- お役立ち記事
- Revolutionizing Japanese Manufacturing: The Role of Lead Sheets in Industrial Innovation
月間77,185名の
製造業ご担当者様が閲覧しています*
*2025年2月28日現在のGoogle Analyticsのデータより
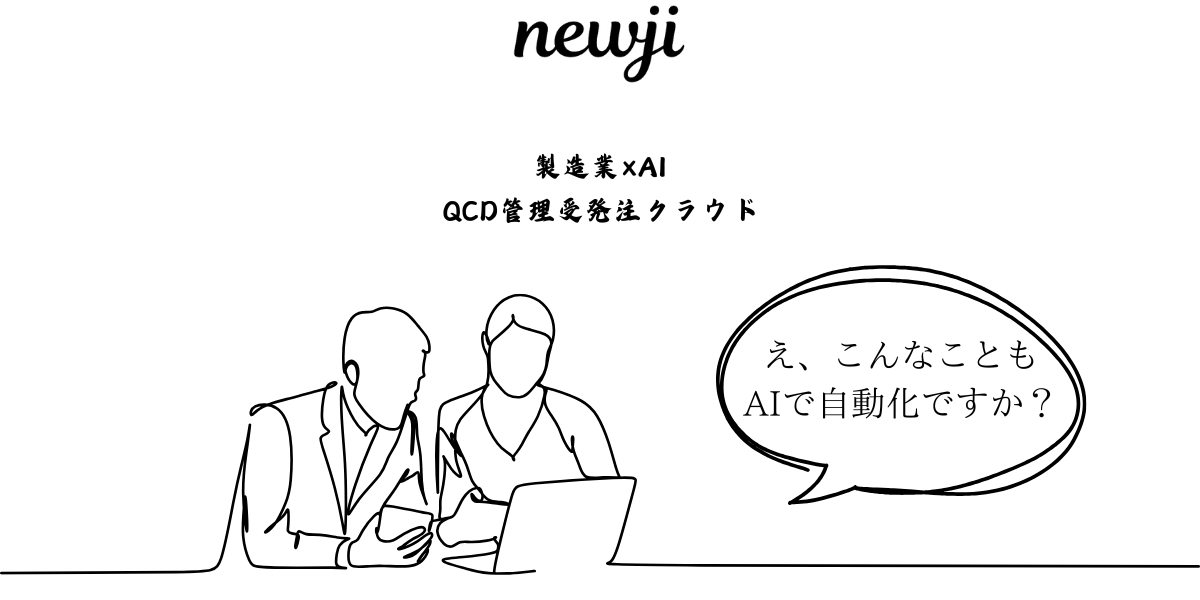
Revolutionizing Japanese Manufacturing: The Role of Lead Sheets in Industrial Innovation
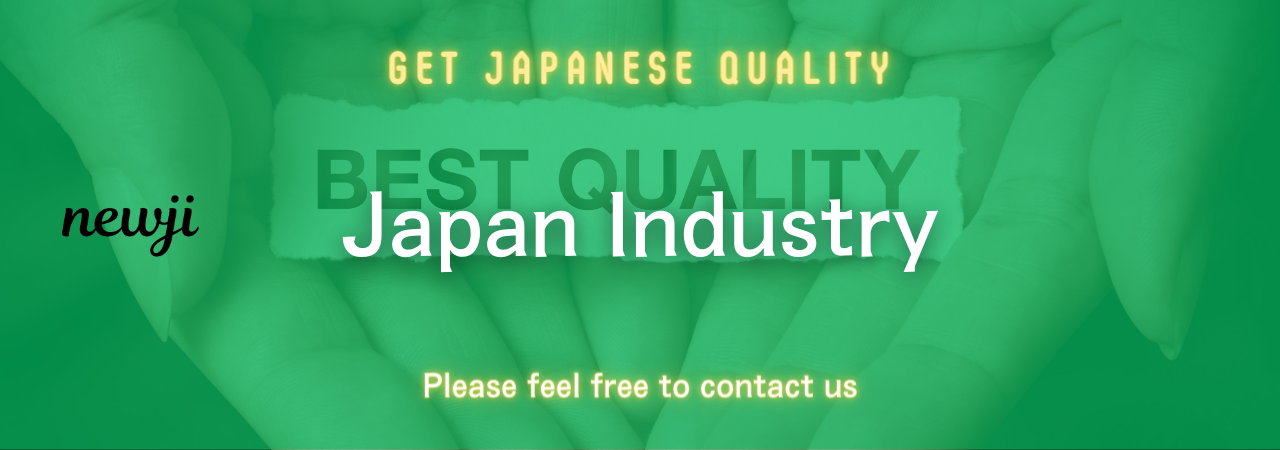
目次
Understanding Lead Sheets in Japanese Manufacturing
Definition and Applications
Lead sheets are thin, pliable sheets made primarily of lead, used extensively across various manufacturing sectors. In Japan, these sheets are integral to industries such as electronics, automotive, construction, and aerospace. Their primary applications include soldering components in electronic devices, providing radiation shielding in medical equipment, and serving as protective layers in battery manufacturing. The versatility of lead sheets makes them indispensable in ensuring the functionality and durability of numerous products.
Importance in Industrial Innovation
Japanese manufacturing is renowned for its emphasis on precision and quality. Lead sheets play a pivotal role in this reputation by enabling the development of high-performance products. For instance, in the electronics industry, lead sheets facilitate the creation of reliable solder joints, which are essential for the longevity and reliability of electronic devices. Additionally, advancements in lead sheet technology have spurred innovations in areas such as battery efficiency and radiation protection, contributing to broader industrial progress in Japan.
Advantages of Using Japanese Lead Sheets
Superior Quality and Precision
One of the standout advantages of Japanese lead sheets is their superior quality. Japanese manufacturers adhere to stringent quality control standards, ensuring that lead sheets meet precise specifications required by various industries. This level of precision minimizes defects and enhances the performance of end products. The consistency in thickness, purity, and mechanical properties of Japanese lead sheets sets them apart in the global market.
Technological Advancements
