- お役立ち記事
- Sampling Techniques and Applications in Manufacturing
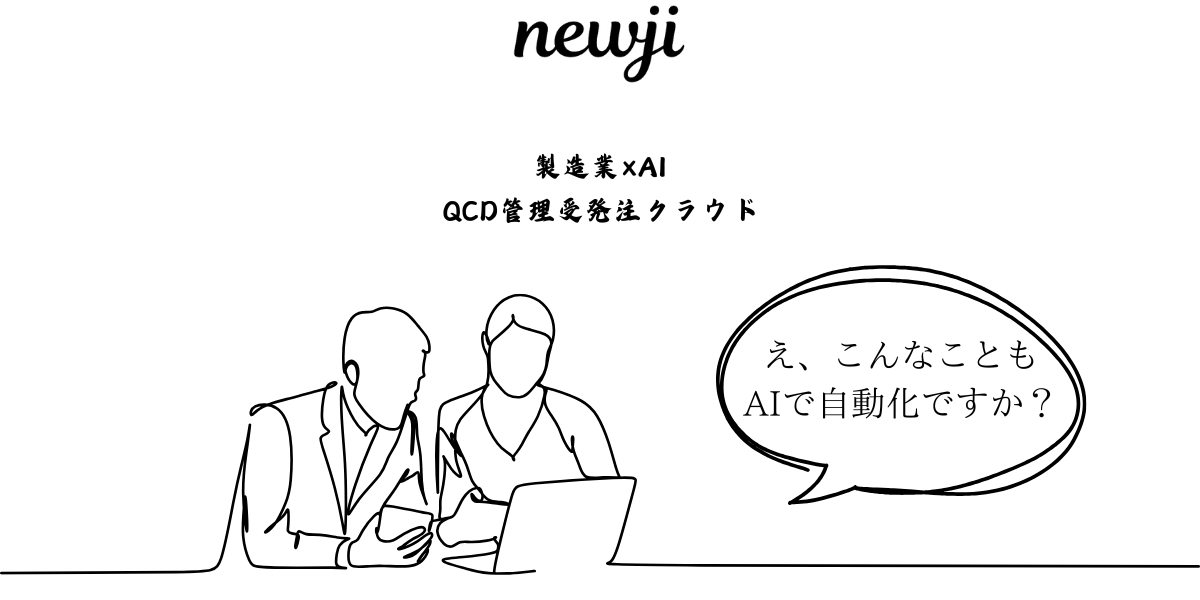
Sampling Techniques and Applications in Manufacturing
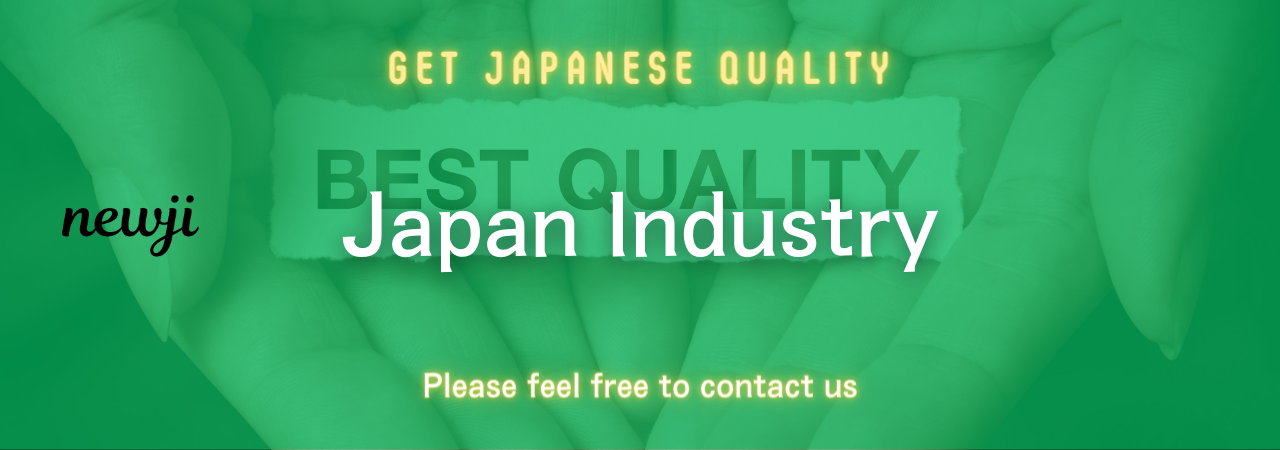
In the world of manufacturing, ensuring the quality of produced goods is crucial.
One effective way to maintain and improve quality is through the use of sampling techniques.
Sampling helps manufacturers understand the quality of their products without examining every single item.
Instead, they inspect a small, manageable portion of the total output.
This method saves time and resources while still providing valuable information about the overall production process.
目次
What is Sampling?
Sampling is the process of selecting a subset of items from a larger group in order to draw conclusions about the entire group.
Imagine you have a big jar of candies.
Instead of counting and examining each piece, you take a handful and check them out.
If the candies in your handful are good, you can assume that the rest are likely okay, too.
In manufacturing, this approach saves time and effort.
Types of Sampling Techniques
There are various sampling techniques used in manufacturing.
