- お役立ち記事
- The difference between Chemical Polishing and Electrolytic Polishing
月間76,176名の
製造業ご担当者様が閲覧しています*
*2025年3月31日現在のGoogle Analyticsのデータより
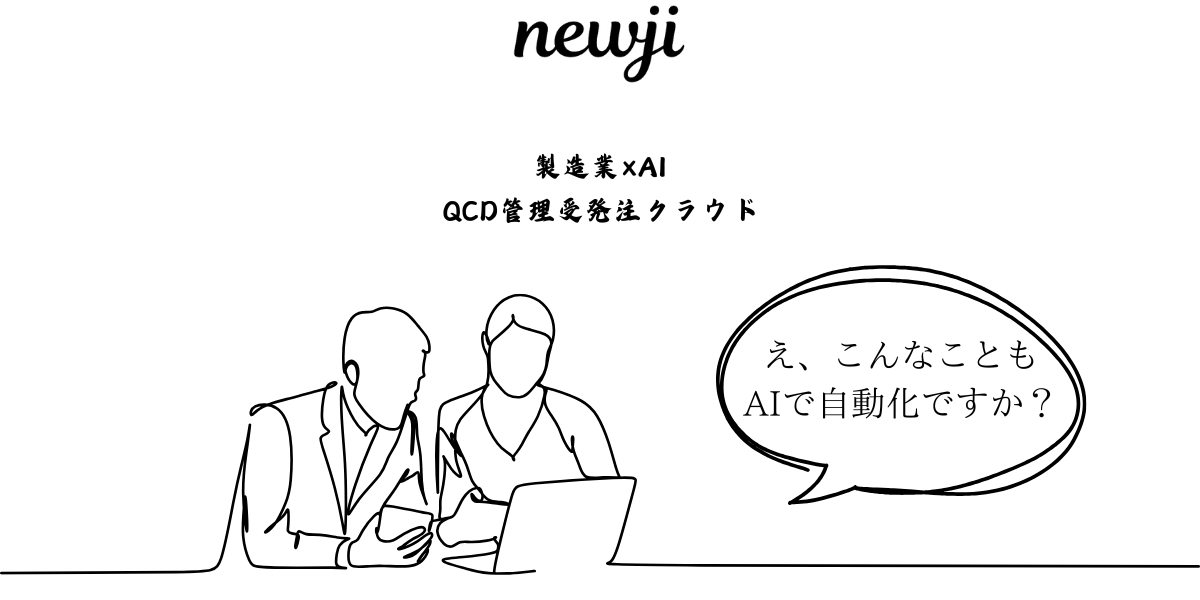
The difference between Chemical Polishing and Electrolytic Polishing
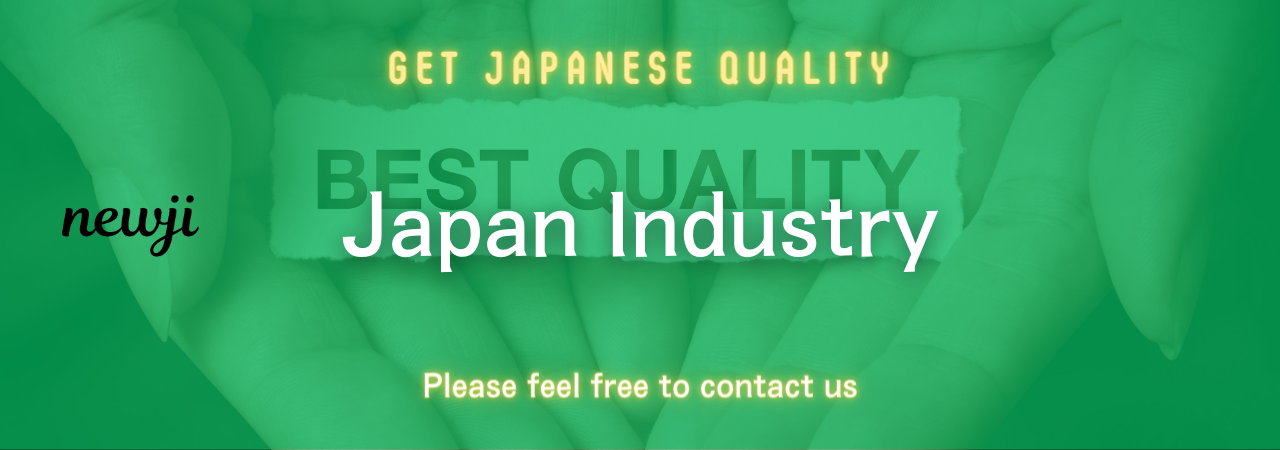
目次
Understanding Chemical Polishing
Chemical polishing is a process used to smooth and brighten the surface of metal objects.
It involves using a chemical solution to dissolve microscopic amounts of material from the surface.
This helps remove burrs, small scratches, and other surface defects.
One of the main benefits of chemical polishing is its ability to improve the appearance of metal parts.
By getting rid of surface imperfections, it makes the metal look shiny and smooth.
This is especially useful for items that need to look good, like decorative pieces or parts of consumer products.
Another advantage of chemical polishing is that it can reach complex shapes and hidden areas.
The chemical solution can flow into tiny crevices and over intricate details, ensuring that the entire surface is evenly polished.
This is something that can be very difficult to achieve with mechanical polishing methods.
