- お役立ち記事
- The difference between Chemical Polishing and Mechanical Polishing
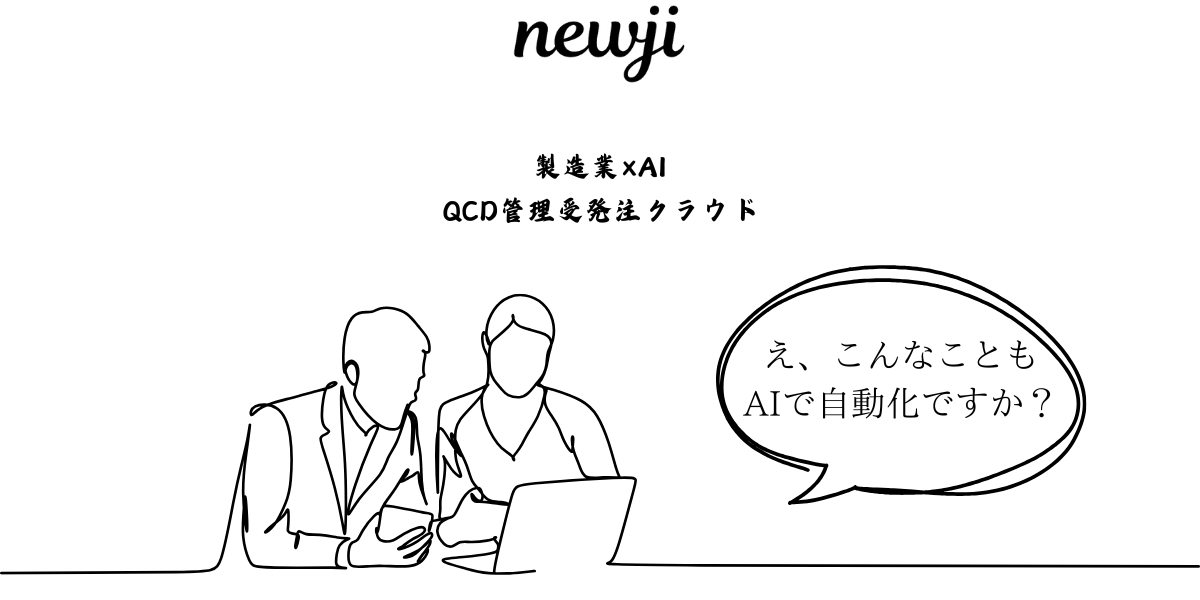
The difference between Chemical Polishing and Mechanical Polishing
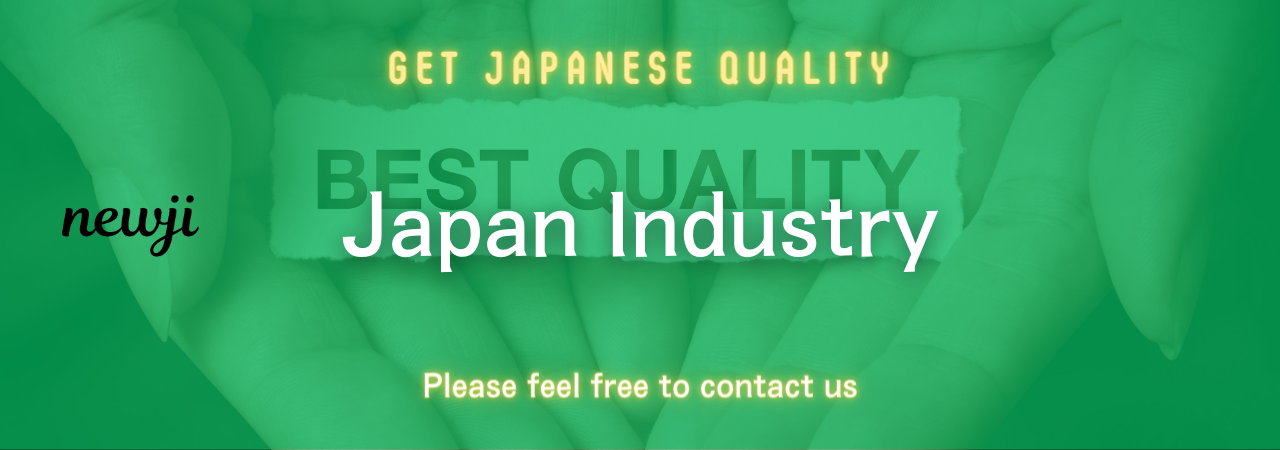
When it comes to finishing metals and other surfaces, both chemical polishing and mechanical polishing are popular methods.
These processes can make a big difference in how the final product looks and performs.
But how are they different?
Let’s dive into the world of polishing to understand the key distinctions between chemical polishing and mechanical polishing.
目次
What is Chemical Polishing?
Chemical polishing, also known as electrolytic polishing or electropolishing, involves the use of chemical solutions to remove material from the surface of a workpiece.
This process smooths the surface by evenly dissolving the highest microscopic peaks.
How It Works
Chemical polishing uses specific chemical solutions to achieve a smooth finish.
The workpiece is submerged in the solution, which typically contains acids or other reactive chemicals.
When current is applied, it facilitates the oxidation process, causing the material to dissolve from the highest points on the surface.
This method allows for polishing complex shapes that may be difficult to achieve with mechanical means.
Advantages
– **Smooth Finish**: Chemical polishing creates a mirror-like surface that is difficult to achieve with mechanical methods.
