- お役立ち記事
- The balance between precision and durability that new employees in the automobile assembly line torque wrench manufacturing industry must keep in mind
The balance between precision and durability that new employees in the automobile assembly line torque wrench manufacturing industry must keep in mind
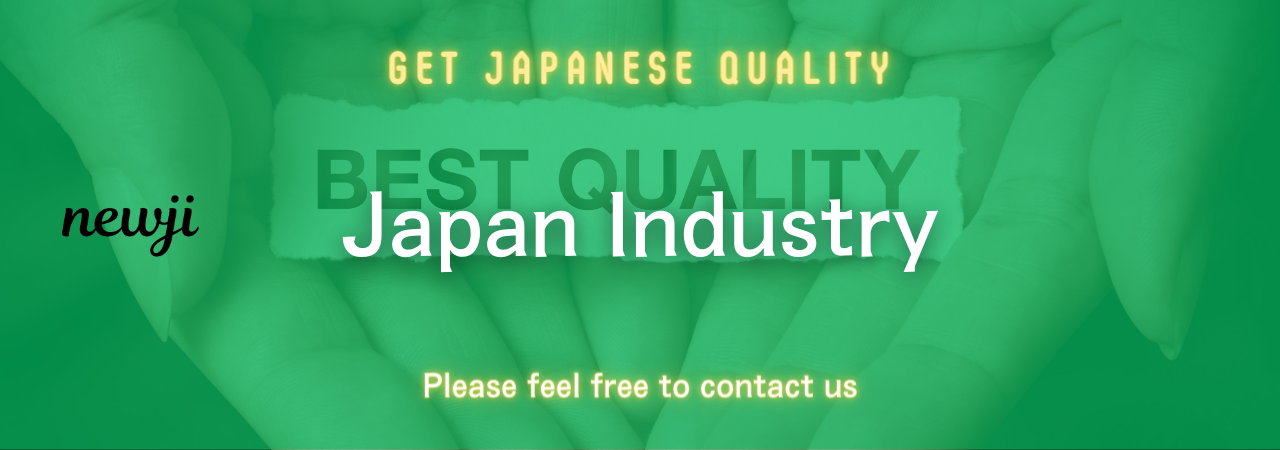
目次
Understanding Torque Wrenches in the Manufacturing Industry
When you join the automobile assembly line, one of the critical tools you’ll encounter is the torque wrench.
This tool is essential in ensuring that bolts in vehicles are tightened precisely to the manufacturer’s specifications.
Achieving this precision is vital for both vehicle safety and performance.
A balanced approach between precision and durability is necessary because the tool must maintain its effectiveness over time despite repeated use.
What is a Torque Wrench?
To begin with, let’s define what a torque wrench is.
A torque wrench is a specialized tool used to apply a specific torque to a fastener, such as a nut or bolt.
It allows mechanics and assemblers to set the bolts firmly enough that they don’t come loose over time, but not so tight that they cause damage.
This balance of tightness is crucial in the auto industry, where a single loose bolt can lead to major safety issues, while over-tightening could break bolts or force cracks into the surrounding materials.
The Importance of Precision
Precision is a primary concern when it comes to using a torque wrench.
Every car model may require different torque settings, meaning technicians need to apply the correct amount for each situation to prevent problems later.
Precision in this context is about ensuring the right amount of force is applied consistently across hundreds or even thousands of bolts across various parts of a vehicle.
Incorrect torque application can lead to complications such as vibrations, inefficient performance, and in worst cases, accidents.
This is why it is essential for new employees to become familiar with the torque specifications for different car models and to understand the significance of each specification.
Maintaining Precision Over Time
Keeping a torque wrench precise over time is equally important as being precise from the start.
Due to frequent usage, a torque wrench can lose its calibration if not maintained correctly, leading to inaccurate readings and potential failures in the assembly line.
New employees should remember to regularly check the calibration of their torque wrenches and recalibrate them as required.
Following the manufacturer’s maintenance guidelines helps prolong the tool’s precision and ensures safety and effectiveness in its use.
The Necessity of Durability
While precision is paramount, durability can’t be overlooked.
A torque wrench faced with repeated use on a busy automobile assembly line must withstand significant wear and tear.
Durability ensures that the tool can perform accurately under various conditions without needing constant replacement.
Factors Affecting Durability
Different factors can impact the durability of a torque wrench, including material quality, design, frequency of use, and maintenance practices.
Investing in high-quality materials and a robust design can ensure that the wrench holds up over time.
Moreover, it’s vital to train employees on using the tool correctly—such as applying the torque smoothly and avoiding dropping or mishandling the wrench—to support its longevity.
Balancing Act Between Precision and Durability
Achieving a balance between precision and durability involves using the tool correctly and maintaining it diligently.
New employees should be taught to handle torque wrenches with care, use them in the right applications, and ensure they are stored properly when not in use.
Practical Tips for New Employees
For those new to the industry, there are a few practical tips to consider regarding torque wrenches:
Understanding Specifications
Learn to read and understand torque specifications as listed in vehicle assembly manuals.
Proper knowledge of these specifications forms the foundation for correct torque application.
Regular Training and Updates
Stay updated with the latest practices and training sessions offered by your company.
Technology and methodologies may change, and continuous education is key to keeping up with best practices.
Implementing Quality Checks
Incorporate regular checks on the torque applied during assembly.
Use precision instruments to ensure the applied torque remains within acceptable limits.
Periodic audits can further help in catching any deviations early.
Building a Routine
Make it a routine to check the calibration of your torque wrenches before starting your shift.
This simple habit can prevent significant issues from developing over time.
Conclusion
The balance between precision and durability is a critical aspect that new employees in the automobile assembly line torque wrench manufacturing industry need to master.
It involves understanding the tool, maintaining it effectively, and implementing the knowledge of torque specifications into daily practice.
By focusing on these aspects, employees can ensure both the safety and quality of the automobiles being produced, contributing positively to the standards and reputation of the industry.
資料ダウンロード
QCD調達購買管理クラウド「newji」は、調達購買部門で必要なQCD管理全てを備えた、現場特化型兼クラウド型の今世紀最高の購買管理システムとなります。
ユーザー登録
調達購買業務の効率化だけでなく、システムを導入することで、コスト削減や製品・資材のステータス可視化のほか、属人化していた購買情報の共有化による内部不正防止や統制にも役立ちます。
NEWJI DX
製造業に特化したデジタルトランスフォーメーション(DX)の実現を目指す請負開発型のコンサルティングサービスです。AI、iPaaS、および先端の技術を駆使して、製造プロセスの効率化、業務効率化、チームワーク強化、コスト削減、品質向上を実現します。このサービスは、製造業の課題を深く理解し、それに対する最適なデジタルソリューションを提供することで、企業が持続的な成長とイノベーションを達成できるようサポートします。
オンライン講座
製造業、主に購買・調達部門にお勤めの方々に向けた情報を配信しております。
新任の方やベテランの方、管理職を対象とした幅広いコンテンツをご用意しております。
お問い合わせ
コストダウンが利益に直結する術だと理解していても、なかなか前に進めることができない状況。そんな時は、newjiのコストダウン自動化機能で大きく利益貢献しよう!
(Β版非公開)