- お役立ち記事
- The difference between Operation Planning and Equipment Planning
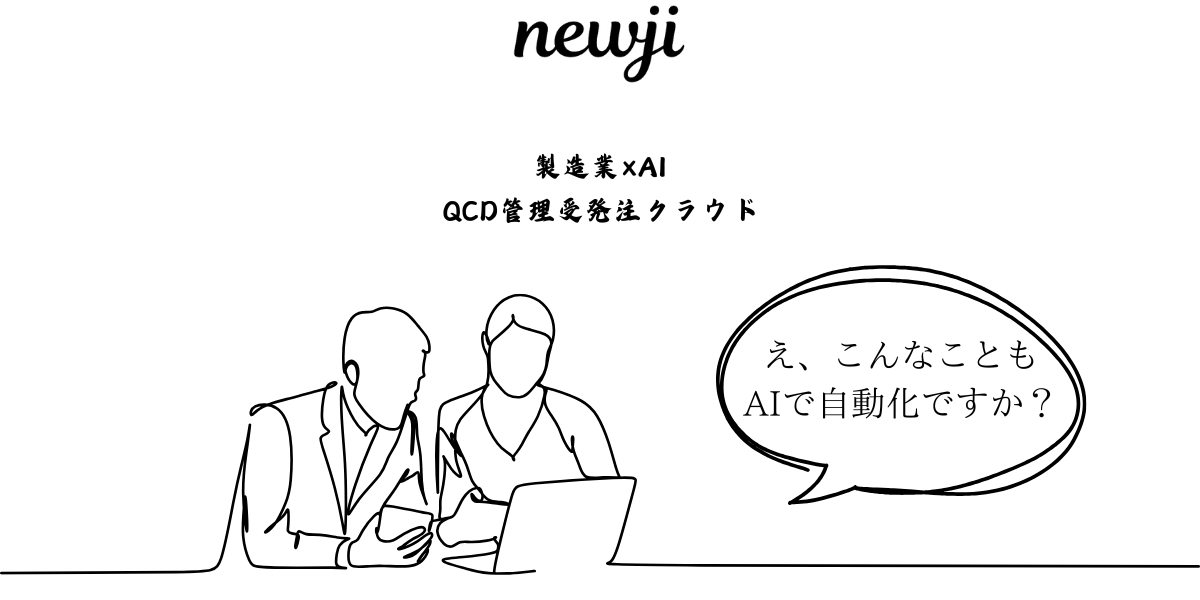
The difference between Operation Planning and Equipment Planning
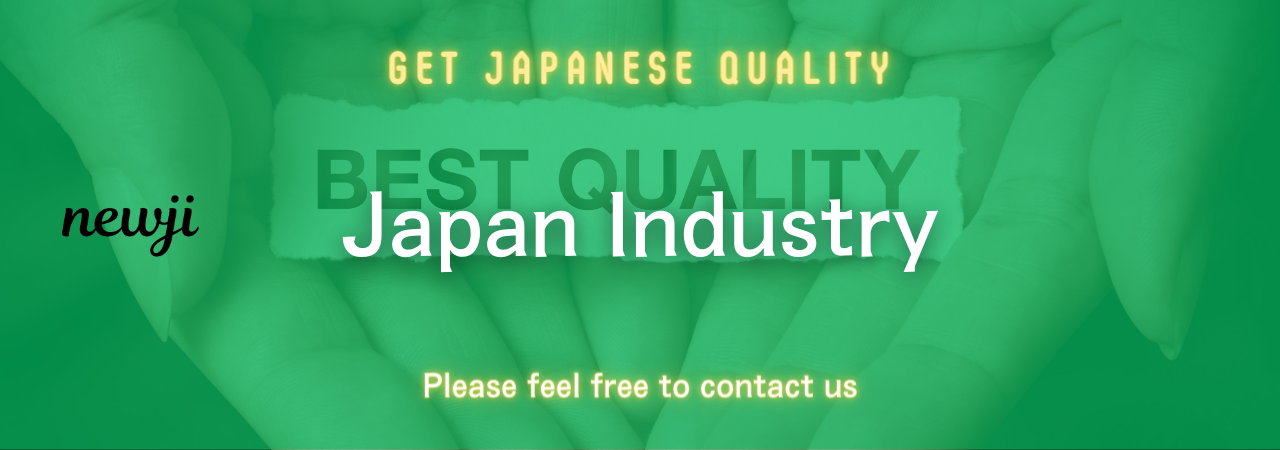
When managing projects, resources, or even entire businesses, planning is critical for success.
Among the various aspects of planning, two significant elements often come up: operation planning and equipment planning.
While they both fall under the broader umbrella of management and logistics, each has its unique characteristics and applications.
Understanding their differences can help improve efficiency and achieve desired outcomes.
目次
What is Operation Planning?
Operation planning refers to the process of outlining the necessary steps to achieve specific business objectives.
This includes the development of strategic plans, tactical plans, and operational plans.
Operation planning ensures that day-to-day activities align with the company’s long-term goals.
Components of Operation Planning
Strategic Plans
These plans are long-term and focus on the overall mission and goals of the organization.
They address questions like:
What are the company’s objectives?
How can resources be allocated to meet these objectives?
Tactical Plans
Tactical plans are short-term and are usually developed by mid-level management.
