- お役立ち記事
- Revolutionizing Japanese Manufacturing with the Ultimate Equipment Data Collection Tool
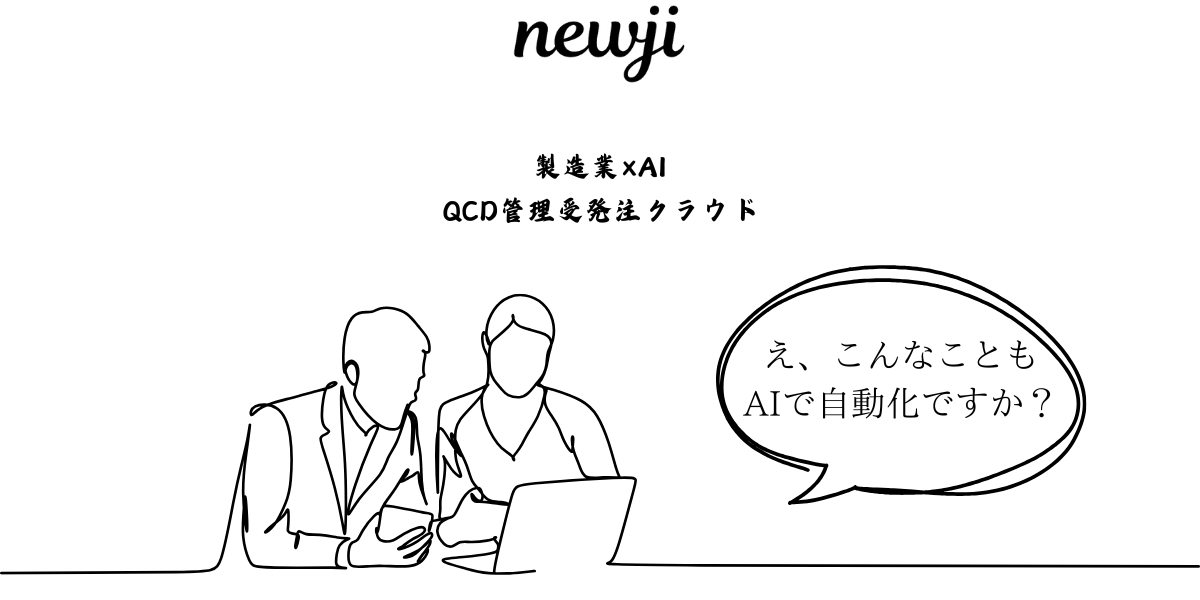
Revolutionizing Japanese Manufacturing with the Ultimate Equipment Data Collection Tool
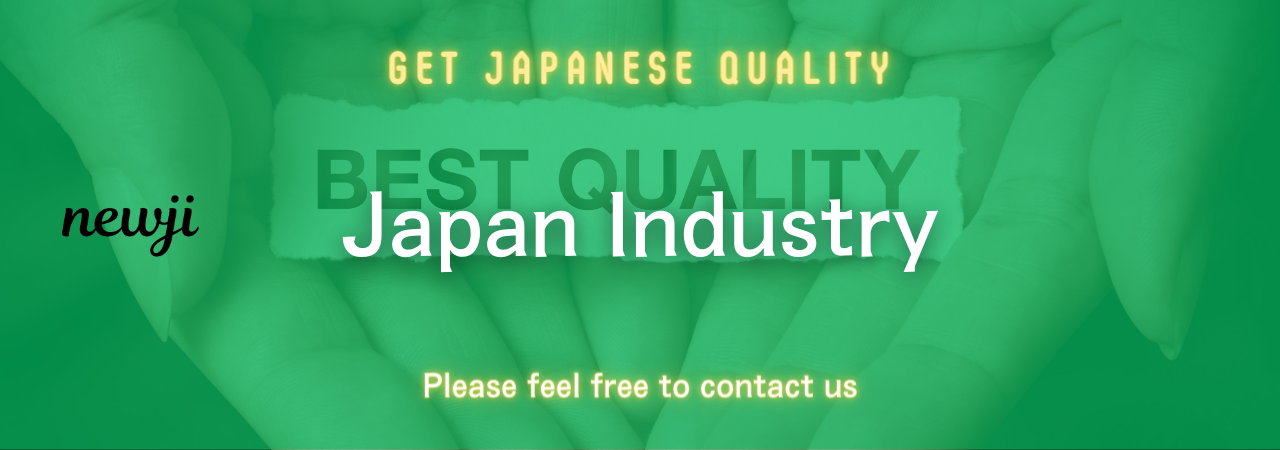
目次
Introduction
Japanese manufacturing has long been synonymous with precision, quality, and efficiency.
