- お役立ち記事
- Revolutionizing Japanese Manufacturing with Advanced Inspection Devices: Ensuring Top-Quality Production
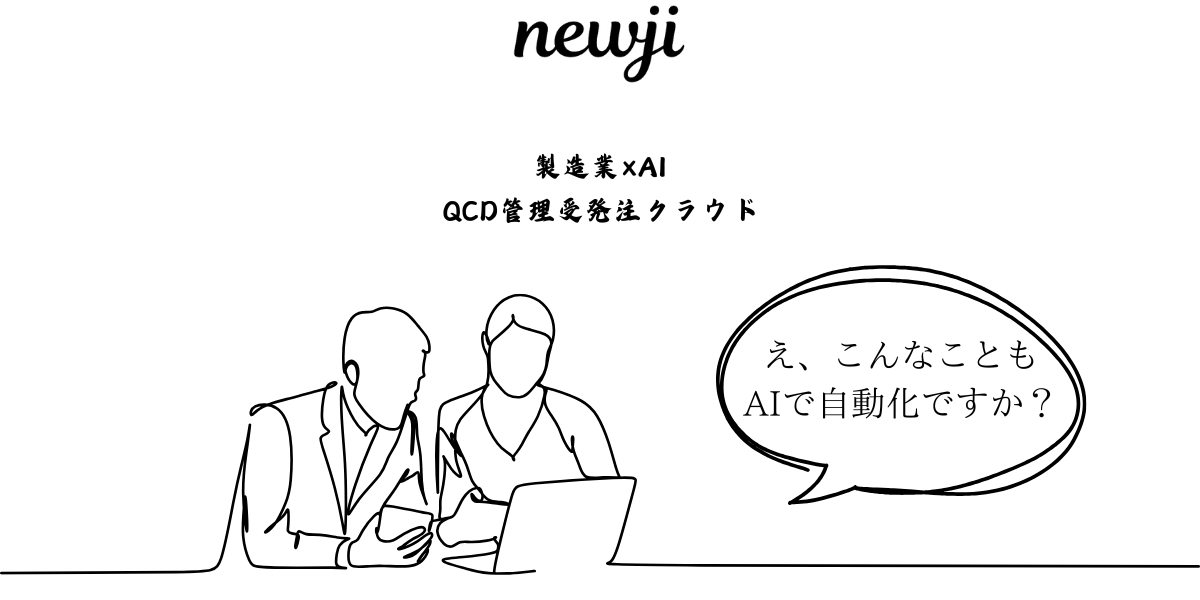
Revolutionizing Japanese Manufacturing with Advanced Inspection Devices: Ensuring Top-Quality Production
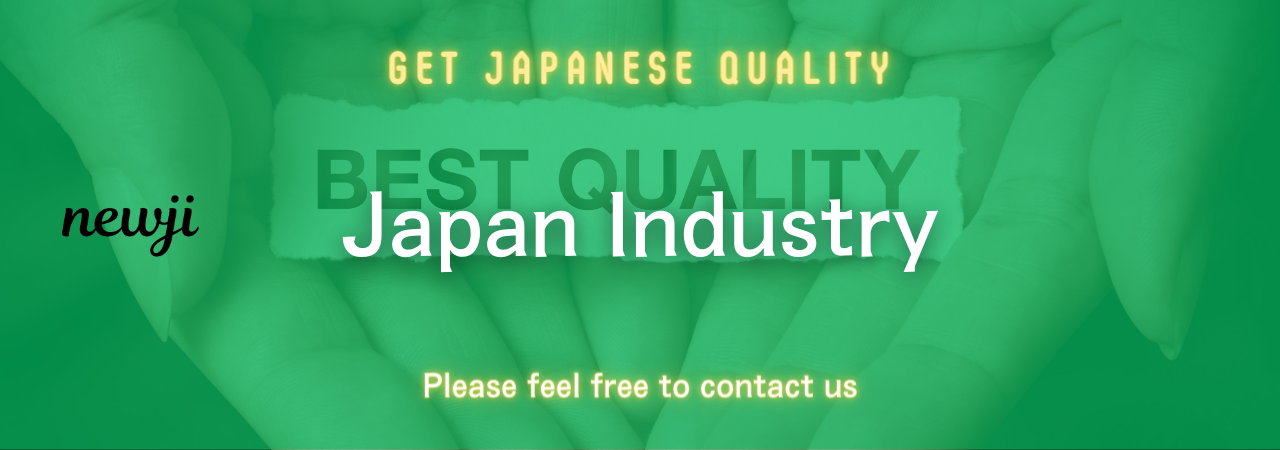
目次
Introduction
Manufacturing is at the heart of Japan’s global competitive edge. Renowned for its precision, innovation, and adherence to the highest quality standards, Japanese manufacturing has set the gold standard in numerous industries. One of the key pillars upholding this formidable reputation is the use of advanced inspection devices. These technologies not only ensure top-quality production but also act as catalysts for continuous improvement and efficiency.