Japan is at the forefront of technological innovation, and this is evident in the production of lead sheets. Advanced manufacturing techniques, such as automated rolling and annealing processes, enable the production of lead sheets with optimal properties. Additionally, Japanese manufacturers invest heavily in research and development to improve the efficiency and environmental sustainability of lead sheet production. These technological advancements ensure that Japanese lead sheets remain competitive and meet the evolving needs of the market.
Reliability and Consistency
Reliability is a key factor in manufacturing, and Japanese lead sheets exemplify this attribute. Consistent quality ensures that products perform reliably over time, which is crucial for industries like automotive and aerospace where safety and performance are paramount. The dependable supply of high-quality lead sheets from Japanese manufacturers allows companies to maintain production schedules and meet customer demands without compromising on quality.
Disadvantages and Challenges
Cost Considerations
While Japanese lead sheets are known for their quality, they can be more expensive compared to alternatives from other regions. The high cost is often attributed to the advanced manufacturing technologies and stringent quality control measures employed by Japanese suppliers. For companies operating on tight budgets, the higher cost of Japanese lead sheets may pose a financial challenge, leading them to explore more cost-effective options.
Environmental Regulations
Lead is a hazardous material, and its use is subject to strict environmental regulations globally. In Japan, manufacturers must comply with rigorous standards to minimize lead exposure and manage waste responsibly. These regulations can increase production costs and limit the applications of lead sheets. Furthermore, the push towards more environmentally friendly materials may impact the demand for traditional lead sheets in the future.
Supply Chain Dependencies
Relying heavily on Japanese suppliers for lead sheets can create vulnerabilities in the supply chain. Geopolitical tensions, natural disasters, or economic fluctuations in Japan can disrupt the supply of lead sheets, affecting manufacturing operations worldwide. Diversifying suppliers and establishing contingency plans are essential strategies to mitigate these risks, but they require additional resources and strategic planning.
