- お役立ち記事
- Selecting the Right Technology for High-Strength Parts in Forging
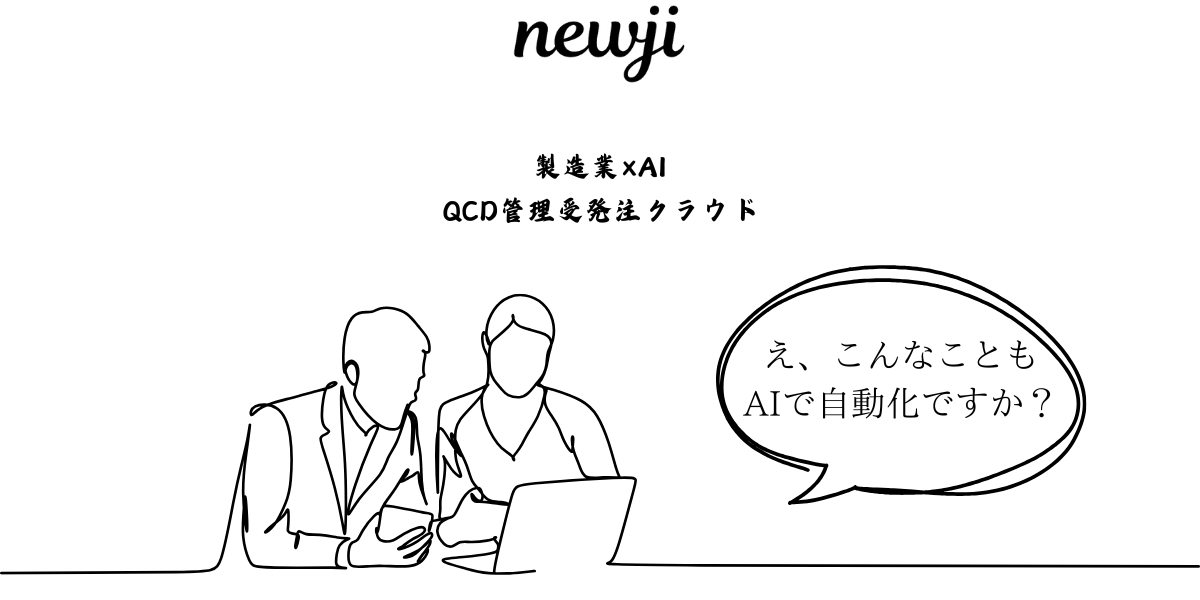
Selecting the Right Technology for High-Strength Parts in Forging
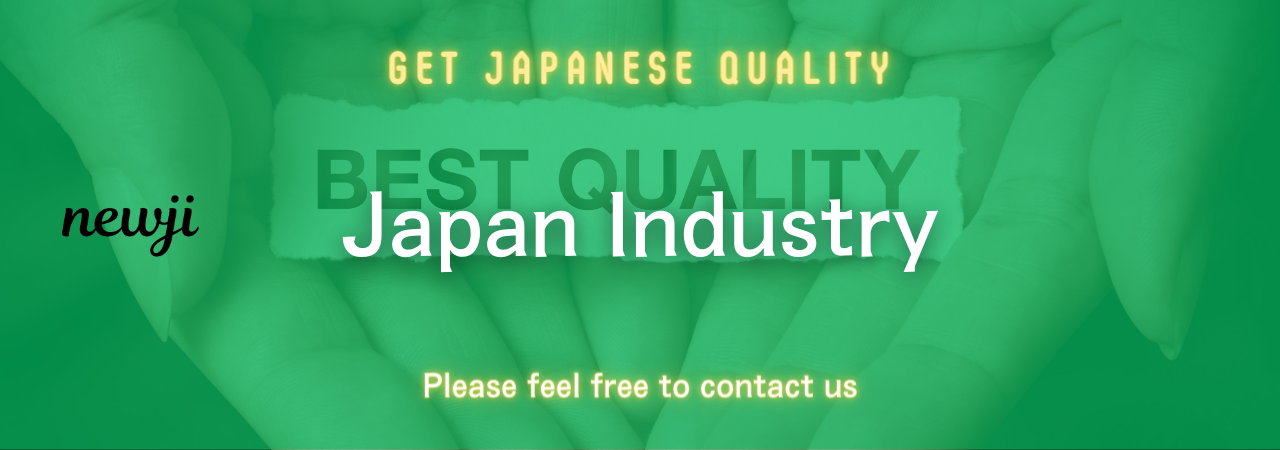
Choosing the right technology for high-strength parts in forging can be a complex decision.
With numerous options available in the market, it is vital to understand what specifically works best for your needs.
The following guide will help clarify what you need to know about selecting the right technology for high-strength forging parts.
目次
Understanding Forging and Its Benefits
Forging is a manufacturing process that involves shaping metal using localized compressive forces.
It can produce components that are exceptionally strong and reliable.
This is particularly important when dealing with high-strength parts.
Forging improves the material’s internal structure, making it more homogeneous.
This results in better performance and durability.
High-strength forged parts are used in critical applications, such as aerospace, automotive, and heavy machinery, where failure is not an option.
The Importance of Material Selection
Before choosing a technology, you must select the appropriate material for your high-strength parts.
