- お役立ち記事
- The difference between Preventive Maintenance and Predictive Maintenance
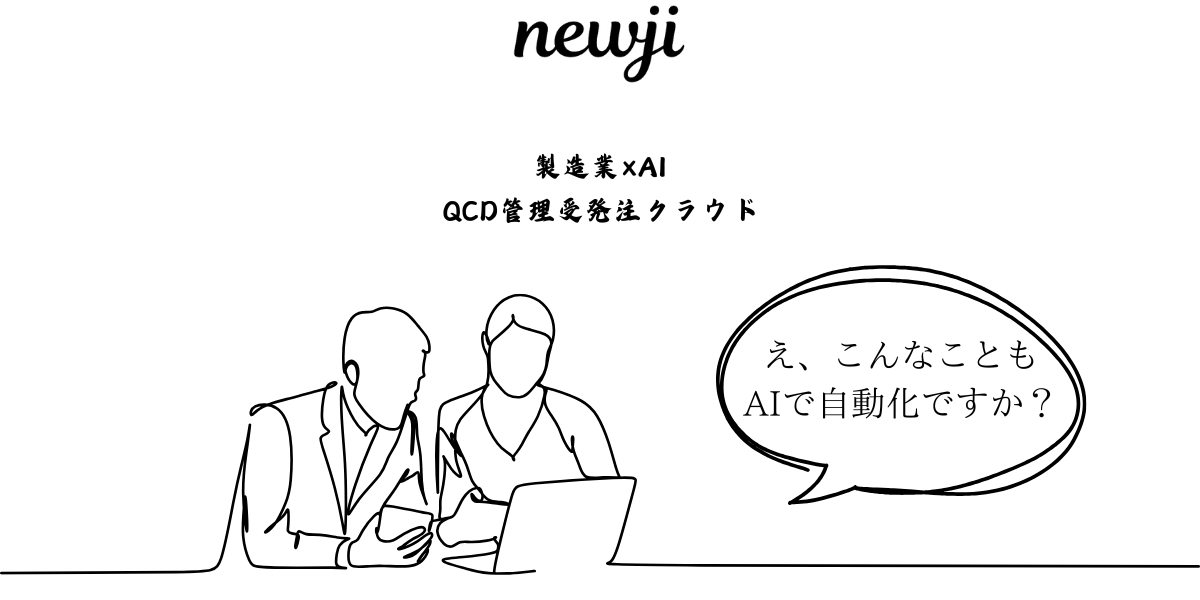
The difference between Preventive Maintenance and Predictive Maintenance
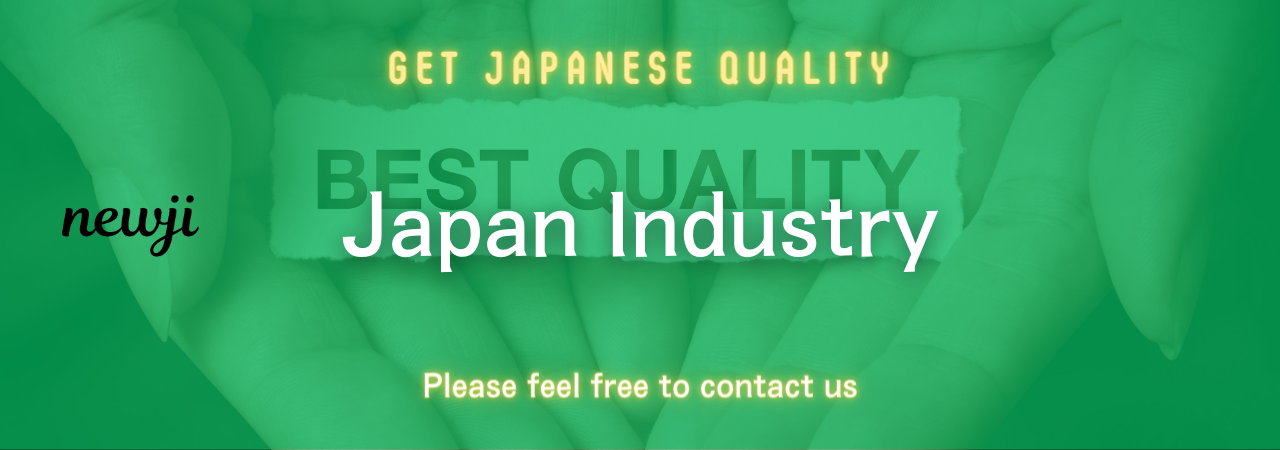
Maintenance is crucial for keeping machinery and equipment in optimal condition.
It ensures that operations run smoothly and minimizes the risk of unexpected breakdowns.
Two common strategies for machinery upkeep are Preventive Maintenance and Predictive Maintenance.
Understanding the differences between these two methods can help in selecting the best approach for your needs.
目次
What is Preventive Maintenance?
Preventive Maintenance involves regular, scheduled inspections, and servicing of equipment.
The primary goal is to prevent machinery failures before they occur.
By following a set maintenance schedule, you can catch potential issues early and fix them before they cause significant problems.
How Does Preventive Maintenance Work?
This approach follows a routine maintenance schedule based on a calendar or operating hours.
It often includes tasks such as checking and replacing parts, lubricating moving components, and performing system diagnostics.
By adhering to a consistent schedule, you can ensure that all equipment receives the attention it needs.
This method relies on historical data and manufacturer recommendations to determine the best intervals for maintenance tasks.
Benefits of Preventive Maintenance
– **Reduced Downtime:** Regular maintenance reduces the likelihood of unexpected breakdowns, keeping equipment running smoothly.
