- お役立ち記事
- Technical Guide for SMEs to Leverage Insert Molding
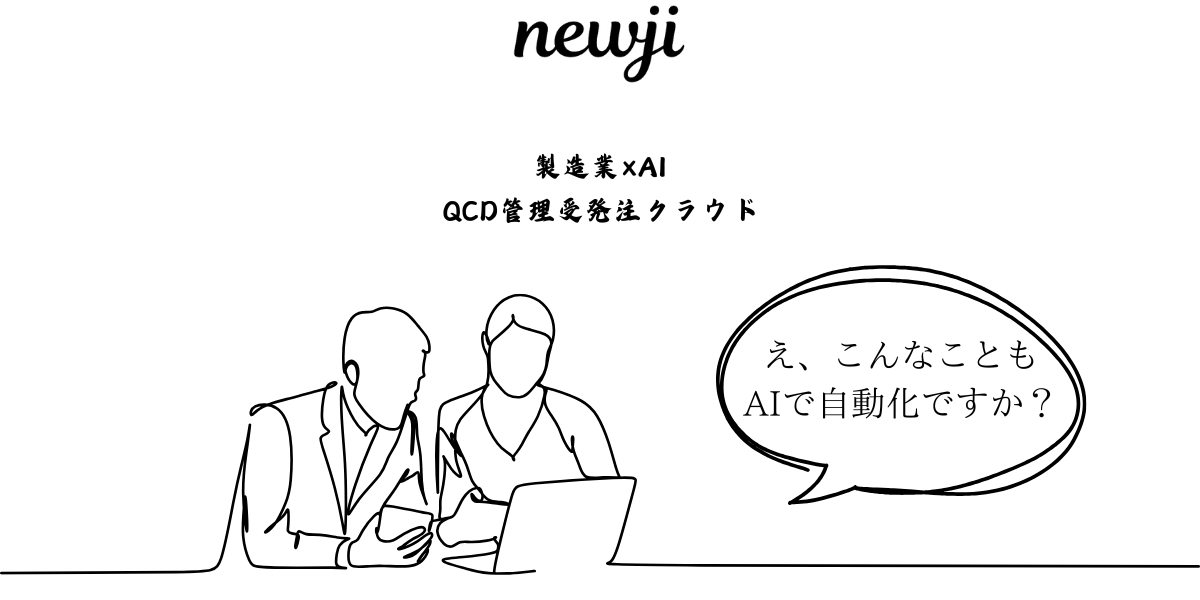
Technical Guide for SMEs to Leverage Insert Molding
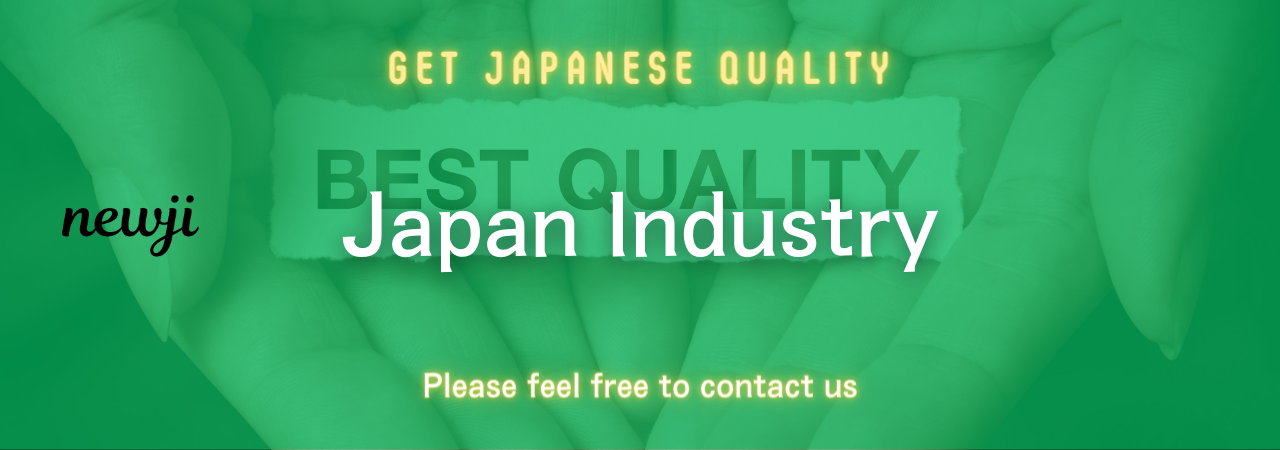
目次
What is Insert Molding?
Insert molding is a versatile manufacturing process used extensively in the production of various plastic parts, especially for small and medium enterprises (SMEs).
This process involves encapsulating a pre-formed part, often metal, with a plastic material in a mold.
The result is a single, integrated unit with enhanced functionality and durability.
Insert molding allows manufacturers to combine materials to achieve properties like improved strength, conductivity, or magnetic capabilities.
SMEs in industries ranging from electronics to automotive use insert molding to streamline production, reduce assembly time, and lower costs.
Benefits of Insert Molding for SMEs
Insert molding offers several advantages for small and medium-sized enterprises looking to enhance their manufacturing processes.
Firstly, it reduces the need for additional assembly steps.
This results in a decrease in labor costs and potential errors during assembly, which is particularly beneficial for SMEs with limited resources.
Another benefit is the design flexibility it provides.
SMEs can integrate complex geometries and multiple functionalities into a single part, making them more competitive by offering innovative solutions to their customers.
