- お役立ち記事
- The difference between Quality Testing and Durability Testing
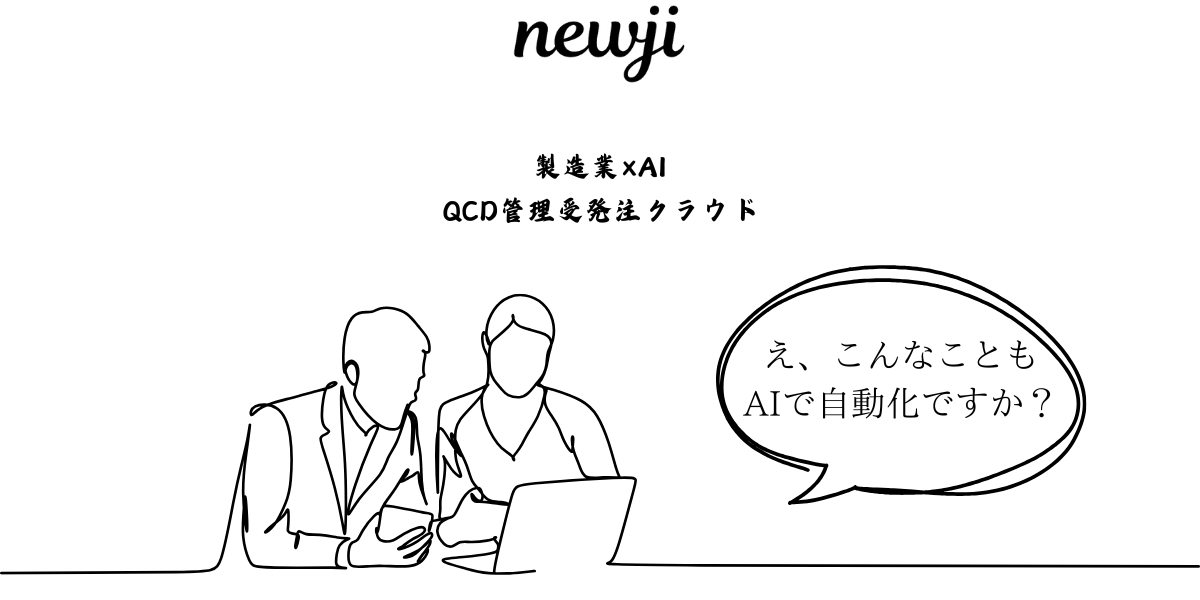
The difference between Quality Testing and Durability Testing
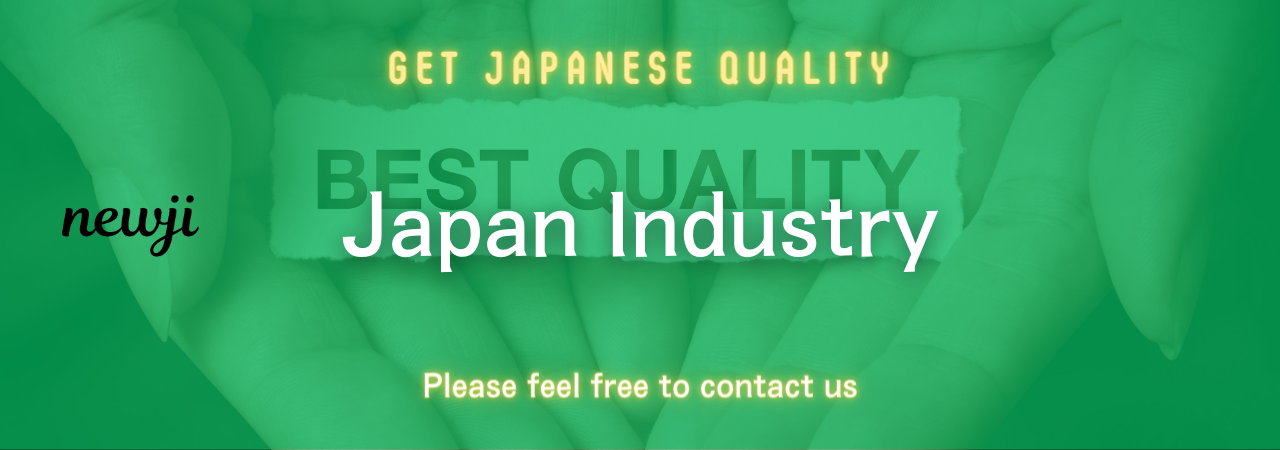
Testing plays a critical role in product development, ensuring that products meet customer expectations and safety standards.
Two important types of testing are quality testing and durability testing.
While they may sound similar, they serve different purposes and have unique methodologies.
Understanding these differences can help manufacturers improve their products and deliver better value to customers.
目次
What is Quality Testing?
Quality testing refers to a variety of procedures and processes used to evaluate the completeness, correctness, and reliability of a product.
The primary purpose is to ensure the product meets specified quality criteria and performance standards.
Ensuring Customer Satisfaction
One of the key goals of quality testing is to ensure customer satisfaction.
By identifying and eliminating defects, manufacturers can deliver products that meet or exceed customer expectations.
This helps in building trust and establishing a positive brand reputation.