– **Corrosion Resistance**: The process can improve the corrosion resistance of metals, making them more durable.
– **Deburring**: It is excellent for removing tiny burrs and imperfections that mechanical polishing might miss.
– **Sterility**: Ideal for equipment in medical and food industries due to its ability to create contamination-free surfaces.
Disadvantages
– **Chemical Handling**: Requires careful handling of potentially hazardous chemicals.
– **Cost**: Can be more expensive due to the cost of chemicals and the need for specialized equipment.
– **Material Limitations**: Not suitable for all materials, particularly those that are not chemically reactive.
What is Mechanical Polishing?
Mechanical polishing, on the other hand, involves physically grinding, sanding, or buffing a material’s surface.
This is typically done using abrasive tools such as grinders, polishers, and buffing wheels.
How It Works
Mechanical polishing employs abrasives to wear down the surface of the material.
Depending on the desired finish, different grades of abrasive materials are used, from coarse to fine.
This method is usually conducted in several stages, with each stage using progressively finer abrasives.
The process can either be automated or done manually, allowing for a high degree of control over the final appearance.
Advantages
– **Cost-Effective**: Generally less expensive compared to chemical polishing.
– **Versatility**: Suitable for a wider range of materials, including metals, plastics, and composites.
– **Control**: Offers more control over the amount of material removed, making it ideal for applications requiring precise tolerances.
– **Availability**: Equipment and abrasives are generally more accessible and easier to handle than chemical solutions.
Disadvantages
– **Surface Irregularities**: More likely to leave micro-scratches or other imperfections compared to chemical polishing.
– **Labor-Intensive**: Can be more time-consuming, especially for complex shapes.
– **Heat Generation**: The friction involved can generate heat, which may affect certain materials.
Applications of Both Methods
Where Chemical Polishing is Used
Chemical polishing shines in industries where surface smoothness and sterility are paramount.
It is commonly used in the manufacturing of medical instruments, pharmaceutical equipment, and components for the food and beverage industry.
This method is also favored in aerospace and automotive industries, where smooth, corrosion-resistant surfaces are essential for performance and longevity.
Where Mechanical Polishing is Used
Mechanical polishing is widespread in manufacturing processes where surface aesthetics and dimensional tolerances are crucial.
It is commonly used in metal fabrication, automotive parts, and custom machinery.
Additionally, it is an excellent choice for plastic components, woodworking projects, and even glass and ceramics.
Environmental and Safety Considerations
Both polishing methods have environmental and safety considerations to keep in mind.
Chemical polishing requires the use of hazardous chemicals that need careful handling and disposal.
Operators must use protective gear, and proper ventilation systems must be in place.
Additionally, disposal of chemical waste must comply with environmental regulations to prevent harm.
Mechanical polishing, although generally safer, involves the generation of dust and particulate matter.
Proper dust collection systems should be utilized to keep the workspace clean.
Operators should also wear protective equipment to guard against flying debris and prolonged exposure to fine particles.
Choosing the Right Method
Deciding between chemical polishing and mechanical polishing often comes down to the specific needs of your project.
Consider the Material
The type of material you are working with will significantly influence your choice.
Chemical polishing may not be suitable for materials that aren’t chemically reactive, while mechanical polishing can handle a broader range of substances, including metals, plastics, and composites.
Evaluate the Desired Finish
If a high-gloss, mirror-like finish is essential, chemical polishing may be the better choice.
However, if you need more control over the amount of material removed or require a specific texture, mechanical polishing would be more appropriate.
Assess Cost and Time
Budget and timeline can also impact your decision.
Mechanical polishing is often less expensive and faster, but it can be more labor-intensive, especially for intricate designs.
Chemical polishing generally offers a quicker route to a flawless finish but can be more costly due to the chemicals and equipment required.
Understand the Application
Consider how the polished component will be used.
In industries requiring sterile and corrosion-resistant finishes, such as medical, pharmaceutical, or food processing, chemical polishing might be the optimal choice.
For construction, automotive, or general manufacturing, mechanical polishing is more likely to meet your needs.
In conclusion, both chemical polishing and mechanical polishing offer unique advantages and drawbacks.
Understanding these differences helps you make an informed decision, ensuring that your polished surfaces not only look good but also perform optimally in their intended applications.
資料ダウンロード
QCD調達購買管理クラウド「newji」は、調達購買部門で必要なQCD管理全てを備えた、現場特化型兼クラウド型の今世紀最高の購買管理システムとなります。
ユーザー登録
調達購買業務の効率化だけでなく、システムを導入することで、コスト削減や製品・資材のステータス可視化のほか、属人化していた購買情報の共有化による内部不正防止や統制にも役立ちます。
NEWJI DX
製造業に特化したデジタルトランスフォーメーション(DX)の実現を目指す請負開発型のコンサルティングサービスです。AI、iPaaS、および先端の技術を駆使して、製造プロセスの効率化、業務効率化、チームワーク強化、コスト削減、品質向上を実現します。このサービスは、製造業の課題を深く理解し、それに対する最適なデジタルソリューションを提供することで、企業が持続的な成長とイノベーションを達成できるようサポートします。
オンライン講座
製造業、主に購買・調達部門にお勤めの方々に向けた情報を配信しております。
新任の方やベテランの方、管理職を対象とした幅広いコンテンツをご用意しております。
お問い合わせ
コストダウンが利益に直結する術だと理解していても、なかなか前に進めることができない状況。そんな時は、newjiのコストダウン自動化機能で大きく利益貢献しよう!
(Β版非公開)