Additionally, insert molding supports the use of multiple materials in a compact form factor, which can be crucial in electronics or medical device manufacturing.
Cost Effectiveness
For SMEs, managing costs is a top priority.
Insert molding helps in this regard by minimizing material waste and reducing cycle times.
Since the process allows for the precise application of plastic, companies can save on raw material expenses while also cutting down on post-production finishing tasks.
Enhanced Durability
Parts produced using insert molding exhibit superior durability compared to those made with conventional assembly techniques.
The bond formed between the plastic and the insert ensures that the components are robust and better equipped to handle mechanical stresses.
This increases the lifespan of the products, which is a significant value-add for SMEs focused on maintaining high-quality standards.
Steps Involved in Insert Molding
Understanding the steps involved in insert molding can help SMEs optimize their production processes.
The first step is to select the appropriate type of insert and the plastic material.
Choosing the right materials is crucial for ensuring the desired properties of the final product.
Once the materials are selected, the next step is to prepare the insert.
This involves cleaning and treating the insert to ensure proper adhesion with the plastic.
Surface treatments enhance the bonding process and can significantly improve the quality of the molded part.
The insert is then placed in a mold where the plastic material is injected around it.
Using high precision equipment, the plastic is melted and injected under pressure to form a solid, integrated part upon cooling.
The final step is the removal of the molded part and any necessary finishing touches, such as deburring or surface polishing, to ensure a flawless final product.
Materials Used in Insert Molding
Insert molding involves a diverse range of materials, allowing SMEs to tailor their products to specific applications.
The inserts are commonly made from metals like stainless steel, brass, or aluminum due to their conductive and structural properties.
However, other materials like ceramic or high-strength composites can also be used depending on the application requirements.
For the plastic portion, thermoplastics such as polycarbonate, nylon, polypropylene, and ABS are popular due to their adaptability and resilience.
The choice of plastic depends on factors like temperature resistance, flexibility, and impact strength.
SMEs should consider the end-use environment of the product when selecting the plastic to ensure the final part meets necessary performance criteria.
Applications of Insert Molding
Insert molding has a wide range of applications across various industries.
In the automotive sector, it’s used to produce components that combine electrical and mechanical functionalities, such as circuit boards and sensor housings.
For electronics, insert molding enables the creation of compact, integrated devices where metal inserts serve as conductors or heat sinks.
The medical industry benefits from the precise and reliable nature of insert molding, which is essential for creating complex and sterile components for medical devices.
In the consumer goods sector, the process is used to produce a variety of everyday items, from kitchen utensils to furniture components, offering enhanced performance and durability.
Considerations for SMEs Implementing Insert Molding
Successfully leveraging insert molding requires careful planning and consideration of several key factors.
Firstly, SMEs need to invest in high-quality molds and injection equipment to ensure consistent and precise production.
The quality of the mold directly impacts the accuracy and surface finish of the final product.
Another consideration is the design of the insert itself.
Engineers must ensure the insert is compatible with the intended plastic material and that it will withstand the injection molding process.
This involves testing various combinations and parameters to achieve the best results.
Furthermore, SMEs should also consider the training and expertise required for their staff to operate and maintain insert molding equipment effectively.
Skilled technicians are essential for troubleshooting and optimizing the process.
Streamlining Production
To fully benefit from insert molding, SMEs can streamline their production by investing in automation technology.
Automated systems can handle repetitive tasks, like loading inserts and removing finished parts, freeing up skilled workers for more complex tasks.
This not only improves efficiency but also reduces production time and costs.
Future Trends in Insert Molding
Insert molding technology continues to evolve, presenting new opportunities for SMEs to innovate and expand their capabilities.
Advancements in materials science are leading to the development of new polymers and composite materials that offer enhanced properties.
These materials can open up new applications and markets for SMEs.
Moreover, the integration of digital technologies, such as IoT and AI, in manufacturing processes is enabling real-time monitoring and predictive maintenance, thus improving productivity and minimizing downtime.
Insert molding for SMEs holds the potential to revolutionize various industries by reducing costs, improving quality, and enhancing product functionality.
SMEs that embrace this technology can gain a competitive edge in a rapidly changing market landscape.
資料ダウンロード
QCD調達購買管理クラウド「newji」は、調達購買部門で必要なQCD管理全てを備えた、現場特化型兼クラウド型の今世紀最高の購買管理システムとなります。
ユーザー登録
調達購買業務の効率化だけでなく、システムを導入することで、コスト削減や製品・資材のステータス可視化のほか、属人化していた購買情報の共有化による内部不正防止や統制にも役立ちます。
NEWJI DX
製造業に特化したデジタルトランスフォーメーション(DX)の実現を目指す請負開発型のコンサルティングサービスです。AI、iPaaS、および先端の技術を駆使して、製造プロセスの効率化、業務効率化、チームワーク強化、コスト削減、品質向上を実現します。このサービスは、製造業の課題を深く理解し、それに対する最適なデジタルソリューションを提供することで、企業が持続的な成長とイノベーションを達成できるようサポートします。
オンライン講座
製造業、主に購買・調達部門にお勤めの方々に向けた情報を配信しております。
新任の方やベテランの方、管理職を対象とした幅広いコンテンツをご用意しております。
お問い合わせ
コストダウンが利益に直結する術だと理解していても、なかなか前に進めることができない状況。そんな時は、newjiのコストダウン自動化機能で大きく利益貢献しよう!
(Β版非公開)