Common materials include steel, titanium, and aluminum alloys.
The choice of material depends on the specific requirements of your application.
Steel
Steel is frequently used due to its excellent mechanical properties and cost-effectiveness.
It is suitable for high-stress applications.
Titanium
Titanium offers a higher strength-to-weight ratio and excellent corrosion resistance.
It’s ideal for aerospace applications where weight reduction is crucial.
Aluminum Alloys
Aluminum alloys are lightweight and possess good corrosion resistance, making them suitable for automotive applications.
Types of Forging Technologies
There are several types of forging technologies to choose from.
Each has its advantages and limitations.
Open Die Forging
Open die forging involves deforming metal between multiple dies that do not completely enclose the material.
This method is particularly useful for large, simple shapes and custom components.
It offers better grain flow and enhanced mechanical properties.
Closed Die Forging
Closed die forging, also known as impression-die forging, uses customized dies that enclose the metal.
It is perfect for producing more complex shapes with tighter tolerances.
This method is highly efficient and cost-effective for large production runs.
Isothermal Forging
Isothermal forging involves maintaining the temperature of both the dies and the workpiece to ensure uniformity.
This technology is beneficial for creating high-precision parts with intricate details.
It is commonly used in aerospace and high-performance applications.
Cold Forging
Cold forging is performed at or near room temperature.
It is suitable for small to medium-sized components and offers excellent surface finish and dimensional accuracy.
However, it generally requires higher force compared to hot forging.
Factors to Consider When Choosing Forging Technology
Several factors should be considered to ensure you select the best forging technology for high-strength parts.
Mechanical Properties
Understanding the required mechanical properties of the final product is crucial.
Different forging technologies produce varying mechanical strengths and grain structures.
Carefully evaluate the strength, toughness, and fatigue resistance needed for your parts.
Scale of Production
The scale of production also influences the choice of forging technology.
Automated and efficient closed die forging works well for large-scale production.
Conversely, open die forging is more suitable for small batches or custom orders.
Complexity of Parts
If you require highly complex parts with intricate details, closed die and isothermal forging are preferable.
These methods provide greater control over the final form and tolerances of the part.
Cost
Cost considerations are always important in manufacturing.
Cold forging generally offers lower operational costs due to less energy consumption.
However, the initial investment in tooling and machinery might be higher.
Make sure to balance initial costs with long-term benefits.
Advancements in Forging Technology
Recent advancements in forging technology have improved efficiency, consistency, and capabilities.
Precision Forging
Precision forging incorporates advanced techniques and machinery to achieve higher accuracy and minimize material wastage.
It is suitable for high-performance, high-strength parts.
Automation and Robotics
Modern forging facilities increasingly utilize automation and robotics to enhance productivity and reduce labor costs.
Automated systems ensure consistent quality and precision, especially in large-volume production.
Simulation and Modeling
Advanced computational tools allow engineers to simulate and model the forging process to optimize parameters.
This leads to reduced trial-and-error, shorter development cycles, and better final products.
Quality Control and Testing
Quality control and testing are integral to the forging process, especially for high-strength parts.
Non-Destructive Testing (NDT)
NDT methods such as ultrasonic testing, radiography, and magnetic particle inspection help detect imperfections without damaging the part.
These tests ensure the integrity and reliability of forged parts.
Material Testing
Conducting material tests such as tensile, hardness, and impact tests confirms the mechanical properties of the forged parts.
This ensures they meet the required standards and specifications.
Dimensional Inspection
Dimensional inspection ensures that the forged parts adhere to the specified tolerances and dimensions.
This is particularly important for parts that need to fit accurately with other components.
Choosing the right technology for high-strength parts in forging involves multiple considerations.
By understanding the basics of forging, material selection, and different forging technologies, you can make informed decisions.
Paying attention to advancements and quality control measures will further ensure you achieve the desired performance and reliability for your high-strength forged parts.
資料ダウンロード
QCD調達購買管理クラウド「newji」は、調達購買部門で必要なQCD管理全てを備えた、現場特化型兼クラウド型の今世紀最高の購買管理システムとなります。
ユーザー登録
調達購買業務の効率化だけでなく、システムを導入することで、コスト削減や製品・資材のステータス可視化のほか、属人化していた購買情報の共有化による内部不正防止や統制にも役立ちます。
NEWJI DX
製造業に特化したデジタルトランスフォーメーション(DX)の実現を目指す請負開発型のコンサルティングサービスです。AI、iPaaS、および先端の技術を駆使して、製造プロセスの効率化、業務効率化、チームワーク強化、コスト削減、品質向上を実現します。このサービスは、製造業の課題を深く理解し、それに対する最適なデジタルソリューションを提供することで、企業が持続的な成長とイノベーションを達成できるようサポートします。
オンライン講座
製造業、主に購買・調達部門にお勤めの方々に向けた情報を配信しております。
新任の方やベテランの方、管理職を対象とした幅広いコンテンツをご用意しております。
お問い合わせ
コストダウンが利益に直結する術だと理解していても、なかなか前に進めることができない状況。そんな時は、newjiのコストダウン自動化機能で大きく利益貢献しよう!
(Β版非公開)