- お役立ち記事
- Technical Points to Prevent Defects in High-Speed Injection Molding
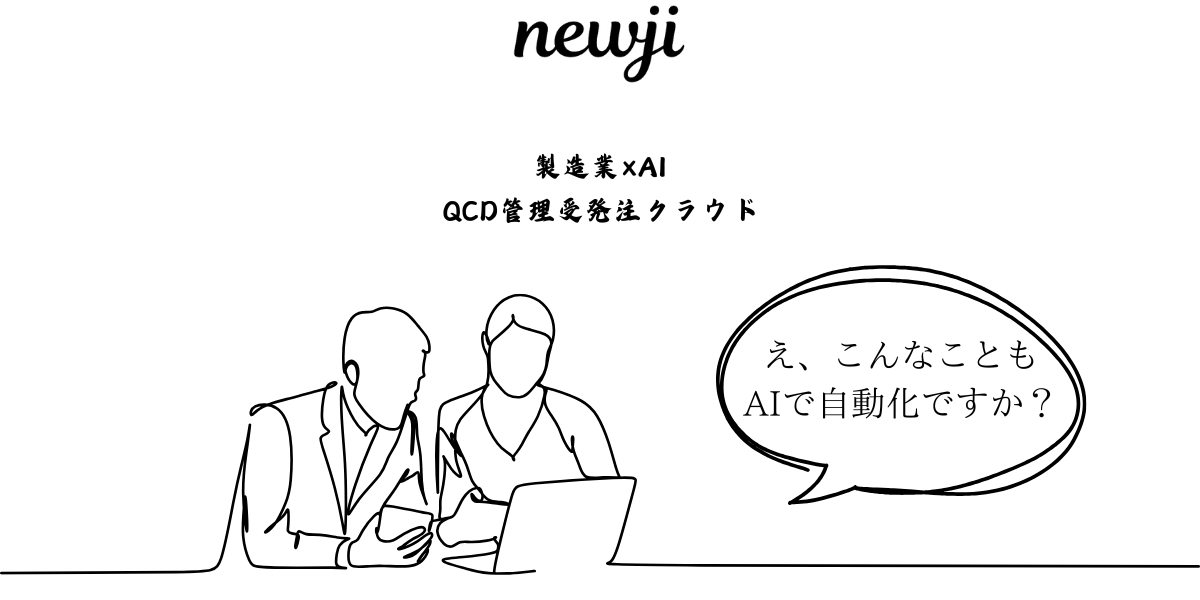
Technical Points to Prevent Defects in High-Speed Injection Molding
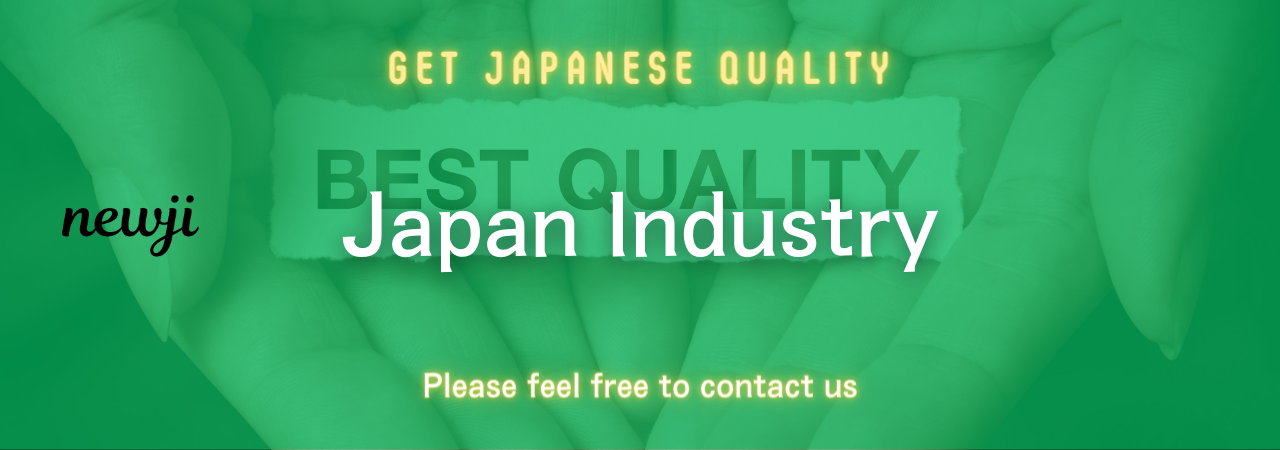
目次
Understanding High-Speed Injection Molding
High-speed injection molding is a manufacturing process commonly used to produce plastic parts at an accelerated rate.
This technique enhances the efficiency of production and is favored for its ability to produce complex components quickly.
It is important to understand the technical intricacies involved in this process to ensure high-quality outputs.
High-speed injection molding involves injecting molten plastic into a mold with high pressure and speed.
This rapid filling can lead to defects if not managed correctly.
Therefore, knowing how to control the variables influencing the process is critical.
Common Defects in High-Speed Injection Molding
Before diving into prevention strategies, let’s explore some of the common defects that can arise in high-speed injection molding.
Shrinkage is a prevalent issue, occurring when the cooling plastic contracts significantly.
Warping is another defect where parts bend or twist, often due to uneven cooling or internal stresses.
