- お役立ち記事
- Success stories on quality control and inventory cost reduction for mid-level purchasing employees
Success stories on quality control and inventory cost reduction for mid-level purchasing employees
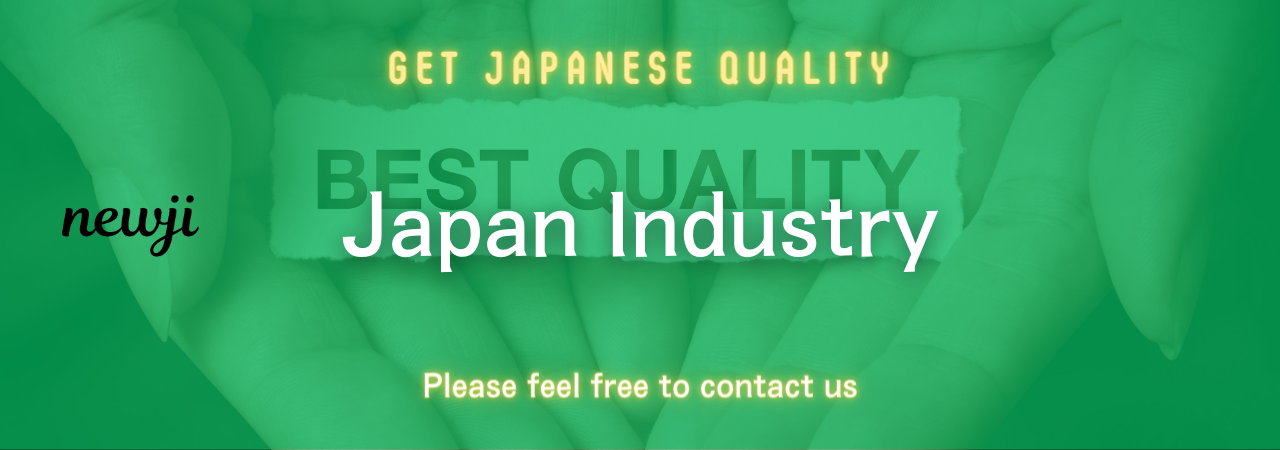
目次
Introduction to Quality Control and Inventory Cost Reduction
Mid-level purchasing employees play a crucial role in ensuring that their organizations maintain high-quality standards while effectively managing inventory costs.
The process of quality control and inventory cost reduction involves a complex set of strategies and practices designed to optimize efficiency and profitability.
By implementing effective quality control measures and reducing inventory costs, businesses can achieve significant long-term benefits.
Understanding how to balance these elements is essential for mid-level purchasing employees as they work towards the organization’s goals.
The Importance of Quality Control in Purchasing
Quality control is a fundamental aspect of the purchasing process.
Ensuring that the goods and materials procured are of high quality can prevent potential defects, reduce waste, and save costs in the long run.
Quality control starts with selecting the right suppliers who adhere to rigorous industry standards.
Employing a robust system for evaluating supplier performance is crucial.
Mid-level purchasing employees should establish clear criteria for assessing suppliers’ capabilities, consistency, and reliability.
Regular audits and performance reviews are effective methods to maintain high quality standards.
Additionally, implementing quality control measures within the organization, such as setting up inspection checkpoints and utilizing technology like automated systems, can help detect and address issues early.
This proactive approach minimizes downstream effects and enhances overall efficiency.
Strategies for Reducing Inventory Costs
Reducing inventory costs is another significant area where mid-level purchasing employees can make a profound impact.
Efficient inventory management involves striking the right balance between maintaining sufficient stock levels to meet demand without overstocking, which can lead to increased holding costs.
One effective strategy is applying Just-In-Time (JIT) inventory practices.
This approach involves receiving goods only as they are needed in the production process, thereby reducing inventory carrying costs.
JIT requires accurate demand forecasting and strong relationships with reliable suppliers to be successful.
Another method is to improve inventory turn rates.
