- お役立ち記事
- Techniques for Managing Machining Tolerances in Machine Tools
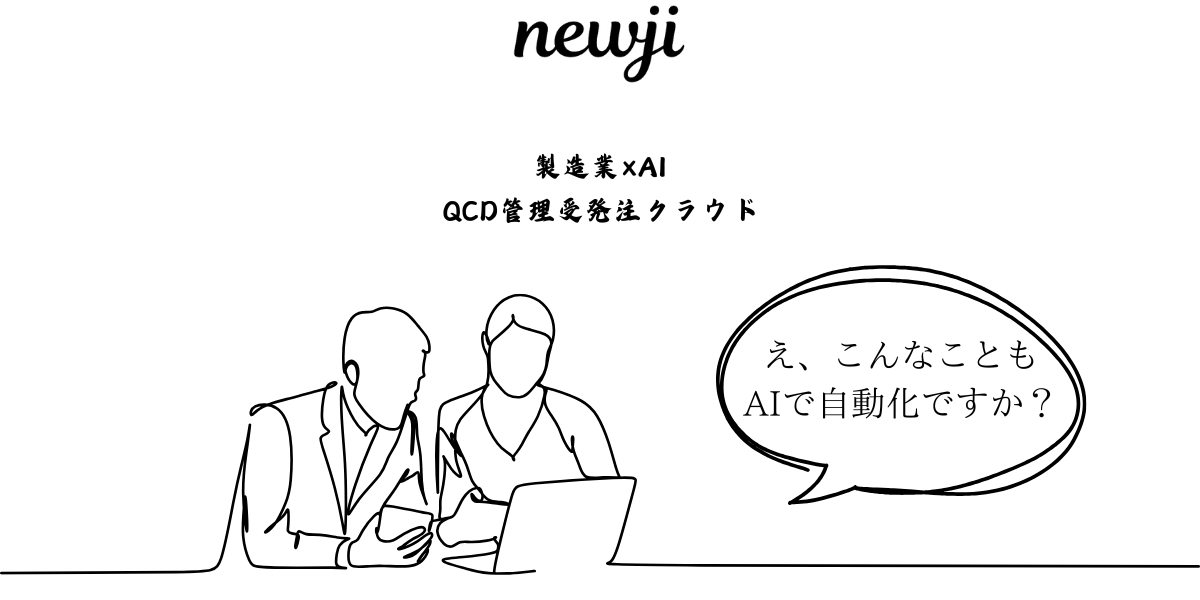
Techniques for Managing Machining Tolerances in Machine Tools
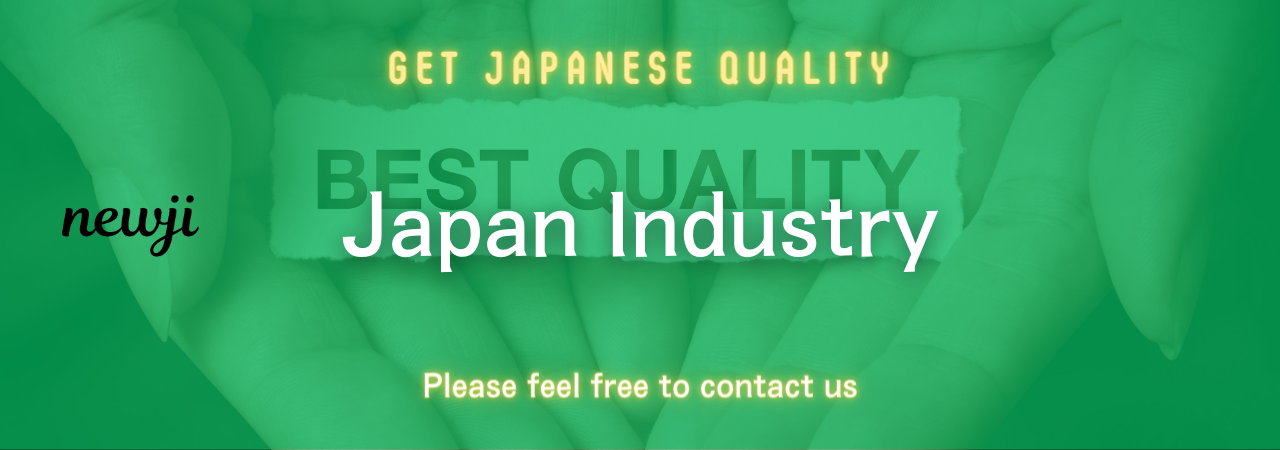
目次
Understanding Machining Tolerances
Machining tolerances refer to the permissible limit of variation in a physical dimension or mechanical property of a manufactured part.
In the world of machine tools, managing these tolerances is crucial to ensure components fit together properly and function as intended.
Tolerances determine how much a part can deviate from its intended dimensions before it is considered unacceptable.
Properly managing machining tolerances is key to achieving precision and maintaining the quality of the final product.
Importance of Tolerances in Machining
Tolerances in machining play a vital role in ensuring parts are manufactured to specification, reducing waste, and improving efficiency.
They directly impact the performance and reliability of mechanical assemblies, making understanding and applying the correct tolerances essential.
