- お役立ち記事
- Revolutionizing Manufacturing: The Rise of Mold Parts OEM in Japan’s Industrial Landscape
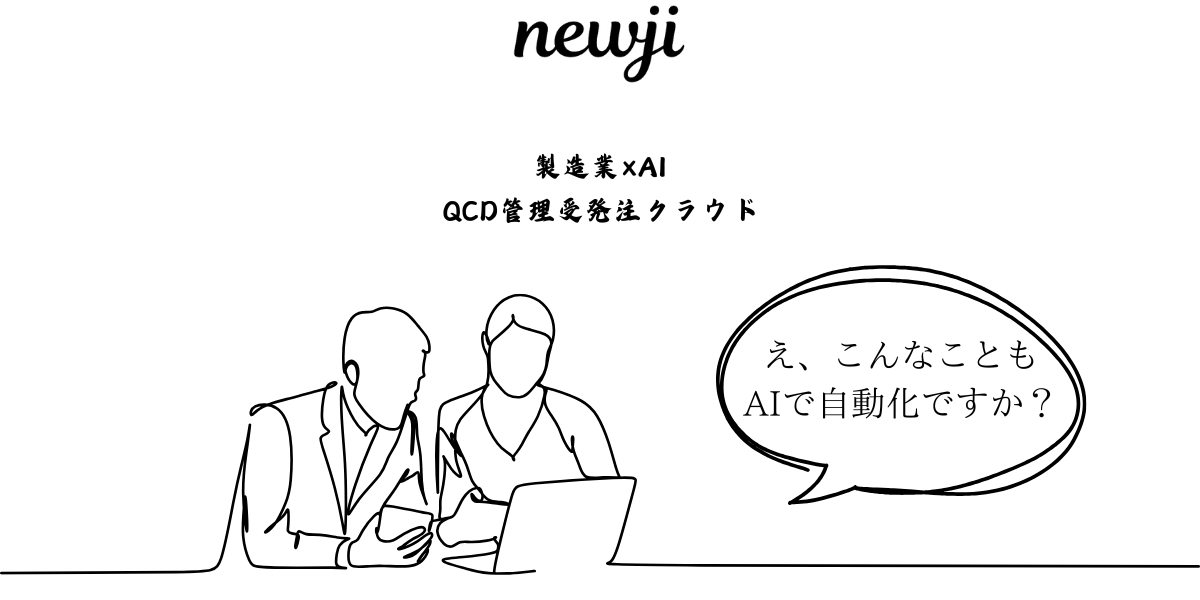
Revolutionizing Manufacturing: The Rise of Mold Parts OEM in Japan’s Industrial Landscape
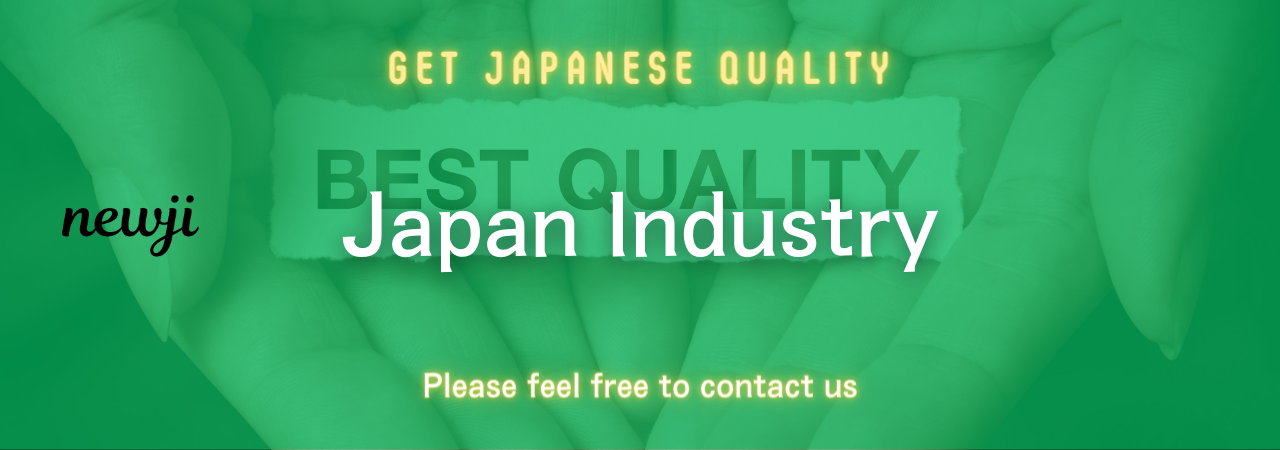
目次
Introduction
In the dynamic landscape of global manufacturing, Japan has emerged as a pivotal player, particularly in the realm of Mold Parts Original Equipment Manufacturing (OEM). This rise is not merely a testament to Japan’s enduring industrial prowess but also reflects strategic advancements in procurement, quality control, and supplier relationships. Understanding the factors driving the growth of Mold Parts OEM in Japan provides valuable insights for manufacturing companies worldwide seeking to enhance their production capabilities and maintain competitive edge.
