DX)の実現を目指す請負開発型のコンサルティングサービスです。AI、iPaaS、および先端の技術を駆使して、製造プロセスの効率化、業務効率化、チームワーク強化、コスト削減、品質向上を実現します。このサービスは、製造業の課題を深く理解し、それに対する最適なデジタルソリューションを提供することで、企業が持続的な成長とイノベーションを達成できるようサポートします。
オンライン講座
製造業、主に購買・調達部門にお勤めの方々に向けた情報を配信しております。
新任の方やベテランの方、管理職を対象とした幅広いコンテンツをご用意しております。
お問い合わせ
コストダウンが利益に直結する術だと理解していても、なかなか前に進めることができない状況。そんな時は、newjiのコストダウン自動化機能で大きく利益貢献しよう!
(Β版非公開)