Procurement and Purchasing Strategies
Supplier Selection and Evaluation
Selecting the right supplier is crucial for ensuring the quality and reliability of lead sheets. Japanese manufacturers typically undergo a rigorous evaluation process that includes assessing the supplier’s production capabilities, quality control systems, and compliance with environmental regulations. Evaluating supplier performance through metrics such as on-time delivery, defect rates, and responsiveness helps in identifying reliable partners. Building a shortlist of potential suppliers based on these criteria ensures a steady supply of high-quality lead sheets.
Negotiation Techniques with Japanese Suppliers
Negotiating with Japanese suppliers requires a deep understanding of their business culture and practices. Emphasizing long-term partnerships rather than short-term gains is key to successful negotiations. Demonstrating respect, patience, and a commitment to mutual benefits fosters trust and collaboration. Additionally, being well-prepared with market data, understanding the supplier’s cost structures, and clearly outlining requirements and expectations can lead to more favorable terms. Flexible payment terms and volume commitments can also be effective negotiation tactics.
Building Long-term Relationships
Long-term relationships with Japanese suppliers are built on trust, reliability, and mutual respect. Investing time in understanding the supplier’s operations and cultural values aids in strengthening the partnership. Regular communication, visiting suppliers’ facilities, and engaging in joint development projects can enhance collaboration. A strong relationship ensures better service, priority during high-demand periods, and access to the latest innovations in lead sheet technology.
Market Conditions and Trends
Global Demand for Lead Sheets
The global demand for lead sheets is influenced by various factors, including the growth of electronics, automotive, and construction industries. In recent years, the surge in electronic device manufacturing has driven the demand for high-quality lead sheets used in soldering and assembly processes. Additionally, the automotive industry’s focus on safety and reliability continues to sustain the need for lead sheets in various applications. Understanding these demand drivers is essential for forecasting and planning procurement strategies.
Impact of Technological Innovations
Technological innovations are reshaping the lead sheet market. The development of lead-free alternatives and the improvement of lead sheet properties through advanced manufacturing techniques are significant trends. Innovations such as nanotechnology-enhanced lead sheets and environmentally friendly production processes are gaining traction. These advancements not only improve the performance of lead sheets but also address environmental and regulatory concerns, influencing the market dynamics.
Regulatory Landscape
The regulatory environment profoundly impacts the lead sheet market. Stringent regulations on lead emissions and waste management require manufacturers to adopt best practices and invest in compliance measures. International agreements and national laws governing the use of lead in products affect production processes and material choices. Staying abreast of regulatory changes and proactively adapting to new standards is crucial for maintaining market access and avoiding compliance-related disruptions.
Best Practices in Managing Japanese Lead Sheet Suppliers
Effective Communication and Collaboration
Clear and effective communication is essential for successful supplier management. Utilizing multiple communication channels, including face-to-face meetings, virtual conferencing, and written documentation, ensures that all parties are aligned. Collaborative approaches, such as joint product development and shared problem-solving initiatives, foster innovation and enhance the quality of lead sheets. Establishing open lines of communication helps in addressing issues promptly and maintaining a smooth supply chain.
Quality Control and Assurance
Implementing robust quality control measures is vital for maintaining the integrity of lead sheets. Conducting regular inspections and audits of supplier facilities ensures adherence to quality standards. Utilizing statistical process control techniques and quality assurance protocols helps in identifying and mitigating defects early in the production process. Collaborating with suppliers to implement continuous improvement programs enhances overall product quality and reduces the incidence of defects.
Leveraging Technology for Supplier Management
Modern technologies play a significant role in managing supplier relationships effectively. Enterprise Resource Planning (ERP) systems, supplier management software, and data analytics tools provide valuable insights into supplier performance and market trends. These technologies facilitate real-time tracking of orders, inventory levels, and delivery schedules, enabling proactive decision-making. Additionally, adopting digital platforms for collaboration and communication enhances transparency and efficiency in supplier interactions.