The Evolution of Mold Parts OEM in Japan
Japan’s manufacturing sector has long been synonymous with precision, efficiency, and innovation. The evolution of Mold Parts OEM within this sector is rooted in several key developments that have collectively revolutionized the way mold parts are produced and integrated into broader manufacturing processes.
Historical Context
Historically, Japan’s commitment to quality and continuous improvement, encapsulated in the principles of Kaizen, has fostered an environment where OEM relationships can thrive. This dedication has enabled Japanese manufacturers to consistently deliver high-quality mold parts that meet the stringent demands of various industries, including automotive, electronics, and consumer goods.
Technological Advancements
Advancements in manufacturing technologies, such as precision machining, automation, and computer-aided design (CAD), have significantly enhanced the capabilities of Japanese OEMs. These technologies allow for the production of highly complex and durable mold parts, reducing lead times and minimizing errors during the manufacturing process.
Advantages of Partnering with Japanese Mold Parts OEMs
Partnering with Japanese OEMs offers a multitude of advantages that can significantly benefit manufacturing companies.
Unmatched Quality Standards
Japanese OEMs are renowned for their stringent quality control measures. The implementation of Total Quality Management (TQM) practices ensures that every mold part produced meets high standards of precision and reliability. This commitment to quality reduces the likelihood of defects and enhances the overall efficiency of the manufacturing process.
Innovative Design and Engineering
Japanese OEMs invest heavily in research and development, fostering innovation in mold design and engineering. This focus on innovation allows for the creation of mold parts that are not only functional but also optimized for performance and longevity, providing manufacturers with a competitive advantage in their respective markets.
Cost Efficiency
While Japanese OEMs are often perceived as premium suppliers, their focus on efficiency and waste reduction can lead to significant cost savings in the long run. Advanced manufacturing techniques and lean production methodologies minimize material waste and reduce production costs, offering value beyond the initial investment.
Strong Supplier Relationships
Japanese business culture emphasizes long-term relationships and trust. This cultural aspect translates into stable and reliable partnerships between manufacturers and OEMs. Consistent communication and collaboration foster mutual understanding and facilitate the seamless integration of OEM-produced mold parts into manufacturing workflows.
Challenges and Disadvantages
Despite the numerous benefits, partnering with Japanese Mold Parts OEMs also presents certain challenges that manufacturers must navigate.
High Initial Investment
The superior quality and advanced technologies employed by Japanese OEMs often come with higher upfront costs. For smaller companies or those with limited budgets, the initial investment required to engage with Japanese suppliers can be a significant barrier.
Cultural and Language Barriers
Differing business practices and language differences can pose challenges in communication and negotiation. Misunderstandings arising from cultural nuances may impact the efficiency of transactions and the overall partnership experience.