Analyzing inventory turnover ratios can provide insight into how efficiently stock is being used and identify opportunities to optimize turnover.
Reducing slow-moving inventory by identifying and phasing out obsolete or excess stock can free up valuable resources.
Implementing technology-driven solutions, such as inventory management software, can streamline the process.
These tools provide real-time data on inventory levels, helping employees make informed purchasing decisions.
Success Stories in Quality Control and Inventory Cost Reduction
To illustrate the effectiveness of quality control and inventory cost reduction, let’s explore some success stories from mid-level purchasing employees who have excelled in these areas.
Case Study 1: Implementing a Supplier Quality Improvement Program
A mid-sized manufacturing firm recognized that their defect rates were too high, impacting both costs and customer satisfaction.
A mid-level purchasing employee took the initiative to establish a supplier quality improvement program.
By collaborating closely with their suppliers and providing them with feedback, they were able to reduce defect rates significantly.
Through regular supplier workshops and establishing clear quality expectations, the firm achieved a 30% reduction in defects and saved on rework and waste costs.
This success not only improved the company’s bottom line but also enhanced its reputation for delivering high-quality products.
Case Study 2: Leveraging Technology for Inventory Management
Another inspiring success story involves a retail company that faced challenges with overstocked inventory and high holding costs.
A savvy mid-level purchasing employee introduced an advanced inventory management system that provided real-time data and insights.
This technology allowed the company to refine their ordering processes, ensuring that inventory levels met actual demand.
As a result, the company experienced a 25% reduction in inventory holding costs and improved overall cash flow.
This case highlights the importance of integrating modern technology to facilitate data-driven decisions in inventory management.
Case Study 3: Effective Demand Forecasting and JIT Implementation
A food and beverage company was struggling with perishable inventory waste due to inaccurate demand forecasts.
A dedicated purchasing employee implemented a robust demand forecasting model combined with a Just-In-Time inventory strategy.
By leveraging historical sales data and predictive analytics, the company was able to better anticipate demand and optimize its inventory levels.
This led to a reduction in waste by 40% and a more efficient supply chain.
This success story underscores the value of precise demand forecasting and strategic inventory practices in reducing costs and improving sustainability.
Conclusion: The Path to Success
Quality control and inventory cost reduction are vital components in achieving operational excellence for any organization.
Mid-level purchasing employees have the power to drive change by implementing effective quality measures, optimizing supply chain processes, and adopting innovative solutions.
By learning from success stories and applying proven strategies, employees can contribute significantly to the organization’s goals and foster a culture of continuous improvement.
The journey towards efficient quality control and inventory management is ongoing, but with the right strategies, it leads to tangible benefits for businesses and their customers alike.
資料ダウンロード
QCD調達購買管理クラウド「newji」は、調達購買部門で必要なQCD管理全てを備えた、現場特化型兼クラウド型の今世紀最高の購買管理システムとなります。
ユーザー登録
調達購買業務の効率化だけでなく、システムを導入することで、コスト削減や製品・資材のステータス可視化のほか、属人化していた購買情報の共有化による内部不正防止や統制にも役立ちます。
NEWJI DX
製造業に特化したデジタルトランスフォーメーション(DX)の実現を目指す請負開発型のコンサルティングサービスです。AI、iPaaS、および先端の技術を駆使して、製造プロセスの効率化、業務効率化、チームワーク強化、コスト削減、品質向上を実現します。このサービスは、製造業の課題を深く理解し、それに対する最適なデジタルソリューションを提供することで、企業が持続的な成長とイノベーションを達成できるようサポートします。
オンライン講座
製造業、主に購買・調達部門にお勤めの方々に向けた情報を配信しております。
新任の方やベテランの方、管理職を対象とした幅広いコンテンツをご用意しております。
お問い合わせ
コストダウンが利益に直結する術だと理解していても、なかなか前に進めることができない状況。そんな時は、newjiのコストダウン自動化機能で大きく利益貢献しよう!
(Β版非公開)