The backbone of this reputation lies in the meticulous data collection and analysis practices employed across production lines.
With advancements in technology, the development of sophisticated equipment data collection tools has been nothing short of revolutionary.
This article will explore the transformative impact of these tools on Japanese manufacturing by delving into their practical applications, advantages and disadvantages, supplier negotiation techniques, market conditions, and best practices.
The Evolution of Equipment Data Collection in Japanese Manufacturing
Manufacturers in Japan have always embraced a kaizen philosophy, focusing on continuous improvement and waste reduction.
However, the methods of collecting and analyzing factory data have evolved dramatically over the past few decades.
Traditional manual data collection methods, though reliable, were time-consuming and prone to human error.
The integration of digital tools has reshaped this landscape, enabling real-time data acquisition and analysis.
Traditional Methods
Japanese factories initially relied on manual logs and charts to track equipment performance, downtime, and maintenance schedules.
Operators were tasked with documenting every aspect of machinery operation.
Although this process provided valuable insights, it was labor-intensive and lacked the immediacy required for swift decision-making.
Digital Transformation
The advent of industrial automation and the Internet of Things (IoT) has ushered in an era where data collection is automated, precise, and instantaneous.
Sensors and interconnected devices continuously monitor equipment conditions, feeding data into centralized systems for real-time analysis.
This transformation enables proactive maintenance, optimized workflows, and enhances overall productivity.
Advantages of Modern Data Collection Tools
The implementation of advanced equipment data collection tools offers myriad advantages, propelling Japanese manufacturing to new heights.
Real-time Monitoring
With sensors and IoT devices attached to machinery, data is collected and analyzed in real-time, providing instant feedback on equipment health and performance.
This immediacy allows for rapid identification and rectification of issues, minimizing downtime and maintaining production efficiency.
Predictive Maintenance
One of the standout benefits is the ability to perform predictive maintenance.
By analyzing historical data and identifying trends, these tools can predict equipment failures before they occur, scheduling maintenance at the most opportune times.
This approach prevents unexpected breakdowns and extends the lifespan of machinery.
Enhanced Quality Control
Modern data collection systems offer detailed insights into every production step.
This comprehensive visibility ensures that any deviation from quality standards is promptly detected and corrected, reducing defect rates and bolstering product reliability.
Increased Efficiency
Automation reduces the need for manual data entry, freeing up human resources for more strategic tasks.
Additionally, data-driven insights guide process optimization, eliminating bottlenecks, and streamlining operations.
Challenges and Considerations
While the benefits are clear, implementing these sophisticated tools comes with its set of challenges.
Initial Investment
The cost of acquiring and integrating modern equipment data collection systems can be substantial.
Businesses must consider hardware, software, and the necessary infrastructure modifications.
However, the long-term gains in efficiency and reduction in operational costs often justify the initial expenditure.
Data Security
With increased digitization comes the added risk of cyber threats.
Ensuring robust cybersecurity measures are in place is imperative to protect sensitive production data from malicious attacks.
Skill Gap
Transitioning to advanced data collection methods requires a workforce proficient in handling modern technologies.
Continual training and development programs must be established to equip employees with the necessary skills.
Negotiating with Suppliers for Data Collection Tools
Securing the best deals on equipment data collection tools involves strategic negotiation tactics with suppliers.
Research and Due Diligence
Thoroughly researching potential suppliers and understanding their offerings is the first step.
Comparing product features, pricing, and post-purchase support can provide a clearer picture of the best value proposition.
Leverage Relationships
Building strong, long-term relationships with suppliers can be beneficial.
A reliable rapport can lead to better terms, priority service, and faster resolution of issues.
Volume Discounts
Purchasing in bulk can often secure significant discounts.
Negotiating a bundled package that includes hardware, software, and maintenance services can also result in better overall pricing.
Customization and Flexibility
Suppliers may provide customization options to tailor the data collection systems to specific production needs.
Negotiating flexibility in terms of payment schedules and upgrade options can further align with budget constraints.
