- お役立ち記事
- Roles and Strategies of Quality Assurance Departments to Achieve Zero Defects in Manufacturing
Roles and Strategies of Quality Assurance Departments to Achieve Zero Defects in Manufacturing
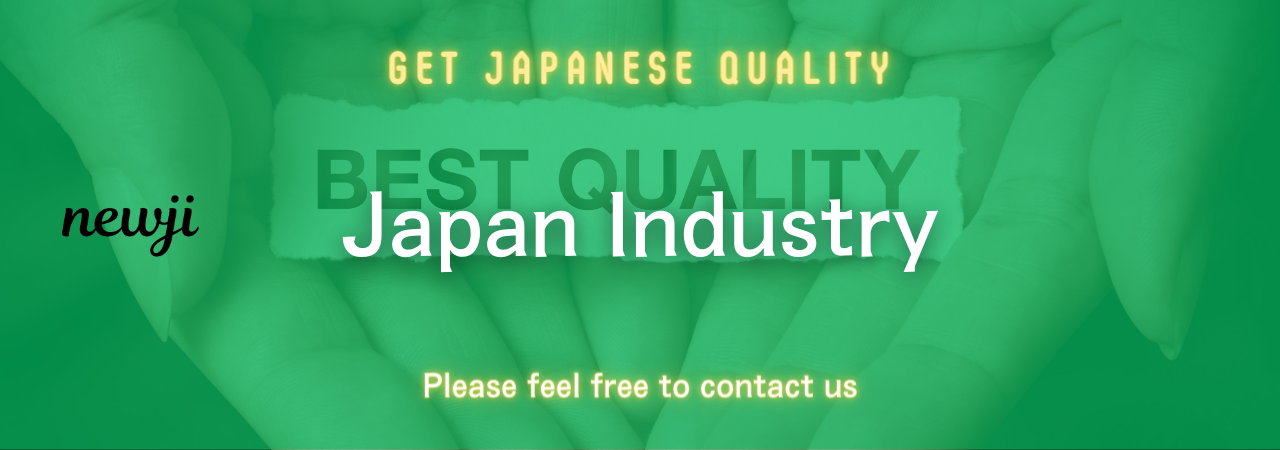
Quality Assurance (QA) departments play a crucial role in manufacturing companies, striving to achieve the ultimate goal of zero defects in their products. To accomplish this, QA teams employ various strategies and techniques to ensure that every product leaving the factory meets the highest standards of quality and performance.
One of the primary roles of QA departments is to establish and maintain a robust quality management system (QMS). A well-designed QMS provides a framework for defining quality objectives, documenting processes, and implementing continuous improvement initiatives. By adhering to international standards such as ISO 9001, QA teams can ensure that their QMS is effective and aligned with industry best practices.
Another key strategy employed by QA departments is the implementation of rigorous inspection and testing procedures. This involves examining products at various stages of the manufacturing process to identify and rectify any defects or non-conformities. QA teams may use a variety of tools and techniques, such as visual inspections, functional testing, and statistical process control (SPC), to monitor product quality and detect issues early in the production cycle.
To achieve zero defects, QA departments also focus on preventing quality issues from occurring in the first place. This is accomplished through the use of quality planning and risk management techniques. By analyzing potential failure modes and their effects (FMEA), QA teams can identify and mitigate risks before they result in defects. Additionally, by collaborating with other departments, such as product design and engineering, QA can ensure that quality considerations are integrated into the product development process from the outset.
Training and employee engagement are also critical components of a successful zero-defect strategy. QA departments work closely with production staff to provide training on quality standards, inspection procedures, and problem-solving techniques. By fostering a culture of quality and empowering employees to take ownership of their work, QA teams can reduce the likelihood of human error and promote continuous improvement.
In addition to these internal strategies, QA departments also play a vital role in managing supplier quality. By establishing clear quality requirements and conducting regular audits of suppliers, QA teams can ensure that incoming materials and components meet the necessary standards. This helps to prevent defects from being introduced into the manufacturing process due to subpar raw materials or parts.
Technology also plays an increasingly important role in helping QA departments achieve zero defects. Automated inspection systems, such as machine vision and 3D scanning, can provide more accurate and consistent results than manual inspections. Additionally, the use of real-time data collection and analysis tools can help QA teams identify trends and potential issues more quickly, allowing for more proactive quality control.
Finally, QA departments must be committed to continuous improvement and learning from any defects that do occur. By conducting thorough root cause analyses and implementing corrective and preventive actions (CAPA), QA teams can identify the underlying causes of quality issues and take steps to prevent their recurrence. This process of ongoing improvement is essential to achieving and maintaining zero defects over time.
In conclusion, the role of Quality Assurance departments in achieving zero defects in manufacturing is multifaceted and critical to the success of any organization. By establishing robust quality management systems, implementing rigorous inspection and testing procedures, focusing on prevention and risk management, engaging employees, managing supplier quality, leveraging technology, and committing to continuous improvement, QA teams can help their companies consistently deliver high-quality products that meet and exceed customer expectations.
資料ダウンロード
QCD調達購買管理クラウド「newji」は、調達購買部門で必要なQCD管理全てを備えた、現場特化型兼クラウド型の今世紀最高の購買管理システムとなります。
ユーザー登録
調達購買業務の効率化だけでなく、システムを導入することで、コスト削減や製品・資材のステータス可視化のほか、属人化していた購買情報の共有化による内部不正防止や統制にも役立ちます。
NEWJI DX
製造業に特化したデジタルトランスフォーメーション(DX)の実現を目指す請負開発型のコンサルティングサービスです。AI、iPaaS、および先端の技術を駆使して、製造プロセスの効率化、業務効率化、チームワーク強化、コスト削減、品質向上を実現します。このサービスは、製造業の課題を深く理解し、それに対する最適なデジタルソリューションを提供することで、企業が持続的な成長とイノベーションを達成できるようサポートします。
オンライン講座
製造業、主に購買・調達部門にお勤めの方々に向けた情報を配信しております。
新任の方やベテランの方、管理職を対象とした幅広いコンテンツをご用意しております。
お問い合わせ
コストダウンが利益に直結する術だと理解していても、なかなか前に進めることができない状況。そんな時は、newjiのコストダウン自動化機能で大きく利益貢献しよう!
(Β版非公開)