- お役立ち記事
- The difference between Maintenance Plan and Equipment Replacement Plan
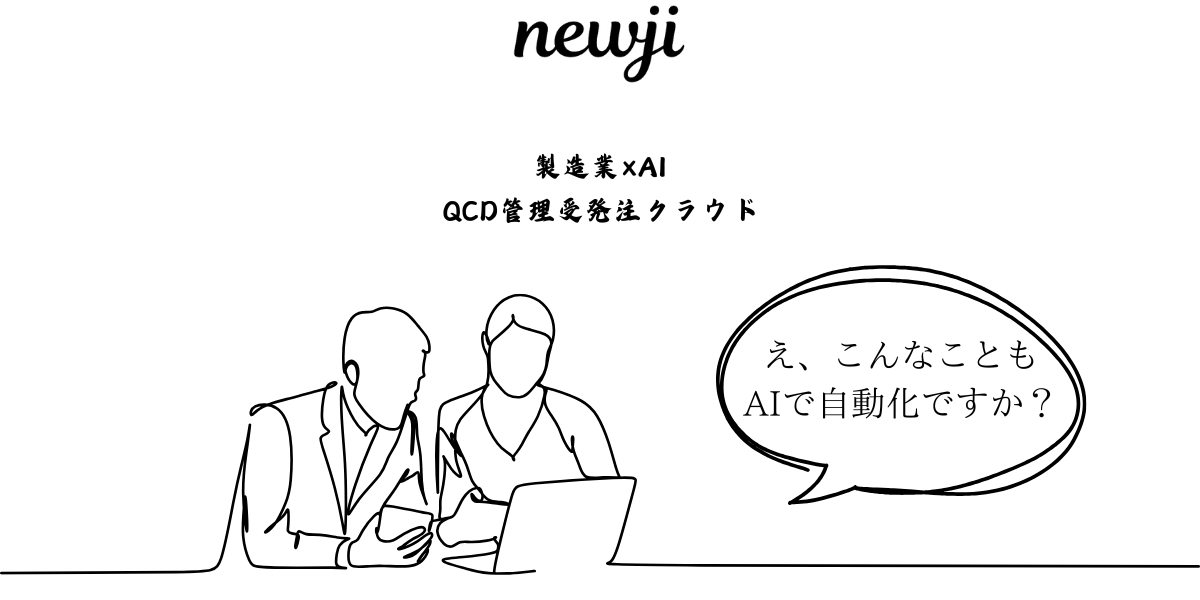
The difference between Maintenance Plan and Equipment Replacement Plan
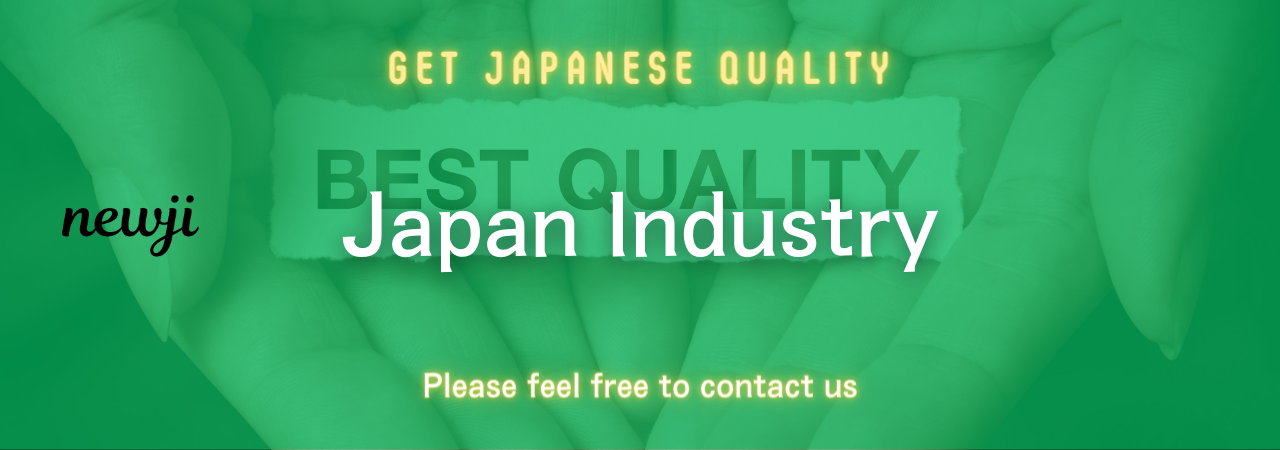
When managing assets, especially in industries relying on heavy machinery, two critical strategies often come into play: the maintenance plan and the equipment replacement plan. Both are designed to enhance the efficiency and longevity of equipment, but they serve different purposes and require different approaches. Understanding these differences can help organizations optimize their operations, reduce costs, and improve overall productivity.
目次
Understanding Maintenance Plans
A maintenance plan is a systematic approach to maintaining equipment in optimal working condition. It involves regular inspections, adjustments, cleaning, lubrication, testing, and parts replacement to ensure machinery continues to run smoothly.
Preventive Maintenance
Preventive maintenance is performed on a scheduled basis to prevent equipment failures before they occur. The idea is to address minor issues before they become significant problems. This approach can lead to reduced downtime, increased equipment lifespan, and improved reliability. For example, routine oil changes in vehicles or regular calibration of industrial machines fall under preventive maintenance.
Predictive Maintenance
Predictive maintenance uses tools and techniques to predict equipment failures before they happen. It involves monitoring equipment conditions such as temperature, vibration, and sound using sensors and diagnostic tools. By analyzing this data, maintenance teams can identify anomalies and address them before they lead to equipment failure.