Understanding Market Conditions
The market for equipment data collection tools is dynamic, influenced by technological advancements and manufacturing trends.
Technological Innovations
Staying abreast of the latest technological trends helps in making informed procurement decisions.
The integration of AI and Machine Learning in data analytics, for instance, offers advanced predictive capabilities that can revolutionize maintenance strategies.
Market Competition
A competitive market can drive innovation and lower prices.
Engaging with multiple suppliers and understanding their competitive advantages can ensure access to the best tools at optimal prices.
Regulatory Compliance
Compliance with local and international regulations is critical.
Ensuring that the chosen data collection tools meet industry standards and regulatory requirements is essential to avoid legal complications and ensure smooth operations.
Best Practices for Implementing Data Collection Tools
To maximize the benefits of equipment data collection tools, certain best practices should be followed:
Define Clear Objectives
Before implementation, it is crucial to define the specific objectives and expected outcomes of deploying the data collection tools.
This might include targets for reducing downtime, improving product quality, or optimizing maintenance schedules.
Phased Implementation
Implementing the system in phases can help in managing the transition smoothly.
Starting with critical equipment and gradually extending to other machinery allows for resolving any challenges incrementally.
Continuous Training
Ensuring that the workforce is adept at using these tools is essential.
Regular training sessions and workshops can keep employees updated on new features and best practices, ensuring seamless integration into daily operations.
Regular Review and Optimization
Continually reviewing the data collected and the insights generated can help in refining the processes further.
Periodic audits of the system’s performance can identify areas for improvement and ensure that the tools consistently deliver value.
Case Studies: Success Stories in Japanese Manufacturing
Automotive Industry
In the automotive sector, a leading Japanese manufacturer implemented an advanced data collection system across its production lines.
By utilizing predictive maintenance, they achieved a 30% reduction in unexpected equipment failures and a 25% increase in production efficiency.
The real-time monitoring capabilities also improved response times, ensuring that quality standards were consistently met.
Electronics Manufacturing
An electronics manufacturer leveraged IoT-enabled data collection tools to enhance their quality control processes.
The detailed insights provided by the system allowed for early detection of defects, reducing rework rates by 20%.
Additionally, the optimization of production schedules based on data analysis led to a significant reduction in lead times.
Food Processing Industry
A major player in Japan’s food processing industry adopted a comprehensive data collection system to monitor their processing lines.
By analyzing the data, they managed to streamline their operations, reducing energy consumption by 15% and cutting waste by 10%.
The system also ensured compliance with food safety regulations by maintaining stringent control over critical parameters.
Conclusion
The impact of advanced equipment data collection tools on Japanese manufacturing is profound.
These tools foster a culture of continuous improvement, driving efficiency, reducing costs, and enhancing product quality.
However, the implementation comes with challenges that require careful consideration of costs, cybersecurity, and workforce training.
Strategic negotiation with suppliers, understanding market conditions, and adhering to best practices can further optimize the benefits.
Embracing this digital transformation keeps Japanese manufacturing ahead of the curve, maintaining its legacy of excellence and innovation in a competitive global market.
資料ダウンロード
QCD調達購買管理クラウド「newji」は、調達購買部門で必要なQCD管理全てを備えた、現場特化型兼クラウド型の今世紀最高の購買管理システムとなります。
ユーザー登録
調達購買業務の効率化だけでなく、システムを導入することで、コスト削減や製品・資材のステータス可視化のほか、属人化していた購買情報の共有化による内部不正防止や統制にも役立ちます。
NEWJI DX
製造業に特化したデジタルトランスフォーメーション(DX)の実現を目指す請負開発型のコンサルティングサービスです。AI、iPaaS、および先端の技術を駆使して、製造プロセスの効率化、業務効率化、チームワーク強化、コスト削減、品質向上を実現します。このサービスは、製造業の課題を深く理解し、それに対する最適なデジタルソリューションを提供することで、企業が持続的な成長とイノベーションを達成できるようサポートします。
オンライン講座
製造業、主に購買・調達部門にお勤めの方々に向けた情報を配信しております。
新任の方やベテランの方、管理職を対象とした幅広いコンテンツをご用意しております。
お問い合わせ
コストダウンが利益に直結する術だと理解していても、なかなか前に進めることができない状況。そんな時は、newjiのコストダウン自動化機能で大きく利益貢献しよう!
(Β版非公開)