Different Methods of Quality Testing
There are several methods to conduct quality testing.
Some of the most common include:
**Manual Testing**
This involves human testers who manually check the product for defects.
Human observation can identify issues that automated systems might miss.
**Automated Testing**
In this method, software tools are used to execute tests automatically.
It’s efficient for repetitive and large-scale testing, reducing the likelihood of human error.
**Functional Testing**
This ensures that the product performs its intended functions correctly.
It tests individual features and functionalities against specified requirements.
**Non-Functional Testing**
This type evaluates aspects like performance, usability, and security.
While functional testing checks if it works, non-functional testing assesses how well it works under various conditions.
What is Durability Testing?
Durability testing assesses the product’s ability to withstand wear, tear, and environmental conditions over time.
Its main objective is to determine the product’s lifespan and performance under stressful conditions.
Why Durability Testing is Important
Durability testing is crucial for several reasons:
**Ensuring Longevity**
Customers expect products to last. Durability testing helps ensure that products meet these expectations and provide long-term value.
**Minimizing Warranty Claims**
Products that fail prematurely can lead to increased warranty claims and higher costs.
Durability testing helps identify potential issues before the product reaches the market.
**Regulatory Compliance**
Certain industries require compliance with durability standards to ensure safety and reliability.
Testing helps manufacturers meet these regulatory requirements.
Types of Durability Testing
Various types of durability testing can be conducted, depending on the product and its intended use.
These include:
**Fatigue Testing**
This tests the product’s ability to withstand repeated stress or load over time.
It’s essential for parts subjected to repetitive actions, like car tires or mechanical components.
**Environmental Testing**
This exposes the product to extreme conditions such as high temperatures, humidity, or corrosive environments.
It helps determine how well the product will perform in different conditions.
**Vibration Testing**
This involves subjecting the product to vibrations to simulate real-world usage.
It’s commonly used for electronics and automotive parts to ensure they can handle the vibrations associated with daily use.
Key Differences Between Quality Testing and Durability Testing
Different Objectives
Quality testing focuses on identifying defects, ensuring the product meets specified criteria, and enhancing customer satisfaction.
Durability testing, however, aims to assess the product’s lifespan and behavior under stress.
Frequency and Timing
Quality testing is typically conducted throughout the product development lifecycle.
It can occur during various stages, from initial design to final production.
Durability testing usually takes place later in the development process to validate that the design can withstand real-world conditions.
Evaluation Methods
Quality testing often employs a mix of manual and automated methods to check functionality and performance.
Durability testing relies more on physical tests, environmental simulations, and repetitive stress tests.
Types of Metrics Used
Quality testing metrics might include defect counts, functional pass rates, and user satisfaction scores.
Durability testing metrics, on the other hand, could involve lifespan under certain conditions, failure rates, and the number of cycles a product can endure before failing.
How They Complement Each Other
Despite their differences, quality testing and durability testing complement each other.
Together, they provide a comprehensive evaluation of a product’s readiness for the market.
Holistic Product Assessment
By combining both types of testing, manufacturers can ensure that their products are not only free from defects but also built to last.
This holistic approach ensures a higher level of customer satisfaction and reduces long-term costs associated with product failures.
Improving Product Design
Data from both quality and durability testing can provide valuable insights for product design and improvement.
For example, durability testing might reveal that a certain material degrades quickly under high stress, leading to a change in material choice in future iterations.
Similarly, quality testing might highlight specific functional issues that need to be addressed.
Boosting Brand Reputation
Products that excel in both quality and durability testing are more likely to earn positive reviews and build customer loyalty.
This boosts brand reputation and can lead to increased market share.
Understanding the differences between quality testing and durability testing is essential for manufacturers aiming to produce high-quality, long-lasting products.
By effectively implementing both testing methodologies, companies can ensure they meet customer expectations and regulatory standards.
Ultimately, this leads to better products and greater market success.
資料ダウンロード
QCD調達購買管理クラウド「newji」は、調達購買部門で必要なQCD管理全てを備えた、現場特化型兼クラウド型の今世紀最高の購買管理システムとなります。
ユーザー登録
調達購買業務の効率化だけでなく、システムを導入することで、コスト削減や製品・資材のステータス可視化のほか、属人化していた購買情報の共有化による内部不正防止や統制にも役立ちます。
NEWJI DX
製造業に特化したデジタルトランスフォーメーション(DX)の実現を目指す請負開発型のコンサルティングサービスです。AI、iPaaS、および先端の技術を駆使して、製造プロセスの効率化、業務効率化、チームワーク強化、コスト削減、品質向上を実現します。このサービスは、製造業の課題を深く理解し、それに対する最適なデジタルソリューションを提供することで、企業が持続的な成長とイノベーションを達成できるようサポートします。
オンライン講座
製造業、主に購買・調達部門にお勤めの方々に向けた情報を配信しております。
新任の方やベテランの方、管理職を対象とした幅広いコンテンツをご用意しております。
お問い合わせ
コストダウンが利益に直結する術だと理解していても、なかなか前に進めることができない状況。そんな時は、newjiのコストダウン自動化機能で大きく利益貢献しよう!
(Β版非公開)