However, chemical polishing is not without its downsides.
It’s a process that requires careful control and consistent monitoring.
The chemicals used can be hazardous, and it’s important to handle them properly to avoid risks to health and safety.
Additionally, the disposal of used chemicals needs to be managed in an environmentally responsible manner.
The Basics of Electrolytic Polishing
Electrolytic polishing, often referred to as electro-polishing, is another technique used to smooth and polish metal surfaces.
Unlike chemical polishing, this method involves using electricity to dissolve material from the metal’s surface.
The process involves immersing the metal part in an electrolytic solution and applying an electric current.
One major benefit of electrolytic polishing is the high level of control it offers.
By adjusting the current and the composition of the electrolytic solution, it’s possible to achieve very precise results.
This makes it an excellent choice for parts that need to meet tight specifications.
Electrolytic polishing also offers excellent results in terms of surface finish.
The process can produce a very shiny and smooth appearance, making it ideal for decorative items or parts that need a high-quality finish.
Moreover, electrolytic polishing can significantly improve the metal part’s resistance to corrosion.
The process removes impurities and imperfections, which can act as initiation sites for corrosion.
By making the surface smoother and reducing the number of these potential initiation sites, electrolytic polishing helps to enhance the longevity of the metal part.
However, like chemical polishing, electrolytic polishing also requires careful handling.
It involves the use of electrical equipment and chemical solutions, both of which can be hazardous if not managed correctly.
Ensuring proper safety measures and handling procedures is essential to avoid accidents and ensure a safe working environment.
Key Differences Between Chemical and Electrolytic Polishing
While both chemical and electrolytic polishing serve the same primary purpose of smoothing and polishing metal surfaces, there are several key differences between the two methods.
Method of Material Removal
In chemical polishing, the material is removed through a purely chemical reaction.
The chemical solution dissolves microscopic amounts of material from the surface of the metal.
In electrolytic polishing, material removal happens through an electrochemical reaction.
An electric current is applied to dissolve the material from the surface.
Level of Control
Electrolytic polishing offers a higher level of control compared to chemical polishing.
By adjusting the electrical parameters and the composition of the electrolytic solution, it’s possible to achieve very precise and consistent results.
Chemical polishing, on the other hand, can be more challenging to control.
The rate of material removal can vary depending on the concentration of the chemicals and the temperature of the solution.
Surface Finish
Both chemical and electrolytic polishing can produce a smooth and shiny surface finish.
However, electrolytic polishing tends to provide a higher quality finish with better consistency.
Equipment and Safety Requirements
Chemical polishing primarily requires a suitable chemical solution and equipment for handling and applying it.
While it requires careful handling, the equipment itself is relatively simple.
Electrolytic polishing, however, requires specialized equipment to apply the electric current and control the electrochemical reaction.
This equipment needs to be handled carefully to ensure safety.
Applications
Chemical polishing is often preferred for its ability to reach complex shapes and hidden areas.
It is a popular choice for parts with intricate designs or those that need to be polished all over.
Electrolytic polishing is often chosen for its precision and ability to produce a very high-quality finish.
It is commonly used for parts that need to meet tight specifications and high standards of appearance.
Choosing the Right Method
When deciding between chemical and electrolytic polishing, it’s important to consider the specific requirements of the project.
If the part has a complex shape with many intricate details, chemical polishing might be the better choice because it can evenly polish the entire surface, including hard-to-reach areas.
If the project requires a high level of precision and a superior surface finish, electrolytic polishing might be more suitable.
Additionally, it’s crucial to consider the safety and environmental aspects of each method.
Both processes involve chemicals that need to be handled and disposed of properly.
Understanding the specific hazards and ensuring proper safety measures are in place is essential for a safe and successful polishing process.
Conclusion
Both chemical polishing and electrolytic polishing are valuable techniques for achieving smooth and polished metal surfaces.
Each method has its own set of advantages and considerations.
By understanding the key differences and the specific needs of the project, it is possible to choose the most appropriate method for achieving the desired results.
In any case, ensuring proper handling, safety measures, and environmental responsibility is crucial for a successful and safe polishing process.
資料ダウンロード
QCD管理受発注クラウド「newji」は、受発注部門で必要なQCD管理全てを備えた、現場特化型兼クラウド型の今世紀最高の受発注管理システムとなります。
ユーザー登録
受発注業務の効率化だけでなく、システムを導入することで、コスト削減や製品・資材のステータス可視化のほか、属人化していた受発注情報の共有化による内部不正防止や統制にも役立ちます。
NEWJI DX
製造業に特化したデジタルトランスフォーメーション(DX)の実現を目指す請負開発型のコンサルティングサービスです。AI、iPaaS、および先端の技術を駆使して、製造プロセスの効率化、業務効率化、チームワーク強化、コスト削減、品質向上を実現します。このサービスは、製造業の課題を深く理解し、それに対する最適なデジタルソリューションを提供することで、企業が持続的な成長とイノベーションを達成できるようサポートします。
製造業ニュース解説
製造業、主に購買・調達部門にお勤めの方々に向けた情報を配信しております。
新任の方やベテランの方、管理職を対象とした幅広いコンテンツをご用意しております。
お問い合わせ
コストダウンが利益に直結する術だと理解していても、なかなか前に進めることができない状況。そんな時は、newjiのコストダウン自動化機能で大きく利益貢献しよう!
(β版非公開)