- お役立ち記事
- The difference between Production Planning and Manufacturing Planning
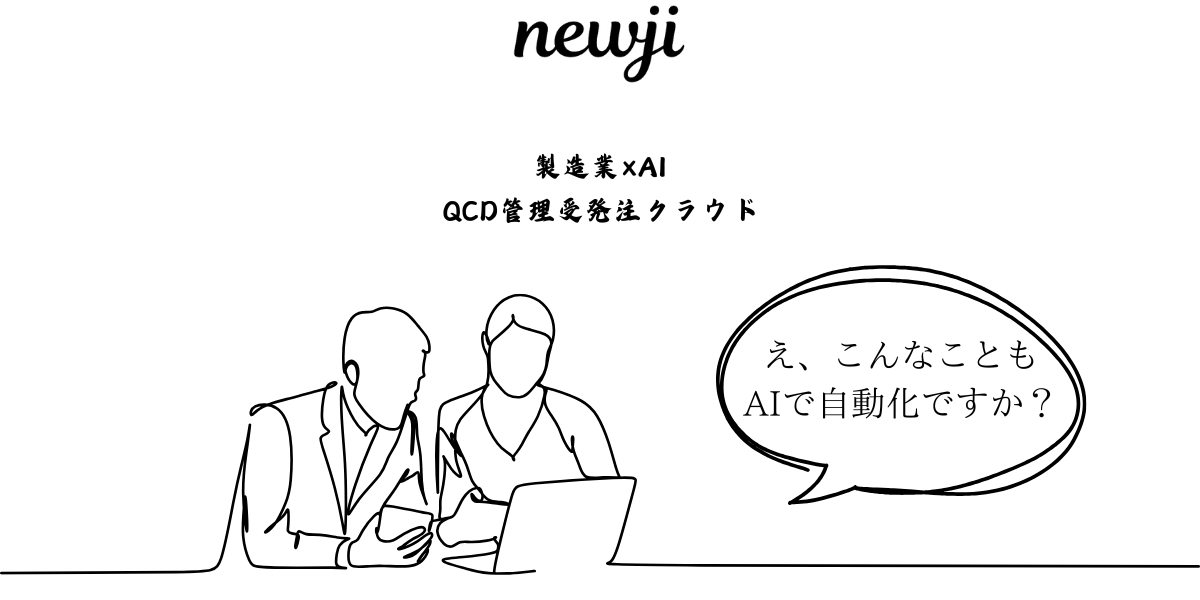
The difference between Production Planning and Manufacturing Planning
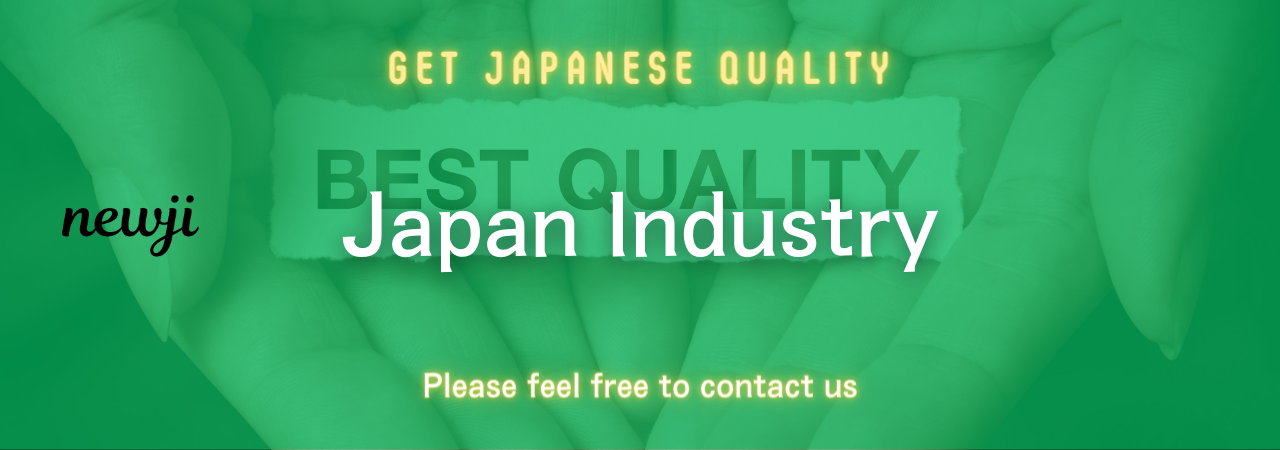
目次
Understanding Production Planning
Production planning is a foundational element in manufacturing and other production processes.
It involves strategizing and deciding what will be produced, when it will be produced, and how it will meet demand.
At its core, production planning aims to balance various factors, including resources, timelines, and market demands.
By accurately forecasting demand, businesses can ensure they produce the right amounts of goods, minimizing both overproduction and shortages.
One of the main components of production planning is demand forecasting.
This process uses historical sales data, market trends, and statistical tools to predict future customer demand.
Accurate demand forecasting ensures that resources are efficiently allocated, reducing waste and optimizing stock levels.
Another critical part is capacity planning.