Longer Lead Times
While Japanese OEMs are efficient, the geographical distance and global supply chain complexities can result in longer lead times compared to local suppliers. Manufacturers must account for these factors in their production planning to avoid potential delays.
Supplier Negotiation Techniques
Effective negotiation with Japanese OEMs requires a strategic approach that respects cultural norms and leverages the strengths of both parties.
Building Trust and Rapport
Establishing a foundation of trust is crucial. This involves demonstrating commitment to long-term partnerships, showing respect for Japanese business etiquette, and engaging in open and honest communication. Building rapport fosters a collaborative environment conducive to successful negotiations.
Emphasizing Mutual Benefits
Highlighting the mutual benefits of the partnership can facilitate more favorable negotiation outcomes. Clearly articulating how the collaboration will enhance both parties’ business objectives encourages a cooperative rather than competitive negotiation stance.
Understanding Cultural Nuances
Awareness of Japanese business culture, such as the importance of hierarchy, consensus decision-making, and indirect communication styles, can enhance negotiation effectiveness. Adapting negotiation strategies to align with these cultural preferences can lead to more productive discussions and agreements.
Leveraging Expertise and Value
Demonstrating an understanding of the technical aspects of mold parts manufacturing and showcasing the value your company brings to the partnership can strengthen your negotiating position. Expertise can be a persuasive factor in securing advantageous terms.
Market Conditions Impacting Mold Parts OEM in Japan
Various market conditions influence the dynamics of Mold Parts OEM in Japan, shaping the opportunities and challenges faced by manufacturers.
Global Supply Chain Disruptions
Events such as natural disasters, pandemics, and geopolitical tensions can disrupt global supply chains, affecting the availability and cost of mold parts. Japanese OEMs have implemented resilient supply chain strategies to mitigate these impacts, but manufacturers must remain adaptable to navigate these uncertainties.
Technological Innovations
The continuous pace of technological innovation in manufacturing necessitates that OEMs keep pace with emerging trends. Japanese companies that adopt new technologies can offer more advanced and efficient mold parts, providing a competitive edge but also requiring manufacturers to stay informed and integrate these advancements into their processes.
Environmental Regulations
Increasingly stringent environmental regulations globally influence manufacturing practices. Japanese OEMs are at the forefront of sustainable manufacturing, incorporating eco-friendly materials and processes. Aligning with these practices not only ensures compliance but also meets the growing consumer demand for sustainable products.
Best Practices for Engaging with Japanese Mold Parts OEMs
To maximize the benefits of partnering with Japanese OEMs, manufacturers should adopt best practices that promote successful and sustainable collaborations.
Comprehensive Due Diligence
Conducting thorough due diligence on potential OEM partners is essential. This includes evaluating their production capabilities, quality control processes, financial stability, and reputation in the industry. Comprehensive assessment ensures that the selected OEM aligns with your company’s quality and performance standards.
Clear Communication Channels
Establishing clear and effective communication channels helps prevent misunderstandings and ensures that both parties are aligned in their objectives and expectations. Utilizing various communication tools and maintaining regular updates fosters transparency and facilitates smooth operations.
Collaborative Planning and Forecasting
Engaging in collaborative planning and forecasting with OEM partners enables better alignment of production schedules and demand forecasts. This collaboration helps in optimizing inventory levels, reducing lead times, and enhancing overall supply chain efficiency.
Continuous Improvement Initiatives
Adopting continuous improvement initiatives, such as regular performance reviews and joint problem-solving sessions, fosters a culture of excellence and innovation. These initiatives enable both manufacturers and OEMs to identify and implement improvements, enhancing the quality and efficiency of mold parts production.
Investing in Relationship Building
Investing time and resources in building strong relationships with OEM partners pays dividends in the long run. Regular visits, joint training programs, and cultural exchange initiatives strengthen the partnership and ensure sustained collaboration.
Case Studies: Success Stories in Japanese Mold Parts OEM
Examining real-world examples of successful partnerships with Japanese Mold Parts OEMs provides valuable lessons and inspiration for manufacturers.
