- お役立ち記事
- The difference between Laser Processing and Electropolishing
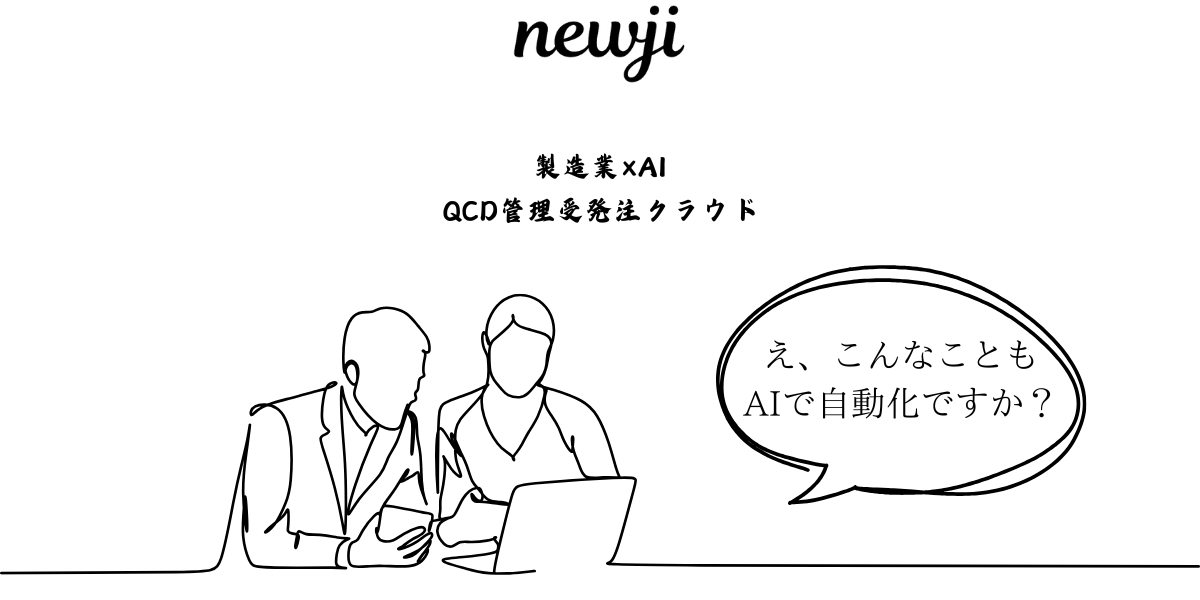
The difference between Laser Processing and Electropolishing
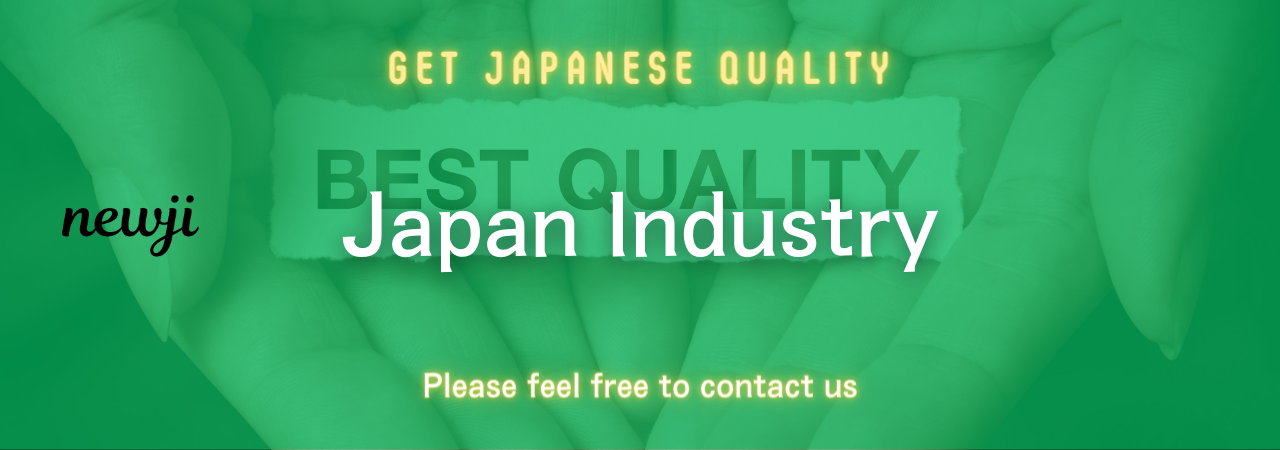
目次
Understanding Laser Processing
Laser processing is a technique that uses high-intensity light beams to cut, engrave, weld, or alter material properties. This method has found applications in various industries due to its precision and versatility.
One of the main advantages of laser processing is its ability to perform detailed work with minimal material waste.
By focusing a laser beam on the material, it can cut through metal, wood, plastic, and other substances with a high degree of accuracy.
Another benefit is that laser processing is often a contactless method, which reduces the risk of contaminating or damaging the material.
Industries such as automotive, aerospace, electronics, and even the medical field use laser processing for different purposes.
In the automotive industry, lasers are used for cutting and welding car components.
In electronics, they are utilized for engraving and micromachining tiny parts that make up various gadgets and devices.