Flash occurs when excess material seeps out of the mold cavity, creating unwanted thin protrusions.
Sink marks can appear if cooling is uneven, leaving small depressions on the surface of the part.
Additionally, short shots happen when the mold cavity isn’t completely filled, resulting in incomplete parts.
Understanding these defects is essential for developing preventative measures.
Selecting the Right Materials
Choosing the appropriate material for high-speed injection molding is crucial.
The properties of the plastic material, such as its viscosity and cooling rate, directly impact the final product.
Opt for materials specifically formulated for high-speed injection, often those that can withstand rapid processing without degrading.
Moreover, working closely with material suppliers can provide valuable insights into selecting plastics that align with your specific production needs.
The right material choice not only prevents defects but enhances the overall efficiency of the molding process.
Importance of Material Consistency
Ensuring material consistency is vital to prevent defects.
Irregularities in raw materials can lead to varying part quality, making it hard to maintain uniformity across production batches.
Regularly test incoming materials and maintain a relationship with reliable suppliers to ensure quality consistency.
Optimizing Mold Design
Mold design plays a pivotal role in defect prevention.
It is essential to design molds that can handle rapid filling without compromising part quality.
Ensuring uniform cavity wall thickness and providing adequate venting helps in maintaining a stable molding process.
Moreover, incorporating well-designed cooling channels contributes to uniform cooling, reducing the likelihood of warping and shrinkage.
Thorough analysis during the mold design phase can significantly reduce defect risks.
Using Advanced Simulation Software
Utilizing simulation software during the design phase allows for testing and analysis of mold performance.
This step helps identify potential problem areas before actual production begins, saving time and resources.
Simulation tools can also assist in predicting how different materials will behave in specific mold designs.
Precision in Equipment Calibration
Accurate calibration of the injection molding machinery is imperative.
The machinery must be precisely set to handle the high speeds and pressures associated with the process.
Regularly calibrate machines to maintain optimum performance and prevent discrepancies in part production.
Machinery maintenance schedules should be strictly followed to ensure all components are functioning correctly.
Automation and Monitoring Systems
Incorporating automation and monitoring systems can greatly aid in defect prevention.
These systems provide real-time data and alerts, allowing for immediate adjustments to the process where needed.
Automated systems can also help in maintaining consistent cycle times, leading to uniform product quality.
Control of Process Parameters
Managing process parameters is a critical aspect of high-speed injection molding.
This includes maintaining optimal temperatures, pressures, and injection speeds.
Temperature control is crucial; too high or too low can cause defects like warping or short shots.
Pressure adjustments need to be carefully managed to ensure the cavity is filled completely without causing flash.
Monitoring and controlling these parameters help in maintaining consistent product quality.
Training and Skilled Workforce
Ensuring that your workforce understands the intricacies of high-speed injection molding can prevent many defects.
Invest in thorough training programs to equip employees with the knowledge and skills necessary to handle the machinery and adjust process parameters effectively.
Skilled operators can identify potential issues before they lead to defects, offering a proactive approach to quality control.
Post-Production Inspection
Implementing a robust post-production inspection process is essential.
Inspect parts thoroughly to identify any defects that may have occurred during production.
Utilizing advanced inspection technologies, such as 3D scanning and automated visual inspectors, can enhance precision in defect identification.
Frequent inspections help in catching trends or issues early, allowing for corrective measures before significant production losses occur.
Feedback Loop for Continuous Improvement
Establishing a feedback loop can lead to continuous improvement.
Collect data on defects and use this information to refine processes and prevent future issues.
Engage in regular reviews of defect rates and process changes to ensure that adjustments lead to better outcomes.
This continuous improvement mindset contributes to long-term efficiency and quality in high-speed injection molding.
Conclusion
Through understanding and implementing these technical points, you can significantly reduce defects in high-speed injection molding.
From material selection and mold design to equipment calibration and process control, each step plays a critical role.
By focusing on these aspects, manufacturers can enhance product quality, increase production efficiency, and ultimately, achieve greater success in their high-speed injection molding operations.
資料ダウンロード
QCD調達購買管理クラウド「newji」は、調達購買部門で必要なQCD管理全てを備えた、現場特化型兼クラウド型の今世紀最高の購買管理システムとなります。
ユーザー登録
調達購買業務の効率化だけでなく、システムを導入することで、コスト削減や製品・資材のステータス可視化のほか、属人化していた購買情報の共有化による内部不正防止や統制にも役立ちます。
NEWJI DX
製造業に特化したデジタルトランスフォーメーション(DX)の実現を目指す請負開発型のコンサルティングサービスです。AI、iPaaS、および先端の技術を駆使して、製造プロセスの効率化、業務効率化、チームワーク強化、コスト削減、品質向上を実現します。このサービスは、製造業の課題を深く理解し、それに対する最適なデジタルソリューションを提供することで、企業が持続的な成長とイノベーションを達成できるようサポートします。
オンライン講座
製造業、主に購買・調達部門にお勤めの方々に向けた情報を配信しております。
新任の方やベテランの方、管理職を対象とした幅広いコンテンツをご用意しております。
お問い合わせ
コストダウンが利益に直結する術だと理解していても、なかなか前に進めることができない状況。そんな時は、newjiのコストダウン自動化機能で大きく利益貢献しよう!
(Β版非公開)