- お役立ち記事
- Techniques to improve wear and corrosion resistance that new employees in the ceramic valve seat manufacturing industry should learn
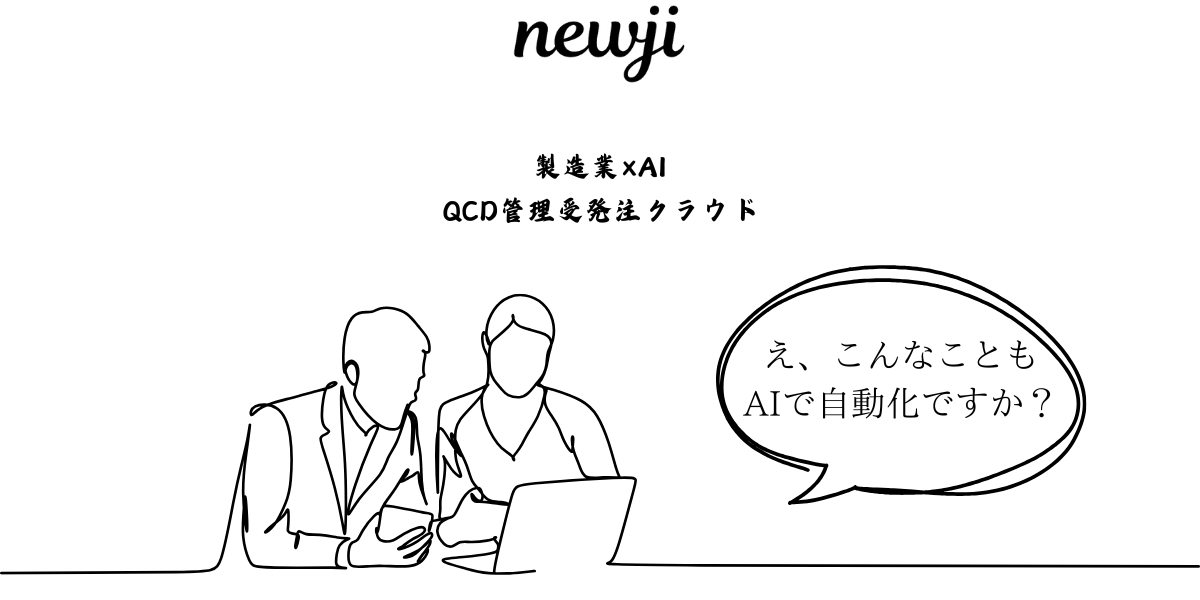
Techniques to improve wear and corrosion resistance that new employees in the ceramic valve seat manufacturing industry should learn
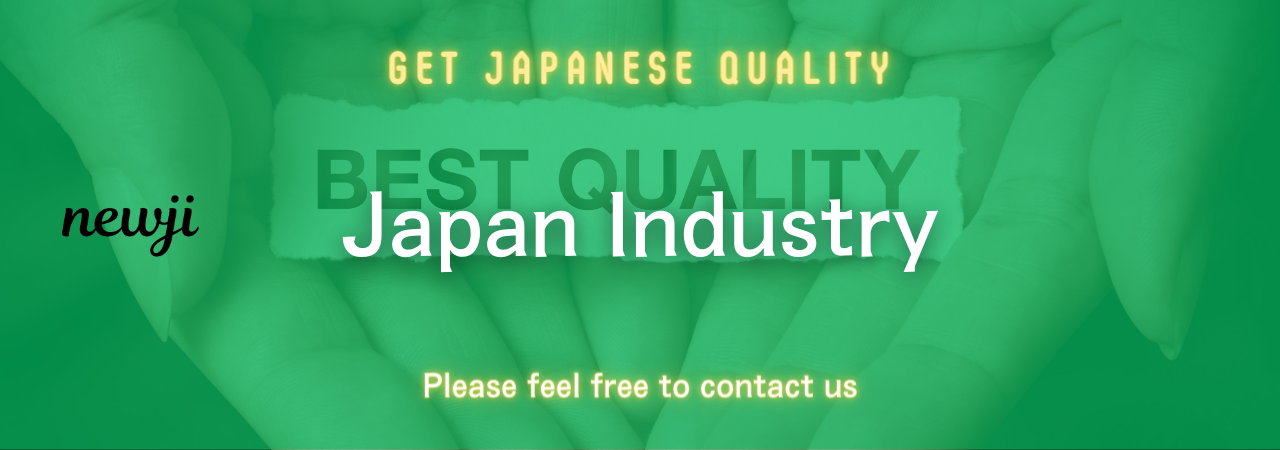
目次
Introduction to Ceramic Valve Seats
Ceramic valve seats play a critical role in various industries due to their exceptional durability and resistance to harsh conditions.
These components are especially valued for their wear and corrosion resistance.
For new employees entering the ceramic valve seat manufacturing industry, understanding the techniques that improve these properties is crucial.
This knowledge not only enhances product quality but also contributes to longer-lasting solutions in industrial applications.
The Importance of Wear and Corrosion Resistance
Wear and corrosion can significantly impact the performance and lifespan of valve seats.
In applications where they are exposed to high temperatures, pressures, and chemically aggressive environments, the ability of ceramic valve seats to withstand these factors is essential.