Case Studies: Successful Integration of Lead Sheets in Japanese Manufacturing
Example 1: Automotive Industry
A leading Japanese automotive manufacturer integrated high-precision lead sheets into their assembly line to enhance the reliability of electrical systems in vehicles. By collaborating closely with a trusted supplier, they implemented advanced quality control measures that reduced solder joint failures by 30%. This integration not only improved vehicle performance but also strengthened the company’s reputation for quality and reliability in the competitive automotive market.
Example 2: Electronics Sector
A major Japanese electronics company adopted innovative lead sheet technology to develop more efficient and compact circuit boards for consumer electronics. Through a strategic partnership with a lead sheet supplier, they leveraged cutting-edge manufacturing techniques to produce thinner and more conductive lead sheets. This advancement enabled the creation of slimmer devices with improved performance, giving the company a competitive edge in the fast-evolving electronics market.
Future Outlook
Innovations on the Horizon
The future of lead sheets in Japanese manufacturing is poised for continued innovation. Advancements in material science are leading to the development of lead sheets with enhanced properties, such as increased strength, flexibility, and conductivity. Additionally, the integration of smart technologies, such as embedded sensors within lead sheets, is expected to create new applications in industries like healthcare and automotive. These innovations will drive the next wave of industrial advancements and maintain Japan’s leadership in manufacturing excellence.
Anticipated Market Shifts
Market shifts are anticipated as industries move towards more sustainable and eco-friendly materials. The demand for lead-free alternatives is likely to grow, influenced by environmental regulations and consumer preferences. However, high-performance applications will continue to rely on traditional lead sheets due to their unmatched properties. Balancing the transition to sustainable materials while maintaining the benefits of lead sheets will be a critical challenge for Japanese manufacturers. Diversifying product offerings and investing in lead-free technologies will be essential strategies to navigate these market shifts.
Conclusion
Lead sheets are a cornerstone of Japanese manufacturing, underpinning innovations across various industries. Their superior quality, precision, and reliability make them invaluable in sectors such as electronics, automotive, and aerospace. Despite challenges like higher costs and stringent environmental regulations, the advantages of Japanese lead sheets continue to drive their global demand. Effective procurement and purchasing strategies, including careful supplier selection, negotiation, and long-term relationship building, are essential for maximizing the benefits of these materials. As the market evolves, ongoing technological advancements and a focus on sustainability will shape the future of lead sheets in Japanese manufacturing. By adhering to best practices and leveraging their expertise, Japanese manufacturers can continue to revolutionize industrial innovation through the strategic use of lead sheets.
資料ダウンロード
QCD管理受発注クラウド「newji」は、受発注部門で必要なQCD管理全てを備えた、現場特化型兼クラウド型の今世紀最高の受発注管理システムとなります。
ユーザー登録
受発注業務の効率化だけでなく、システムを導入することで、コスト削減や製品・資材のステータス可視化のほか、属人化していた受発注情報の共有化による内部不正防止や統制にも役立ちます。
NEWJI DX
製造業に特化したデジタルトランスフォーメーション(DX)の実現を目指す請負開発型のコンサルティングサービスです。AI、iPaaS、および先端の技術を駆使して、製造プロセスの効率化、業務効率化、チームワーク強化、コスト削減、品質向上を実現します。このサービスは、製造業の課題を深く理解し、それに対する最適なデジタルソリューションを提供することで、企業が持続的な成長とイノベーションを達成できるようサポートします。
製造業ニュース解説
製造業、主に購買・調達部門にお勤めの方々に向けた情報を配信しております。
新任の方やベテランの方、管理職を対象とした幅広いコンテンツをご用意しております。
お問い合わせ
コストダウンが利益に直結する術だと理解していても、なかなか前に進めることができない状況。そんな時は、newjiのコストダウン自動化機能で大きく利益貢献しよう!
(β版非公開)