With precise tolerances in place, manufacturers can ensure that parts fit together without excessive force, avoiding damage and wear.
This precision is particularly important in industries like aerospace and automotive, where parts need to meet stringent standards to ensure safety and functionality.
Types of Tolerances
There are several types of tolerances used in machining, each suited for different purposes:
– **Linear Tolerance**: This type measures variation in dimensions such as length, width, and height.
– **Geometric Tolerance**: This involves the shape, orientation, and location of a feature within a part.
– **Symmetric Tolerance**: These are equal deviations allowed on either side of a median dimension.
– **Limit Tolerance**: A dimension specified with both upper and lower bounds to restrict variability.
Understanding these types of tolerances helps machinists and engineers specify the right limits for their projects.
Factors Influencing Tolerances
Several factors can influence the machining tolerances, affecting how they are managed:
Material Properties
The material from which a part is made can greatly influence its tolerance.
Different materials expand or contract at varying rates when exposed to temperature changes during machining.
Soft materials might deform easily, while harder materials may be more challenging to machine to tight tolerances.
Machine Tool Accuracy
The precision and capability of the machine tool itself play a significant role.
Modern CNC machines can achieve high accuracy, but regular maintenance and calibration are necessary to maintain their precision.
Tool Wear and Calibration
Tool wear is a natural occurrence in machining processes.
As tools wear, they can affect the precision of the cut, leading to deviations in tolerance.
Regular calibration and replacement of tools are necessary to manage this factor effectively.
Operator Skill and Experience
The skill level and experience of the operator can significantly influence the outcome.
Operators must have a deep understanding of machining processes and the ability to adjust settings to compensate for material variations, tool wear, and machine performance.
Techniques for Managing Machining Tolerances
Proper techniques are essential for managing machining tolerances effectively:
Utilizing Precision Measuring Tools
Precision measuring tools such as calipers, micrometers, and coordinate measuring machines (CMMs) are vital for checking and verifying tolerances.
These tools help ensure that all components meet the specified requirements before they are assembled or delivered.
Implementing Statistical Process Control (SPC)
SPC involves using statistical methods to monitor and control a process.
By analyzing data from manufacturing processes, operators can identify trends and variations in real-time.
This enables timely adjustments to maintain control over tolerances, improving the overall quality of the final product.
Regular Maintenance of Machinery
Consistent maintenance schedules for machine tools help maintain their accuracy.
This includes checking machine alignment, lubricating moving parts, and replacing worn components.
Regular maintenance reduces the risk of producing parts outside of acceptable tolerances.
Operator Training and Continual Learning
Investing in operator training ensures they are skilled in using tools and technologies necessary for precision machining.
Continual learning programs help operators stay up-to-date with the latest advancements and best practices in managing machining tolerances.
Benefits of Effective Tolerance Management
By mastering tolerance management, manufacturers can enjoy several benefits:
Improved Quality and Performance
Precise tolerance management ensures high-quality products that perform reliably under specified conditions.
This leads to fewer defects, higher customer satisfaction, and enhanced reputation in the market.
Cost Savings
By reducing waste and minimizing the need for rework, businesses can save on material costs and labor expenses.
Effective tolerance management also extends the life of both machine tools and components, further contributing to cost efficiency.
Competitive Advantage
Companies that consistently deliver high-precision parts can differentiate themselves from competitors.
This leads to increased business opportunities and access to markets requiring exacting standards, such as aerospace, automotive, and medical industries.
Conclusion
Managing machining tolerances effectively is a critical component of modern manufacturing.
Understanding the types, factors influencing them, and the techniques available ensures components are made accurately and efficiently.
Through careful control and monitoring, businesses can enhance product quality, reduce costs, and gain a competitive edge in the market.
As technology continues to advance, staying informed and adapting these techniques will be crucial for maintaining excellence in precision machining.
資料ダウンロード
QCD調達購買管理クラウド「newji」は、調達購買部門で必要なQCD管理全てを備えた、現場特化型兼クラウド型の今世紀最高の購買管理システムとなります。
ユーザー登録
調達購買業務の効率化だけでなく、システムを導入することで、コスト削減や製品・資材のステータス可視化のほか、属人化していた購買情報の共有化による内部不正防止や統制にも役立ちます。
NEWJI DX
製造業に特化したデジタルトランスフォーメーション(DX)の実現を目指す請負開発型のコンサルティングサービスです。AI、iPaaS、および先端の技術を駆使して、製造プロセスの効率化、業務効率化、チームワーク強化、コスト削減、品質向上を実現します。このサービスは、製造業の課題を深く理解し、それに対する最適なデジタルソリューションを提供することで、企業が持続的な成長とイノベーションを達成できるようサポートします。
オンライン講座
製造業、主に購買・調達部門にお勤めの方々に向けた情報を配信しております。
新任の方やベテランの方、管理職を対象とした幅広いコンテンツをご用意しております。
お問い合わせ
コストダウンが利益に直結する術だと理解していても、なかなか前に進めることができない状況。そんな時は、newjiのコストダウン自動化機能で大きく利益貢献しよう!
(Β版非公開)