Types of Laser Processing
There are several types of laser processing techniques, each suited for different applications and materials.
Some common types include:
Laser Cutting
Laser cutting involves using a focused laser beam to cut materials into specific shapes and sizes.
It is widely used in manufacturing to create complex parts that require high precision.
Laser Engraving
Laser engraving is another technique where the laser is used to etch designs or information onto surfaces.
This process is popular for creating intricate patterns, marks, and text on various items, from jewelry to industrial components.
Laser Welding
Laser welding uses a laser beam to join pieces of material together with a strong, precise weld.
This method is particularly useful for delicate or intricate work where traditional welding techniques might fail.
Laser Marking
Laser marking is used for placing identification marks, such as barcodes, serial numbers, or logos, on various products and materials.
This process ensures clear and permanent markings without damaging the material’s surface.
Understanding Electropolishing
Electropolishing is a process that removes a thin layer of material from a metal surface using an electrochemical solution.
This technique is widely used for polishing, passivating, and deburring metal parts, providing a smooth and shiny finish.
The primary function of electropolishing is to improve the surface quality of the metal, removing imperfections and reducing roughness.
The process also enhances corrosion resistance by creating a passive oxide layer on the metal surface.
As a result, components treated with electropolishing are much more resistant to chemical and environmental wear.
Applications of electropolishing are vast and include the medical, pharmaceutical, food and beverage, and aerospace industries.
In the medical sector, electropolished components are essential for surgical instruments and implants, where a smooth and bacteria-resistant surface is crucial.
In the food industry, electropolishing is used to ensure that equipment meets strict hygiene standards, preventing bacteria from adhering to the surfaces of processing equipment.
How Electropolishing Works
Electropolishing involves immersing the metal part into a specially formulated electrolyte solution.
An electrical current is then passed through the solution, which causes material removal at a microscopic level.
The process is relatively quick and straightforward:
Preparation
Before electropolishing, the metal surface needs to be cleaned thoroughly to remove any oils, dirt, or oxides that may interfere with the process.
Electrolyte Bath
The cleaned metal part is submerged in the electrolyte solution, typically containing phosphoric and sulfuric acids.
Current Application
An electrical current is applied, causing the high points on the metal surface to dissolve more quickly than the low points, resulting in a smooth, polished finish.
Comparing Laser Processing and Electropolishing
While both laser processing and electropolishing are used to enhance material properties and finish, they serve different functions and are suitable for distinct applications.
Precision and Detail
Laser processing excels in applications requiring high precision and intricate details.
This method can cut, engrave, and mark materials with exceptional accuracy, making it ideal for industries like electronics and automotive.
On the other hand, electropolishing is more suitable for applications that demand a uniform, smooth surface finish and enhanced corrosion resistance.
It is extensively used in the medical and food industries where surface hygiene and smoothness are critical.
Material and Surface Type
Laser processing can work on a variety of materials, including metals, plastics, wood, and even ceramics.
Its versatility makes it applicable to a wide array of industries.
Electropolishing, however, is mainly used for metal materials.
Commonly polished metals include stainless steel, aluminum, and titanium.
Environmental Impact
Laser processing is generally considered environmentally friendly as it produces minimal waste and does not require harmful chemicals.
However, the energy consumption of laser equipment can be high, depending on the application.
Electropolishing involves the use of chemical solutions, which could pose environmental hazards if not handled properly.
Safe disposal of the electrolyte solution is crucial to minimize environmental impact.
Conclusion
Both laser processing and electropolishing offer unique benefits and are integral to modern manufacturing processes.
Laser processing is preferred for tasks that require precision, flexibility, and minimal material waste.
Electropolishing, though limited to metals, provides superior surface finishes, making it essential for industries demanding high hygiene and corrosion resistance standards.
Understanding the distinct advantages of these two techniques can help you select the most appropriate method for your specific application.
By making informed decisions, you can optimize manufacturing processes, ensuring high-quality outcomes that meet your industry’s requirements.
資料ダウンロード
QCD調達購買管理クラウド「newji」は、調達購買部門で必要なQCD管理全てを備えた、現場特化型兼クラウド型の今世紀最高の購買管理システムとなります。
ユーザー登録
調達購買業務の効率化だけでなく、システムを導入することで、コスト削減や製品・資材のステータス可視化のほか、属人化していた購買情報の共有化による内部不正防止や統制にも役立ちます。
NEWJI DX
製造業に特化したデジタルトランスフォーメーション(DX)の実現を目指す請負開発型のコンサルティングサービスです。AI、iPaaS、および先端の技術を駆使して、製造プロセスの効率化、業務効率化、チームワーク強化、コスト削減、品質向上を実現します。このサービスは、製造業の課題を深く理解し、それに対する最適なデジタルソリューションを提供することで、企業が持続的な成長とイノベーションを達成できるようサポートします。
オンライン講座
製造業、主に購買・調達部門にお勤めの方々に向けた情報を配信しております。
新任の方やベテランの方、管理職を対象とした幅広いコンテンツをご用意しております。
お問い合わせ
コストダウンが利益に直結する術だと理解していても、なかなか前に進めることができない状況。そんな時は、newjiのコストダウン自動化機能で大きく利益貢献しよう!
(Β版非公開)