- お役立ち記事
- Strategic efforts by the purchasing department to reduce inventory in the manufacturing industry
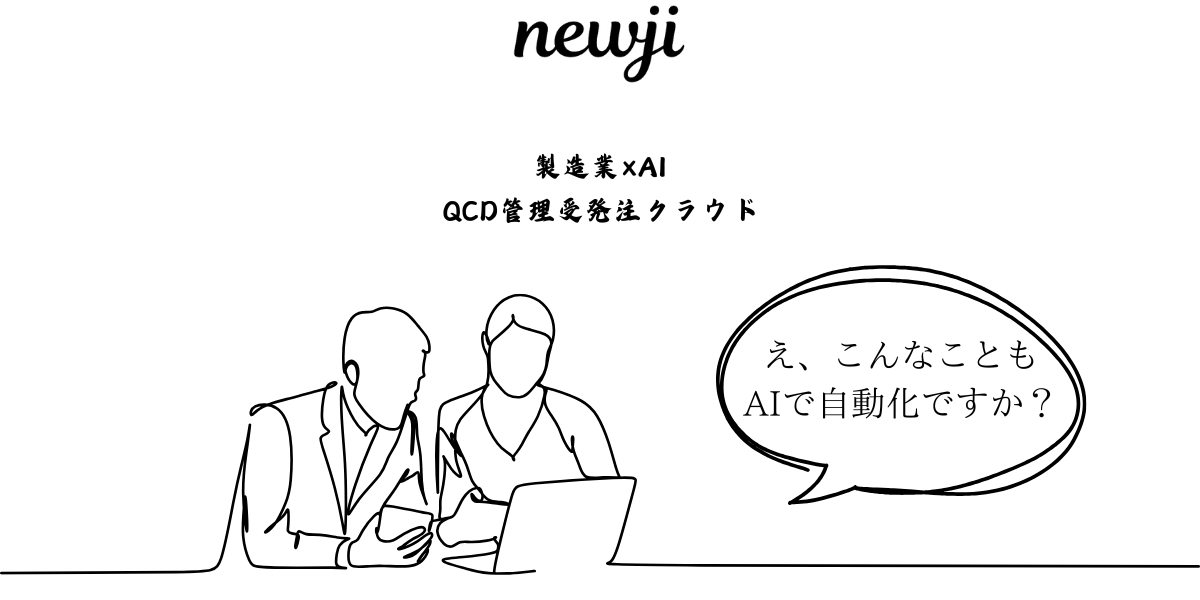
Strategic efforts by the purchasing department to reduce inventory in the manufacturing industry
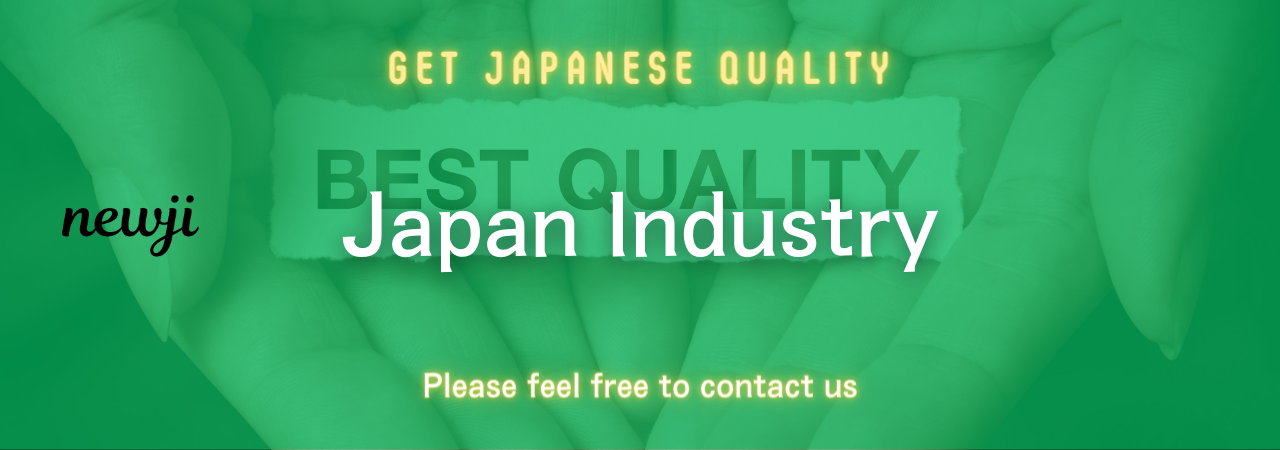
目次
Understanding Inventory Management in the Manufacturing Industry
Inventory management plays a crucial role in the manufacturing industry.
Efficient inventory management ensures that the right amount of materials is available for production without excessive stock that ties up capital.
Having too much inventory can lead to increased storage costs, risk of obsolescence, and wasted resources.
On the other hand, inadequate inventory levels may lead to production delays and potentially lost sales.
Thus, it is essential for the purchasing department to implement strategic efforts in managing inventory levels effectively.
The Role of the Purchasing Department
The purchasing department is responsible for sourcing raw materials and components required for manufacturing products.
