- お役立ち記事
- Sustainability and Manufacturing Digitally Supported Eco-Friendly Production
Sustainability and Manufacturing Digitally Supported Eco-Friendly Production
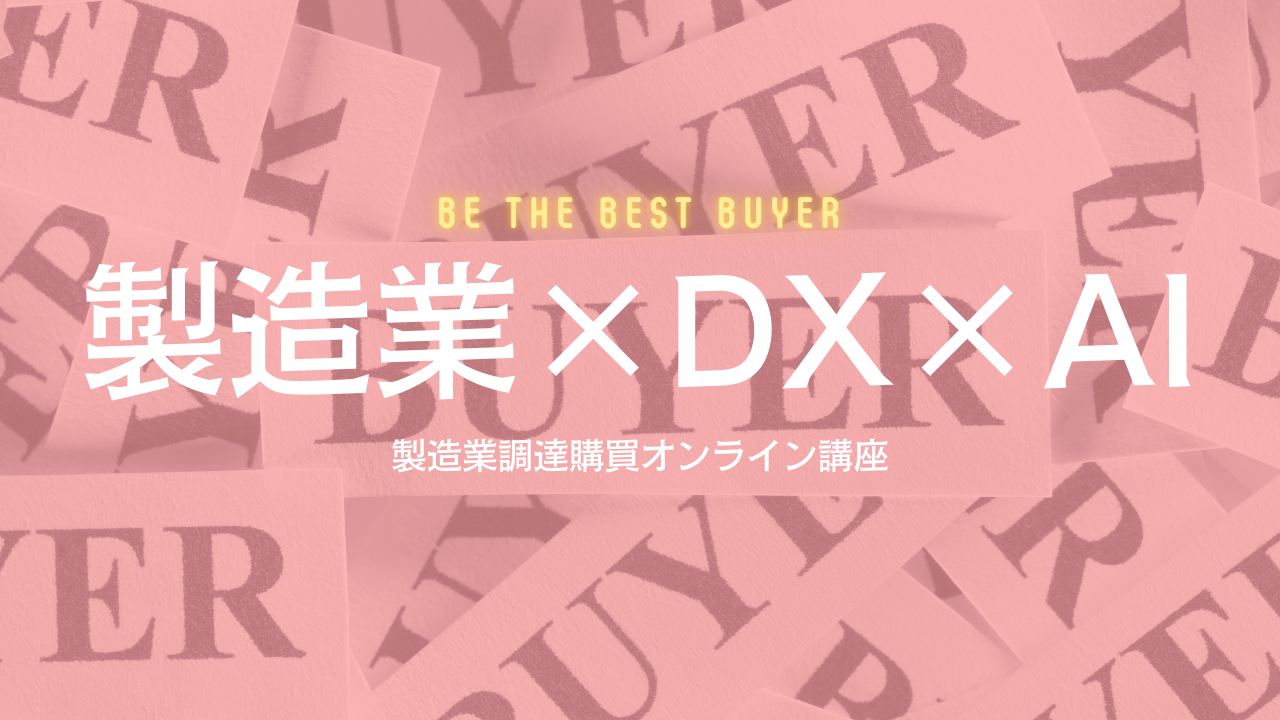
Sustainability and Manufacturing
Sustainability has become increasingly important in manufacturing as consumers and governments alike call for greener practices that reduce environmental impact. By implementing digital solutions, manufacturers can streamline operations to produce goods in a more eco-friendly way. Technologies like the industrial internet of things (IIoT), cloud computing, 3D printing, and robotics offer data-driven opportunities to shrink factories’ carbon footprints and operate more sustainably.
A major sustainability win comes from using data collected via IoT sensors to optimize energy usage. IIoT devices can monitor energy consumption across manufacturing equipment in real-time, spotting inefficiencies that point to wasted power. Analytics reveal which machines run hottest or sit idle too long, allowing targeted efficiency efforts. With data-backed insights, manufacturers fine-tune processes, program automated shutdowns, or switch to renewable energy sources optimized for daily or seasonal usage profiles. Studies show IoT-powered energy management yields energy savings of 10-30% on average.