Each has its benefits and is chosen based on the specific needs and conditions of the production process.
Random Sampling
Random sampling is like picking names out of a hat.
You randomly select items from the production line without any specific pattern.
This method is unbiased because every item has an equal chance of being picked.
It is often used when manufacturers want to get a fair representation of the entire production lot.
Systematic Sampling
In systematic sampling, you pick items using a fixed interval.
For example, every tenth item on the conveyor belt might be selected.
This method is easier to implement than random sampling and ensures that items are chosen at regular intervals.
However, the chosen interval must not coincide with any hidden patterns in the production process, as this could lead to biased results.
Stratified Sampling
Stratified sampling involves dividing the produced items into different groups or “strata” based on certain characteristics.
For example, a car manufacturer might separate cars by model type before sampling.
The idea is to ensure that specific subgroups are adequately represented.
This method is particularly useful when the production process involves diverse products with varying characteristics.
Cluster Sampling
In cluster sampling, the production batch is divided into several clusters, and a few clusters are selected randomly for inspection.
Instead of sampling individual items across the entire batch, whole clusters are examined.
This technique is practical when dealing with large-scale production, as it reduces the number of items that need to be checked.
Applications of Sampling in Manufacturing
Sampling techniques are applied at various stages of the manufacturing process to ensure quality and efficiency.
Incoming Material Inspection
Before starting the production process, manufacturers receive raw materials and components.
Sampling these materials ensures that only high-quality inputs go into the production line.
For instance, a smartphone manufacturer might sample a batch of processors to check for potential defects before assembly.
In-Process Quality Control
Sampling is vital during the production process to monitor and maintain quality control.
By inspecting items at various stages, manufacturers can catch and address issues before they become significant problems.
This proactive approach minimizes waste and rework.
For example, in a textile factory, fabric might be sampled at different stages of dying and weaving to ensure consistency and colorfastness.
Final Product Inspection
Before products are shipped to customers, manufacturers perform final inspections to ensure quality.
Sampling helps verify that items meet established standards and specifications.
In the automotive industry, for instance, a few cars from each batch might be thoroughly inspected for safety and performance features.
Compliance with Regulatory Standards
Many industries are subject to strict regulations regarding product safety and quality.
Regulatory bodies often require manufacturers to use sampling techniques to ensure compliance.
For example, the food industry must regularly sample products to test for contaminants and ensure they meet health standards.
Benefits of Using Sampling Techniques
Using sampling techniques in manufacturing offers several substantial benefits.
Cost Efficiency
Sampling reduces the need to inspect every single item, which saves both time and labor costs.
Manufacturers can allocate resources more effectively and focus on other critical aspects of production.
Improved Quality Control
By identifying defects early, manufacturers can take corrective actions promptly.
This continuous monitoring leads to higher overall quality and a reduction in defective products reaching customers.
Data-Driven Decisions
The data collected from sampling provide valuable insights into the production process.
Manufacturers can use this information to make informed decisions, optimize processes, and improve product designs.
Challenges of Sampling in Manufacturing
While sampling techniques offer numerous advantages, they also come with some challenges.
Sampling Bias
If the sampling method is not appropriately chosen, it can introduce bias, leading to inaccurate conclusions.
For example, if a systematic sampling interval coincides with a hidden flaw pattern, the sample might not represent the entire batch accurately.
Sample Size Determination
Determining the correct sample size is critical yet challenging.
A smaller sample might not provide reliable data, while a larger sample increases inspection costs and time.
Manufacturers must find a balance to achieve accurate results without excessive effort.
Conclusion
Sampling techniques are essential tools in the realm of manufacturing.
They help ensure product quality, efficiency, and compliance with regulations.
By understanding and correctly implementing various sampling methods, manufacturers can save time, reduce costs, and consistently deliver high-quality products to their customers.
Despite some challenges, the benefits of sampling in the manufacturing sector make it an indispensable practice.
資料ダウンロード
QCD調達購買管理クラウド「newji」は、調達購買部門で必要なQCD管理全てを備えた、現場特化型兼クラウド型の今世紀最高の購買管理システムとなります。
ユーザー登録
調達購買業務の効率化だけでなく、システムを導入することで、コスト削減や製品・資材のステータス可視化のほか、属人化していた購買情報の共有化による内部不正防止や統制にも役立ちます。
NEWJI DX
製造業に特化したデジタルトランスフォーメーション(DX)の実現を目指す請負開発型のコンサルティングサービスです。AI、iPaaS、および先端の技術を駆使して、製造プロセスの効率化、業務効率化、チームワーク強化、コスト削減、品質向上を実現します。このサービスは、製造業の課題を深く理解し、それに対する最適なデジタルソリューションを提供することで、企業が持続的な成長とイノベーションを達成できるようサポートします。
オンライン講座
製造業、主に購買・調達部門にお勤めの方々に向けた情報を配信しております。
新任の方やベテランの方、管理職を対象とした幅広いコンテンツをご用意しております。
お問い合わせ
コストダウンが利益に直結する術だと理解していても、なかなか前に進めることができない状況。そんな時は、newjiのコストダウン自動化機能で大きく利益貢献しよう!
(Β版非公開)