– **Extended Equipment Life:** Consistent care prolongs the lifespan of machinery and components.
– **Cost Savings:** Catching issues early can prevent expensive repairs and reduce the need for emergency service calls.
– **Improved Safety:** Regular inspections and servicing can identify hazardous conditions, reducing the risk of accidents.
Limitations of Preventive Maintenance
– **Time-Consuming:** Following a strict maintenance schedule can be time-intensive.
– **Over-Maintenance:** Routine servicing may lead to unnecessary maintenance on equipment that is still in good condition.
– **Initial Costs:** Implementing a comprehensive maintenance plan can require significant upfront investment.
What is Predictive Maintenance?
Predictive Maintenance, on the other hand, uses data and analytics to predict when equipment failures might occur.
This method relies on real-time monitoring and advanced technologies to assess the condition of machinery continually.
By predicting potential issues before they happen, you can address problems before they lead to unplanned downtime.
How Does Predictive Maintenance Work?
Predictive Maintenance involves the use of sensors and software to monitor equipment performance continuously.
These tools collect data on factors such as vibration, temperature, and machine load.
The data is then analyzed to identify patterns and trends that may indicate an impending failure.
By predicting when issues are likely to arise, maintenance can be scheduled at the most opportune times.
This data-driven approach can pinpoint specific problems, allowing for targeted and efficient repairs.
Benefits of Predictive Maintenance
– **Minimized Downtime:** Predictive maintenance reduces unexpected equipment failures, ensuring smoother operations.
– **Optimized Maintenance Scheduling:** Maintenance is performed only when necessary, avoiding unnecessary interruptions.
– **Cost Efficiency:** Early detection of issues can prevent costly repairs and extend equipment lifespan.
– **Enhanced Safety:** Real-time monitoring can identify potential hazards promptly, improving workplace safety.
Limitations of Predictive Maintenance
– **Technology Investment:** Implementing predictive maintenance requires significant investment in sensors, monitoring tools, and software.
– **Complexity:** Understanding and analyzing data requires specialized knowledge and skills.
– **Initial Setup Time:** Establishing a comprehensive predictive maintenance system can be time-consuming and complex.
Which Approach is Best for You?
Choosing between Preventive and Predictive Maintenance depends on several factors.
Consider the following aspects to determine which method suits your needs best:
Cost
Preventive Maintenance generally involves lower upfront costs compared to Predictive Maintenance.
However, over time, Predictive Maintenance can offer cost savings by optimizing maintenance schedules and reducing equipment failures.
Equipment Type
For simpler machinery with fewer variables, Preventive Maintenance may be sufficient.
Complex equipment with many moving parts may benefit more from the detailed insights provided by Predictive Maintenance.
Availability of Data
Predictive Maintenance relies heavily on data collection and analysis.
If your equipment is capable of providing detailed performance data, this approach can be highly effective.
Conversely, if data collection is not practical, a Preventive Maintenance strategy may be more appropriate.
Resource Availability
Consider the resources available for implementing and maintaining each strategy.
While Preventive Maintenance primarily requires scheduling and manual labor, Predictive Maintenance involves technological investments and data analysis expertise.
Combining Both Approaches
In many cases, a hybrid approach may offer the best results.
By combining elements of both Preventive and Predictive Maintenance, you can create a comprehensive maintenance strategy.
Regular scheduled inspections can be supplemented with real-time monitoring to ensure the highest level of equipment reliability.
Implementing a Hybrid Strategy
– **Assess Equipment Needs:** Determine which equipment will benefit most from predictive monitoring.
– **Set Maintenance Goals:** Define your maintenance objectives, such as minimizing downtime or extending equipment lifespan.
– **Invest in Technology:** Equip critical machinery with necessary sensors and monitoring tools.
– **Schedule Regular Inspections:** Continue with routine maintenance for less complex equipment.
– **Analyze Data:** Regularly review performance data to predict and address potential issues.
– **Adapt and Improve:** Continuously assess the effectiveness of your maintenance strategy and make adjustments as needed.
By understanding the differences between Preventive and Predictive Maintenance, you can make informed decisions to enhance the efficiency and reliability of your operations.
Choosing the right maintenance strategy—or a combination of both—will help you keep your equipment in top condition and minimize the risk of unexpected failures.
資料ダウンロード
QCD調達購買管理クラウド「newji」は、調達購買部門で必要なQCD管理全てを備えた、現場特化型兼クラウド型の今世紀最高の購買管理システムとなります。
ユーザー登録
調達購買業務の効率化だけでなく、システムを導入することで、コスト削減や製品・資材のステータス可視化のほか、属人化していた購買情報の共有化による内部不正防止や統制にも役立ちます。
NEWJI DX
製造業に特化したデジタルトランスフォーメーション(DX)の実現を目指す請負開発型のコンサルティングサービスです。AI、iPaaS、および先端の技術を駆使して、製造プロセスの効率化、業務効率化、チームワーク強化、コスト削減、品質向上を実現します。このサービスは、製造業の課題を深く理解し、それに対する最適なデジタルソリューションを提供することで、企業が持続的な成長とイノベーションを達成できるようサポートします。
オンライン講座
製造業、主に購買・調達部門にお勤めの方々に向けた情報を配信しております。
新任の方やベテランの方、管理職を対象とした幅広いコンテンツをご用意しております。
お問い合わせ
コストダウンが利益に直結する術だと理解していても、なかなか前に進めることができない状況。そんな時は、newjiのコストダウン自動化機能で大きく利益貢献しよう!
(Β版非公開)