In this article, we will delve into the various aspects of implementing advanced inspection devices in Japanese manufacturing. From the advantages and disadvantages, supplier negotiation techniques, market conditions, and best practices, this comprehensive guide will provide you with actionable insights into how inspection technologies are revolutionizing the manufacturing sector in Japan.
Why Advanced Inspection Devices are Essential
Ensuring Unwavering Quality
The primary benefit of advanced inspection devices is their ability to maintain stringent quality standards. By utilizing technologies such as optical inspection systems, Coordinate Measuring Machines (CMM), and AI-based anomaly detection, manufacturers can identify defects at microscopic levels. This is essential for industries that require impeccable precision, such as automotive, aerospace, and medical devices.
Reducing Waste and Costs
Advanced inspection devices contribute to significant cost savings by reducing waste. With accurate real-time data on production quality, companies can minimize the number of defective products and reduce material scrap. This not only lowers production costs but also aligns with sustainable manufacturing practices.
Enhancing Efficiency
Incorporating advanced inspection technologies into the production process can streamline operations and reduce bottlenecks. Automated inspection systems that integrate with manufacturing execution systems (MES) can offer instantaneous feedback and adjustments. This results in a smoother, more efficient production line, reducing downtime and increasing throughput.
Advantages and Disadvantages of Advanced Inspection Devices
Advantages
1. **Precision and Accuracy**: Advanced inspection devices offer unparalleled precision, ensuring that each product meets stringent quality standards.
2. **Real-time Feedback**: These devices provide immediate results, allowing for quick adjustments and minimizing downtime.
3. **Cost Savings**: By reducing waste and improving efficiency, advanced inspection technologies can significantly lower operational costs.
4. **Sustainability**: Reducing scrap and energy consumption aligns with green manufacturing initiatives, enhancing the company’s environmental responsibility and public image.
5. **Scalability**: Technologies can be scaled up or down depending on the production volume, making them versatile for various manufacturing environments.
Disadvantages
1. **High Initial Costs**: Investment in advanced inspection devices can be significant, which might be a barrier for smaller manufacturers.
2. **Training Requirements**: Employees need to be trained to operate new technologies effectively, which requires time and resources.
3. **Maintenance**: Advanced devices require regular maintenance and calibration to function optimally, adding to the operational overhead.
4. **Integration Challenges**: Incorporating new inspection technologies into existing production lines can be challenging and may require modification of current processes.
Supplier Negotiation Techniques
Negotiating with suppliers of advanced inspection devices necessitates a strategic approach. Here are some proven techniques:
Understand Your Needs
Be clear about your specific requirements and expectations concerning inspection devices. This includes the types of defects you want to detect, the production volume, and the integration capabilities with your existing systems.
Research and Shortlist
Conduct thorough research to identify potential suppliers. Look for those with a proven track record and expertise in your industry. Shortlist suppliers who offer the technology that best suits your needs.
Request Demonstrations
Before making any decisions, request demonstrations of the inspection devices. This allows you to evaluate their efficacy and compatibility with your production line.