They outline the actions needed to implement the strategic plans.
These plans often span months to a couple of years and are more detailed than strategic plans.
Operational Plans
These are highly specific plans that outline daily, weekly, or monthly tasks.
Operational plans ensure that tactical plans are implemented effectively.
These include schedules, budgets, and detailed procedures.
What is Equipment Planning?
Equipment planning, on the other hand, focuses specifically on managing the tools and machinery required for fulfilling tasks and meeting business goals.
It includes selecting, acquiring, maintaining, and disposing of equipment.
Efficient equipment planning can significantly affect productivity and operational costs.
Key Aspects of Equipment Planning
Selection
Identifying the right equipment for a particular task is crucial.
The selection process involves analyzing the requirements and evaluating various options based on efficiency, cost, and suitability.
Acquisition
Once the appropriate equipment is selected, the acquisition process begins.
This includes budgeting, procurement, and sometimes negotiations with suppliers to ensure a cost-effective purchase.
Maintenance
Regular maintenance is essential to keep the equipment in working condition.
This includes scheduled inspections, repairs, and upgrades to prevent unexpected breakdowns and ensure longevity.
Disposal
When equipment becomes outdated or non-functional, an effective disposal plan is necessary.
This may involve selling, recycling, or discarding the equipment responsibly.
Differences Between Operation Planning and Equipment Planning
Scope
Operation planning is broad and encompasses the overall strategy and day-to-day operations of a business.
It includes various elements such as workforce management, process optimization, and more.
Equipment planning is narrower in scope and focuses specifically on the machinery and tools required for specific tasks.
Focus
Operation planning aims at achieving specific business objectives and involves a wide range of activities, from resource allocation to performance monitoring.
Equipment planning primarily concentrates on the lifecycle of equipment, including its selection, maintenance, and replacement.
Timeframe
Operation planning includes long-term, mid-term, and short-term plans.
Strategic plans may span several years, while tactical plans cover a few months to a couple of years, and operational plans deal with daily activities.
Equipment planning usually involves a shorter timeframe, dealing mostly with the operational phase of equipment unless long-term investments and future acquisitions are considered.
Resource Allocation
In operation planning, a variety of resources are considered, such as human resources, financial capital, and raw materials.
Equipment planning focuses solely on the tools and machinery necessary for completing tasks efficiently.
Decision-Making Process
Operation planning often involves input from various levels of management and requires coordination among different departments.
Decisions in this realm are more complex due to the multiple variables involved.
Equipment planning typically involves fewer stakeholders and is more straightforward, mainly requiring approval from the financial and operational departments.
Importance of Integrating Both Plans
While operation planning and equipment planning have distinct roles, integrating the two can offer a comprehensive approach to achieving business goals.
For instance, ineffective equipment planning can derail even the best-formulated operational plans by causing delays and increasing costs.
Enhanced Efficiency
By integrating both planning processes, businesses can ensure that the necessary equipment is available when needed, thus preventing downtime and enhancing operational efficiency.
This integration helps in aligning the availability of resources with the execution of tasks.
Cost Management
Effective equipment planning can prevent unnecessary expenditures on equipment purchase and maintenance.
When combined with operation planning, it helps in better budgeting and financial planning.
This holistic approach ensures that funds are allocated judiciously, enhancing overall financial stability.
Risk Management
Integrating both types of planning can also aid in risk management.
Having a well-maintained inventory of equipment reduces the risks associated with unexpected breakdowns or obsolescence.
On the other hand, thorough operational planning can identify potential bottlenecks and develop contingency plans, thus ensuring smoother operations.
Conclusion
Understanding the differences between operation planning and equipment planning is essential for effective business management.
While operation planning focuses on achieving broader business goals through strategic and tactical initiatives, equipment planning zeroes in on the lifecycle of the tools and machinery required for these tasks.
By integrating both approaches, businesses can achieve higher efficiency, better cost management, and comprehensive risk mitigation.
Ultimately, the synergy between operation planning and equipment planning can pave the way for sustained success and growth.
資料ダウンロード
QCD調達購買管理クラウド「newji」は、調達購買部門で必要なQCD管理全てを備えた、現場特化型兼クラウド型の今世紀最高の購買管理システムとなります。
ユーザー登録
調達購買業務の効率化だけでなく、システムを導入することで、コスト削減や製品・資材のステータス可視化のほか、属人化していた購買情報の共有化による内部不正防止や統制にも役立ちます。
NEWJI DX
製造業に特化したデジタルトランスフォーメーション(DX)の実現を目指す請負開発型のコンサルティングサービスです。AI、iPaaS、および先端の技術を駆使して、製造プロセスの効率化、業務効率化、チームワーク強化、コスト削減、品質向上を実現します。このサービスは、製造業の課題を深く理解し、それに対する最適なデジタルソリューションを提供することで、企業が持続的な成長とイノベーションを達成できるようサポートします。
オンライン講座
製造業、主に購買・調達部門にお勤めの方々に向けた情報を配信しております。
新任の方やベテランの方、管理職を対象とした幅広いコンテンツをご用意しております。
お問い合わせ
コストダウンが利益に直結する術だと理解していても、なかなか前に進めることができない状況。そんな時は、newjiのコストダウン自動化機能で大きく利益貢献しよう!
(Β版非公開)