- お役立ち記事
- The Best Molding Techniques for Polypropylene Chosen by SMEs
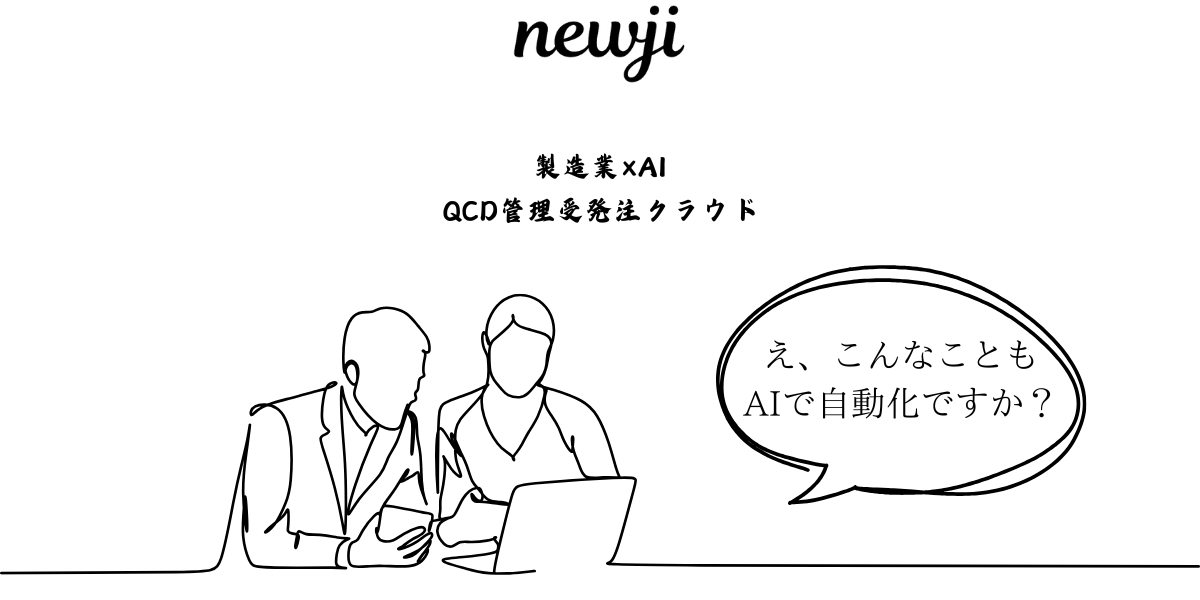
The Best Molding Techniques for Polypropylene Chosen by SMEs
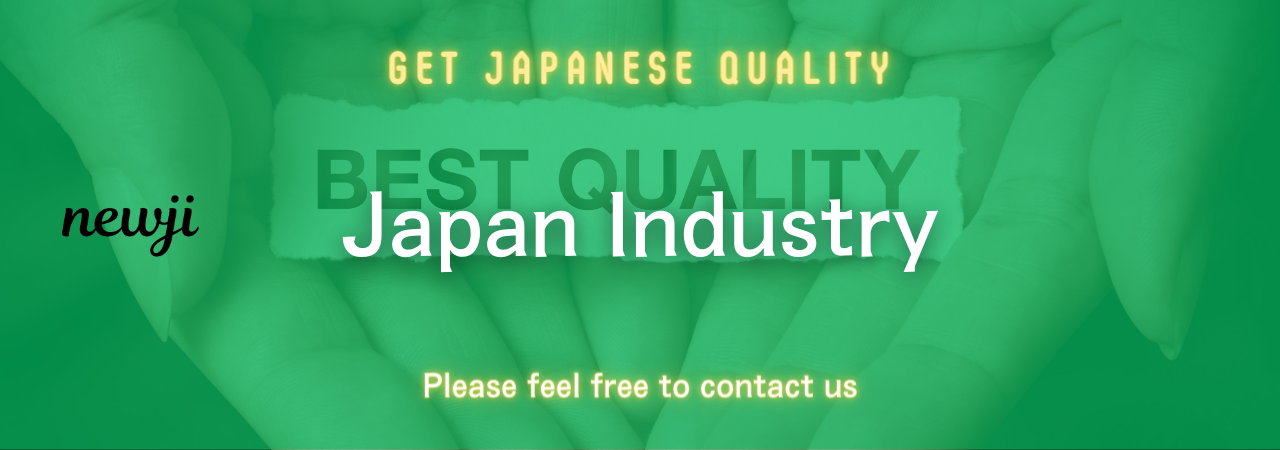
When it comes to creating products with polypropylene, small and medium-sized enterprises (SMEs) have several molding techniques to consider.
Selecting the right method can greatly influence the quality, cost, and production speed of the final product.
Understanding the different techniques available will empower SMEs to make informed decisions that best align with their specific project needs.
目次
What is Polypropylene?
Polypropylene is a versatile thermoplastic polymer used widely in various industries due to its strength, flexibility, and resistance to heat and chemical wear.