Corrective Maintenance
Corrective maintenance is performed after a problem has occurred. It involves diagnosing the issue, repairing or replacing faulty parts, and restoring the equipment to working condition. While it’s reactive in nature, it is an essential part of the overall maintenance strategy for dealing with unexpected breakdowns.
Understanding Equipment Replacement Plans
An equipment replacement plan, on the other hand, is a strategy that outlines when and how to replace equipment before it becomes inefficient, unreliable, or too costly to maintain. This plan aims to ensure organizations operate with up-to-date equipment, minimizing downtime and maximizing productivity.
Cost-Benefit Analysis
One of the primary considerations in an equipment replacement plan is the cost-benefit analysis. This involves comparing the costs of maintaining existing equipment versus the cost of purchasing new equipment. Factors such as repair frequency, energy consumption, efficiency, and potential downtime are considered. If maintaining the old equipment is more expensive in the long run, it might be more economical to replace it.
Lifespan of Equipment
Understanding the expected lifespan of equipment is crucial in an equipment replacement plan. Every piece of machinery has a finite lifespan and will eventually need to be replaced. By keeping track of the age and condition of each piece of equipment, organizations can plan for replacements before they become critical.
Technological Advancements
Advancements in technology can significantly impact equipment replacement decisions. Newer models often offer improved efficiency, better performance, and more advanced features. By staying up-to-date with the latest technological advancements, companies can take advantage of innovations that can enhance their operations.
Key Differences Between Maintenance Plan and Equipment Replacement Plan
While both maintenance and equipment replacement plans aim to ensure smooth operations, they differ in their focus and implementation.
Objective
The primary objective of a maintenance plan is to keep equipment running efficiently and to prevent breakdowns through regular upkeep. It emphasizes proactive measures to extend the lifecycle of existing equipment.
In contrast, an equipment replacement plan is focused on determining the optimal time to replace outdated or failing equipment. The goal is to ensure the organization benefits from the latest technology and avoids excessive maintenance costs.
Strategy
Maintenance plans are typically ongoing and require continuous monitoring, inspection, and minor repairs. The strategy involves spending smaller amounts regularly to prevent significant issues.
Equipment replacement plans, however, involve larger, sporadic investments in new equipment. The strategy is to make more significant capital expenditures at intervals that are economically justified based on equipment performance and technological advancements.
Cost Implications
Maintenance plans can involve regular shorter-term costs that add up over time but help avoid the significant expenses associated with unplanned downtime and major repairs.
Equipment replacement plans, on the other hand, require a considerable capital expenditure at the time of purchasing new equipment but can lead to long-term savings by reducing maintenance costs and improving efficiency.
Operational Impact
A well-implemented maintenance plan can minimize downtime and keep operations running smoothly. It ensures that equipment is always in good working condition.
In contrast, equipment replacement can involve scheduled downtime for the installation and setup of new machinery. However, this downtime is generally planned and can be managed to minimize disruptions.
Integrating Maintenance and Equipment Replacement Plans
While maintenance and equipment replacement plans have distinct differences, they are not mutually exclusive. In fact, the best asset management strategy often involves integrating both approaches.
Holistic Asset Management
A comprehensive asset management strategy should include both maintenance and replacement plans. Regular maintenance ensures that equipment performs optimally throughout its lifespan, while a strategic replacement plan ensures that outdated equipment is replaced before it becomes a liability.
Data-Driven Decisions
Utilizing data from maintenance records and equipment performance can inform better equipment replacement decisions. By analyzing maintenance trends and equipment costs, organizations can make data-driven decisions on when to maintain and when to replace.
Financial Planning
Budgeting for both maintenance costs and future equipment replacements is crucial. Organizations should set aside funds for regular maintenance while planning for larger capital expenditures associated with equipment replacement.
Conclusion
Understanding the difference between maintenance plans and equipment replacement plans is vital for effective asset management.
Maintenance plans focus on keeping existing equipment in optimal condition through regular upkeep and preventive measures.
In contrast, equipment replacement plans aim to identify the right time to invest in new equipment, considering factors like cost, performance, and technological advancements.
By integrating both strategies, organizations can maximize their operational efficiency, minimize downtime, and ensure a cost-effective approach to managing their assets.
資料ダウンロード
QCD調達購買管理クラウド「newji」は、調達購買部門で必要なQCD管理全てを備えた、現場特化型兼クラウド型の今世紀最高の購買管理システムとなります。
ユーザー登録
調達購買業務の効率化だけでなく、システムを導入することで、コスト削減や製品・資材のステータス可視化のほか、属人化していた購買情報の共有化による内部不正防止や統制にも役立ちます。
NEWJI DX
製造業に特化したデジタルトランスフォーメーション(DX)の実現を目指す請負開発型のコンサルティングサービスです。AI、iPaaS、および先端の技術を駆使して、製造プロセスの効率化、業務効率化、チームワーク強化、コスト削減、品質向上を実現します。このサービスは、製造業の課題を深く理解し、それに対する最適なデジタルソリューションを提供することで、企業が持続的な成長とイノベーションを達成できるようサポートします。
オンライン講座
製造業、主に購買・調達部門にお勤めの方々に向けた情報を配信しております。
新任の方やベテランの方、管理職を対象とした幅広いコンテンツをご用意しております。
お問い合わせ
コストダウンが利益に直結する術だと理解していても、なかなか前に進めることができない状況。そんな時は、newjiのコストダウン自動化機能で大きく利益貢献しよう!
(Β版非公開)