This involves evaluating the production facility’s capability to meet demand.
By understanding current production capabilities, businesses can determine whether they need to invest in new machinery, hire additional staff, or extend working hours.
Steps in Production Planning
1. **Demand Forecasting**: Predict future customer demand using various tools and techniques.
2. **Capacity Planning**: Assess production capabilities and identify any gaps that might hinder meeting demand.
3. **Material Requirement Planning (MRP)**: Determine the materials required for production and ensure their availability.
4. **Scheduling**: Create a timeline for when production activities will take place.
5. **Monitoring and Control**: Continuously oversee production activities to ensure everything is on track and adjust as necessary.
Understanding Manufacturing Planning
Manufacturing planning is closely related to production planning but has a distinct focus.
While production planning involves deciding what to produce and when, manufacturing planning is concerned with how goods will be produced efficiently and effectively.
Manufacturing planning delves deeper into the specifics of the production process.
It includes selecting the appropriate manufacturing methods, equipment, and technology to be used.
Additionally, it encompasses organizing the workforce and determining the optimal workflow to achieve maximum efficiency.
A crucial element of manufacturing planning is process optimization.
This involves analyzing production processes to identify bottlenecks, inefficiencies, and potential areas for improvement.
By streamlining processes, businesses can improve output quality, reduce production time, and lower costs.
Steps in Manufacturing Planning
1. **Process Design**: Develop a detailed plan for the production process, including steps, equipment, and workforce requirements.
2. **Resource Allocation**: Ensure all necessary resources (materials, labor, machinery) are available and effectively allocated.
3. **Workflow Organization**: Arrange the production process flow to maximize efficiency and minimize disruptions.
4. **Quality Control**: Implement measures to ensure all products meet the required quality standards.
5. **Continuous Improvement**: Regularly review and optimize production processes to enhance performance and efficiency.
Key Differences Between Production Planning and Manufacturing Planning
While production planning and manufacturing planning are interconnected, they serve distinct purposes within the production cycle.
Focus and Objectives
Production planning is primarily concerned with determining **what** to produce and **when** to produce it.
It aims to align production with market demand and resource availability.
Manufacturing planning, on the other hand, focuses on **how** to produce the goods.
Its primary goal is to implement the most efficient and effective production processes, ensuring high-quality output.
Scope of Work
Production planning covers a broader scope, including demand forecasting, capacity planning, and scheduling.
It looks at the production process from a macro perspective, considering overall market dynamics and long-term goals.
Manufacturing planning takes a more micro approach.
It deals with the specifics of the production line, such as process optimization, resource allocation, and workflow management.
Tools and Techniques
Production planning often utilizes tools like demand forecasting software, ERP (Enterprise Resource Planning) systems, and scheduling software.
These tools help in making informed decisions based on market data and resource availability.
Manufacturing planning relies on process mapping, lean manufacturing principles, and quality control systems.
These techniques help in designing efficient production processes and maintaining product quality.
Why Both Are Essential
Integrating both production planning and manufacturing planning is crucial for any manufacturing business.
Accurate production planning ensures that a company can meet customer demand without overburdening its resources.
On the other hand, effective manufacturing planning ensures that the production process is efficient and capable of delivering high-quality products.
Failure in production planning can lead to issues like overproduction, stockouts, and missed deadlines.
Similarly, poor manufacturing planning can result in low-quality products, production delays, and increased costs.
Thus, both elements are essential for a well-rounded, successful production strategy.
Conclusion
In summary, production planning and manufacturing planning are vital components of a successful manufacturing process.
While production planning focuses on determining what to produce and when, manufacturing planning zeroes in on how to produce it most efficiently.
By understanding the differences and integrating both sets of planning practices, businesses can achieve optimal production outcomes, meet market demand, and maintain high-quality standards.
Balancing these two aspects allows for a streamlined, effective, and profitable production operation.
資料ダウンロード
QCD調達購買管理クラウド「newji」は、調達購買部門で必要なQCD管理全てを備えた、現場特化型兼クラウド型の今世紀最高の購買管理システムとなります。
ユーザー登録
調達購買業務の効率化だけでなく、システムを導入することで、コスト削減や製品・資材のステータス可視化のほか、属人化していた購買情報の共有化による内部不正防止や統制にも役立ちます。
NEWJI DX
製造業に特化したデジタルトランスフォーメーション(DX)の実現を目指す請負開発型のコンサルティングサービスです。AI、iPaaS、および先端の技術を駆使して、製造プロセスの効率化、業務効率化、チームワーク強化、コスト削減、品質向上を実現します。このサービスは、製造業の課題を深く理解し、それに対する最適なデジタルソリューションを提供することで、企業が持続的な成長とイノベーションを達成できるようサポートします。
オンライン講座
製造業、主に購買・調達部門にお勤めの方々に向けた情報を配信しております。
新任の方やベテランの方、管理職を対象とした幅広いコンテンツをご用意しております。
お問い合わせ
コストダウンが利益に直結する術だと理解していても、なかなか前に進めることができない状況。そんな時は、newjiのコストダウン自動化機能で大きく利益貢献しよう!
(Β版非公開)