Further production sustainability gains arise from deploying robotics and automation. Where humans once performed manual labor intensive and repetitive tasks, robots now take over dangerous, physically demanding roles. This protects worker safety and wellness while maintaining throughput. Robots also operate 24/7 with precision, enabling tighter quality control that reduces scrap. Less human involvement means less opportunity for accidents or defects that necessitate reworks – a major sustainability win when each redo consumes additional materials and factory resources. Automation also allows leaner, more adaptable facilities that optimize real estate footprints.
Digital technologies enhance eco-friendly design and prototyping workflows as well. 3D printing streamlines product development cycles, enabling rapid testing of sustainable design concepts. Engineers produce and iterate part designs virtually, minimizing physical prototyping needs. This cuts waste from discarded prototype iterations. 3D printing also promotes on-demand, localized manufacturing by leveraging digital files to produce custom components as and when needed. Without maintaining large centralized inventories, factories reduce excess stockpiles that may go unused. This distributed manufacturing model optimizes supply chains and lowers transportation emissions from fewer long-haul product shipments.
Cloud infrastructure further supports sustainable digital transformation. Manufacturers access cloud-hosted design software, simulation tools, and data analytics platforms from any internet-connected location. This improves collaboration and information sharing between global teams without large capital outlays on physical IT hardware. Cloud adoption reduces upfront costs and long-term operational expenses compared to maintaining expensive, rigid on-premise systems. Resources are consumed elastically based on real usage versus purchasing excess on-site capacity that sits idle. Overall equipment and cooling needs shrink, lowering physical plant footprints and energy loads.
Digitally-enabled Lean Manufacturing strategies also boost eco-friendliness. Manufacturers leverage data insights to identify value-adding from non-value-adding activities across workflows. They eliminate waste and inefficiency whether that means reducing motion, waiting times, defects, or overproduction. Less rework means less material, water and energy consumption. Better planned just-in-time production schedules match supplies with demand, avoiding excess inventory storing. This all cuts factory space demands while optimizing resource usage. Data-driven process optimization identifies small areas for incremental improvement with compounding sustainability effects at scale.
While upfront investments are required, digital transformation’s long term sustainability and economic benefits make a compelling case for manufacturers. Savings from energy cost reductions, increased throughput, and optimized operations pay back initial technology spend. Beyond pure dollars, manufacturers earn brand reputation uplift by demonstrating genuine commitment to ESG initiatives. They attract and retain top talent who increasingly prioritize companies leading the sustainability charge. Government regulators may also offer incentives for manufacturers reducing emissions and waste. Overall the digitally-supported path to eco-friendly production equips manufacturers with competitive advantages well into the future as sustainability becomes ever more imperative.
資料ダウンロード
QCD調達購買管理クラウド「newji」は、調達購買部門で必要なQCD管理全てを備えた、現場特化型兼クラウド型の今世紀最高の購買管理システムとなります。
ユーザー登録
調達購買業務の効率化だけでなく、システムを導入することで、コスト削減や製品・資材のステータス可視化のほか、属人化していた購買情報の共有化による内部不正防止や統制にも役立ちます。
NEWJI DX
製造業に特化したデジタルトランスフォーメーション(DX)の実現を目指す請負開発型のコンサルティングサービスです。AI、iPaaS、および先端の技術を駆使して、製造プロセスの効率化、業務効率化、チームワーク強化、コスト削減、品質向上を実現します。このサービスは、製造業の課題を深く理解し、それに対する最適なデジタルソリューションを提供することで、企業が持続的な成長とイノベーションを達成できるようサポートします。
オンライン講座
製造業、主に購買・調達部門にお勤めの方々に向けた情報を配信しております。
新任の方やベテランの方、管理職を対象とした幅広いコンテンツをご用意しております。
お問い合わせ
コストダウンが利益に直結する術だと理解していても、なかなか前に進めることができない状況。そんな時は、newjiのコストダウン自動化機能で大きく利益貢献しよう!
(Β版非公開)