Negotiate Terms
Negotiating isn’t just about price. Consider terms such as warranty, maintenance services, training programs for your staff, and software updates. Aim for a comprehensive package that provides long-term value.
Form Long-term Relationships
Building a long-term relationship with suppliers can result in better service, priority support, and potentially better pricing in future purchases. Mutual trust and ongoing collaboration can be highly beneficial.
Market Conditions
The market for advanced inspection devices in Japan is highly competitive and dynamic. Key players include both domestic and international firms, offering a wide range of devices tailored for various industries.
Domestic vs. International Suppliers
Japanese manufacturers often prefer domestic suppliers due to geographic proximity, cultural alignment, and easier communication. However, international suppliers bring diverse technologies and competitive pricing.
Technological Advancements
Rapid advancements in AI, machine learning, and sensor technology are constantly shaping the market for inspection devices. Staying updated with the latest developments is crucial in making informed procurement decisions.
Regulatory Environment
Compliance with local and international standards is essential. Ensure that the inspection devices meet all relevant quality and safety regulations.
Best Practices for Implementing Advanced Inspection Devices
Successful implementation of advanced inspection devices requires meticulous planning and execution. Here are some best practices:
Conduct a Needs Assessment
Begin with a comprehensive needs assessment to determine the specific requirements of your production line. Understand the types of defects that need to be inspected and the acceptable tolerance levels.
Choose the Right Technology
Select inspection devices that align with your assessment. For instance, if your industry demands high precision, consider CMMs or laser scanning systems. For real-time defect detection, AI-based optical inspection may be more suitable.
Integration with Existing Systems
Ensure that the new devices can seamlessly integrate with your current manufacturing execution systems (MES) and other production management software. This enables efficient data flow and real-time adjustments.
Training and Support
Provide comprehensive training to your staff to operate the new technologies effectively. Utilize supplier support and training programs to ensure optimal usage.
Regular Maintenance and Updates
Establish a maintenance schedule to keep the devices calibrated and functioning accurately. Stay updated with software upgrades and new features to continually enhance inspection capabilities.
Continuous Improvement
Monitor the performance of the inspection devices and gather data for continuous improvement. Use the insights gained to refine processes, identify areas for enhancement, and implement corrective actions promptly.
Conclusion
Integrating advanced inspection devices into Japanese manufacturing is a game-changer, ensuring top-quality production and maintaining a competitive edge in the global market. While the initial investment and integration challenges can be daunting, the long-term benefits of precision, efficiency, and cost savings make it a worthwhile endeavor.
By employing effective supplier negotiation techniques, understanding current market conditions, and following best practices for implementation, manufacturers can successfully revolutionize their production processes. The journey towards excellence is an ongoing one, but with the right tools and strategies, Japanese manufacturing can continue to set the benchmark for quality and innovation.
資料ダウンロード
QCD調達購買管理クラウド「newji」は、調達購買部門で必要なQCD管理全てを備えた、現場特化型兼クラウド型の今世紀最高の購買管理システムとなります。
ユーザー登録
調達購買業務の効率化だけでなく、システムを導入することで、コスト削減や製品・資材のステータス可視化のほか、属人化していた購買情報の共有化による内部不正防止や統制にも役立ちます。
NEWJI DX
製造業に特化したデジタルトランスフォーメーション(DX)の実現を目指す請負開発型のコンサルティングサービスです。AI、iPaaS、および先端の技術を駆使して、製造プロセスの効率化、業務効率化、チームワーク強化、コスト削減、品質向上を実現します。このサービスは、製造業の課題を深く理解し、それに対する最適なデジタルソリューションを提供することで、企業が持続的な成長とイノベーションを達成できるようサポートします。
オンライン講座
製造業、主に購買・調達部門にお勤めの方々に向けた情報を配信しております。
新任の方やベテランの方、管理職を対象とした幅広いコンテンツをご用意しております。
お問い合わせ
コストダウンが利益に直結する術だと理解していても、なかなか前に進めることができない状況。そんな時は、newjiのコストダウン自動化機能で大きく利益貢献しよう!
(Β版非公開)