Their role extends beyond simply buying goods; it involves negotiating with suppliers, assessing quality, and selecting the best fit for the company’s needs.
With their unique position in the supply chain, the purchasing department can significantly influence inventory levels.
Their decisions impact how much inventory is available, how long it sits in storage, and the costs associated with maintaining it.
Building Strong Supplier Relationships
One of the strategic efforts that the purchasing department can undertake is building and maintaining strong relationships with suppliers.
Establishing trust and open channels of communication with suppliers allows for better negotiation terms, such as flexible delivery schedules and bulk discounts.
Strong supplier relationships can help in improving delivery reliability and reducing lead times, which plays a crucial role in maintaining optimal inventory levels.
Adopting Just-in-Time Inventory Systems
Just-in-Time (JIT) inventory is a strategy aimed at reducing waste by receiving goods only as needed in the production process.
This approach minimizes the amount of inventory held at any given time and reduces the costs associated with storage.
For the purchasing department, implementing JIT involves precise planning and coordination with suppliers to ensure materials are delivered at the right time and quantity.
Utilizing Technology for Better Inventory Management
Technology has transformed inventory management processes through automation and data analytics.
The purchasing department can use sophisticated enterprise resource planning (ERP) systems to track inventory levels in real-time, forecast future demands, and optimize order quantities.
Analytics tools help in understanding usage patterns and seasonal variations, allowing for more accurate predictions and timely responses to demand fluctuations.
Implementing Inventory Control Techniques
Inventory control techniques such as ABC analysis, Economic Order Quantity (EOQ), and safety stock calculations assist the purchasing department in maintaining inventory balance.
ABC analysis helps prioritize inventory into categories based on their importance, with ‘A’ items being the most valuable.
EOQ helps determine the ideal order quantity that minimizes total costs, considering both ordering and holding costs.
Safety stock acts as a buffer against unexpected demand spikes, ensuring production continuity.
Improving Demand Forecasting
Accurate demand forecasting is essential for reducing excess inventory.
The purchasing department can collaborate with sales and marketing to gain insights into market trends, consumer preferences, and upcoming promotions.
Using advanced forecasting models and historical data, purchasing managers can more accurately predict demand, making informed decisions regarding inventory purchases.
Lean Manufacturing Practices
The adoption of lean manufacturing principles can significantly benefit inventory management.
Lean manufacturing focuses on eliminating waste, improving processes, and enhancing product flow.
The purchasing department works closely with production teams to identify areas where excess inventory can be reduced without affecting operations.
Streamlining processes and continuous improvement initiatives lead to more efficient inventory management.
Inventory Audits and Continuous Improvement
Regular inventory audits allow the purchasing department to physically verify stock levels and identify discrepancies between records and actual inventory.
Audits help uncover issues such as theft, damage, or miscounts, prompting corrective actions.
The purchasing team should also embrace a culture of continuous improvement, regularly analyzing processes, identifying inefficiencies, and implementing changes to optimize inventory turnover.
Environmental and Cost Considerations
Reducing inventory in the manufacturing industry aligns with sustainability efforts, as lower stock levels mean less waste.
The purchasing department can explore eco-friendly materials and sourcing strategies that minimize environmental impact.
By continually reviewing inventory levels, they can also reduce associated costs, leading to higher profitability for the company.
Conclusion
Strategic efforts by the purchasing department are essential in effectively managing inventory levels in the manufacturing industry.
By building strong supplier relationships, adopting technology, implementing control techniques, and focusing on lean manufacturing, the purchasing department can optimize inventory turnover.
This not only reduces costs and frees up capital but also ensures smooth production processes and customer satisfaction.
Through meticulous planning and continuous improvement, inventory management becomes a dynamic process that significantly contributes to a company’s success.
資料ダウンロード
QCD調達購買管理クラウド「newji」は、調達購買部門で必要なQCD管理全てを備えた、現場特化型兼クラウド型の今世紀最高の購買管理システムとなります。
ユーザー登録
調達購買業務の効率化だけでなく、システムを導入することで、コスト削減や製品・資材のステータス可視化のほか、属人化していた購買情報の共有化による内部不正防止や統制にも役立ちます。
NEWJI DX
製造業に特化したデジタルトランスフォーメーション(DX)の実現を目指す請負開発型のコンサルティングサービスです。AI、iPaaS、および先端の技術を駆使して、製造プロセスの効率化、業務効率化、チームワーク強化、コスト削減、品質向上を実現します。このサービスは、製造業の課題を深く理解し、それに対する最適なデジタルソリューションを提供することで、企業が持続的な成長とイノベーションを達成できるようサポートします。
オンライン講座
製造業、主に購買・調達部門にお勤めの方々に向けた情報を配信しております。
新任の方やベテランの方、管理職を対象とした幅広いコンテンツをご用意しております。
お問い合わせ
コストダウンが利益に直結する術だと理解していても、なかなか前に進めることができない状況。そんな時は、newjiのコストダウン自動化機能で大きく利益貢献しよう!
(Β版非公開)