Failures in these components can lead to system downtime and costly repairs.
For new employees, recognizing the value of wear and corrosion resistance helps in appreciating the intricacies of manufacturing processes.
Moreover, it equips them with the understanding necessary to contribute effectively to innovation and quality improvement efforts in their roles.
Key Techniques to Enhance Wear Resistance
Material Selection
The choice of ceramic material is fundamental to enhancing wear resistance.
Alumina, zirconia, and silicon carbide are popular choices due to their excellent hardness and strength.
Zirconia, for instance, provides excellent toughness and thermal shock resistance, making it suitable for arduous environments.
Understanding the properties of different ceramic materials enables new employees to make informed decisions during the manufacturing process, which directly impacts the product’s performance.
Advanced Manufacturing Processes
Employing advanced manufacturing techniques can significantly improve the wear resistance of ceramic valve seats.
Processes such as hot isostatic pressing (HIP) and pressure-assisted sintering enhance the density and microstructure of ceramics, leading to superior wear characteristics.
New employees should familiarize themselves with these processes, as they are vital in producing high-quality components that stand up to demanding conditions.
Surface Treatments
Surface treatments, such as laser cladding and ion implantation, can further enhance wear resistance.
These treatments strengthen the outer layer of the ceramic valve seat, providing additional protection against abrasion and mechanical wear.
Training in these techniques allows new employees to understand how to apply them effectively, ensuring that the final product meets the required standards for durability and performance.
Techniques to Improve Corrosion Resistance
Chemical Coatings
Applying chemical coatings is a proven method for bolstering the corrosion resistance of ceramic valve seats.
Coatings made from materials such as silicon nitride or silicon carbide create a protective barrier that shields the underlying ceramic from corrosive agents.
New employees should be trained in selecting and applying the right coatings for specific applications, as this skill is essential for producing components that can withstand corrosive environments.
Material Composites
Utilizing composite materials by incorporating corrosion-resistant elements into the ceramic matrix is another effective technique.
This approach enhances the material’s resistance to chemical attacks while maintaining its inherent strength and hardness.
For new employees, understanding how to engineer and apply these composites is key to developing innovative solutions that extend the life of valve seats in corrosive settings.
Environmental Control
Controlling the environmental factors during manufacturing can significantly influence the corrosion resistance of ceramic valve seats.
By ensuring optimal conditions such as humidity, temperature, and cleanliness, manufacturers can reduce the risk of incorporating impurities that compromise corrosion resistance.
New employees should learn about the importance of these factors and how to monitor and control them during the production process.
Quality Assurance and Testing
Quality assurance is a critical component of the ceramic valve seat manufacturing process.
It ensures that the products meet specified standards for wear and corrosion resistance.
Standardized Testing Methods
Familiarity with testing methods such as ASTM and ISO standards is crucial for new employees.
These tests evaluate critical properties like hardness, toughness, and resistance to wear and corrosion, providing insights into the quality of the ceramic valve seats.
Understanding how to conduct these tests and interpret the results is invaluable for maintaining quality and identifying areas for improvement.
Continuous Improvement
Continuous improvement processes such as Six Sigma and lean manufacturing help in identifying inefficiencies and potential upgrades in the manufacturing system.
Encouraging new employees to participate in these initiatives fosters an environment of innovation and quality enhancement.
By understanding these methodologies, new employees can contribute to developing efficient processes that consistently produce high-performance ceramic valve seats.
Conclusion
New employees in the ceramic valve seat manufacturing industry have an exciting opportunity to learn and implement techniques that enhance wear and corrosion resistance.
Through a deep understanding of material selection, advanced manufacturing processes, and quality assurance, they can significantly impact product quality and durability.
Equipping themselves with this knowledge ensures that they can contribute effectively to their organizations, driving innovation and excellence in producing ceramic valve seats that meet the demands of challenging industrial environments.
資料ダウンロード
QCD調達購買管理クラウド「newji」は、調達購買部門で必要なQCD管理全てを備えた、現場特化型兼クラウド型の今世紀最高の購買管理システムとなります。
ユーザー登録
調達購買業務の効率化だけでなく、システムを導入することで、コスト削減や製品・資材のステータス可視化のほか、属人化していた購買情報の共有化による内部不正防止や統制にも役立ちます。
NEWJI DX
製造業に特化したデジタルトランスフォーメーション(DX)の実現を目指す請負開発型のコンサルティングサービスです。AI、iPaaS、および先端の技術を駆使して、製造プロセスの効率化、業務効率化、チームワーク強化、コスト削減、品質向上を実現します。このサービスは、製造業の課題を深く理解し、それに対する最適なデジタルソリューションを提供することで、企業が持続的な成長とイノベーションを達成できるようサポートします。
オンライン講座
製造業、主に購買・調達部門にお勤めの方々に向けた情報を配信しております。
新任の方やベテランの方、管理職を対象とした幅広いコンテンツをご用意しております。
お問い合わせ
コストダウンが利益に直結する術だと理解していても、なかなか前に進めることができない状況。そんな時は、newjiのコストダウン自動化機能で大きく利益貢献しよう!
(Β版非公開)