With its lightweight yet durable nature, polypropylene is a popular choice for a range of applications, from packaging and automotive components to textiles and consumer goods.
Common Molding Techniques for Polypropylene
Injection Molding
Injection molding is one of the most popular methods for shaping polypropylene.
This process involves injecting molten polypropylene into a mold under high pressure.
Once the material cools, it solidifies into the desired shape.
This technique is favored by SMEs because it allows for high-volume production while maintaining consistent quality.
Injection molding is particularly effective for complex shapes and designs, making it ideal for detailed and intricate products.
Additionally, it offers a quick turnaround time, which is beneficial for businesses looking to bring products to market swiftly.
Blow Molding
Blow molding is another commonly used technique, especially suited for making hollow objects such as bottles and containers.
This process starts with melting polypropylene and forming it into a preform or parison.
Air is then blown into this heated tube, expanding it into the shape of the mold.
For SMEs specializing in packaging solutions, blow molding offers a cost-effective way to produce lightweight yet durable items in large volumes.
Its primary advantage is the ability to manufacture products with uniform wall thickness and a seamless finish.
Rotational Molding
Rotational molding, or rotomolding, involves heating polypropylene in a mold that is slowly rotated along two axes.
This ensures even distribution of the material over the interior surfaces of the mold.
Though rotational molding has a slower production rate compared to other methods, it allows for the creation of large, hollow items with uniform wall thickness.
This technique is ideal for SMEs focused on producing items like tanks, bins, and playground equipment.
Thermoforming
Thermoforming uses heat to shape polypropylene sheets into a form by stretching them over or into a mold.
The experimental setup is then cooled to retain its shape.
SMEs may prefer thermoforming for its low tooling costs and fast prototyping capabilities.
The method is well-suited for creating large, simple parts and is commonly employed in the automotive and packaging industries.
Choosing the Right Molding Technique
Selecting the right molding technique for polypropylene largely depends on the specific requirements of the project.
Here are several factors SMEs should consider:
Product Complexity
For products with intricate designs and complex details, injection molding is often the best choice.
Its precision and ability to accommodate complex geometries make it the preferred method.
However, for simpler items, techniques like thermoforming may be more adequate with lower costs and faster turnaround times.
Production Volume
High-volume production generally benefits from injection or blow molding because of their efficiency and ability to produce large quantities quickly.
Conversely, for limited runs or custom orders, rotational molding or thermoforming can be more cost-effective.
Material Considerations
While polypropylene is the material in question, SMEs should also consider any additives or blends that may be needed, as these can affect the molding process.
Certain techniques may be better suited for handling modified materials.
Cost and Time Constraints
Budget and timeline are critical drivers in the decision-making process.
Injection molding offers efficiency and cost-effectiveness for large-scale productions.
In contrast, methods like rotational molding, which have higher initial investment and longer cycle times, might be more suitable for niche applications due to their flexibility in producing custom shapes.
Quality of Finish
The desired finish of the final product also plays a role in choosing the molding technique.
Blow molding is excellent for achieving smooth finishes in hollow items, while injection molding provides detailed and precise results.
Thermoforming offers a good finish for larger, uncomplicated parts.
Conclusion
Selecting the best molding technique for polypropylene is a crucial decision for SMEs, as it influences both the operational efficiency and the quality of the end product.
By understanding the advantages and limitations of each method, businesses can align their production strategies with their specific needs and objectives.
Whether it’s intricate designs via injection molding, or cost-effective hollow items through blow molding, SMEs have a variety of options at their disposal.
Ultimately, successful selection depends on a thorough analysis of product requirements, budget constraints, and scale of production.
In a rapidly evolving market, SMEs that adeptly choose the right molding techniques will be better positioned to compete, innovate, and deliver superior products.
資料ダウンロード
QCD調達購買管理クラウド「newji」は、調達購買部門で必要なQCD管理全てを備えた、現場特化型兼クラウド型の今世紀最高の購買管理システムとなります。
ユーザー登録
調達購買業務の効率化だけでなく、システムを導入することで、コスト削減や製品・資材のステータス可視化のほか、属人化していた購買情報の共有化による内部不正防止や統制にも役立ちます。
NEWJI DX
製造業に特化したデジタルトランスフォーメーション(DX)の実現を目指す請負開発型のコンサルティングサービスです。AI、iPaaS、および先端の技術を駆使して、製造プロセスの効率化、業務効率化、チームワーク強化、コスト削減、品質向上を実現します。このサービスは、製造業の課題を深く理解し、それに対する最適なデジタルソリューションを提供することで、企業が持続的な成長とイノベーションを達成できるようサポートします。
オンライン講座
製造業、主に購買・調達部門にお勤めの方々に向けた情報を配信しております。
新任の方やベテランの方、管理職を対象とした幅広いコンテンツをご用意しております。
お問い合わせ
コストダウンが利益に直結する術だと理解していても、なかなか前に進めることができない状況。そんな時は、newjiのコストダウン自動化機能で大きく利益貢献しよう!
(Β版非公開)