Automotive Industry Collaboration
A leading automotive manufacturer partnered with a Japanese OEM to develop high-precision mold parts for their new electric vehicle lineup. Through collaborative engineering and rigorous quality control, the partnership resulted in mold parts that significantly improved assembly efficiency and vehicle performance, contributing to the manufacturer’s market success.
Electronics Sector Partnership
A global electronics company engaged with a Japanese OEM to source intricate mold parts for consumer gadgets. The OEM’s expertise in micro-molding techniques enabled the production of complex components with exceptional accuracy, enhancing the final product’s quality and reliability, and strengthening the manufacturer’s brand reputation.
Future Trends in Mold Parts OEM in Japan
Looking ahead, several trends are poised to shape the future of Mold Parts OEM in Japan, offering new opportunities and challenges for manufacturers.
Integration of Artificial Intelligence and Machine Learning
The incorporation of artificial intelligence (AI) and machine learning (ML) in manufacturing processes is set to revolutionize mold parts production. These technologies enable predictive maintenance, optimize production schedules, and enhance quality inspections, leading to increased efficiency and reduced downtimes.
Adoption of Additive Manufacturing
Additive manufacturing, or 3D printing, is gaining traction in mold parts production. This technology allows for rapid prototyping and the production of complex geometries that are difficult to achieve with traditional methods. The adoption of additive manufacturing can lead to greater design flexibility and quicker turnaround times.
Focus on Sustainability
Sustainability continues to be a significant focus in manufacturing. Japanese OEMs are increasingly adopting green manufacturing practices, such as using recyclable materials and reducing energy consumption. Manufacturers partnering with these OEMs can enhance their own sustainability credentials and meet the growing demand for eco-friendly products.
Customization and Flexibility
The demand for customized products is rising, necessitating greater flexibility in mold parts production. Japanese OEMs are responding by offering more adaptable manufacturing solutions that can accommodate varying specifications and smaller production runs, enabling manufacturers to cater to niche markets and diverse customer needs.
Conclusion
The rise of Mold Parts OEM in Japan’s industrial landscape signifies a transformative shift in global manufacturing dynamics. By leveraging Japan’s expertise in quality, innovation, and efficient manufacturing practices, manufacturers worldwide can enhance their production capabilities and achieve greater competitive advantage. However, navigating the challenges of cultural differences, initial investment costs, and supply chain complexities requires strategic planning and a commitment to building strong, collaborative partnerships. As the industry continues to evolve with emerging technologies and sustainability initiatives, the role of Japanese Mold Parts OEMs will undoubtedly become even more integral to the success of global manufacturing enterprises.
資料ダウンロード
QCD調達購買管理クラウド「newji」は、調達購買部門で必要なQCD管理全てを備えた、現場特化型兼クラウド型の今世紀最高の購買管理システムとなります。
ユーザー登録
調達購買業務の効率化だけでなく、システムを導入することで、コスト削減や製品・資材のステータス可視化のほか、属人化していた購買情報の共有化による内部不正防止や統制にも役立ちます。
NEWJI DX
製造業に特化したデジタルトランスフォーメーション(DX)の実現を目指す請負開発型のコンサルティングサービスです。AI、iPaaS、および先端の技術を駆使して、製造プロセスの効率化、業務効率化、チームワーク強化、コスト削減、品質向上を実現します。このサービスは、製造業の課題を深く理解し、それに対する最適なデジタルソリューションを提供することで、企業が持続的な成長とイノベーションを達成できるようサポートします。
オンライン講座
製造業、主に購買・調達部門にお勤めの方々に向けた情報を配信しております。
新任の方やベテランの方、管理職を対象とした幅広いコンテンツをご用意しております。
お問い合わせ
コストダウンが利益に直結する術だと理解していても、なかなか前に進めることができない状況。そんな時は、newjiのコストダウン自動化機能で大きく利益貢献しよう!
(Β版非公開)